- お役立ち記事
- Defect prevention technology in printed circuit board mounting, micro bonding, and solder bonding
月間76,176名の
製造業ご担当者様が閲覧しています*
*2025年3月31日現在のGoogle Analyticsのデータより
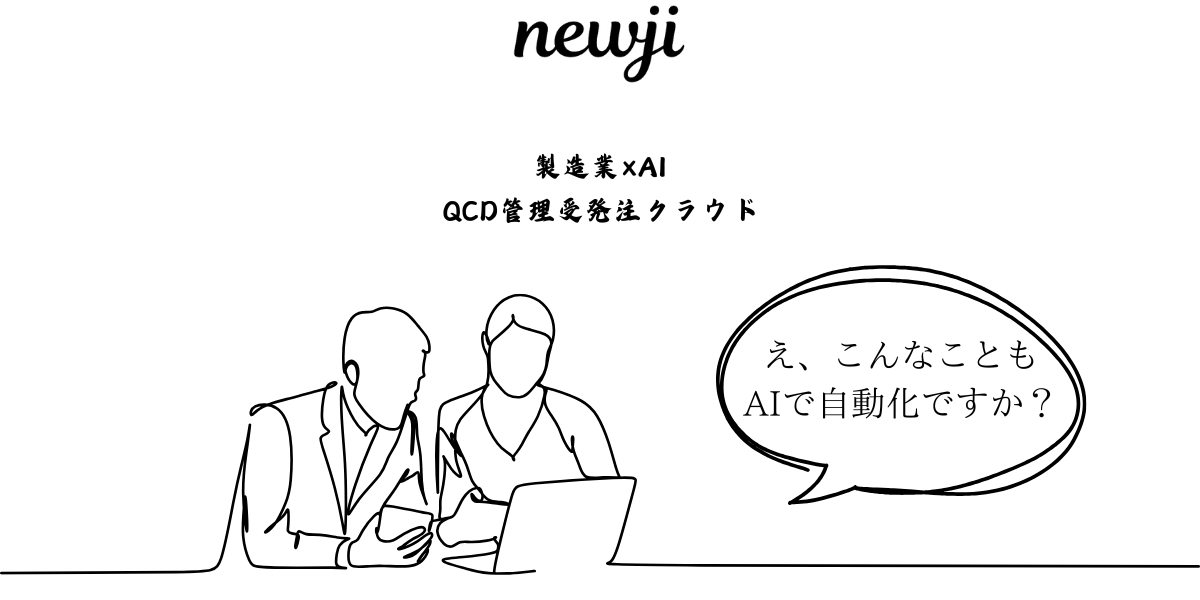
Defect prevention technology in printed circuit board mounting, micro bonding, and solder bonding
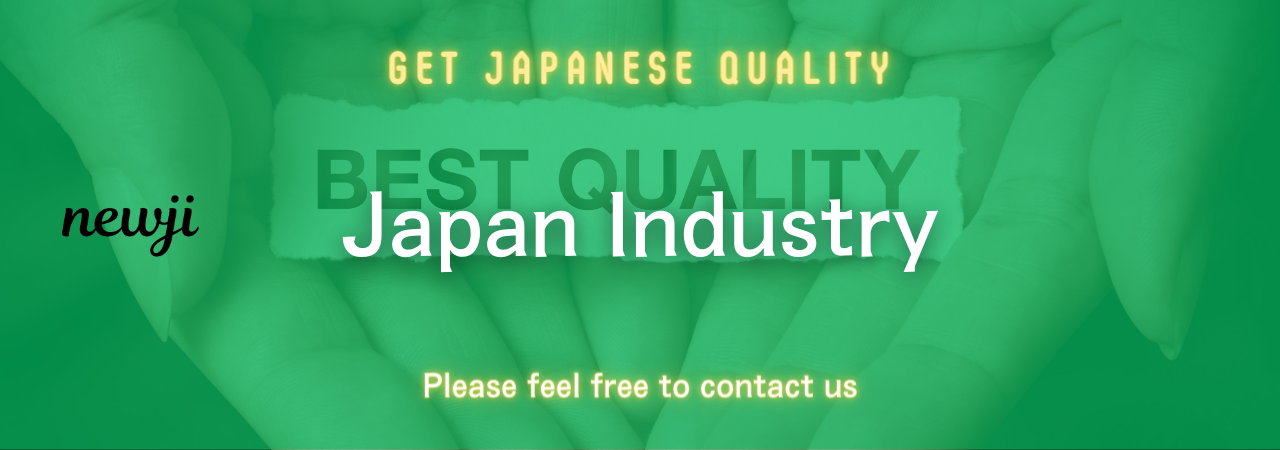
目次
Introduction to Defect Prevention in Circuit Board Manufacturing
In the world of electronics manufacturing, defects can lead to significant setbacks.
When it comes to printed circuit board (PCB) mounting, micro bonding, and solder bonding, even minor errors can compromise the integrity and functionality of an entire product.
Understanding defect prevention technologies is pivotal for enhancing product reliability and ensuring optimal performance.
This article delves into effective defect prevention strategies in PCB mounting, micro bonding, and solder bonding processes used in modern electronics manufacturing.
Understanding Printed Circuit Boards (PCBs)
PCBs are the backbone of most electronic devices.
They provide support and electrically connect various electronic components using conductive paths.
PCBs are used in a range of applications, from simple devices like toys to complex systems like industrial machinery.
Ensuring PCB functionality means preventing defects at every stage of its assembly, particularly during component mounting and bonding.
Common PCB Defects
Before exploring prevention technologies, let’s identify common PCB defects.
These include misaligned components, insufficient solder joints, open circuits, short circuits, and component damage.
Such defects can result from manufacturing errors, improper handling, or environmental factors.
Addressing these issues requires a proactive approach, utilizing technology and strict quality control measures.
Defect Prevention in PCB Mounting
PCB mounting is a critical step where various electronic components are placed onto the board.
Preventing defects at this stage requires precise techniques and modern technology.
Design for Manufacturability (DFM)
DFM is a vital strategy in defect prevention.
By designing PCBs with manufacturability in mind, potential defects can be minimized even before manufacturing begins.
This includes optimal layout of components, appropriate spacing, and proper pad sizes.
Using DFM principles ensures that the PCBs are easy to manufacture, reducing likelihood of defects.
Automated Optical Inspection (AOI)
AOI technology is employed during PCB assembly to inspect and identify defects early.
Cameras and software are used to detect alignment issues, missing components, or solder paste irregularities.
This swift identification prevents defective PCBs from advancing through production, ensuring high-quality output.
Enhancing Micro Bonding Processes
Micro bonding is essential for connecting tiny components, particularly in advanced electronics.
Ensuring precision in these processes is key to avoiding defects.
Wire Bonding Techniques
Proper wire bonding techniques are crucial in micro bonding.
This includes ensuring correct pressure, temperature, and time parameters during bonding.
Automated wire bonding machines provide accuracy and repeatability, significantly reducing the risk of human error.
Using gold or copper wires with precise bonding tools contributes to defect-free connections.
Environmental Control
The environment in which micro bonding takes place can drastically affect its quality.
Maintaining clean and controlled settings minimizes contamination and environmental variability, which could lead to defects.
Implementing HEPA filters and regulating humidity and temperature are effective measures in maintaining high-quality micro bonding outputs.
Optimizing Solder Bonding
Solder bonding is pivotal in securing components to a PCB.
Preventing defects such as cold joints, voids, or bridging is essential for ensuring functionality.
Reflow Soldering Process
The reflow soldering process is widely used for affixing SMD components.
Precision in temperature profiling is critical to avoid defects.
Preheating, soaking, and reflow phases must be carefully controlled to ensure proper melting and solidification of solder paste.
Employing high-precision reflow ovens can significantly enhance soldering quality.
Solder Paste Inspection (SPI)
SPI systems are crucial for preventing defects in solder bonding.
They assess solder paste deposits to ensure they meet specifications in volume and height.
By detecting anomalies early, SPI limits the reach of potential defects, contributing to a seamless soldering process.
Continuous Improvement and Training
Consistent learning and adaptation are vital for defect prevention.
Implementing feedback mechanisms and training staff to identify and rectify errors can lead to continuous improvement.
Regularly updating skills and knowledge on the latest technologies ensures that teams are equipped to prevent defects effectively.
Conclusion: A Systematic Approach to Defect Prevention
Defect prevention in PCB mounting, micro bonding, and solder bonding is integral to producing high-quality electronic products.
By employing technologies like AOI, SPI, and maintaining optimal manufacturing conditions, manufacturers can dramatically reduce the occurrence of defects.
Additionally, a focus on DFM and regular training empowers teams to contribute actively to defect-free production processes.
As technology evolves, staying ahead with these strategies is crucial for maintaining quality standards in the ever-competitive electronics industry.
資料ダウンロード
QCD管理受発注クラウド「newji」は、受発注部門で必要なQCD管理全てを備えた、現場特化型兼クラウド型の今世紀最高の受発注管理システムとなります。
ユーザー登録
受発注業務の効率化だけでなく、システムを導入することで、コスト削減や製品・資材のステータス可視化のほか、属人化していた受発注情報の共有化による内部不正防止や統制にも役立ちます。
NEWJI DX
製造業に特化したデジタルトランスフォーメーション(DX)の実現を目指す請負開発型のコンサルティングサービスです。AI、iPaaS、および先端の技術を駆使して、製造プロセスの効率化、業務効率化、チームワーク強化、コスト削減、品質向上を実現します。このサービスは、製造業の課題を深く理解し、それに対する最適なデジタルソリューションを提供することで、企業が持続的な成長とイノベーションを達成できるようサポートします。
製造業ニュース解説
製造業、主に購買・調達部門にお勤めの方々に向けた情報を配信しております。
新任の方やベテランの方、管理職を対象とした幅広いコンテンツをご用意しております。
お問い合わせ
コストダウンが利益に直結する術だと理解していても、なかなか前に進めることができない状況。そんな時は、newjiのコストダウン自動化機能で大きく利益貢献しよう!
(β版非公開)