- お役立ち記事
- Description of resolver technology and accuracy of rotational position sensing
月間76,176名の
製造業ご担当者様が閲覧しています*
*2025年3月31日現在のGoogle Analyticsのデータより
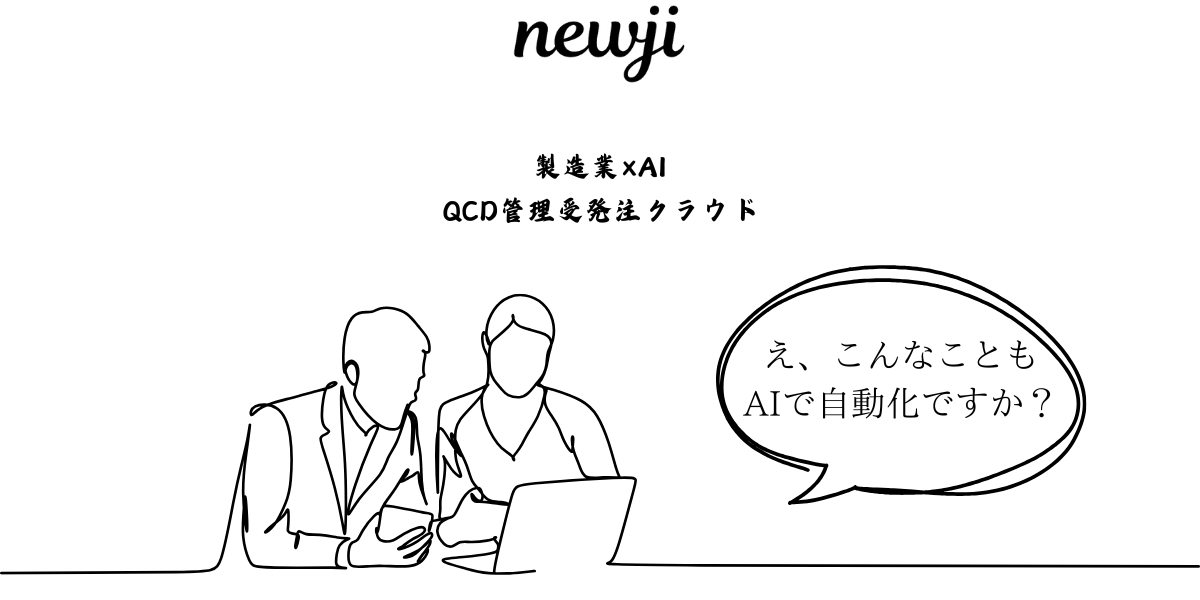
Description of resolver technology and accuracy of rotational position sensing
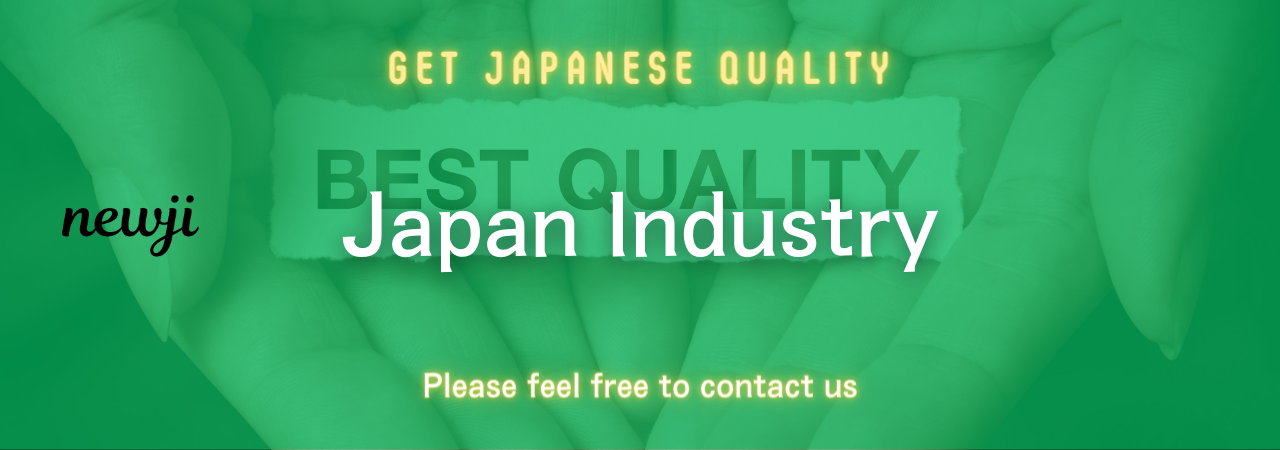
目次
Understanding Resolver Technology
Resolvers are electromechanical devices used to measure the rotational position of a shaft.
They provide precise angle measurements, making them crucial in many applications such as robotics, aerospace, and industrial automation.
Despite being an older technology, resolvers remain popular due to their reliability and accuracy in harsh environments.
How Resolvers Work
Resolvers operate based on the principles of electromagnetic induction.
A typical resolver consists of a rotor and stator windings.
When an AC signal is applied to the rotor winding, it induces voltages in the stator windings.
These induced voltages vary as a function of the rotor’s position, allowing the resolver to determine the exact angular position.
The stator usually has two windings positioned 90 degrees apart.
When the rotor is energized, it couples energy to the stator.
The output voltages from the stator windings are sinusoidal signals whose amplitudes are proportional to the cosine and sine of the rotor angle.
By processing these signals, the exact angle can be calculated.
Advantages of Resolvers
Resolvers offer several benefits that make them suitable for various applications.
Firstly, they have a robust construction, making them highly durable and resistant to extreme temperatures, vibrations, and contaminants.
This durability ensures consistent performance in challenging environments.
Secondly, resolvers do not require an onboard microprocessor or special conditioning.
They are purely analog devices, which makes them less susceptible to digital signal issues like noise and latency.
Lastly, the accuracy of resolvers is very high.
They can provide precise angular measurement with minimal drift over time.
This accuracy is maintained even under challenging conditions, ensuring reliable performance across various applications.
Applications of Resolvers
Due to their reliability and accuracy, resolvers find applications in many industries.
In aerospace, they are used to control flight surfaces, engine positions, and landing gear mechanisms.
In robotics, they assist in precise arm movements and positioning.
In industrial automation, resolvers monitor the position of motors and machine parts.
They also contribute to the accuracy of CNC machines and other precision tools.
Because of their robust design, resolvers excel in industries where harsh environmental conditions are prevalent.
Accuracy of Rotational Position Sensing
The accuracy of rotational position sensing is vital in many applications.
Resolvers are known for their high accuracy, which is primarily due to their analog nature.
Digital encoders, while popular, can introduce errors due to quantization and resolution limits.
Factors Affecting Accuracy
Several factors contribute to the accuracy of resolvers in rotational position sensing.
The quality of the resolver’s construction—such as the precision of the windings and the assembly—plays a significant role.
An accurately constructed resolver can minimize errors due to mechanical imperfections.
The quality of the signal processing electronics also impacts accuracy.
High-quality signal conditioning can enhance the resolver’s performance by accurately converting analog signals to digital data.
Poor quality electronics can introduce noise and errors that degrade accuracy.
Environmental factors such as temperature, vibration, and contamination can affect accuracy.
Resolvers are designed to operate in harsh environments, but excessive exposure to extreme conditions can still impact performance.
Regular maintenance and proper installation can mitigate these effects.
Improving Accuracy
Improving the accuracy of rotational position sensing using resolvers involves several strategies.
Firstly, using high-quality components and precise manufacturing processes can significantly enhance accuracy.
Ensuring that the resolver is correctly aligned when installed is also crucial.
Misalignment can introduce errors that degrade performance.
Secondly, high-quality signal processing electronics must be used.
Advanced filtering and error-correction algorithms can improve the accuracy of angle measurements.
Ensuring that the electronics are shielded from noise and electromagnetic interference is also essential.
Thirdly, proper calibration and regular maintenance are necessary.
Calibrating the resolver to account for any system-specific factors can enhance accuracy.
Regular maintenance can ensure the resolver operates within its specified parameters, reducing the likelihood of errors.
Conclusion
Resolvers remain a highly reliable and accurate technology for measuring rotational positions.
Their robust design and excellent performance in harsh environments make them indispensable in industries like aerospace, robotics, and industrial automation.
By understanding the factors affecting their accuracy and implementing strategies to enhance performance, resolver technology can provide precise angular measurements necessary for a wide range of applications.
資料ダウンロード
QCD管理受発注クラウド「newji」は、受発注部門で必要なQCD管理全てを備えた、現場特化型兼クラウド型の今世紀最高の受発注管理システムとなります。
ユーザー登録
受発注業務の効率化だけでなく、システムを導入することで、コスト削減や製品・資材のステータス可視化のほか、属人化していた受発注情報の共有化による内部不正防止や統制にも役立ちます。
NEWJI DX
製造業に特化したデジタルトランスフォーメーション(DX)の実現を目指す請負開発型のコンサルティングサービスです。AI、iPaaS、および先端の技術を駆使して、製造プロセスの効率化、業務効率化、チームワーク強化、コスト削減、品質向上を実現します。このサービスは、製造業の課題を深く理解し、それに対する最適なデジタルソリューションを提供することで、企業が持続的な成長とイノベーションを達成できるようサポートします。
製造業ニュース解説
製造業、主に購買・調達部門にお勤めの方々に向けた情報を配信しております。
新任の方やベテランの方、管理職を対象とした幅広いコンテンツをご用意しております。
お問い合わせ
コストダウンが利益に直結する術だと理解していても、なかなか前に進めることができない状況。そんな時は、newjiのコストダウン自動化機能で大きく利益貢献しよう!
(β版非公開)