- お役立ち記事
- Design and OEM Manufacturing of Gears for High-Performance Machine Parts
月間76,176名の
製造業ご担当者様が閲覧しています*
*2025年3月31日現在のGoogle Analyticsのデータより
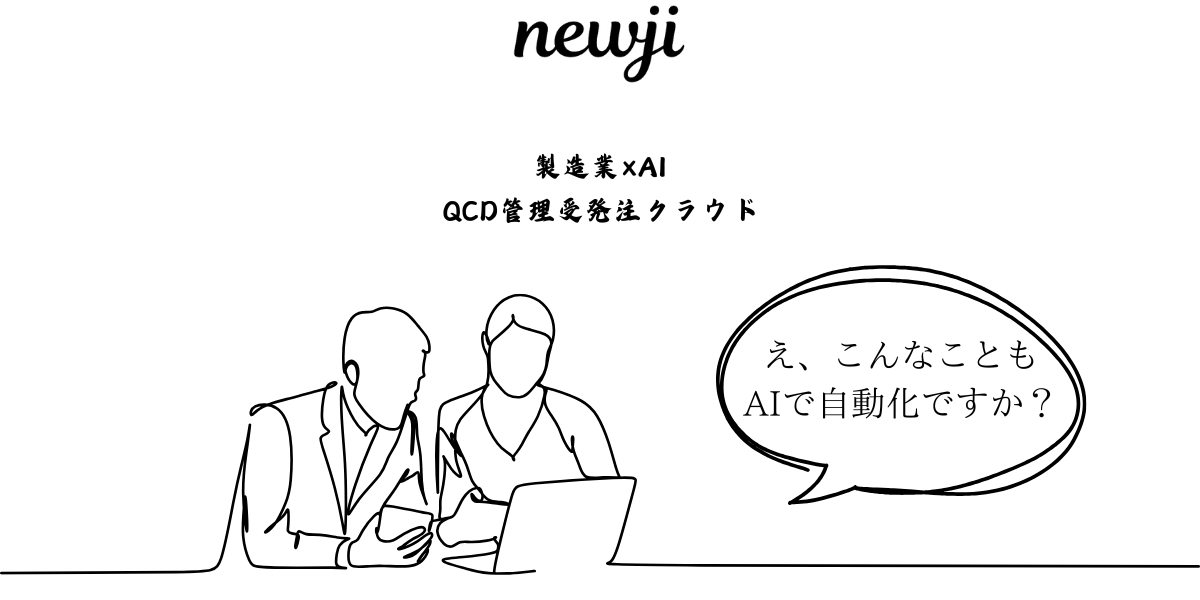
Design and OEM Manufacturing of Gears for High-Performance Machine Parts
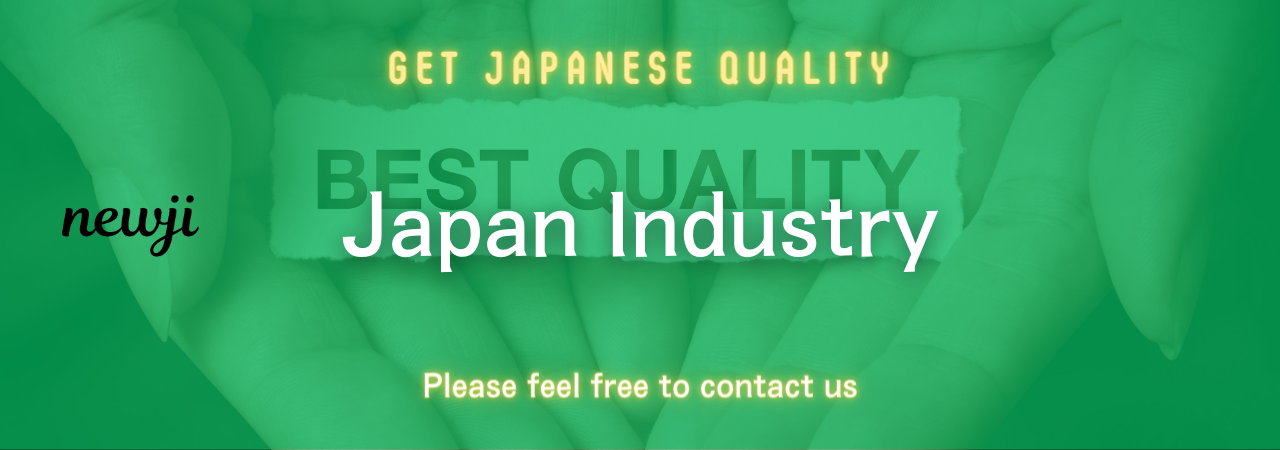
目次
Understanding Gear Design
Gears are a vital part of any machine that requires the transfer of motion and power.
They come in various shapes and sizes, all designed to perform specific tasks.
But what goes into designing these important components?
First, it’s crucial to understand the different types of gears and their unique functions.
Gear design involves several steps, starting from selecting the right type of gear for the application.
Some common types include spur gears, helical gears, bevel gears, and worm gears.
Each type has its own advantages and disadvantages, depending on factors like load capacity, speed, and efficiency.
When designing gears, engineers must also consider the materials used.
The material affects the gears’ strength, durability, and overall performance.
Common materials for gears include steel, brass, and plastic.
After selecting the right type and material, engineers use computer software to create detailed gear designs.
These designs are simulated to ensure they meet performance requirements.
OEM Manufacturing of Gears
OEM stands for Original Equipment Manufacturer.
OEM manufacturers produce gears that are used in other companies’ products.
This means the gears must be high-quality and precisely made to fit and function perfectly in various machines and devices.
The OEM manufacturing process starts with a thorough understanding of the gear design specifications.
These specifications include the gear’s dimensions, material, and performance requirements.
Once the design is finalized, the manufacturing process begins.
The first stage in gear manufacturing is cutting or shaping the raw material into the desired gear shape.
This can be done through various methods like hobbing, milling, or forging.
Each method has its own advantages and is chosen based on the type of gear and the required precision.
After shaping, the gears undergo heat treatment to enhance their strength and durability.
This involves heating the gears to high temperatures and then cooling them in a controlled manner.
Heat treatment is particularly important for gears that will be used in high-stress environments, as it ensures they can withstand heavy loads and high speeds.
Ensuring High Performance
For gears to function effectively in high-performance machine parts, they must meet strict quality standards.
This involves rigorous testing at various stages of production.
One common test is the hardness test, which measures the gear’s resistance to becoming deformed.
Harder gears are generally more durable and can handle higher loads.
Another crucial test is the accuracy test, which checks if the gear’s teeth are perfectly shaped and spaced.
Inaccurate teeth can lead to inefficient power transmission and increased wear and tear.
Engineers use precision measuring tools and software to ensure the gears meet the required accuracy standards.
Finally, gears are tested for their overall performance.
This involves running the gears in simulated operating conditions to check for factors like noise, vibration, and efficiency.
Only gears that pass all these tests are approved for use in high-performance machine parts.
Applications of High-Performance Gears
High-performance gears are used in a variety of applications, from automotive engines to industrial machinery.
In the automotive industry, gears are essential for transmitting power from the engine to the wheels.
This requires gears that can handle high speeds and heavy loads while maintaining efficiency.
In industrial machinery, gears are used to drive various components like conveyor belts, pumps, and mixers.
These applications often involve continuous operation, so the gears must be both durable and reliable.
High-performance gears help ensure that these machines run smoothly and efficiently.
Another important application is in robotics, where gears are used in the joints of robotic arms and legs.
These gears must be lightweight yet strong enough to handle rapid and precise movements.
High-performance gears are essential for achieving the high levels of precision required in robotic applications.
The Future of Gear Design and Manufacturing
The field of gear design and manufacturing is constantly evolving, driven by advancements in technology and materials.
One promising development is the use of advanced materials like carbon fiber composites.
These materials offer a higher strength-to-weight ratio compared to traditional materials, making them ideal for high-performance applications.
Another exciting trend is the use of 3D printing in gear manufacturing.
3D printing allows for the production of complex gear shapes that would be difficult or impossible to achieve with traditional methods.
This technology also offers the potential for rapid prototyping, enabling engineers to quickly test and refine new gear designs.
Finally, advancements in computer-aided design (CAD) and simulation software are making it easier for engineers to create and test innovative gear designs.
These tools allow for more accurate simulations of real-world operating conditions, leading to better-performing gears.
In conclusion, the design and OEM manufacturing of gears for high-performance machine parts involves a combination of careful design, precise manufacturing, and rigorous testing.
As technology continues to advance, we can expect even more efficient and durable gears that will help power the machines of the future.
資料ダウンロード
QCD管理受発注クラウド「newji」は、受発注部門で必要なQCD管理全てを備えた、現場特化型兼クラウド型の今世紀最高の受発注管理システムとなります。
ユーザー登録
受発注業務の効率化だけでなく、システムを導入することで、コスト削減や製品・資材のステータス可視化のほか、属人化していた受発注情報の共有化による内部不正防止や統制にも役立ちます。
NEWJI DX
製造業に特化したデジタルトランスフォーメーション(DX)の実現を目指す請負開発型のコンサルティングサービスです。AI、iPaaS、および先端の技術を駆使して、製造プロセスの効率化、業務効率化、チームワーク強化、コスト削減、品質向上を実現します。このサービスは、製造業の課題を深く理解し、それに対する最適なデジタルソリューションを提供することで、企業が持続的な成長とイノベーションを達成できるようサポートします。
製造業ニュース解説
製造業、主に購買・調達部門にお勤めの方々に向けた情報を配信しております。
新任の方やベテランの方、管理職を対象とした幅広いコンテンツをご用意しております。
お問い合わせ
コストダウンが利益に直結する術だと理解していても、なかなか前に進めることができない状況。そんな時は、newjiのコストダウン自動化機能で大きく利益貢献しよう!
(β版非公開)