- お役立ち記事
- Design and optimization using design of experiments
月間76,176名の
製造業ご担当者様が閲覧しています*
*2025年3月31日現在のGoogle Analyticsのデータより
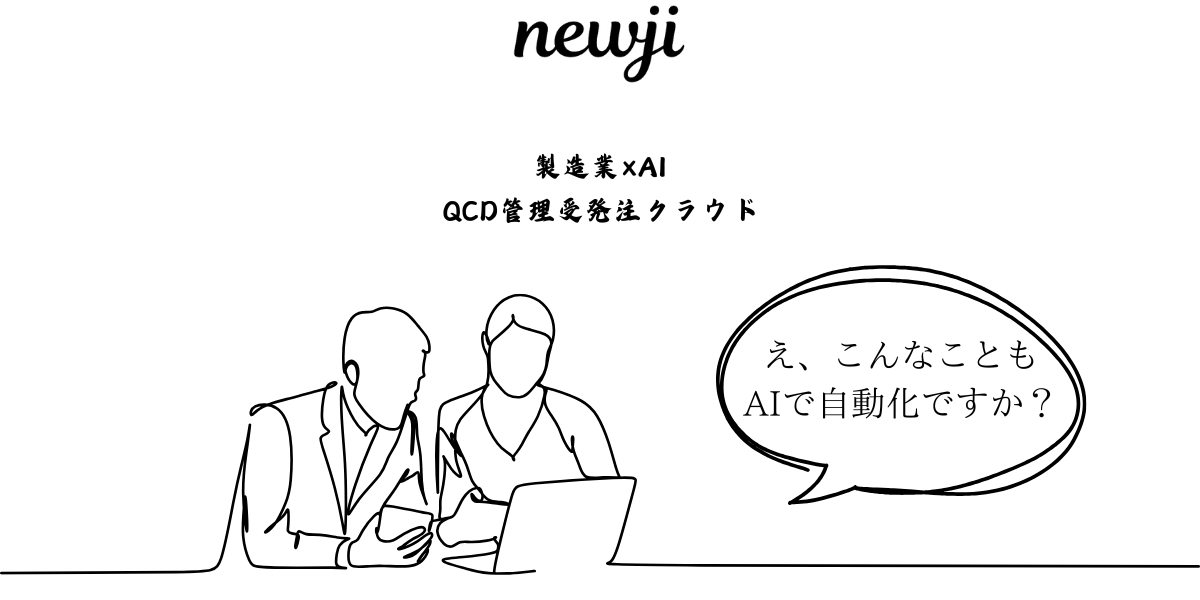
Design and optimization using design of experiments
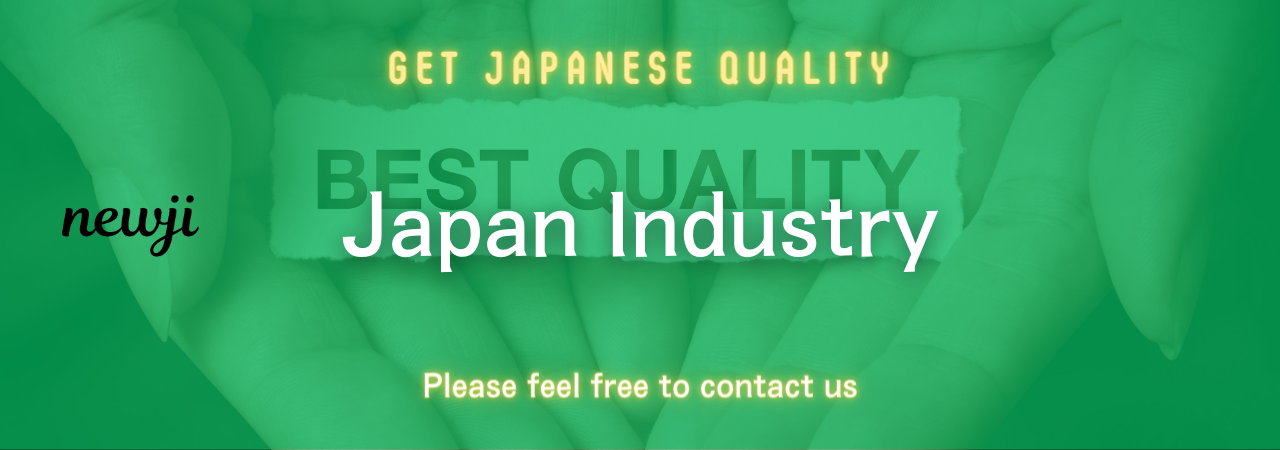
目次
Understanding Design of Experiments (DOE)
Design of Experiments (DOE) is a systematic approach used to determine the relationship between factors affecting a process and the output of that process.
This methodology is widely used to assess the impact of different variables and to find optimal conditions for experiments and processes.
By using DOE, researchers and engineers can evaluate multiple variables simultaneously, reducing the number of trials required to understand these relationships.
The efficient design of experiments helps in making informed decisions, optimizing processes, and achieving desired outcomes.
Benefits of Using DOE
The primary advantage of using DOE is its ability to identify critical factors without requiring exhaustive testing.
Traditional methods often involve adjusting one variable at a time, which can be time-consuming and may miss interactions between variables.
In contrast, DOE allows simultaneous examination of several factors, providing insights into how they interact and affect the outcome.
Further benefits include:
– **Efficiency**: Fewer experiments are needed to obtain meaningful data.
– **Insights**: Identifies interactions between factors that might be missed in simpler approaches.
– **Optimization**: Allows finding of optimal conditions and settings more quickly.
– **Cost-effectiveness**: Reduces time and resources needed for experimentation.
Key Concepts in DOE
Understanding DOE involves familiarizing yourself with some key concepts and terms used in this methodology.
– **Factors**: These are the variables that are changed in an experiment. Each factor can have different levels or settings.
– **Levels**: These represent the values that a factor can take. For example, temperature might have high, medium, and low levels.
– **Response**: The output or result measured in the experiment. This is affected by the different factors and their levels.
– **Interactions**: A scenario where the effect of one factor depends on the level of another factor. Discovering these interactions is critical for understanding complex processes.
– **Replicates**: Repeated trials at the same combination of factor levels to ensure reliability and validity of the results.
Designing Experiments
Designing effective experiments requires careful planning and consideration of the objectives, factors, and resources available.
Several types of experimental designs are commonly used in DOE, each suited to different applications and complexity levels.
Full Factorial Design
A full factorial design examines all possible combinations of factor levels.
This type of design is comprehensive and allows for complete understanding of interactions between all factors.
However, it can become impractical if the number of factors or levels is too high due to the sheer number of experiments required.
Fractional Factorial Design
Fractional factorial designs are a subset of the full factorial design, examining only a fraction of all possible combinations.
This approach reduces the number of experiments needed while still providing sufficient information to identify important factors and interactions.
It is especially useful when resources are limited or when the number of factors is large.
Response Surface Methodology
Response Surface Methodology (RSM) is useful for modeling and analyzing the relationship between several variables and one or more response variables.
RSM aims to optimize these responses and is particularly effective once initial significant factors are identified.
The method uses mathematical models to predict optimal conditions, allowing researchers and engineers to fine-tune processes.
Taguchi Methods
Taguchi methods focus on improving product quality and performance through robust design.
These methods emphasize minimizing variations and finding factor levels that produce consistent results despite external noise.
Taguchi methods are particularly effective in manufacturing settings, where maintaining quality across varying conditions is crucial.
Optimization Using DOE
Optimization using Design of Experiments involves finding settings of factors that maximize or minimize a desired response.
It requires interpreting the results of the experiments to identify crucial interactions and effects.
Steps to Optimize
1. **Define Objectives**: Clearly outline the goals of the optimization, such as improving efficiency, reducing cost, or enhancing quality.
2. **Select Factors and Levels**: Choose which variables to test and their respective settings. Ensure these are within the control of the experimenter and relevant to the objectives.
3. **Choose Design Strategy**: Decide on the appropriate type of design, such as full factorial, fractional factorial, or RSM, based on resources and objectives.
4. **Conduct Experiments**: Carry out the experiments according to the design plan, ensuring accuracy and consistency in measurements.
5. **Analyze Data**: Use statistical methods to evaluate the results, focusing on identifying significant factors and interactions that impact the response.
6. **Develop a Model**: Construct a mathematical model that describes the relationship between factors and responses. This model is used for predicting outcomes of different factor combinations.
7. **Test Predictions**: Validate the model by testing additional experiments to confirm predicted outcomes match actual results.
8. **Implement Optimal Conditions**: Apply the optimized settings to the process or product to achieve the desired improvement.
Conclusion
Design of Experiments provides a powerful framework for understanding and optimizing processes.
By systematically exploring the influence of multiple factors on an output, DOE enables organizations to enhance efficiency, quality, and performance.
For any organization seeking to innovate and improve, mastering DOE methodologies is indispensable for driving informed decisions and achieving competitive advantages.
資料ダウンロード
QCD管理受発注クラウド「newji」は、受発注部門で必要なQCD管理全てを備えた、現場特化型兼クラウド型の今世紀最高の受発注管理システムとなります。
ユーザー登録
受発注業務の効率化だけでなく、システムを導入することで、コスト削減や製品・資材のステータス可視化のほか、属人化していた受発注情報の共有化による内部不正防止や統制にも役立ちます。
NEWJI DX
製造業に特化したデジタルトランスフォーメーション(DX)の実現を目指す請負開発型のコンサルティングサービスです。AI、iPaaS、および先端の技術を駆使して、製造プロセスの効率化、業務効率化、チームワーク強化、コスト削減、品質向上を実現します。このサービスは、製造業の課題を深く理解し、それに対する最適なデジタルソリューションを提供することで、企業が持続的な成長とイノベーションを達成できるようサポートします。
製造業ニュース解説
製造業、主に購買・調達部門にお勤めの方々に向けた情報を配信しております。
新任の方やベテランの方、管理職を対象とした幅広いコンテンツをご用意しております。
お問い合わせ
コストダウンが利益に直結する術だと理解していても、なかなか前に進めることができない状況。そんな時は、newjiのコストダウン自動化機能で大きく利益貢献しよう!
(β版非公開)