- お役立ち記事
- Design/development and troubleshooting using the Taguchi method (parameter design)
月間76,176名の
製造業ご担当者様が閲覧しています*
*2025年3月31日現在のGoogle Analyticsのデータより
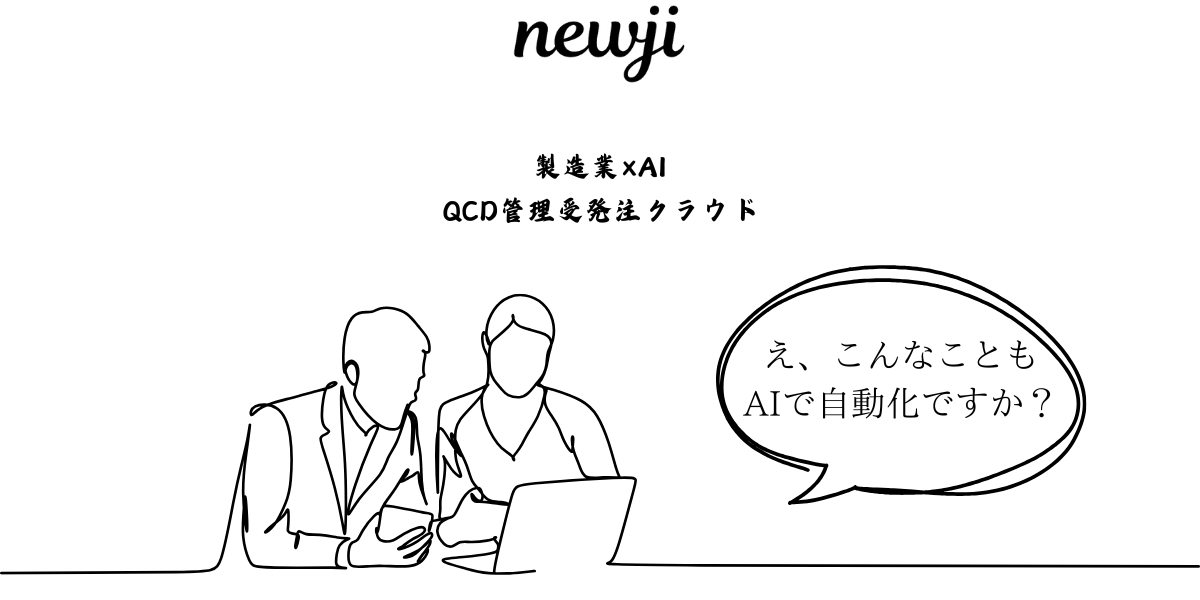
Design/development and troubleshooting using the Taguchi method (parameter design)
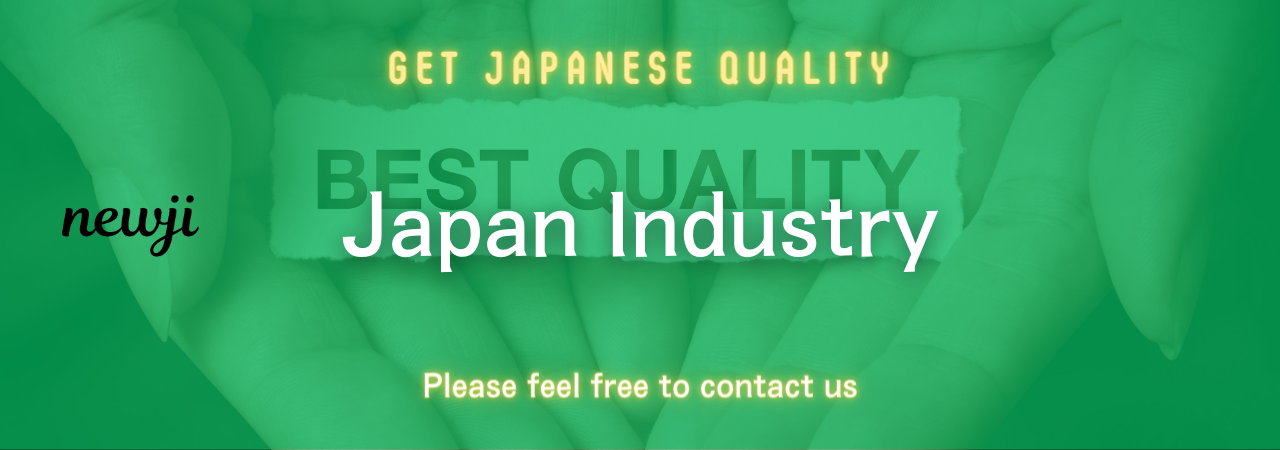
目次
Understanding the Taguchi Method
The Taguchi Method is a statistical approach used in designing and optimizing processes and products.
Named after its creator, Dr. Genichi Taguchi, this method emphasizes improving the quality and performance while reducing production costs and time.
One of the most unique features of the Taguchi Method is its focus on robustness—the ability of a product or process to perform consistently under varying conditions.
What Is Parameter Design?
At the core of the Taguchi Method is parameter design.
This aspect involves selecting the best parameters for a product or process to optimize its performance.
The goal is to make the product or process resistant to variations that are unavoidable during manufacturing or in use.
Parameter design helps in identifying the optimal conditions that lead to the desired output.
Implementing the Taguchi Method
The application of the Taguchi Method involves a series of steps.
Firstly, you identify the main factors affecting the performance of your process or product.
These include both controllable factors (parameters you can adjust) and noise factors (uncontrollable variables that cause variation).
Next, you conduct experiments.
These are usually orthogonal arrays designed to efficiently test different combinations of factors.
Orthogonal arrays help in simplifying the experimentation process by reducing the number of experiments needed to identify the best parameters.
After conducting experiments, the data collected is analyzed to determine the optimal settings for these parameters.
The Taguchi Method uses the signal-to-noise (S/N) ratio as a metric to evaluate the performance of different settings.
A higher S/N ratio indicates better performance stability under varying conditions.
Benefits of the Taguchi Method
The primary benefit of the Taguchi Method is its ability to enhance product quality and process efficiency while minimizing costs.
By focusing on parameter design, the method reduces the variability of product performance.
This robustness ensures that products perform well despite environmental and manufacturing fluctuations.
Additionally, the Taguchi Method provides a structured experimental approach, ensuring that you gain maximum information from minimum testing.
Its systematic analysis helps in getting clear insights into how different parameters interact and affect the outcome.
As a result, companies can significantly reduce waste, rework, and warranty claims.
Examples of Taguchi Method in Practice
The Taguchi Method has been widely adopted across various industries.
In the automotive industry, companies often use it to design engines and other components that perform consistently under diverse driving conditions.
In electronics, the method helps in developing circuits and systems that maintain quality even in fluctuating temperatures and power supply.
For example, a car manufacturer might use the Taguchi Method to optimize the design of a braking system.
By experimenting with various materials and configurations under varying road conditions, they determine the combination that offers the best performance and durability.
Another example in the medical device industry may involve optimizing the parameters for manufacturing a prosthetic limb to ensure it remains functional under different user conditions.
Troubleshooting with the Taguchi Method
In addition to design and development, the Taguchi Method is invaluable for troubleshooting existing products and processes.
When a product fails to meet performance specifications, the method can identify the key factors causing deviations.
By analyzing the effects of various parameters and conditions, companies can pinpoint the source of the problem.
The troubleshooting process starts by defining the problem clearly.
A team identifies the factors that could influence this issue, including potential noise factors.
Orthogonal arrays are then used to design a series of experiments to investigate the possible causes.
After conducting these experiments, the data is analyzed to identify which factors have the most significant impact on the failure.
Once the disturbing factors are identified, adjustments can be made to the controllable parameters to improve robustness against these disturbances, often leading to an innovative solution that provides better performance consistently.
Challenges and Considerations
While the Taguchi Method offers numerous benefits, it does have its own set of challenges.
The most notable is the need for a deep understanding of the factors involved in the product or process being examined.
Gathering accurate data and setting up proper experiments can be complicated for teams inexperienced with statistical methodologies.
Another consideration is that this method assumes interactions between factors can be ignored, which might not always be the case.
In scenarios where interactions significantly affect performance, additional analysis might be required.
Despite these challenges, the Taguchi Method remains a powerful tool for improving quality and performance.
By focusing on optimization and robustness, it provides a practical way to maintain high standards while navigating the complexities of variability in manufacturing and application environments.
Conclusion
The Taguchi Method is a valuable approach for anyone involved in design, development, and troubleshooting.
Its clear focus on parameter design offers a robust way to optimize products and processes, making them more resilient to variations.
By efficiently identifying optimal conditions, this method enhances quality, reduces costs, and delivers more consistent performance.
Industries ranging from automotive to electronics leverage its principles to maintain high quality and meet consumer expectations.
While it may require expertise to implement effectively, the long-term benefits often far outweigh the initial investments in training and setup.
For those tasked with improving and ensuring quality and reliability, embracing the Taguchi Method could be a significant step forward.
資料ダウンロード
QCD管理受発注クラウド「newji」は、受発注部門で必要なQCD管理全てを備えた、現場特化型兼クラウド型の今世紀最高の受発注管理システムとなります。
ユーザー登録
受発注業務の効率化だけでなく、システムを導入することで、コスト削減や製品・資材のステータス可視化のほか、属人化していた受発注情報の共有化による内部不正防止や統制にも役立ちます。
NEWJI DX
製造業に特化したデジタルトランスフォーメーション(DX)の実現を目指す請負開発型のコンサルティングサービスです。AI、iPaaS、および先端の技術を駆使して、製造プロセスの効率化、業務効率化、チームワーク強化、コスト削減、品質向上を実現します。このサービスは、製造業の課題を深く理解し、それに対する最適なデジタルソリューションを提供することで、企業が持続的な成長とイノベーションを達成できるようサポートします。
製造業ニュース解説
製造業、主に購買・調達部門にお勤めの方々に向けた情報を配信しております。
新任の方やベテランの方、管理職を対象とした幅広いコンテンツをご用意しております。
お問い合わせ
コストダウンが利益に直結する術だと理解していても、なかなか前に進めることができない状況。そんな時は、newjiのコストダウン自動化機能で大きく利益貢献しよう!
(β版非公開)