- お役立ち記事
- Design process to eliminate rework and how to use 3D CAD/CAE for design verification
月間76,176名の
製造業ご担当者様が閲覧しています*
*2025年3月31日現在のGoogle Analyticsのデータより
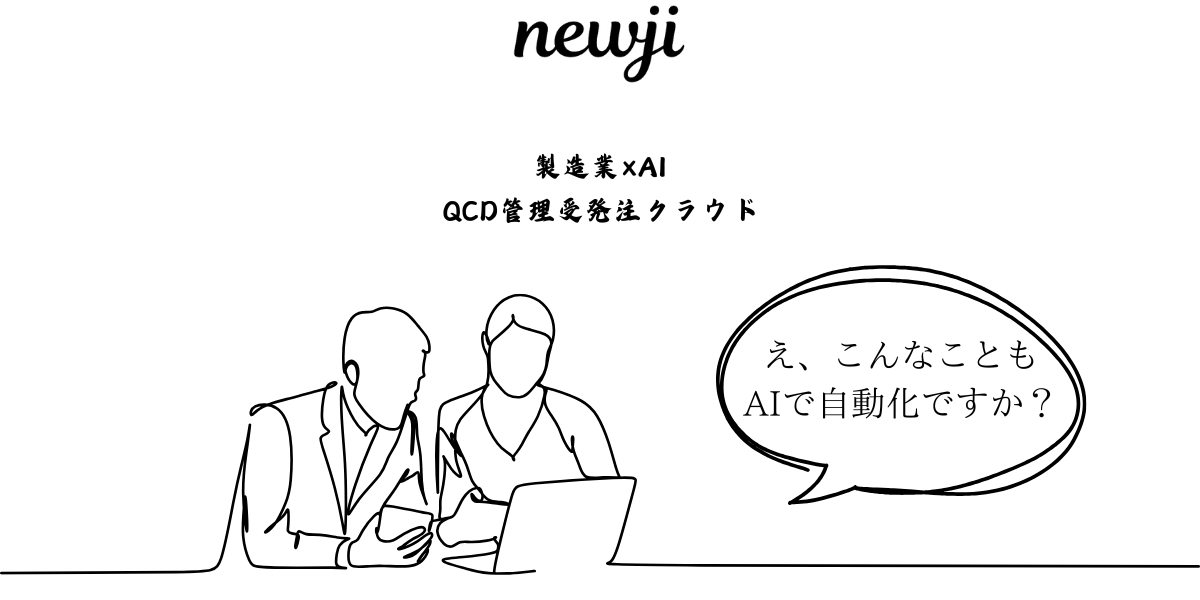
Design process to eliminate rework and how to use 3D CAD/CAE for design verification
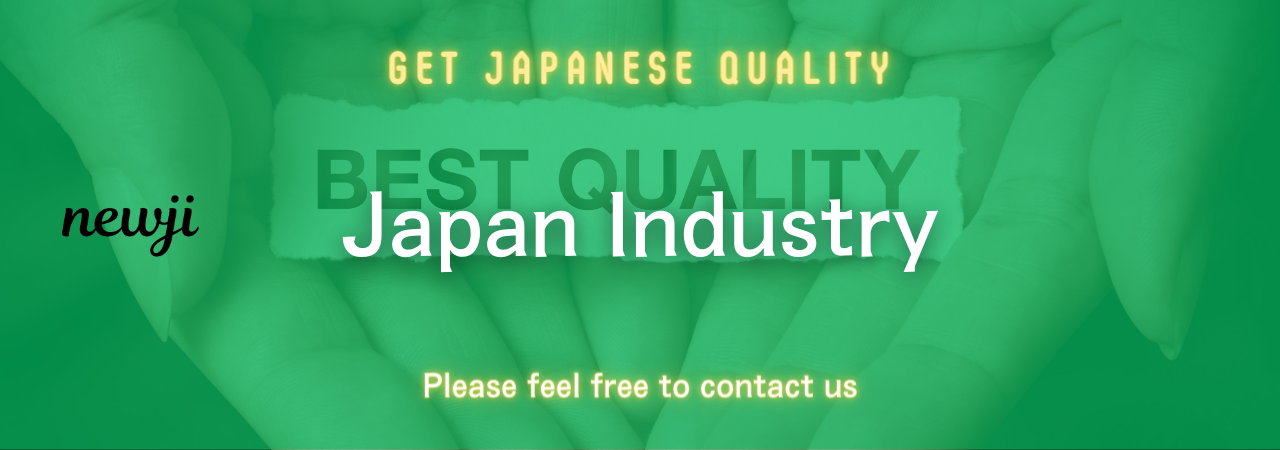
目次
Understanding the Design Process and the Role of 3D CAD/CAE
Design processes in engineering and manufacturing are intricate, involving multiple stages that require precision and attention to detail.
One of the primary goals in this process is to eliminate rework, which not only saves time and resources but also enhances overall efficiency.
A key factor in achieving this goal is the use of 3D CAD (Computer-Aided Design) and CAE (Computer-Aided Engineering) tools for design verification.
These powerful technologies enable engineers to visualize, simulate, and validate their designs before moving to production.
What is Rework and Why Should It Be Eliminated?
Rework refers to the process of revising or correcting a design after it has gone through some stages of manufacturing.
This can be due to errors, design flaws, or unexpected issues that arise.
Rework can significantly increase costs, extend project timelines, and consume additional resources.
Moreover, frequent rework can lead to wastage of materials and a decrease in the quality of the final product.
By eliminating or minimizing rework, companies can achieve greater productivity and maintain a competitive edge in the market.
The Importance of Design Verification
Design verification is the process of ensuring that a design meets all specified requirements and functions as intended.
It is a crucial step in the design process because it helps identify potential issues early on, reducing the likelihood of rework.
How Design Verification Works
Design verification typically involves a series of checks and validations.
These can include reviews, simulations, and tests designed to confirm that the design will operate under intended conditions.
Verification can be done through various means, including manual checks, physical prototypes, and increasingly through digital simulations using tools like 3D CAD and CAE.
Benefits of Efficient Design Verification
– **Early Error Detection:** By verifying designs early in the process, errors can be detected and corrected before they result in costly rework.
– **Improved Quality:** Efficient verification helps ensure that the final product meets high-quality standards and performs as expected.
– **Cost Savings:** Detecting and fixing errors earlier minimizes the resources spent on corrections, reducing the overall project cost.
– **Faster Time to Market:** With fewer errors, projects progress more smoothly, leading to quicker completion and delivery times.
Utilizing 3D CAD in the Design Process
3D CAD software is a vital component of modern design processes, offering a wide range of tools to create detailed digital models of products.
3D CAD Capabilities
– **Visualization:** CAD allows designers to create and manipulate detailed models, helping them visualize the product more clearly than 2D sketches or blueprints.
– **Collaboration:** With CAD, teams can easily share designs with stakeholders for feedback and approval, fostering collaboration across different departments.
– **Flexibility:** Designers can quickly change models in CAD without needing to redraw entire sections, making it easier to explore and iterate design options.
The Role of CAD in Eliminating Rework
By providing a comprehensive view of the design, 3D CAD helps identify potential problems before they reach the manufacturing floor.
Designs can be reviewed and adjusted in the digital space, reducing the need for physical prototypes and subsequent rework.
This not only speeds up the design process but also contributes to better resource management and cost efficiency.
The Power of CAE for Design Verification
While CAD focuses on the design aspect, CAE is used for simulating and analyzing how a product will perform.
CAE tools play a crucial role in verifying that the design will meet performance expectations and be reliable in real-world conditions.
Capabilities of CAE
– **Simulation:** CAE software can simulate physical phenomena such as stress, heat transfer, and fluid dynamics.
This helps predict how a product will behave under various conditions.
– **Optimization:** It allows for the testing of different design variations to find the optimal configuration that meets all requirements.
– **Validation:** CAE aids in validating designs against industry standards and regulations, ensuring compliance and reducing risks.
Reducing Rework with CAE
By leveraging simulations, CAE allows designers to test multiple scenarios and detect potential failures before production.
This critical step ensures that the design is robust and that potential issues are resolved early, thereby reducing the chances of rework after production begins.
Integrating 3D CAD/CAE in the Design Process
The integration of 3D CAD and CAE offers a comprehensive approach to design, from initial visualization to final verification.
Benefits of Integration
– **Streamlined Workflow:** Combining CAD and CAE provides a seamless workflow that covers all aspects of design and verification.
– **Enhanced Collaboration:** Integrated tools offer better collaboration, with teams able to share data and insights more effectively.
– **Increased Efficiency:** By connecting design and simulation tools, teams can work more efficiently and make informed decisions faster.
– **Data Consistency:** Integrated systems maintain data integrity across processes, reducing errors and ensuring consistent results.
Best Practices for Implementation
– **Training and Development:** Ensure that your team is well-trained in both CAD and CAE tools, and encourage continual learning to keep up with new features and technologies.
– **Cross-Department Coordination:** Foster collaboration between design, engineering, and production teams to leverage insights from various stages of the process.
– **Incremental Implementation:** Start by integrating one aspect of CAD or CAE and gradually expand the integration to cover more processes as your team becomes comfortable.
In conclusion, by utilizing 3D CAD and CAE tools for design verification, companies can significantly reduce rework and enhance the overall design process.
This not only leads to better-quality products but also ensures efficient use of resources and quicker delivery to market, providing a substantial competitive advantage.
資料ダウンロード
QCD管理受発注クラウド「newji」は、受発注部門で必要なQCD管理全てを備えた、現場特化型兼クラウド型の今世紀最高の受発注管理システムとなります。
ユーザー登録
受発注業務の効率化だけでなく、システムを導入することで、コスト削減や製品・資材のステータス可視化のほか、属人化していた受発注情報の共有化による内部不正防止や統制にも役立ちます。
NEWJI DX
製造業に特化したデジタルトランスフォーメーション(DX)の実現を目指す請負開発型のコンサルティングサービスです。AI、iPaaS、および先端の技術を駆使して、製造プロセスの効率化、業務効率化、チームワーク強化、コスト削減、品質向上を実現します。このサービスは、製造業の課題を深く理解し、それに対する最適なデジタルソリューションを提供することで、企業が持続的な成長とイノベーションを達成できるようサポートします。
製造業ニュース解説
製造業、主に購買・調達部門にお勤めの方々に向けた情報を配信しております。
新任の方やベテランの方、管理職を対象とした幅広いコンテンツをご用意しております。
お問い合わせ
コストダウンが利益に直結する術だと理解していても、なかなか前に進めることができない状況。そんな時は、newjiのコストダウン自動化機能で大きく利益貢献しよう!
(β版非公開)