- お役立ち記事
- Design techniques that combine precision and durability that new employees in the high-precision rotary encoder manufacturing industry should learn
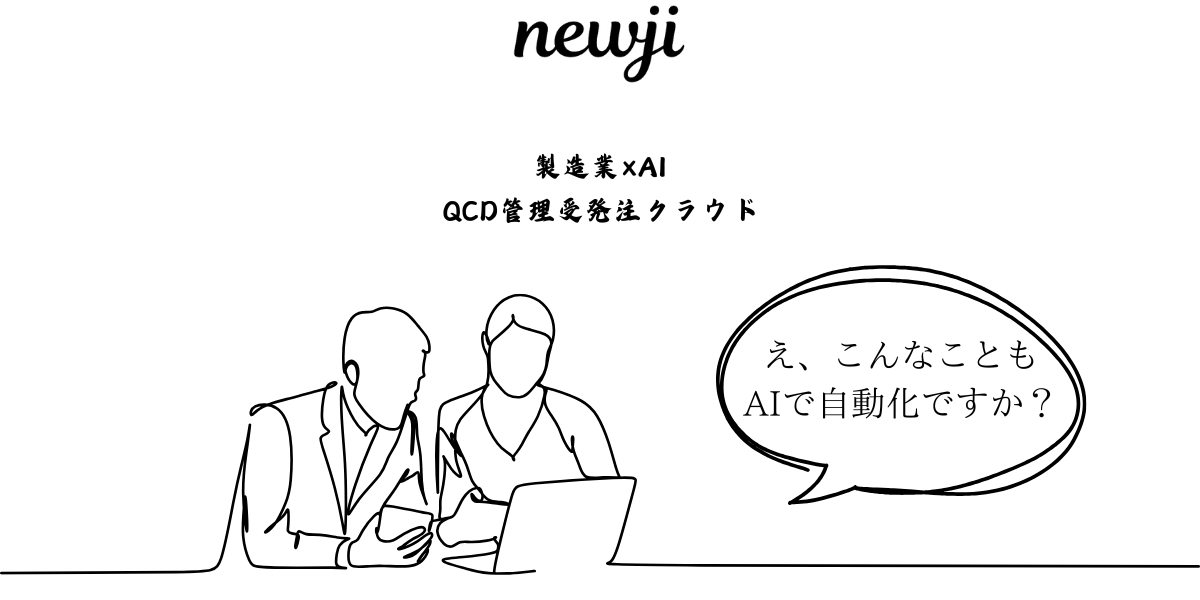
Design techniques that combine precision and durability that new employees in the high-precision rotary encoder manufacturing industry should learn
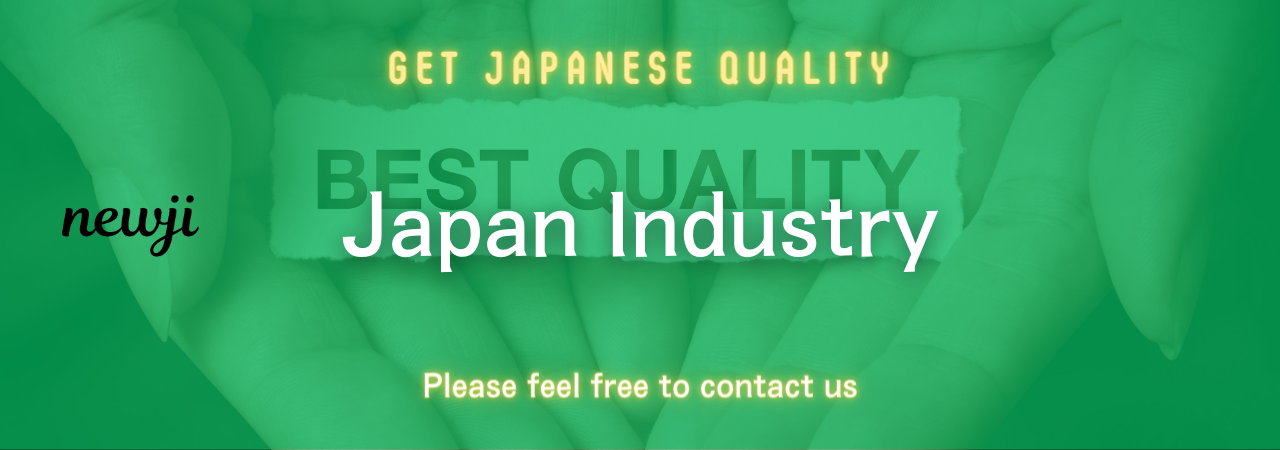
目次
Understanding High-Precision Rotary Encoders
High-precision rotary encoders are essential components in various industries, playing a crucial role in the accurate measurement of rotation, speed, and position of equipment.
These encoders are widely used in robotics, CNC machines, and industrial automation.
For new employees entering the high-precision rotary encoder manufacturing industry, understanding the fundamentals of these devices is the first step toward mastering design techniques that combine precision and durability.
Rotary encoders can be broadly classified into two types: incremental and absolute.
Incremental encoders provide relative position information, making them suited for applications where tracking the changes in position is required.
Absolute encoders, on the other hand, provide a unique position value within a full rotation, ensuring precise and repeatable positioning.
Design Techniques for Precision
In the manufacturing of rotary encoders, achieving high precision is paramount.
Precision ensures that the encoders provide accurate data, which is critical for the smooth operation of automated systems.
Material Selection
The choice of materials is critical for the precision of rotary encoders.
Materials should be chosen for their resilience against wear and tear, as well as their ability to maintain structural integrity under various environmental conditions.
Common materials include stainless steel, aluminum, and high-grade plastics.
These materials are known for their durability and ability to withstand thermal variations without significant deformation.
Precision Machining
Precision machining is a core aspect of manufacturing rotary encoders.
Advanced CNC machines are often used to ensure that each component is manufactured to tight tolerances.
Precision machining involves cutting, grinding, and milling to achieve the exact specifications required.
New employees should learn to operate these machines with accuracy and be aware of how even slight deviations in component dimensions can impact overall encoder performance.
Calibration and Testing
Once manufactured, rotary encoders undergo rigorous testing to ensure precision.
Calibration processes include aligning the encoder with known measurements and adjusting their outputs to match.
Testing in simulated environments helps manufacturers verify the encoder’s accuracy under various conditions.
This process is crucial, as it identifies any discrepancies that can be corrected to enhance precision before deployment.
Design Techniques for Durability
Along with precision, durability is a critical factor in rotary encoder design.
Durable encoders ensure long-lasting performance and reduce the likelihood of mechanical failures in the field.
Sealing and Protection
Rotary encoders often operate in environments with dust, moisture, or chemicals.
Sealing the encoders with appropriate materials can protect internal components from these elements.
Using gaskets, O-rings, and sealant compounds can enhance the durability of encoders by preventing ingress that might otherwise cause damage or impair function.
Robust Housing Design
The housing of a rotary encoder is pivotal for its durability.
It must be designed to withstand mechanical stresses, vibrations, and impacts.
Utilizing robust materials like anodized aluminum or impact-resistant plastic for the housing can enhance durability.
New employees must understand the importance of a well-designed housing and its contribution to the encoder’s longevity.
Maintenance-Free Bearings
Choosing the right bearings is essential for durable rotary encoder design.
Maintenance-free bearings, such as those made from self-lubricating materials, reduce the necessity for regular maintenance, thus increasing the life span of the encoder.
Understanding bearing types and selecting the appropriate maintenance-free options can significantly impact an encoder’s durability.
Integrating Precision and Durability
Combining precision and durability in rotary encoders is a challenging but rewarding endeavor.
New employees should focus on integrating both aspects to meet industry demands and customer satisfaction.
Design Optimization
Optimal design is achieved through a fine balance between precision and durability.
By conducting thorough research and analysis, designers can create rotary encoders that satisfy both criteria.
Simulation software plays an integral role in this process, allowing designers to model performance and durability under different scenarios.
Understanding simulation tools and how to leverage them is a key skill for new employees.
Continuous Improvement
The field of rotary encoder manufacturing is dynamic, with continuous advancements in technology and materials.
New employees should adopt a mindset of continuous improvement, always seeking ways to enhance encoder designs.
This involves staying informed about the latest industry trends, participating in training programs, and collaborating with experienced team members.
Quality Assurance
Quality assurance is essential in delivering high-precision, durable rotary encoders.
New employees should engage with quality assurance protocols to ensure that every encoder meets the stringent standards required by the industry.
By prioritizing quality control measures, companies can produce reliable products that combine both precision and durability, ultimately leading to higher customer satisfaction.
Understanding and mastering these design techniques will equip new employees with the knowledge and skills needed to succeed and innovate in the high-precision rotary encoder manufacturing industry.
By emphasizing precision and durability, they can contribute to the creation of products that meet the evolving needs of modern technology and industrial applications.
資料ダウンロード
QCD調達購買管理クラウド「newji」は、調達購買部門で必要なQCD管理全てを備えた、現場特化型兼クラウド型の今世紀最高の購買管理システムとなります。
ユーザー登録
調達購買業務の効率化だけでなく、システムを導入することで、コスト削減や製品・資材のステータス可視化のほか、属人化していた購買情報の共有化による内部不正防止や統制にも役立ちます。
NEWJI DX
製造業に特化したデジタルトランスフォーメーション(DX)の実現を目指す請負開発型のコンサルティングサービスです。AI、iPaaS、および先端の技術を駆使して、製造プロセスの効率化、業務効率化、チームワーク強化、コスト削減、品質向上を実現します。このサービスは、製造業の課題を深く理解し、それに対する最適なデジタルソリューションを提供することで、企業が持続的な成長とイノベーションを達成できるようサポートします。
オンライン講座
製造業、主に購買・調達部門にお勤めの方々に向けた情報を配信しております。
新任の方やベテランの方、管理職を対象とした幅広いコンテンツをご用意しております。
お問い合わせ
コストダウンが利益に直結する術だと理解していても、なかなか前に進めることができない状況。そんな時は、newjiのコストダウン自動化機能で大きく利益貢献しよう!
(Β版非公開)