- お役立ち記事
- Design techniques to improve reliability and environmental resistance that new employees in the aircraft electronic connector manufacturing industry should know
月間76,176名の
製造業ご担当者様が閲覧しています*
*2025年3月31日現在のGoogle Analyticsのデータより
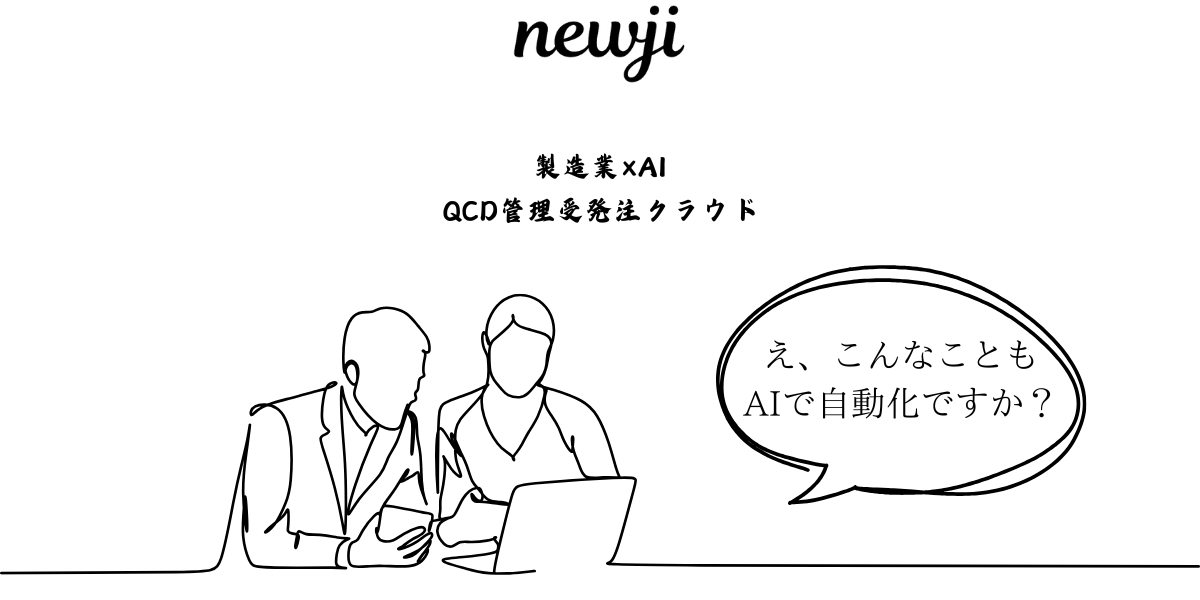
Design techniques to improve reliability and environmental resistance that new employees in the aircraft electronic connector manufacturing industry should know
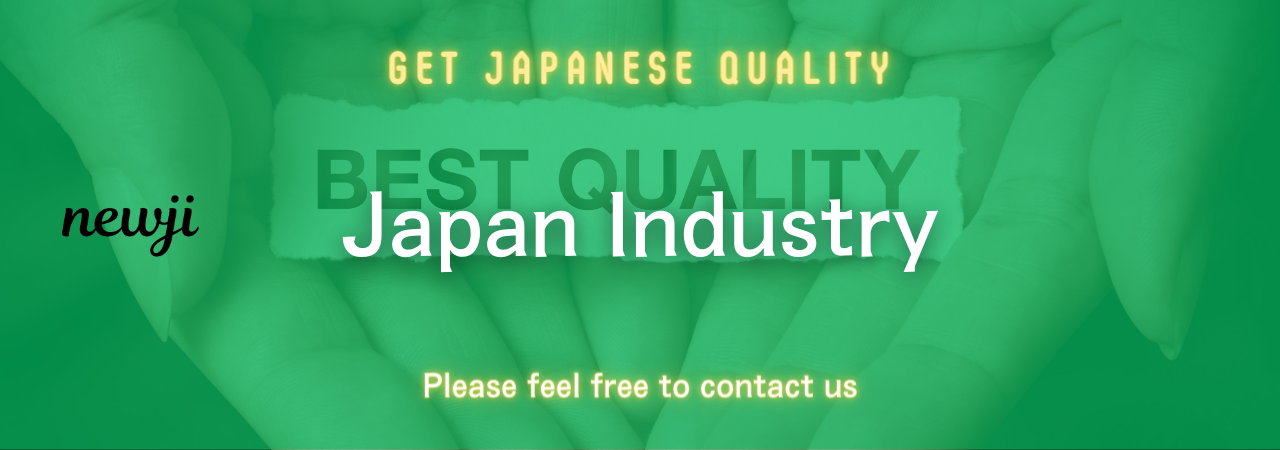
目次
Understanding Reliability in Aircraft Electronic Connectors
When working in the aircraft electronic connector manufacturing industry, understanding reliability is crucial.
Aircraft connectors play a significant role in ensuring that different electronic systems communicate effectively.
These connectors are subject to rigorous demands, as they must operate reliably under various environmental conditions.
Reliability in design means minimizing the risk of failures, which is critical in the aviation industry where safety is paramount.
New employees should focus on learning techniques that enhance the dependability of these components to ensure consistent performance.
One fundamental approach to achieving reliability is through thorough testing and quality assurance processes.
These processes help in identifying potential weaknesses that could lead to failures when the connectors are in use.
Design Techniques for Enhanced Reliability
Selecting Appropriate Materials
The choice of materials significantly affects the reliability of aircraft connectors.
Engineers often choose materials that are resistant to corrosion, high temperatures, and mechanical wear.
For instance, using high-grade metals and robust insulating materials can prevent degradation over time.
Understanding material properties and how they react under specific conditions is essential.
This knowledge allows engineers to predict how connectors will behave during flights, thus ensuring reliability.
Implementing Redundancy
Redundancy is a design principle that involves having multiple independent systems or components perform the same function.
By implementing redundancy, if one component fails, another can take over without affecting overall system performance.
This concept is especially important in aviation, where safety cannot be compromised.
Redundant designs help maintain communication between critical systems, even in the event of a failure.
New employees should learn how to incorporate redundancy effectively to enhance reliability.
Sealing and Shielding
Aircraft often fly through various environments, from hot deserts to cold, high-altitude skies.
Thus, environmental resistance is a key consideration in designing aircraft connectors.
Sealing techniques such as using gaskets and O-rings can protect connectors from moisture, dust, and other contaminants.
Shielding is another technique used to protect connectors from electromagnetic interference, which can disrupt electronic communications.
Understanding how to apply these protective measures ensures that connectors function properly, regardless of external conditions.
Robust Mechanical Design
A well-thought-out mechanical design enhances the connector’s ability to withstand physical stress.
It’s essential to consider factors like vibration, impact, and mechanical fatigue, all of which connectors are exposed to during a flight.
Using features like strain reliefs helps prevent damage to wires and contacts when connectors are moved or twisted.
Flexible designs that can absorb and distribute forces evenly are also beneficial.
Engineers should prioritize designing connectors that can handle the physical demands of their operating environments.
Addressing Environmental Resistance
Temperature Extremes
Aircraft connectors must operate flawlessly in both extremities of temperature.
It’s vital to select materials and designs that can withstand high temperatures in the engine compartment and freezing temperatures at high altitudes.
Testing connectors in climatic chambers that simulate these conditions is essential.
This testing helps in identifying materials and designs that can maintain performance across temperature extremes.
Moisture and Corrosion
Corrosion can significantly impact the reliability and lifespan of aircraft connectors.
Aviation environments often include high humidity and exposure to saltwater, especially in marine aircraft.
Engineers use coatings and platings to protect connectors from corrosion.
Materials like stainless steel and coatings such as nickel or chromate provide excellent resistance to moisture-induced corrosion.
Employing these protective coatings can significantly extend the life of a connector and ensure reliable performance.
Vibration and Shock
Aircraft are subject to constant vibration and occasional shocks during operation.
Connectors must be designed to withstand these forces without losing connectivity.
Design strategies include using secure locking mechanisms to prevent disconnection and incorporating flexible materials that absorb vibrations.
Performing vibration testing during the design phase can also identify weaknesses that need to be addressed.
Understanding how to make connectors vibration-resistant is key to maintaining reliable connections throughout a flight.
Continuous Learning and Improvement
Staying updated on the latest design techniques is essential for new employees in the aircraft electronic connector manufacturing industry.
The field continually evolves with technological advances, presenting new opportunities to improve reliability and environmental resistance.
Engaging in ongoing training and participating in industry workshops can provide valuable insights into new materials and technologies.
Networking with experienced professionals can also offer practical advice and shared experiences in designing reliable connectors.
Investing time in continuous learning ensures that employees are well-equipped to contribute to the development of high-quality, reliable aircraft connectors.
Conclusion
In the aircraft electronic connector manufacturing industry, designing for reliability and environmental resistance is non-negotiable.
New employees should immerse themselves in understanding the principles of material science, redundancy, shielding, and robust mechanical design.
Addressing environmental challenges like temperature extremes, moisture, and vibration is critical for ensuring that connectors perform under all conditions.
By committing to continuous learning and improvement, employees can significantly impact the safety and efficiency of aviation electronics, ultimately contributing to advancements in the field.
資料ダウンロード
QCD管理受発注クラウド「newji」は、受発注部門で必要なQCD管理全てを備えた、現場特化型兼クラウド型の今世紀最高の受発注管理システムとなります。
ユーザー登録
受発注業務の効率化だけでなく、システムを導入することで、コスト削減や製品・資材のステータス可視化のほか、属人化していた受発注情報の共有化による内部不正防止や統制にも役立ちます。
NEWJI DX
製造業に特化したデジタルトランスフォーメーション(DX)の実現を目指す請負開発型のコンサルティングサービスです。AI、iPaaS、および先端の技術を駆使して、製造プロセスの効率化、業務効率化、チームワーク強化、コスト削減、品質向上を実現します。このサービスは、製造業の課題を深く理解し、それに対する最適なデジタルソリューションを提供することで、企業が持続的な成長とイノベーションを達成できるようサポートします。
製造業ニュース解説
製造業、主に購買・調達部門にお勤めの方々に向けた情報を配信しております。
新任の方やベテランの方、管理職を対象とした幅広いコンテンツをご用意しております。
お問い合わせ
コストダウンが利益に直結する術だと理解していても、なかなか前に進めることができない状況。そんな時は、newjiのコストダウン自動化機能で大きく利益貢献しよう!
(β版非公開)