- お役立ち記事
- Design verification method using 3D CAD/CAE tools
月間77,185名の
製造業ご担当者様が閲覧しています*
*2025年2月28日現在のGoogle Analyticsのデータより
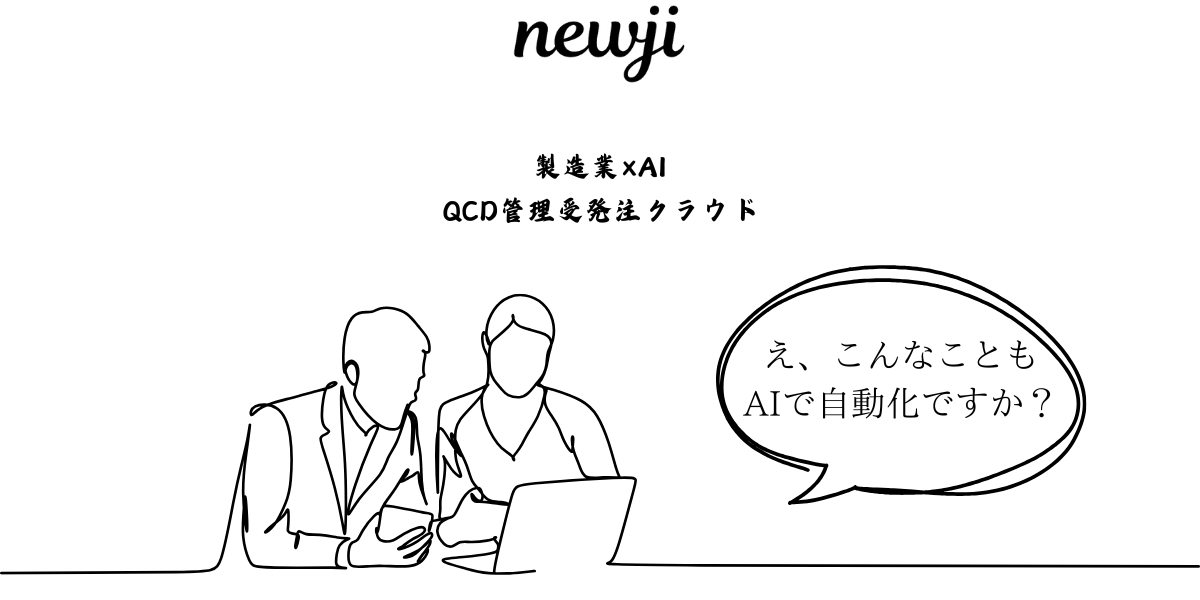
Design verification method using 3D CAD/CAE tools
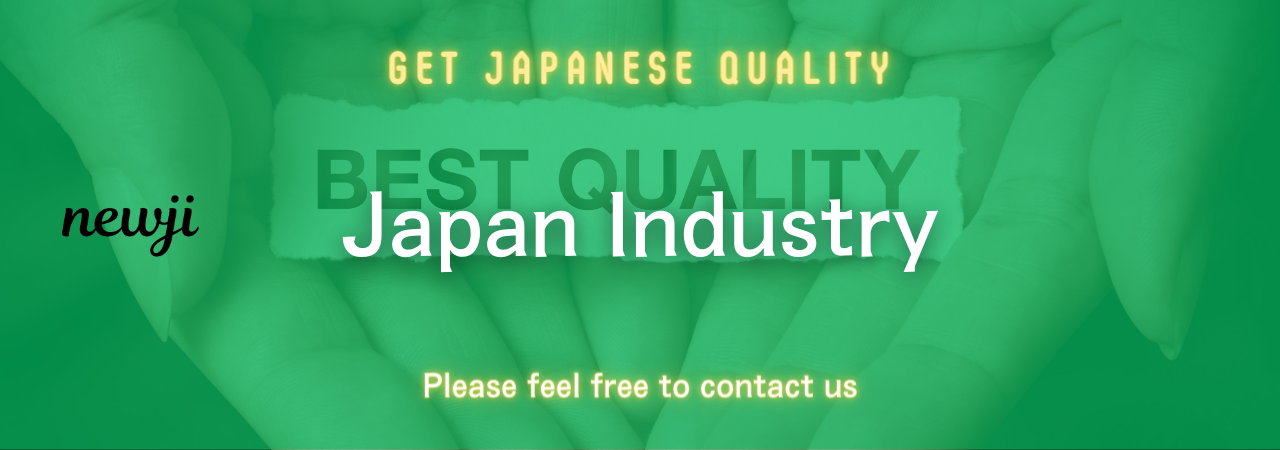
目次
Understanding 3D CAD/CAE Tools
3D CAD (Computer-Aided Design) and CAE (Computer-Aided Engineering) tools are essential in the modern design and engineering industries.
These tools assist engineers and designers in creating detailed models and simulations, offering a virtual environment to test ideas before physical prototypes are built.
The integration of CAD and CAE allows for efficient design processes, reducing time and costs while improving product quality.
Benefits of Using 3D CAD
3D CAD tools offer numerous advantages in design and engineering. Firstly, they allow for the creation of precise and complex geometries that can easily be modified and optimized for various applications.
This flexibility is crucial for accommodating changes and testing different configurations without needing to restart the design process.
Moreover, 3D CAD models can be easily shared and collaborated on, facilitating communication between teams and stakeholders.
This ensures that everyone involved in a project is on the same page, thereby reducing the chances of errors and miscommunication.
Additionally, CAD models can be directly used for CNC machining, 3D printing, or other manufacturing processes.
This seamless transition from design to production helps in maintaining accuracy and reducing the lead time.
The Role of 3D CAE in Design Verification
CAE tools complement CAD by providing the means to simulate real-world conditions and assess how a design will perform.
By using CAE, engineers can conduct various analyses, such as stress tests, thermal simulations, and fluid dynamics, to ensure that their designs meet required specifications and safety standards.
Simulating real-world conditions helps in identifying potential weaknesses and points of failure in a design before a prototype is built.
This early detection is vital for addressing issues without incurring the high costs associated with physical testing and revisions.
Furthermore, CAE tools offer insights into how materials and different design elements interact under different conditions, enabling designers to optimize their designs for durability, efficiency, and performance.
Design Verification Process
Design verification is a crucial step in the product development lifecycle.
It ensures that a product meets all required specifications and customer needs before moving on to production.
3D CAD/CAE tools play a significant role in this process by allowing for detailed analysis and validation of designs.
Initial Design Assessment
The initial phase of design verification involves creating a preliminary CAD model.
This model acts as a blueprint that can be refined and optimized in subsequent stages.
Engineers can use this stage to evaluate the basic structure and functionality of a design, ensuring it aligns with initial project goals and requirements.
Simulation and Testing
Once the basic design is established, CAE tools are employed to simulate various operational conditions.
These simulations help identify stress concentrations, temperature variations, and other critical performance metrics.
Engineers can then make necessary adjustments to improve the design and ensure it meets performance criteria.
By running multiple scenarios, designers can also explore how different variables impact the design.
This iterative process is crucial for refining designs to achieve the best possible outcomes and avoid unforeseen issues during physical testing.
Optimization and Refinement
Optimization is the next step after initial simulations.
Using feedback from CAE analysis, designers make informed tweaks to the model to enhance its performance and efficiency.
Optimization might involve reducing weight, adjusting material usage, or changing geometries to minimize costs and maximize performance.
In this stage, designers can also focus on enhancing the aesthetic aspects of the design.
A well-optimized product not only performs well but is also visually pleasing and meets consumer expectations.
Final Verification and Prototyping
After a detailed optimization process, the design undergoes a final round of verification.
This involves rechecking all performance criteria and ensuring compliance with industry standards and regulations.
Once verified, the design is ready for prototype development.
Prototyping serves as the last test before mass production.
It validates the design in a real-world setting, providing final confirmation that the product functions as intended.
Any issues found at this stage are typically minor and can be quickly addressed.
Conclusion
Using 3D CAD/CAE tools for design verification offers a comprehensive approach to product development.
These tools streamline the design process, ensuring that products meet the highest standards of quality and performance.
By leveraging advanced simulations and optimizations, engineers can confidently progress from initial concept to production with reduced risk and increased efficiency.
In a competitive market, the ability to efficiently test and verify designs is invaluable.
With 3D CAD/CAE tools, designers and engineers have the technology needed to innovate and deliver superior products that meet both consumer demands and industry standards.
資料ダウンロード
QCD管理受発注クラウド「newji」は、受発注部門で必要なQCD管理全てを備えた、現場特化型兼クラウド型の今世紀最高の受発注管理システムとなります。
ユーザー登録
受発注業務の効率化だけでなく、システムを導入することで、コスト削減や製品・資材のステータス可視化のほか、属人化していた受発注情報の共有化による内部不正防止や統制にも役立ちます。
NEWJI DX
製造業に特化したデジタルトランスフォーメーション(DX)の実現を目指す請負開発型のコンサルティングサービスです。AI、iPaaS、および先端の技術を駆使して、製造プロセスの効率化、業務効率化、チームワーク強化、コスト削減、品質向上を実現します。このサービスは、製造業の課題を深く理解し、それに対する最適なデジタルソリューションを提供することで、企業が持続的な成長とイノベーションを達成できるようサポートします。
製造業ニュース解説
製造業、主に購買・調達部門にお勤めの方々に向けた情報を配信しております。
新任の方やベテランの方、管理職を対象とした幅広いコンテンツをご用意しております。
お問い合わせ
コストダウンが利益に直結する術だと理解していても、なかなか前に進めることができない状況。そんな時は、newjiのコストダウン自動化機能で大きく利益貢献しよう!
(β版非公開)