- お役立ち記事
- Destruction mechanism and strength evaluation of solder joints and measures to improve strength reliability
月間77,185名の
製造業ご担当者様が閲覧しています*
*2025年2月28日現在のGoogle Analyticsのデータより
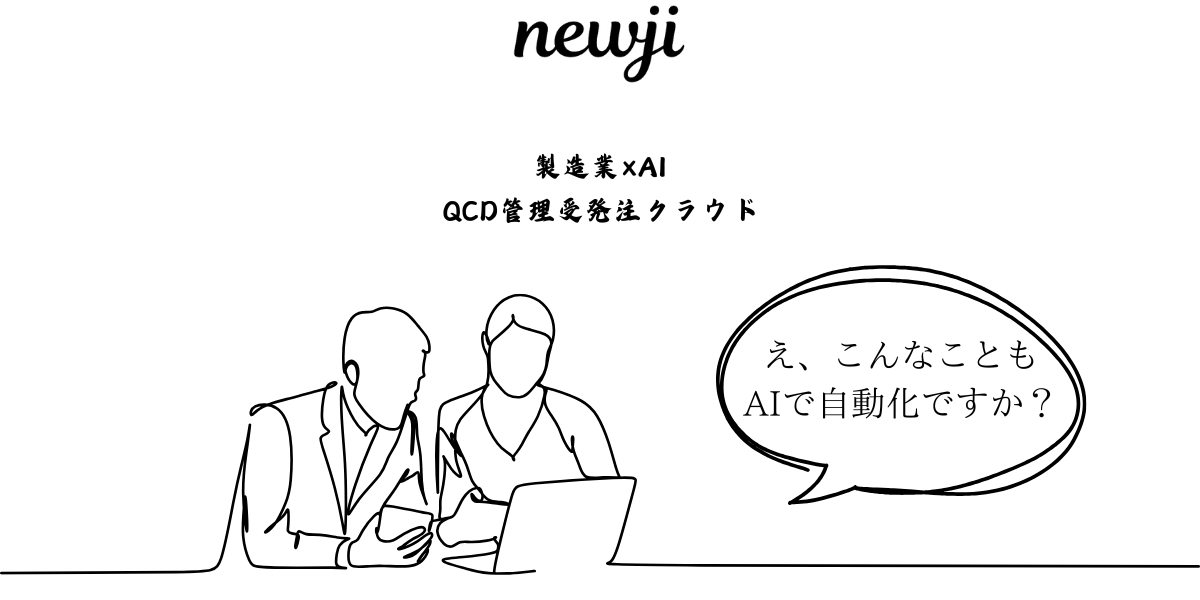
Destruction mechanism and strength evaluation of solder joints and measures to improve strength reliability
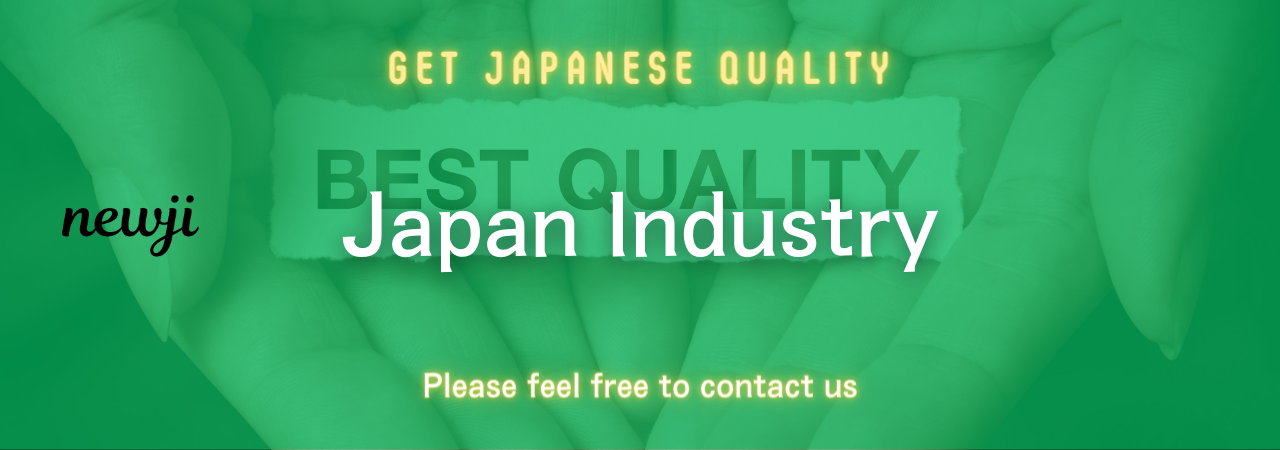
目次
Understanding Solder Joints
Solder joints are crucial in the assembly of electronic devices.
These joints provide both mechanical and electrical connections between components and printed circuit boards (PCBs).
To appreciate their importance, think of solder joints as the glue that holds the heart of an electronic device together.
Without them, electronic components would fail to communicate effectively, leading to device malfunctions or failure.
Destruction Mechanisms of Solder Joints
To ensure the longevity and reliability of solder joints, it’s vital to understand the mechanisms that lead to their destruction.
Various factors can contribute to solder joint failure.
Thermal Cycling
One of the primary causes of solder joint failure is thermal cycling.
This refers to the repeated rise and fall of temperature during device operation or environmental exposure.
Thermal cycling can cause the solder to expand and contract, which can lead to fatigue over time.
Eventually, this can result in crack formation and propagation, ultimately leading to joint failure.
Mechanical Stress
Mechanical stress is another critical factor.
Vibrations, shocks, and bending can apply undue stress on solder joints.
Delicate electronic devices, especially those carried around like mobile phones, are particularly susceptible to such stresses.
Over time, mechanical stress can cause solder joints to fracture or become detached.
Corrosion
Corrosion is a less obvious, yet significant, factor contributing to solder joint failure.
Environmental factors such as humidity, air pollution, and even sweat can lead to corrosion.
Corrosion can degrade the solder material and compromise the integrity of the joint.
Evaluating the Strength of Solder Joints
Evaluating the strength of solder joints involves meticulous testing and analysis.
This process helps determine their reliability and predict any potential failures.
Shear Testing
Shear testing involves applying forces parallel to the plane of the solder joint.
It’s an effective method for assessing the mechanical strength of the joint.
During this test, the force required to shear the joint is measured, providing valuable data about its robustness.
Microsection Analysis
Microsection analysis involves slicing the solder joint and examining it under a microscope.
This test helps in identifying any voids, cracks, or other imperfections within the joint.
Such detailed inspections provide insights into the quality and potential weak points of the solder joint.
Thermal Cycle Testing
Thermal cycle testing involves exposing solder joints to repeated cycles of heating and cooling.
This test mimics the real-world thermal stresses that joints would experience in actual operation.
The test gauges the joint’s ability to withstand thermal fatigue over extended periods.
Improving the Strength and Reliability of Solder Joints
To enhance the strength and reliability of solder joints, several strategies can be employed.
Optimizing Solder Material
Choosing the right solder material is crucial.
Lead-free solders are becoming popular due to environmental concerns, but each type of solder has its advantages and drawbacks.
Understanding the properties of different solder materials can help in selecting the ideal one for specific applications.
Proper Joint Design
The design of the solder joint can significantly influence its durability.
Ensuring that components are well-aligned and the joints are not overly stressed in any direction can prevent premature failure.
Employing solder masks and other support structures can also increase joint reliability.
Controlled Manufacturing Process
Maintaining a controlled manufacturing environment ensures that solder joints are produced consistently and without defects.
Temperature controls, timely process execution, and regular equipment maintenance can help in achieving this.
Protective Coatings
Applying protective coatings can shield solder joints from environmental factors that cause corrosion.
These coatings can extend the life of the joint by reducing exposure to humidity and pollutants.
Conclusion
Solder joints may be tiny, but they play a massive role in the functioning of electronic devices.
By understanding the mechanisms that lead to their destruction and implementing measures to improve their strength and reliability, we can enhance the overall performance and longevity of electronic devices.
Through innovative design, careful material selection, controlled manufacturing, and protective strategies, the industry can continue to develop electronics that are both reliable and enduring.
資料ダウンロード
QCD管理受発注クラウド「newji」は、受発注部門で必要なQCD管理全てを備えた、現場特化型兼クラウド型の今世紀最高の受発注管理システムとなります。
ユーザー登録
受発注業務の効率化だけでなく、システムを導入することで、コスト削減や製品・資材のステータス可視化のほか、属人化していた受発注情報の共有化による内部不正防止や統制にも役立ちます。
NEWJI DX
製造業に特化したデジタルトランスフォーメーション(DX)の実現を目指す請負開発型のコンサルティングサービスです。AI、iPaaS、および先端の技術を駆使して、製造プロセスの効率化、業務効率化、チームワーク強化、コスト削減、品質向上を実現します。このサービスは、製造業の課題を深く理解し、それに対する最適なデジタルソリューションを提供することで、企業が持続的な成長とイノベーションを達成できるようサポートします。
製造業ニュース解説
製造業、主に購買・調達部門にお勤めの方々に向けた情報を配信しております。
新任の方やベテランの方、管理職を対象とした幅広いコンテンツをご用意しております。
お問い合わせ
コストダウンが利益に直結する術だと理解していても、なかなか前に進めることができない状況。そんな時は、newjiのコストダウン自動化機能で大きく利益貢献しよう!
(β版非公開)