- お役立ち記事
- Detailed Planning Techniques for Equipment Investment and Financial Planning in Manufacturing
この記事は、当社の提供するお役立ち記事の一部です。詳しくは公式サイトをご覧ください。
Detailed Planning Techniques for Equipment Investment and Financial Planning in Manufacturing
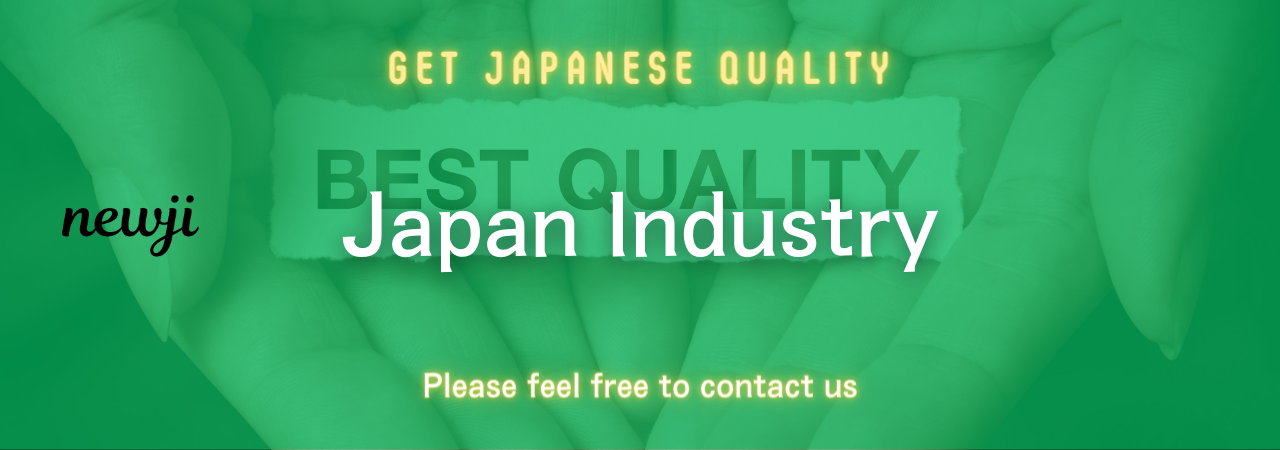
目次
Introduction to Equipment Investment
Equipment investment in manufacturing is a critical decision that can impact both short-term productivity and long-term profitability.
Understanding the nuances of this investment and planning accordingly can help manufacturing companies maximize their returns.
Effective planning for equipment investment involves evaluating the potential benefits, costs, and risks associated with purchasing new machinery or upgrading existing equipment.
Understanding the Importance of Financial Planning
Financial planning plays an essential role in the success of any equipment investment.
Without a well-structured financial plan, even the soundest investments can result in financial strain or failure.
A robust financial plan helps in forecasting expenses, revenue, and potential returns, thus ensuring the sustainability of the investment.
Steps to Effective Equipment Investment Planning
1. Identifying Needs and Objectives
The first step in equipment investment is identifying the specific needs and objectives of the manufacturing facility.
Assess the current equipment’s performance and determine whether new machinery is necessary to meet production goals.
Consider if the new equipment will improve efficiency, reduce costs, or increase production capacity.
This initial assessment will form the foundation for the entire investment planning process.
2. Conducting a Cost-Benefit Analysis
Once the needs and objectives are clear, a cost-benefit analysis should be conducted.
This involves comparing the costs associated with the new equipment against the expected benefits.
Costs can include purchase price, installation, maintenance, and training, while benefits may encompass improved efficiency, reduced downtime, and increased output.
A comprehensive cost-benefit analysis helps in understanding the true value of the investment and whether it aligns with the company’s financial goals.
3. Exploring Financing Options
Funding the investment is a crucial aspect of the planning process.
Manufacturing companies have various financing options, including loans, leases, and lines of credit.
Exploring these options and selecting the most suitable one can significantly impact the overall financial health of the company.
Consider interest rates, repayment terms, and the impact of debt on the company’s balance sheet when deciding on a financing option.
4. Evaluating Potential Risks
Every investment comes with inherent risks, and equipment investment is no exception.
It is vital to identify and evaluate potential risks such as technological obsolescence, equipment failure, or fluctuating market demand.
Developing a risk mitigation strategy can help in minimizing the impact of these risks on the company’s operations and financial stability.
5. Establishing a Monitoring System
Once the equipment is purchased and installed, it is important to have a monitoring system in place.
This system should track the performance of the new equipment, compare it against the projected benefits, and identify any discrepancies.
Regular monitoring ensures that the equipment is functioning optimally and any issues are addressed promptly.
Principles of Effective Financial Planning
1. Setting Realistic Goals
Effective financial planning starts with setting realistic financial goals.
These goals should be specific, measurable, achievable, relevant, and time-bound (SMART).
Having clear objectives helps in formulating a financial plan that is aligned with the company’s vision and mission.
2. Forecasting and Budgeting
Accurate forecasting and budgeting are critical components of financial planning.
Forecasting involves estimating future revenue, expenses, and cash flow.
This helps in identifying potential financial challenges and opportunities.
Budgeting, on the other hand, involves allocating resources efficiently to ensure that financial goals are met.
Both forecasting and budgeting require continuous monitoring and adjustment to stay aligned with the company’s financial objectives.
3. Managing Cash Flow
Managing cash flow is essential to ensure that the company has sufficient liquidity to meet its operational needs and investment commitments.
A positive cash flow indicates that the company can cover its expenses and still have funds available for new investments.
Implementing effective cash flow management practices, such as timely invoicing, efficient inventory management, and controlling expenses, can help in maintaining a healthy cash flow.
4. Diversifying Investments
Diversifying investments is a strategy that helps in spreading risk and maximizing returns.
Instead of investing all funds in a single asset or project, companies should consider a portfolio of investments.
This could include equipment, real estate, stocks, or other financial instruments.
Diversification helps in mitigating the impact of potential losses and ensuring a balance between risk and return.
Conclusion
Planning for equipment investment and financial planning in manufacturing requires a detailed and strategic approach.
It involves identifying needs, conducting thorough analyses, exploring financing options, and managing financial resources effectively.
By following these principles and steps, manufacturing companies can make informed decisions that enhance productivity, profitability, and long-term success.
資料ダウンロード
QCD調達購買管理クラウド「newji」は、調達購買部門で必要なQCD管理全てを備えた、現場特化型兼クラウド型の今世紀最高の購買管理システムとなります。
ユーザー登録
調達購買業務の効率化だけでなく、システムを導入することで、コスト削減や製品・資材のステータス可視化のほか、属人化していた購買情報の共有化による内部不正防止や統制にも役立ちます。
NEWJI DX
製造業に特化したデジタルトランスフォーメーション(DX)の実現を目指す請負開発型のコンサルティングサービスです。AI、iPaaS、および先端の技術を駆使して、製造プロセスの効率化、業務効率化、チームワーク強化、コスト削減、品質向上を実現します。このサービスは、製造業の課題を深く理解し、それに対する最適なデジタルソリューションを提供することで、企業が持続的な成長とイノベーションを達成できるようサポートします。
オンライン講座
製造業、主に購買・調達部門にお勤めの方々に向けた情報を配信しております。
新任の方やベテランの方、管理職を対象とした幅広いコンテンツをご用意しております。
お問い合わせ
コストダウンが利益に直結する術だと理解していても、なかなか前に進めることができない状況。そんな時は、newjiのコストダウン自動化機能で大きく利益貢献しよう!
(Β版非公開)