- お役立ち記事
- Detailed Step-by-Step Explanation of Electronic Component Assembly Processes
月間76,176名の
製造業ご担当者様が閲覧しています*
*2025年3月31日現在のGoogle Analyticsのデータより
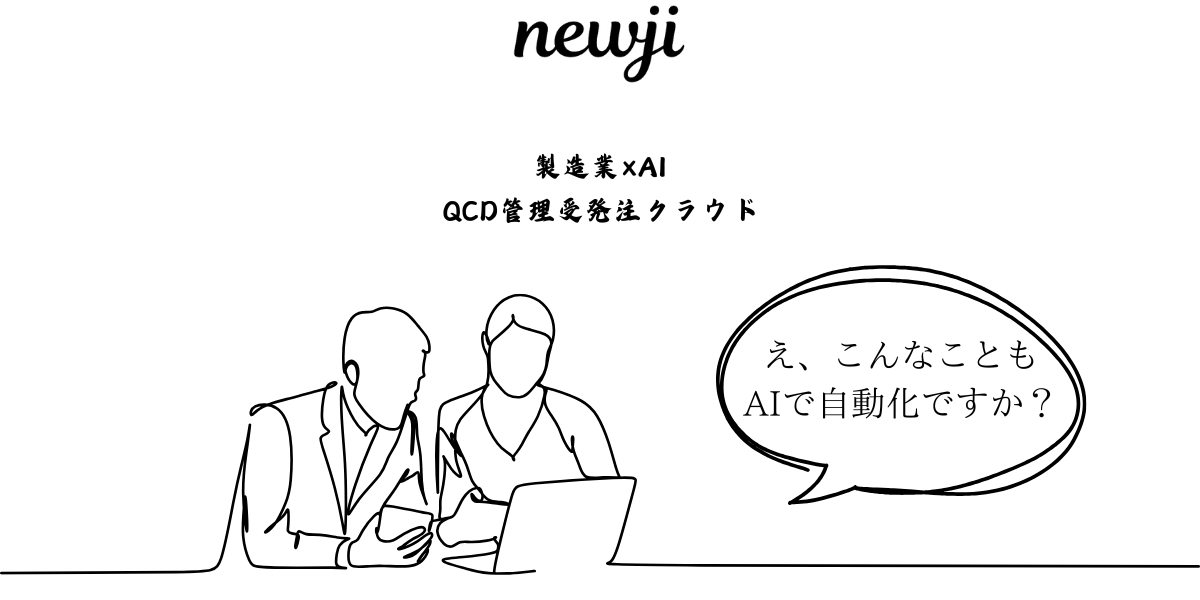
Detailed Step-by-Step Explanation of Electronic Component Assembly Processes
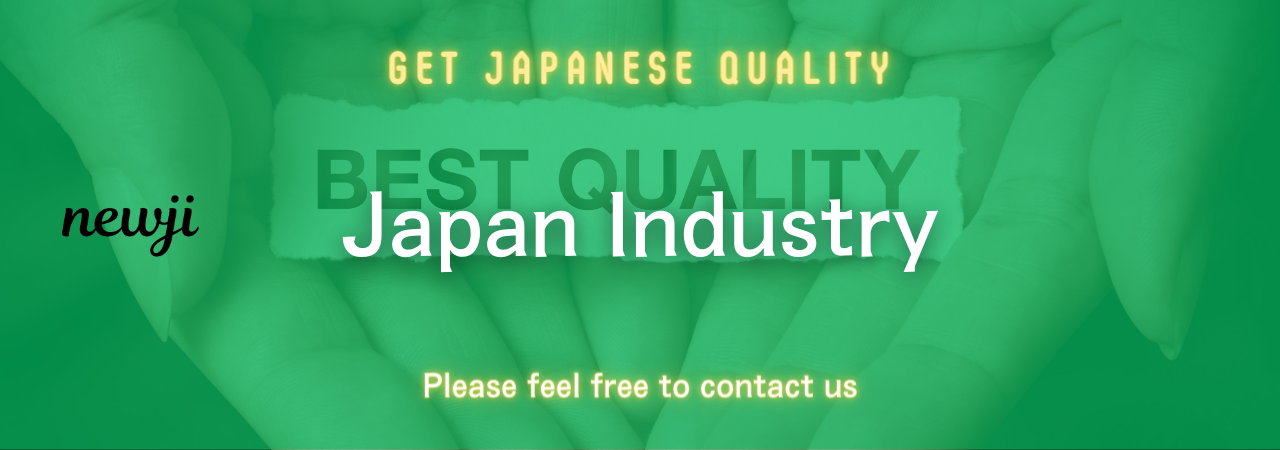
Electronic component assembly processes are essential to creating the modern electronic devices we use daily.
Understanding these processes helps businesses ensure quality and efficiency in production.
In this article, we will explore the detailed steps involved in electronic component assembly, emphasizing the importance of each stage.
目次
Design and Planning
The first and most crucial phase in electronic component assembly is design and planning.
Here, engineers create detailed designs of the electronic circuit, including the layout of components and their connections.
Software tools like CAD (Computer-Aided Design) are widely used to develop precise schematics.
Component Selection
Choosing the right components is essential.
Various factors, such as voltage ratings, current ratings, and compatibility, are taken into account.
Engineers need to ensure that each component fits the overall design and function of the device.
Schematic Diagram
A schematic diagram is created to serve as a blueprint for the assembly process.
This diagram illustrates the electrical connections and arrangements of the components in the circuit.
Sourcing Components
Once the design is finalized, the next step is to source the necessary components.
Manufacturers often partner with trusted suppliers to ensure the availability of high-quality parts.
Quality Assurance
Quality control measures are essential during sourcing.
Each component must be checked for compliance with industry standards to guarantee reliability and performance.
Inventory Management
Efficient inventory management ensures that the right components are available when needed.
This minimizes delays and streamlines the assembly process.
PCB Fabrication
The next significant step is the fabrication of the Printed Circuit Board (PCB).
PCBs serve as the foundation for mounting electronic components.
PCB Design
Using the schematic diagram, a detailed PCB design is created.
This design specifies the physical layout of the board, including the placement of components and routing of electrical traces.
Photolithography
In this process, a light-sensitive film is applied to the PCB material.
A pattern corresponding to the PCB design is transferred onto the film using ultraviolet light.
Etching
The excess copper is etched away, leaving behind the precise conductive paths as per the design.
This stage requires high precision to ensure the integrity of the circuit paths.
Component Placement
With the PCB ready, it’s time for component placement.
This stage involves carefully positioning each component on the board according to the design specifications.
Manual Placement
In cases involving delicate or specific components, manual placement by skilled workers ensures accuracy.
Automated Placement
Automated machines, such as pick-and-place robots, are widely used for efficient and rapid component placement.
These machines can place thousands of components per hour with high precision.
Soldering
Once the components are in place, they need to be securely attached to the PCB.
Soldering is the primary method for achieving this.
Wave Soldering
For through-hole components, wave soldering is commonly used.
The PCB passes over a wave of molten solder, which bonds the component leads to the board.
Reflow Soldering
For surface-mount components, reflow soldering is utilized.
Solder paste is applied to the PCB, and the board is heated in a reflow oven to melt the solder, creating strong connections.
Inspection and Testing
After soldering, thorough inspection and testing are conducted to ensure the assembled PCB functions correctly.
Visual Inspection
Skilled technicians visually inspect the board for any defects, such as solder bridges or misplaced components.
Automated Optical Inspection (AOI) systems may also be employed for this purpose.
Electrical Testing
Electrical tests, including In-Circuit Testing (ICT) and Functional Testing (FT), verify the performance and functionality of the assembled PCB.
These tests check for shorts, open circuits, and other potential issues.
Assembly of Final Product
Upon successful testing, the assembled PCB is ready to be integrated into the final product.
This involves additional steps like casing, wiring, and final assembly.
Casing
The PCB is placed within a protective casing to shield it from environmental factors and physical damage.
The design of the casing varies depending on the product.
Final Assembly
All other components, such as displays, buttons, and connectors, are integrated into the final product.
This step ensures the device is complete and ready for use.
Final Quality Assurance
Before the product is shipped, a final quality assurance check is performed.
This step guarantees that the product meets all required specifications and industry standards.
Functional Testing
The product undergoes comprehensive functional tests to ensure it operates correctly under various conditions.
This includes checking the overall performance, user interface, and any additional features.
Certification
Depending on the product, certification from regulatory bodies may be required.
This ensures the product complies with safety and performance standards.
Packaging and Shipping
The final step in the assembly process is packaging and shipping.
The product is carefully packaged to prevent any damage during transit.
Protective Packaging
Protective packaging materials, such as foam inserts and anti-static bags, are used to safeguard the product.
Shipping
Once packaged, the product is shipped to retailers or directly to consumers.
Efficient logistics ensure timely delivery.
Understanding the detailed processes involved in electronic component assembly is crucial for businesses aiming to manufacture high-quality and reliable electronic products.
Each step, from design and planning to final quality assurance, plays a vital role in ensuring the success of the assembly process.
By emphasizing precision and thoroughness at every stage, manufacturers can deliver superior products to the market.
資料ダウンロード
QCD管理受発注クラウド「newji」は、受発注部門で必要なQCD管理全てを備えた、現場特化型兼クラウド型の今世紀最高の受発注管理システムとなります。
ユーザー登録
受発注業務の効率化だけでなく、システムを導入することで、コスト削減や製品・資材のステータス可視化のほか、属人化していた受発注情報の共有化による内部不正防止や統制にも役立ちます。
NEWJI DX
製造業に特化したデジタルトランスフォーメーション(DX)の実現を目指す請負開発型のコンサルティングサービスです。AI、iPaaS、および先端の技術を駆使して、製造プロセスの効率化、業務効率化、チームワーク強化、コスト削減、品質向上を実現します。このサービスは、製造業の課題を深く理解し、それに対する最適なデジタルソリューションを提供することで、企業が持続的な成長とイノベーションを達成できるようサポートします。
製造業ニュース解説
製造業、主に購買・調達部門にお勤めの方々に向けた情報を配信しております。
新任の方やベテランの方、管理職を対象とした幅広いコンテンツをご用意しております。
お問い合わせ
コストダウンが利益に直結する術だと理解していても、なかなか前に進めることができない状況。そんな時は、newjiのコストダウン自動化機能で大きく利益貢献しよう!
(β版非公開)