- お役立ち記事
- Deterioration and corrosion mechanisms of electronic components, failure analysis and deterioration evaluation methods, and points for improving reliability
Deterioration and corrosion mechanisms of electronic components, failure analysis and deterioration evaluation methods, and points for improving reliability
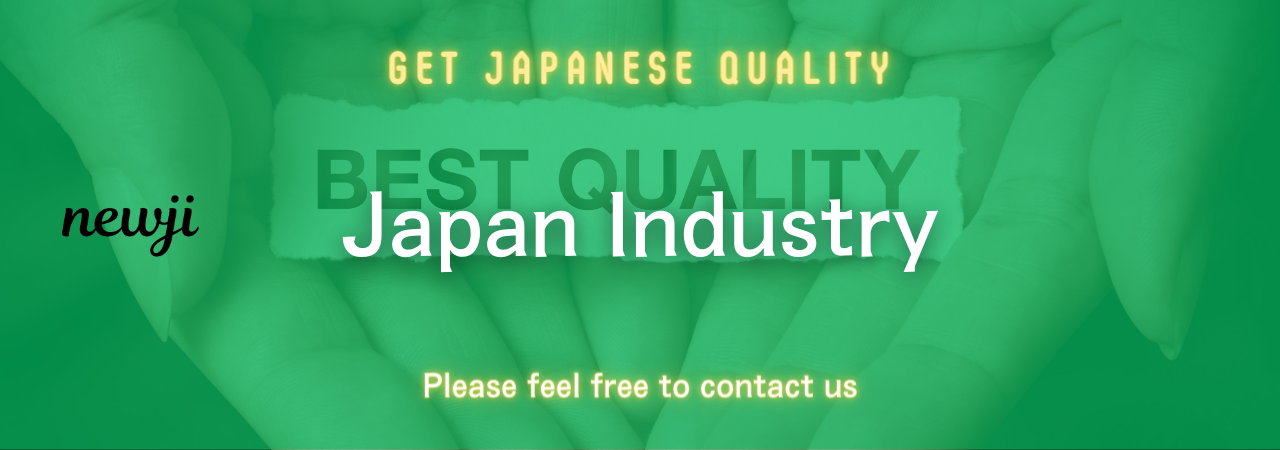
目次
Understanding Deterioration and Corrosion in Electronic Components
Electronic components are integral to modern technology, powering everything from smartphones to industrial machinery.
However, these components are not immune to the influences of time and environment, often undergoing deterioration and corrosion that can lead to failure if not properly managed.
Understanding the mechanisms behind these processes is crucial for improving the reliability and longevity of electronic devices.
The Deterioration Process
Deterioration in electronic components can occur due to various factors, including thermal stress, mechanical stress, and environmental exposure.
Thermal stress arises when components operate at or beyond their thermal limits, causing physical and chemical changes.
This phenomenon is common in semiconductors where excessive heat can lead to changes in material properties, resulting in performance degradation.
Mechanical stress, on the other hand, impacts components through vibration, shock, or flexion.
This type of stress is prevalent in applications where devices are subject to movement or constant use, such as in automotive or portable electronics.
Mechanical stress can lead to micro-cracks or even complete structural failure of components.
Lastly, environmental exposure plays a significant role in the deterioration of electronic components.
Humidity, ultraviolet radiation, and chemical pollutants are just a few examples of environmental factors that can accelerate wear and tear.
Prolonged exposure to these elements leads to the breakdown of protective coatings or insulating materials, facilitating deterioration.
Corrosion Mechanisms
Corrosion is a specific form of deterioration primarily affecting metal components in electronic devices.
It occurs when metal reacts chemically or electrochemically with its environment, leading to its degradation.
Several mechanisms can cause corrosion in electronic components.
One of the most common is galvanic corrosion, which occurs when two dissimilar metals are in contact in the presence of an electrolyte, such as water.
This reaction can lead to accelerated corrosion of one metal while the other is protected.
Another mechanism is pitting corrosion, a localized form of corrosion that creates small, yet deep pits in the metal surface.
Pitting is particularly insidious because it is difficult to detect until significant damage has occurred.
Furthermore, stress-corrosion cracking is a phenomenon where cracks develop in a material due to the combined effects of tensile stress and a corrosive environment.
This type of corrosion is dangerous as it can lead to sudden and unexpected component failures.
Failure Analysis and Evaluation
Failure analysis is a critical process in understanding why electronic components fail and developing strategies for improvement.
This analysis involves a systematic approach to inspecting, analyzing, and identifying the root cause of failures.
An essential part of failure analysis is non-destructive testing.
Techniques such as X-ray imaging, acoustic microscopy, and infrared thermography allow researchers and engineers to examine the internal structures of components without altering or destroying them.
These methods provide insights into potential defects, inconsistencies, or internal damage that could lead to failure.
Destructive testing, while more extreme, can also be necessary in certain evaluations.
This method involves dissecting a component to examine its internal features and assess any failures at a microstructural level.
It allows detailed examination of internal failures and offers a complete understanding of the material’s response to operational stresses.
Reliability testing is another crucial evaluation component, focusing on predicting a component’s performance over time.
Accelerated life testing, for example, subjects components to elevated stress levels to simulate aging and wear, allowing a quicker evaluation of their reliability.
Through such tests, manufacturers can predict the lifecycle and durability of their products under various conditions.
Improving Reliability of Electronic Components
Enhancing the reliability of electronic components is essential for maximizing performance and minimizing failure risks.
Several strategies can be employed to achieve this goal, each focusing on different aspects from design to maintenance.
One effective approach is the use of protective coatings.
These coatings act as a barrier, shielding sensitive parts from environmental factors that accelerate deterioration and corrosion.
Polymeric coatings, for instance, offer excellent protection against moisture and chemical exposure.
Material selection also plays a pivotal role in increasing reliability.
Choosing materials with inherent resistance to corrosion, such as stainless steel or titanium, can significantly reduce the risk of corrosion-related failures.
Additionally, designing components with appropriate thermal management can address thermal stress issues.
Incorporating heat sinks, thermal pads, and efficient ventilation can help dissipate heat effectively, safeguarding components from overheating.
Regular maintenance and inspection are simple yet effective strategies for early detection and prevention of potential failures.
Routine checks can identify wear signs and prompt timely corrective actions, significantly extending the operational life of components.
Lastly, implementing redundancy in design can improve reliability by ensuring that if one component fails, others can take over to maintain functionality.
This approach is particularly useful in critical systems such as aerospace or medical devices where failure is not an option.
Conclusion
The understanding and management of deterioration and corrosion mechanisms in electronic components are critical in achieving high reliability and performance standards.
By leveraging failure analysis and evaluation methods, combined with strategic improvements in design and maintenance, manufacturers can significantly enhance the durability and reliability of their products.
These efforts not only ensure extended service life for electronic components but also contribute to overall technological advancement and user satisfaction.
資料ダウンロード
QCD調達購買管理クラウド「newji」は、調達購買部門で必要なQCD管理全てを備えた、現場特化型兼クラウド型の今世紀最高の購買管理システムとなります。
ユーザー登録
調達購買業務の効率化だけでなく、システムを導入することで、コスト削減や製品・資材のステータス可視化のほか、属人化していた購買情報の共有化による内部不正防止や統制にも役立ちます。
NEWJI DX
製造業に特化したデジタルトランスフォーメーション(DX)の実現を目指す請負開発型のコンサルティングサービスです。AI、iPaaS、および先端の技術を駆使して、製造プロセスの効率化、業務効率化、チームワーク強化、コスト削減、品質向上を実現します。このサービスは、製造業の課題を深く理解し、それに対する最適なデジタルソリューションを提供することで、企業が持続的な成長とイノベーションを達成できるようサポートします。
オンライン講座
製造業、主に購買・調達部門にお勤めの方々に向けた情報を配信しております。
新任の方やベテランの方、管理職を対象とした幅広いコンテンツをご用意しております。
お問い合わせ
コストダウンが利益に直結する術だと理解していても、なかなか前に進めることができない状況。そんな時は、newjiのコストダウン自動化機能で大きく利益貢献しよう!
(Β版非公開)