- お役立ち記事
- Development and manufacturing method of high-performance plastics using nanotechnology
月間77,185名の
製造業ご担当者様が閲覧しています*
*2025年2月28日現在のGoogle Analyticsのデータより
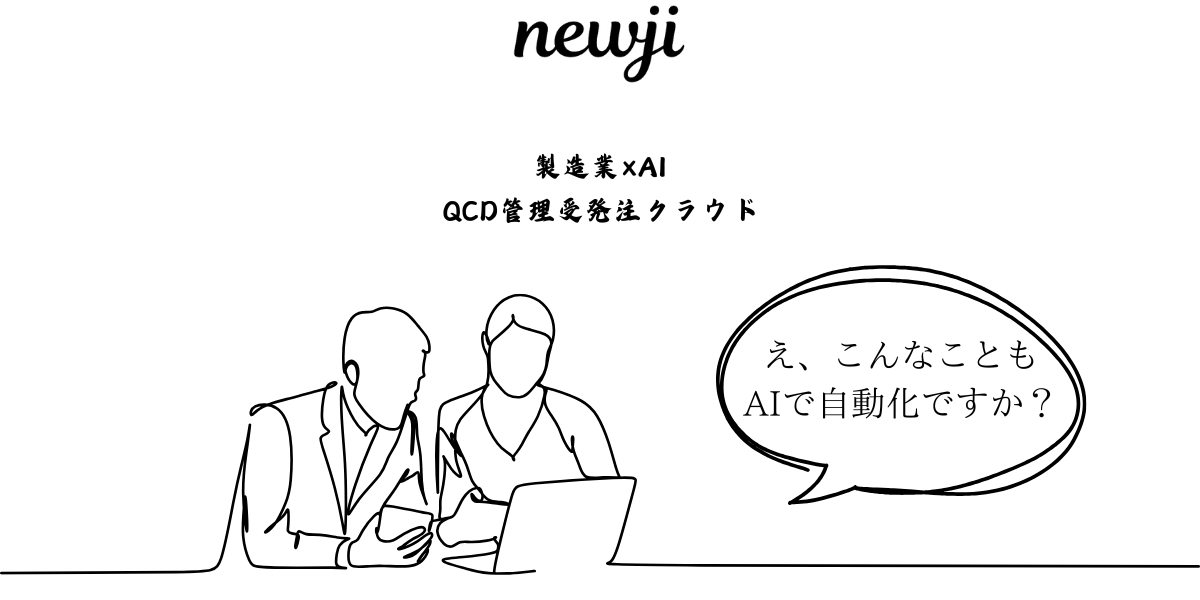
Development and manufacturing method of high-performance plastics using nanotechnology
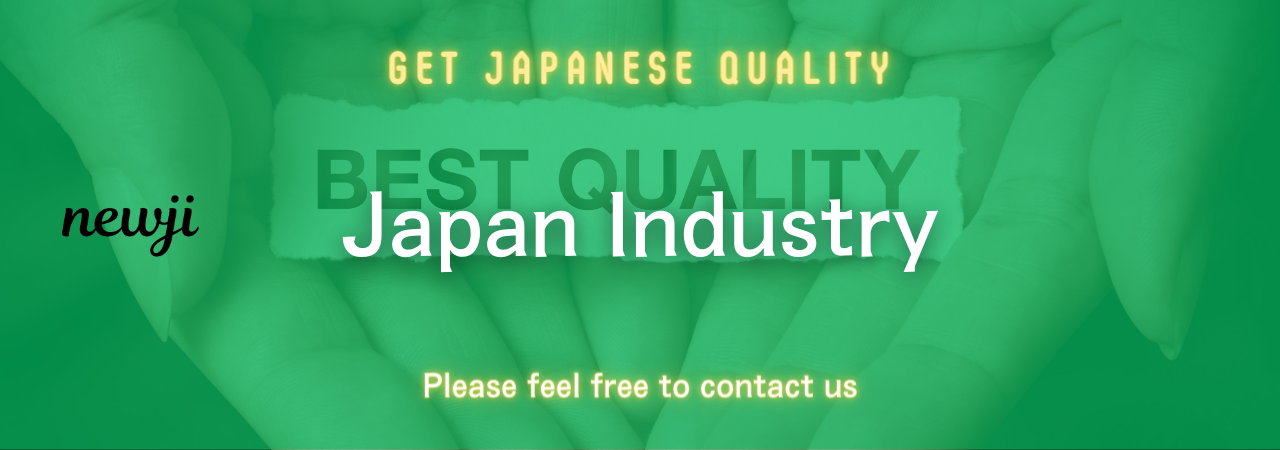
目次
Introduction to High-Performance Plastics
High-performance plastics are an essential part of modern industry, providing the durability and versatility needed for advanced applications in various fields, such as automotive, electronics, and medical devices.
These plastics surpass their conventional counterparts in strength, heat resistance, and chemical stability, making them crucial in the development of cutting-edge technologies.
In recent years, the integration of nanotechnology has further enhanced their capabilities, offering unprecedented material properties and manufacturing techniques.
The Role of Nanotechnology in Plastics
Nanotechnology involves the manipulation of matter on a molecular or atomic scale, typically less than 100 nanometers.
By utilizing nanotechnology, scientists and engineers can develop plastics with superior characteristics compared to traditional methods.
The addition of nanoparticles, such as carbon nanotubes, nanoclays, or silica, enhances mechanical properties like tensile strength and impact resistance.
Nanotechnology can also lead to improved thermal stability and resistance to chemical degradation, which are critical factors in many industrial applications.
Types of Nanomaterials Used in Plastics
Various nanomaterials are employed to enhance the performance of plastics.
Carbon nanotubes are one of the most popular choices due to their exceptional strength and electrical conductivity.
They are often used in applications where electrical conductivity is necessary, such as electronic components and sensors.
Nanoclays provide excellent barrier properties, making them suitable for packaging materials that need to protect contents from moisture or gases.
The addition of nanosilica improves wear resistance, extending the lifespan of components used in high-stress environments.
Benefits of Using Nanotechnology in Plastics
The integration of nanotechnology offers numerous benefits, making it an attractive option for manufacturers.
Improved strength and durability are among the most significant advantages, allowing products to withstand harsh conditions and reduce the need for frequent replacements.
Thermal stability is another critical factor for applications subjected to extreme temperatures, such as automotive and aerospace components.
Nanocomposites can maintain their mechanical integrity and prevent degradation under high heat.
Enhanced chemical resistance is particularly valuable for medical devices and components exposed to corrosive substances.
Nanotechnology allows these plastics to endure aggressive environments without compromising performance.
Manufacturing Methods of High-Performance Nanocomposites
The development of high-performance plastics using nanotechnology involves several manufacturing methods.
Each method has its own set of advantages, making it suitable for specific applications and material requirements.
Melt Compounding
Melt compounding is a widely used method for incorporating nanoparticles into a polymer matrix.
This process involves melting the polymer and dispersing nanoparticles into it, followed by cooling to form a solid composite.
The advantage of melt compounding is its adaptability to existing processing equipment, making it cost-effective for large-scale production.
The challenge, however, lies in achieving a uniform dispersion of nanoparticles, as agglomeration can reduce the material’s performance.
Solution Casting
Solution casting involves dissolving both the polymer and nanoparticles in a suitable solvent, followed by precipitation and drying to remove the solvent.
This method allows for better control over nanoparticle dispersion and is typically used for producing thin films and coatings.
Though solution casting offers high-quality results, it may not be as scalable as other methods due to the need for solvent recovery and disposal.
In-Situ Polymerization
In-situ polymerization involves dispersing nanoparticles in monomers or pre-polymers, which are then polymerized to form a solid nanocomposite.
This method allows for excellent nanoparticle distribution and strong interfacial bonding, resulting in superior mechanical properties.
However, in-situ polymerization requires careful control of reaction conditions and may be limited by the choice of monomers that are compatible with nanoparticles.
Applications of High-Performance Nanocomposites
High-performance nanocomposites are used in a wide range of industries, each benefiting from the unique properties imparted by nanotechnology.
Automotive Industry
In the automotive industry, nanocomposites are utilized for components that demand lightweight construction and high strength, such as bumpers, engine covers, and fuel systems.
Their use contributes to improved fuel efficiency and reduced emissions.
Nanocomposites with enhanced thermal stability are also used in under-the-hood applications, where high temperatures are commonplace.
Electronics and Telecommunications
Nanotechnologies are critical in the electronics sector, where miniaturization and improved performance are continually sought.
High-performance plastics are used for circuit boards, connectors, and enclosures, providing the necessary electrical insulation and thermal management.
Enhanced conductivity, obtained from nanomaterials like carbon nanotubes, is crucial in developing flexible electronics and wearable devices.
Medical Devices
The medical industry benefits from nanocomposites’ excellent biocompatibility and chemical resistance.
Applications include surgical instruments, diagnostic equipment, and prosthetic devices.
Nanocomposites can also be tailored to provide antimicrobial properties, which are essential in maintaining sterility and preventing infections.
Challenges and Future Prospects
While nanotechnology has revolutionized the development of high-performance plastics, several challenges remain.
Achieving uniform nanoparticle dispersion remains a significant hurdle, as it directly affects the material’s properties.
Cost is another consideration, with nanomaterials often being expensive compared to traditional fillers.
Efforts to scale production while maintaining quality and consistency continue to be critical areas of research.
Looking to the future, advances in nanotechnology promise even greater enhancements to high-performance plastics.
Research is focusing on developing sustainable and environmentally friendly processes, as well as expanding the range of nanomaterials available for use.
By overcoming current limitations, high-performance nanocomposites will find broader applications and contribute significantly to technological advancements across various industries.
資料ダウンロード
QCD管理受発注クラウド「newji」は、受発注部門で必要なQCD管理全てを備えた、現場特化型兼クラウド型の今世紀最高の受発注管理システムとなります。
ユーザー登録
受発注業務の効率化だけでなく、システムを導入することで、コスト削減や製品・資材のステータス可視化のほか、属人化していた受発注情報の共有化による内部不正防止や統制にも役立ちます。
NEWJI DX
製造業に特化したデジタルトランスフォーメーション(DX)の実現を目指す請負開発型のコンサルティングサービスです。AI、iPaaS、および先端の技術を駆使して、製造プロセスの効率化、業務効率化、チームワーク強化、コスト削減、品質向上を実現します。このサービスは、製造業の課題を深く理解し、それに対する最適なデジタルソリューションを提供することで、企業が持続的な成長とイノベーションを達成できるようサポートします。
製造業ニュース解説
製造業、主に購買・調達部門にお勤めの方々に向けた情報を配信しております。
新任の方やベテランの方、管理職を対象とした幅広いコンテンツをご用意しております。
お問い合わせ
コストダウンが利益に直結する術だと理解していても、なかなか前に進めることができない状況。そんな時は、newjiのコストダウン自動化機能で大きく利益貢献しよう!
(β版非公開)