- お役立ち記事
- Development contract process from design to evaluation of control equipment for energy and FA fields
月間77,185名の
製造業ご担当者様が閲覧しています*
*2025年2月28日現在のGoogle Analyticsのデータより
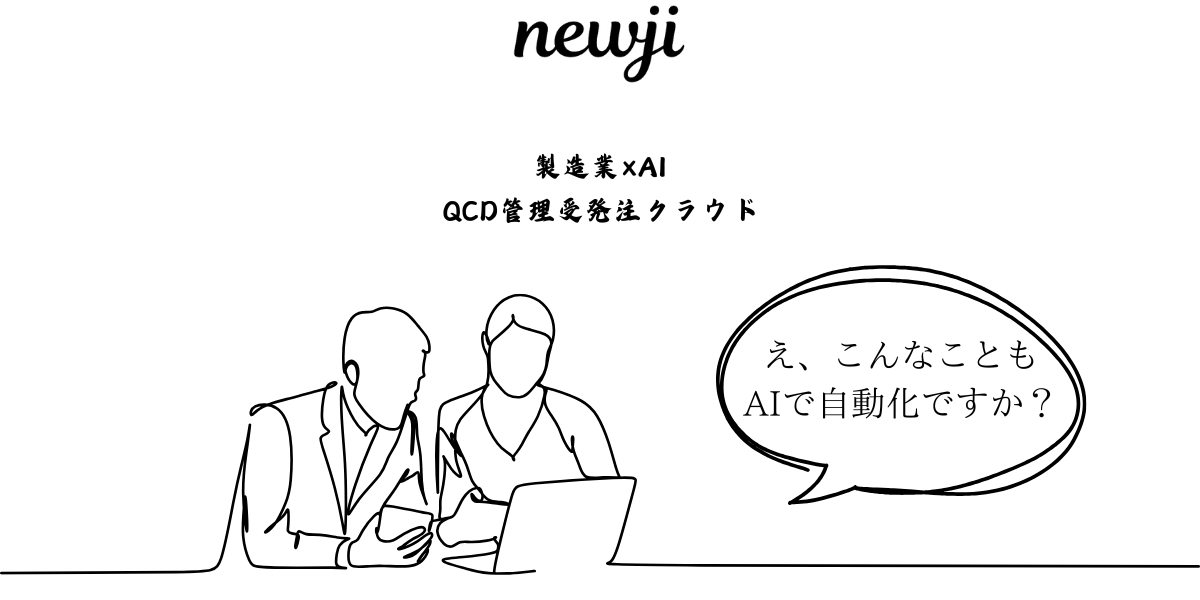
Development contract process from design to evaluation of control equipment for energy and FA fields
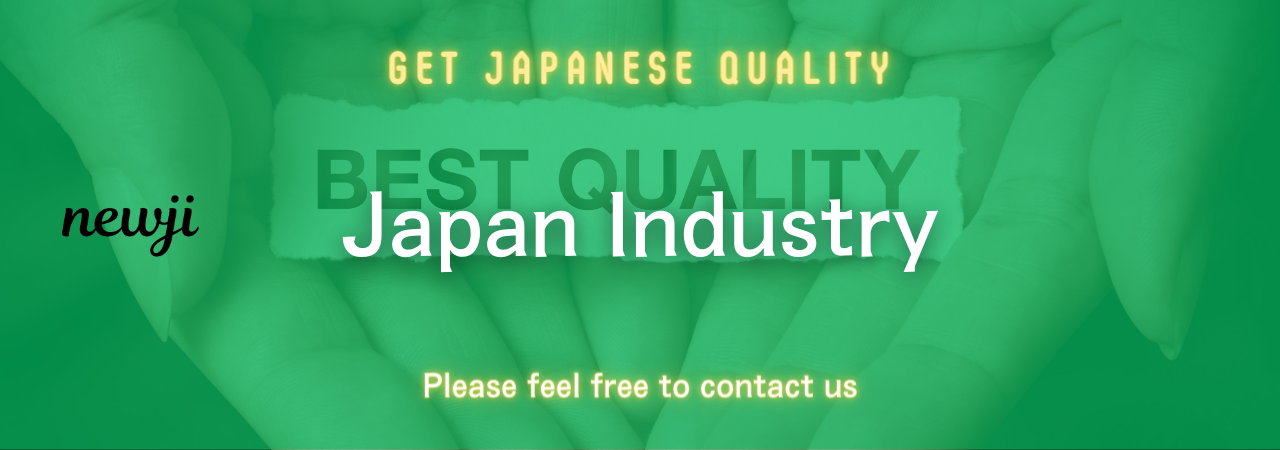
目次
Introduction to Control Equipment Development
In the realm of energy and factory automation (FA) fields, control equipment plays a pivotal role.
These systems help in enhancing productivity, maintaining precision, and ensuring the safety of operations.
Developing control equipment involves several critical phases, from initial design to the final evaluation.
Understanding this process can significantly benefit those engaged in or planning to enter this industry.
Design Phase of Control Equipment
The design phase lays the foundation for successful control equipment development.
It begins with comprehensive research and requirements gathering.
At this stage, collaboration with stakeholders, clients, and potential end-users is essential to understand the specific needs and expectations.
With a clear understanding of the requirements, design engineers start creating blueprints.
The design phase often utilizes computer-aided design (CAD) tools to create detailed schematics and models.
These tools allow engineers to visualize the control system, identify potential issues, and make necessary modifications early in the process.
During this phase, engineers must also consider factors like cost-effectiveness, energy efficiency, and scalability.
Ensuring that the design can adapt to future advancements is crucial for long-term success.
Control System Architecture
A vital component of the design is the control system architecture.
This includes deciding on the type of controllers to be used, such as programmable logic controllers (PLC) or distributed control systems (DCS).
Selecting the appropriate sensors, actuators, and communication networks also falls under this category.
The architecture should support seamless integration of all components to achieve optimal performance.
Development and Testing Phase
Once the design is finalized, the project moves into the development and testing phase.
This is where theoretical designs are transformed into physical prototypes.
During development, software engineers write and test code that will control the equipment.
Simultaneously, hardware components are assembled.
Integration of hardware and software is a delicate process that requires careful attention to detail.
Testing is an integral part of this phase.
Each component must undergo rigorous testing to ensure it meets the design specifications.
Common tests include functional testing, stress testing, and interoperability testing.
These tests help identify any discrepancies or faults that need addressing before progressing to the next stage.
Prototyping
Developing a working prototype is crucial in bridging the gap between design and full-scale production.
Prototyping allows engineers to evaluate the practicality of the design.
It provides an opportunity to make iterative improvements based on real-world testing feedback.
A prototype can also be advantageous for securing stakeholder approval, providing a tangible representation of the final product.
Integration and Production Phase
After successful testing and prototyping, the project moves into the integration and production phase.
At this point, production engineers and technicians work together to ensure that all components fit together seamlessly and function as intended.
Production involves scaling the successful prototype into a full-scale working model.
This requires meticulous planning to ensure that materials, labor, and scheduling align with project goals and timelines.
Quality Assurance
Quality assurance (QA) is vital during production.
QA processes ensure that each unit produced meets the required standards and specifications.
This involves ongoing inspections and tests to uphold the integrity and performance of the control equipment.
Implementation and Evaluation Phase
The final stage in the development contract process is the implementation and evaluation phase.
At this point, the control equipment is deployed in its operational environment.
The implementation phase often includes training operators and maintenance staff to ensure they understand how to use the equipment effectively.
Proper training minimizes downtime and maximizes efficiency.
Performance Evaluation
After implementation, the focus shifts to performance evaluation.
This involves monitoring the control system to ensure it operates as expected.
Any issues that arise must be addressed promptly to maintain optimal performance.
Feedback collected during this phase is invaluable.
It helps in further refining the system and may inform future development projects.
Conclusion
The development contract process for control equipment in the energy and FA fields is comprehensive, encompassing design, development, production, and evaluation phases.
Each phase plays a crucial role in ensuring that the final product meets expectations in terms of functionality, efficiency, and reliability.
Understanding these stages can aid professionals in navigating the complexities of developing control systems effectively.
It also highlights the importance of collaboration, rigorous testing, and quality assurance in achieving successful outcomes.
資料ダウンロード
QCD管理受発注クラウド「newji」は、受発注部門で必要なQCD管理全てを備えた、現場特化型兼クラウド型の今世紀最高の受発注管理システムとなります。
ユーザー登録
受発注業務の効率化だけでなく、システムを導入することで、コスト削減や製品・資材のステータス可視化のほか、属人化していた受発注情報の共有化による内部不正防止や統制にも役立ちます。
NEWJI DX
製造業に特化したデジタルトランスフォーメーション(DX)の実現を目指す請負開発型のコンサルティングサービスです。AI、iPaaS、および先端の技術を駆使して、製造プロセスの効率化、業務効率化、チームワーク強化、コスト削減、品質向上を実現します。このサービスは、製造業の課題を深く理解し、それに対する最適なデジタルソリューションを提供することで、企業が持続的な成長とイノベーションを達成できるようサポートします。
製造業ニュース解説
製造業、主に購買・調達部門にお勤めの方々に向けた情報を配信しております。
新任の方やベテランの方、管理職を対象とした幅広いコンテンツをご用意しております。
お問い合わせ
コストダウンが利益に直結する術だと理解していても、なかなか前に進めることができない状況。そんな時は、newjiのコストダウン自動化機能で大きく利益貢献しよう!
(β版非公開)