- お役立ち記事
- Development method for high-precision three-dimensional measurement technology for aircraft engine parts
月間77,185名の
製造業ご担当者様が閲覧しています*
*2025年2月28日現在のGoogle Analyticsのデータより
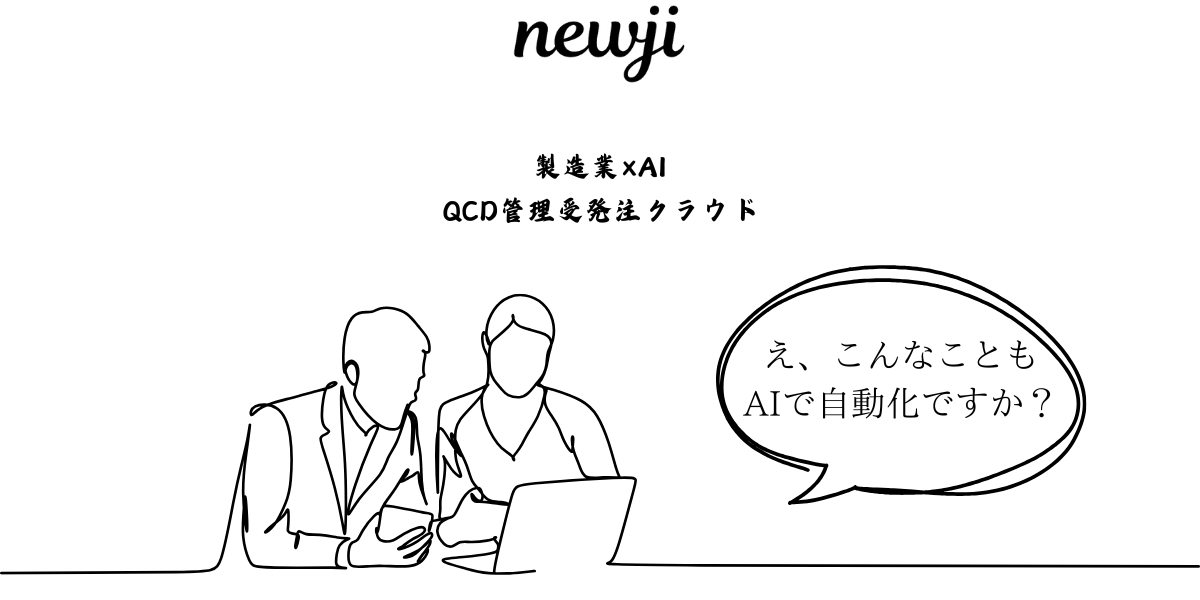
Development method for high-precision three-dimensional measurement technology for aircraft engine parts
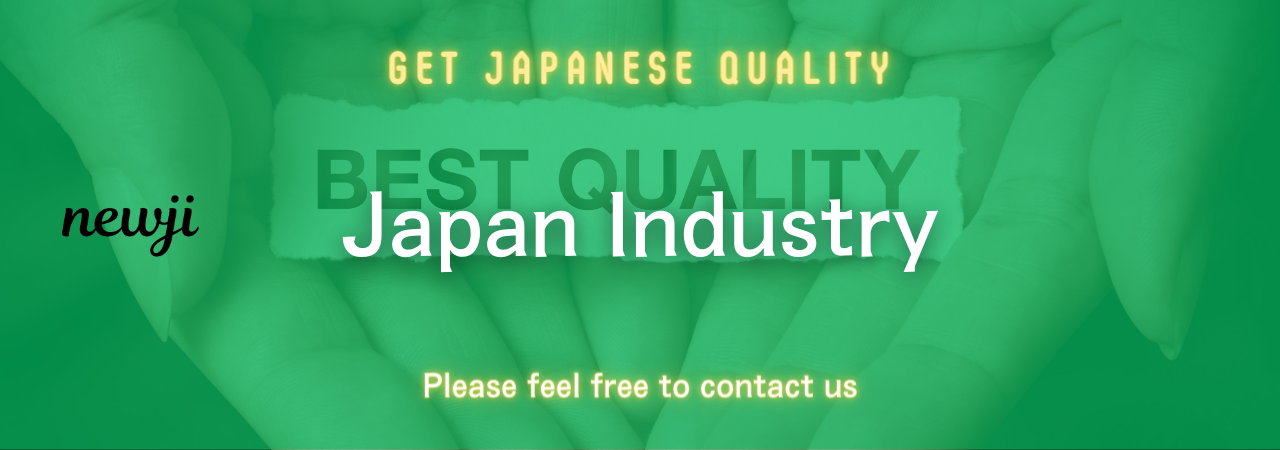
目次
Introduction to High-Precision Three-Dimensional Measurement
In the realm of aerospace engineering, precision is paramount.
Aircraft engine parts are complex and must adhere to exact specifications to ensure safety and performance.
Achieving high-precision measurements for these parts is a critical task, and recent advancements in three-dimensional (3D) measurement technology offer promising solutions.
This article delves into the development methods for high-precision 3D measurement technology used in the inspection and production of aircraft engine components.
Understanding the Need for Precision in Aerospace
The production and maintenance of aircraft require adherence to stringent standards.
Each component must fit perfectly with others to ensure overall functionality and safety.
Minor deviations in measurements can lead to significant issues, such as reduced efficiency or even catastrophic failure.
This makes high-precision measurements a vital part of the aerospace manufacturing process.
Moreover, as aircraft designs become more sophisticated, the complexity of components increases.
Consequently, the need for precise and reliable measurement techniques grows.
The Evolution of 3D Measurement Technology
3D measurement technology has evolved significantly over the years.
Initially, manual tools were used to measure parts, but these lacked the precision needed for modern aerospace requirements.
As technology advanced, digital calipers and coordinate measuring machines (CMMs) became industry staples.
Currently, optical and laser scanning technologies have pushed the boundaries further, enabling even higher precision and faster measurement times.
These advancements not only improve accuracy but also enhance the speed at which measurements can be conducted, thus reducing downtime and improving efficiency in production lines.
Optical Scanning Technologies
Optical scanning technologies are at the forefront of 3D measurement advancements.
These systems use light to capture the shape of objects with remarkable precision.
Structured light scanners project patterns onto surfaces and measure the deformation of the pattern to generate 3D models.
Confocal and interferometric techniques have also been developed, which allow for ultra-precise measurements down to the nanometer scale.
These methods are particularly useful in capturing detailed surface characteristics that were previously difficult to measure with traditional tools.
Laser Scanning Solutions
Laser scanning technologies also play a crucial role in high-precision measurements.
Time-of-flight and triangulation-based laser scanners are commonly used in aerospace for their accuracy and speed.
Time-of-flight scanners measure the time it takes for a laser to return after hitting a surface, calculating distances with high precision.
Triangulation methods use the angle of reflected laser beams to create detailed 3D models of engine parts.
LIDAR technology, commonly used in mapping and navigation, has also found applications in the aerospace industry for measuring large components or assemblies quickly and accurately.
Implementation of 3D Measurement in Aerospace
Incorporating high-precision 3D measurement technology into the aerospace sector involves several steps.
It begins with the evaluation of the specific requirements of the components to be measured, followed by the selection of the appropriate measurement technology.
Training and skill development for personnel is vital, as operating these advanced systems requires specific knowledge and expertise.
Integrating these technologies into existing production and quality control processes is another critical phase, necessitating coordination across various departments.
Case Study: Engine Part Inspection
A practical example of 3D measurement application can be found in the inspection of turbine blades.
Given their complex geometry and critical function, turbine blades demand extreme precision during manufacturing.
Using advanced 3D scanning technologies, every blade is meticulously measured to match the design specifications.
These high-precision measurements ensure that the manufactured blades exhibit optimal aerodynamic performance and durability under operational stresses.
Challenges and Solutions
Despite the advantages, implementing high-precision 3D measurements in aerospace comes with challenges.
One common issue is the calibration and maintenance of the measurement equipment to ensure accuracy over time.
Environmental factors such as temperature fluctuations can also affect measurement outcomes, necessitating the use of controlled environments for scanning processes.
Advanced error-correction algorithms are often incorporated to compensate for these variables to maintain measurement accuracy.
Future Trends in 3D Measurement Technology
As technology continues to advance, the future of high-precision 3D measurement is promising.
The integration of artificial intelligence (AI) and machine learning into measurement systems is expected to further enhance accuracy and efficiency.
AI-driven analysis can automate error detection and correction, while also optimizing measurement strategies based on the complexity of the parts being measured.
The use of virtual and augmented reality in inspections is also an emerging trend.
These technologies can provide real-time feedback and visualization, improving the speed and accuracy of the inspection process.
Meanwhile, continued miniaturization of measurement devices will make them more versatile and adaptable for use in different environments and for measuring smaller parts.
Conclusion
High-precision 3D measurement technology is transforming the aerospace industry by ensuring that every component meets the required standards for safety and performance.
Through the use of advanced optical and laser scanning technologies, aircraft manufacturers can achieve unmatched precision, ultimately enhancing the quality and reliability of aircraft.
The ongoing development and integration of these technologies are paving the way for more efficient and accurate manufacturing and inspection processes in the future.
As the industry moves forward, staying at the cutting edge of measurement technology will be indispensable for maintaining competitiveness and ensuring the highest standards of safety and performance.
資料ダウンロード
QCD管理受発注クラウド「newji」は、受発注部門で必要なQCD管理全てを備えた、現場特化型兼クラウド型の今世紀最高の受発注管理システムとなります。
ユーザー登録
受発注業務の効率化だけでなく、システムを導入することで、コスト削減や製品・資材のステータス可視化のほか、属人化していた受発注情報の共有化による内部不正防止や統制にも役立ちます。
NEWJI DX
製造業に特化したデジタルトランスフォーメーション(DX)の実現を目指す請負開発型のコンサルティングサービスです。AI、iPaaS、および先端の技術を駆使して、製造プロセスの効率化、業務効率化、チームワーク強化、コスト削減、品質向上を実現します。このサービスは、製造業の課題を深く理解し、それに対する最適なデジタルソリューションを提供することで、企業が持続的な成長とイノベーションを達成できるようサポートします。
製造業ニュース解説
製造業、主に購買・調達部門にお勤めの方々に向けた情報を配信しております。
新任の方やベテランの方、管理職を対象とした幅広いコンテンツをご用意しております。
お問い合わせ
コストダウンが利益に直結する術だと理解していても、なかなか前に進めることができない状況。そんな時は、newjiのコストダウン自動化機能で大きく利益貢献しよう!
(β版非公開)