- お役立ち記事
- Development method of highly accurate filler orientation control technology
月間77,185名の
製造業ご担当者様が閲覧しています*
*2025年2月28日現在のGoogle Analyticsのデータより
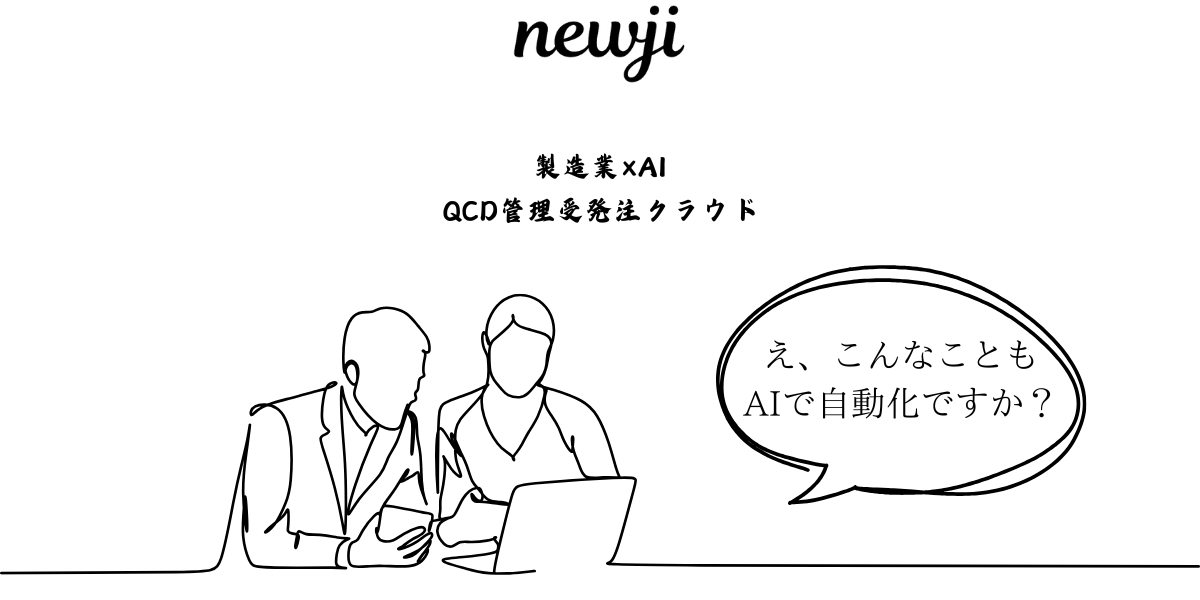
Development method of highly accurate filler orientation control technology
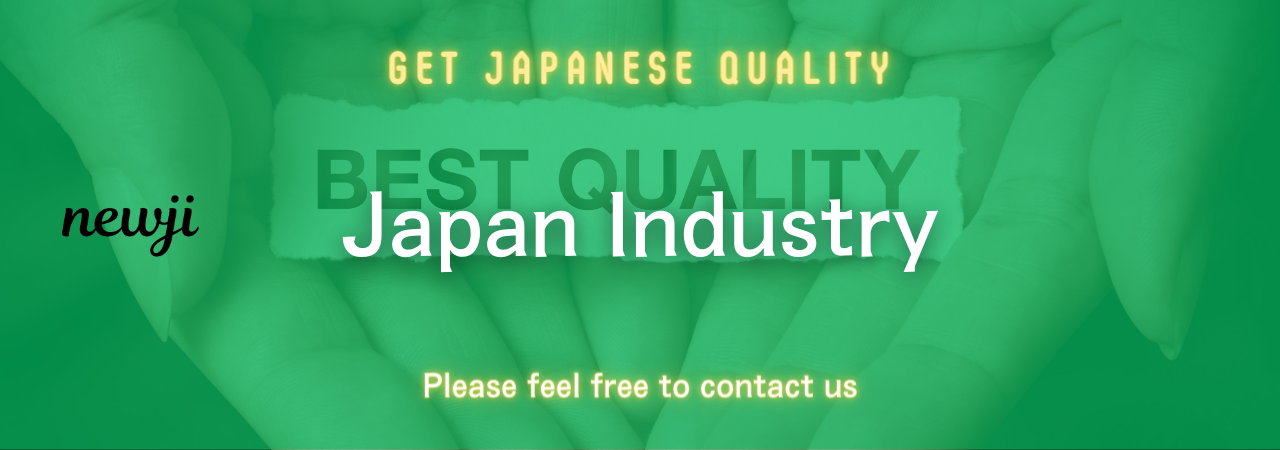
目次
Understanding Filler Orientation Control Technology
Filler orientation control technology is an advanced methodology used in various manufacturing processes to enhance the mechanical properties of composite materials.
Understanding the basics of this technology is crucial for developing precise control methods for various industries, including automotive, aerospace, and consumer electronics.
When fillers are aligned in a specific direction, it improves the strength, stiffness, and overall performance of composite materials.
Filler orientation plays a critical role in determining the mechanical properties of composite materials.
Materials with aligned fillers can withstand greater forces and stresses compared to those with randomly oriented fillers.
This is because orderly alignment allows for an optimized load transfer from the matrix to the fibers, translating into higher mechanical efficiency and reliability.
Steps to Develop an Accurate Filler Orientation Control Method
Step 1: Material Selection
The first step in developing a highly accurate filler orientation control method is selecting the appropriate materials.
Composite materials are commonly composed of a matrix and fillers.
The matrix is typically a polymer, while fillers can range from fibers to particles such as carbon, glass, or ceramics.
These fillers are integral for defining the composite’s final properties, including strength, flexibility, and thermal resistance.
Choosing the right type of filler depends on the desired properties of the final product.
For instance, carbon fibers are preferred for applications requiring high strength and low weight, whereas glass fibers are often used for reducing manufacturing costs.
Research and development teams should conduct a thorough analysis to evaluate which material is suitable for their specific application.
Step 2: Understanding Filler Alignment Techniques
There are various methods for controlling filler orientation, each with its own set of advantages and limitations.
Common techniques include mechanical alignment, electric or magnetic field alignment, and chemical methods.
Mechanical alignment often involves extrusion or rolling processes where fillers are physically oriented in a particular direction.
Electric and magnetic field alignment are advanced techniques where fillers are aligned by applying an external field across the composite.
This method is highly effective for conductive fillers such as carbon nanotubes or metallic particles.
Chemical methods involve surface functionalization, allowing fillers to orient themselves through chemical interactions with the matrix material.
Step 3: Process Optimization and Simulation
Once an alignment method is selected, the next step involves optimizing the process parameters.
This requires a detailed understanding of the material’s rheological properties and the processing conditions.
For ensuring that the fillers are perfectly aligned in the desired direction, simulation tools such as Finite Element Analysis (FEA) can be incredibly beneficial.
Simulations enable engineers to model the behavior of composites under various conditions, allowing them to predict how fillers will orient themselves in the matrix.
This predictive capability is crucial for reducing trial and error in the development phase and establishing a reliable control strategy.
The Role of Technology in Advancing Filler Orientation
Advancements in technology play a pivotal role in enhancing the accuracy of filler orientation control methods.
Innovations such as advanced sensors, real-time data analytics, and machine learning algorithms provide unprecedented insights into the manufacturing process.
Sensors integrated into manufacturing systems can track the orientation of fillers in real-time, enabling instantaneous adjustments to processing conditions.
Real-time data analytics collect valuable performance metrics, which can be analyzed to refine alignment techniques continually.
Machine learning algorithms can assist in identifying patterns and insights from vast sets of data, driving further optimizations.
Role of Automation and AI
Automation and Artificial Intelligence (AI) significantly contribute to advancing filler orientation control technology.
Automated systems reduce human intervention, minimizing errors and ensuring a highly precise and consistent filler orientation.
AI-powered systems predict potential issues and dynamically adjust processing parameters for optimal filler alignment.
These technologies combine to facilitate a self-optimizing manufacturing process that consistently produces high-quality composite materials.
The role of automated and AI-driven approaches is expected to grow in importance in the future, as industries increasingly seek efficient production methods.
Applications of Filler Orientation Control Technology
The practical applications of filler orientation control technology are vast and varied, showing immense potential across multiple sectors.
In the automotive industry, oriented fillers in composites are used to obtain lightweight and strong vehicle components, lowering fuel consumption and enhancing overall performance.
Aerospace applications benefit from advanced filler orientation control, where materials must endure extreme conditions while maintaining structural integrity.
In the field of consumer electronics, controlled filler orientation can lead to the development of durable, high-performance devices with excellent thermal management properties.
This technology also finds applications in the realm of sports equipment, where optimized materials significantly improve athletic performance.
Future Prospects and Challenges
The continuous evolution of filler orientation control technology presents numerous future prospects.
As the technology progresses, it is anticipated to offer even more refined control methods, enhancing the functional properties of composite materials across various industries.
Developments in the application of nanotechnology and the integration of IoT devices in manufacturing processes hold promise for further advancements.
Nevertheless, challenges remain, such as high production costs and the complexity of integrating new technologies into existing manufacturing lines.
Addressing these challenges will require collaboration between researchers, engineers, and industry professionals to innovate and develop cost-effective, scalable solutions.
In conclusion, the development of highly accurate filler orientation control technology is a rapidly evolving field that holds the potential to revolutionize material engineering.
With ongoing research and the adoption of cutting-edge technologies, filler orientation control methods will continue to advance, paving the way for better, more efficient composite materials.
Understanding and implementing these methodologies will be essential for industries aiming to improve their products’ quality, reliability, and performance.
資料ダウンロード
QCD管理受発注クラウド「newji」は、受発注部門で必要なQCD管理全てを備えた、現場特化型兼クラウド型の今世紀最高の受発注管理システムとなります。
ユーザー登録
受発注業務の効率化だけでなく、システムを導入することで、コスト削減や製品・資材のステータス可視化のほか、属人化していた受発注情報の共有化による内部不正防止や統制にも役立ちます。
NEWJI DX
製造業に特化したデジタルトランスフォーメーション(DX)の実現を目指す請負開発型のコンサルティングサービスです。AI、iPaaS、および先端の技術を駆使して、製造プロセスの効率化、業務効率化、チームワーク強化、コスト削減、品質向上を実現します。このサービスは、製造業の課題を深く理解し、それに対する最適なデジタルソリューションを提供することで、企業が持続的な成長とイノベーションを達成できるようサポートします。
製造業ニュース解説
製造業、主に購買・調達部門にお勤めの方々に向けた情報を配信しております。
新任の方やベテランの方、管理職を対象とした幅広いコンテンツをご用意しております。
お問い合わせ
コストダウンが利益に直結する術だと理解していても、なかなか前に進めることができない状況。そんな時は、newjiのコストダウン自動化機能で大きく利益貢献しよう!
(β版非公開)