- お役立ち記事
- Development of next-generation antistatic paint and application in electronics manufacturing environment
月間76,176名の
製造業ご担当者様が閲覧しています*
*2025年3月31日現在のGoogle Analyticsのデータより
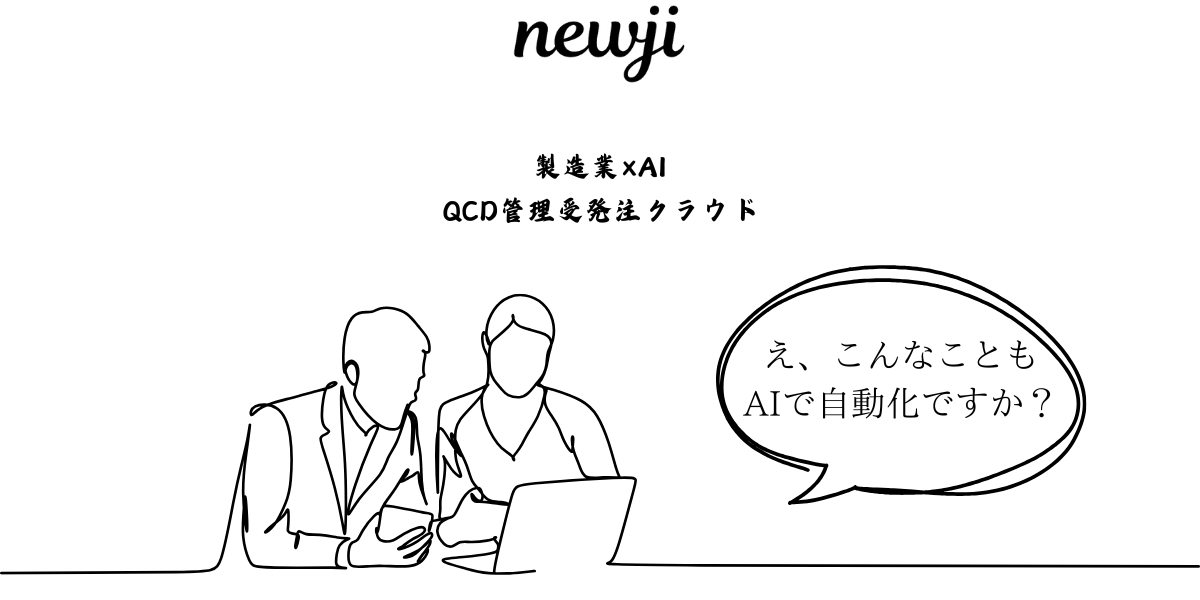
Development of next-generation antistatic paint and application in electronics manufacturing environment
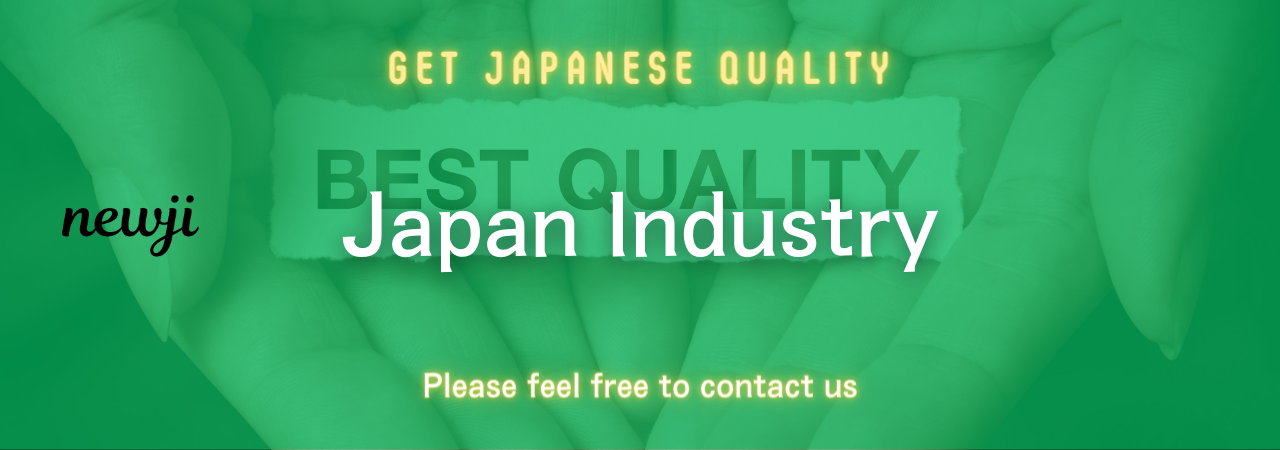
目次
Understanding Antistatic Paint
Antistatic paint is an innovative solution designed to combat static electricity, a common problem in various industries, particularly in electronics manufacturing.
Static electricity can cause significant damage to sensitive electronic components during production, handling, and even after installation.
Antistatic paint works by reducing the buildup of static charge on surfaces, which can otherwise lead to sudden discharges that might damage electronic circuits.
In recent years, research and development in the field of next-generation antistatic paints have led to more effective and versatile products.
These new formulations are engineered to offer improved performance while catering to the specific needs of the electronics manufacturing environment.
Understanding these advancements and their applications is crucial for manufacturers looking to enhance their processes and protect their products.
Why Is Antistatic Paint Important in Electronics Manufacturing?
Electronics manufacturing involves delicate processes where even the slightest disruption can have significant consequences.
Static electricity is one such disruption that can lead to irreparable damage to sensitive electronic components.
When static charge builds up on surfaces, it can discharge unpredictably, potentially resulting in the failure of electronic circuits and components.
The deployment of antistatic paint helps in mitigating these risks by creating a conductive path that dissipates static charges safely.
This is essential in maintaining the integrity and functionality of the components being manufactured.
Moreover, in facilities where sensitive electronics are produced, controlling the environment to prevent static discharges is of utmost importance.
Reducing Production Downtime
One of the primary advantages of using antistatic paint in electronics manufacturing is the reduction of production downtime.
Unplanned stoppages due to equipment failure or damaged components caused by electrostatic discharge can be costly.
By applying antistatic paint, manufacturers can significantly reduce these risks, leading to more efficient production lines and fewer interruptions.
Enhancing Product Quality
The use of antistatic paint also contributes to the overall quality of the final product.
Protecting electronic components from static discharge during manufacturing ensures that they perform as intended once in use.
This not only enhances the reliability of the product but also boosts customer satisfaction and trust in the brand.
Developments in Next-Generation Antistatic Paint
The development of next-generation antistatic paints involves integrating advanced materials and technologies to create more effective solutions.
These new products are formulated to provide better conductivity, durability, and ease of application compared to traditional antistatic paints.
Nanotechnology Integration
One of the key advancements in antistatic paint technology is the incorporation of nanotechnology.
By utilizing nanoparticles, manufacturers can create paints with enhanced electrical conductivity and improved adhesion properties.
Nanoparticles also contribute to the overall durability of the paint, ensuring that the antistatic properties last longer, even in demanding environments.
Environmentally Friendly Formulations
Another noteworthy development in this field is the creation of environmentally friendly antistatic paints.
As industries become more conscious of their environmental impact, there is a growing demand for paints that are free from volatile organic compounds (VOCs) and other harmful substances.
New formulations use sustainable materials and processes, making them safer for workers and reducing their ecological footprint.
Customization for Specific Applications
Next-generation antistatic paints are also being developed to meet the specific requirements of different applications within electronics manufacturing.
Manufacturers can tailor these paints to provide optimal performance based on the unique conditions of their production environments.
This level of customization ensures that the paint’s antistatic properties are maximized, providing better protection for electronic components.
Applying Antistatic Paint in Electronics Manufacturing
For manufacturers seeking to implement next-generation antistatic paint in their facilities, understanding the application process is crucial.
Proper application of the paint ensures that its full potential is realized, providing the best protection against static electricity.
Surface Preparation
The first step in applying antistatic paint is thorough surface preparation.
This involves cleaning and, if necessary, priming the surfaces to ensure that the paint adheres properly.
Any existing dust, debris, or contaminants must be removed to achieve optimal results.
Application Techniques
There are various techniques available for applying antistatic paint, including brushing, rolling, and spraying.
The choice of technique depends on the specific requirements of the manufacturing environment and the surface area that needs to be covered.
Spraying is often preferred for large or intricate surfaces as it provides an even coat, ensuring consistent antistatic properties.
Drying and Curing
Once applied, the paint must be allowed to dry and cure properly to activate its antistatic properties fully.
Manufacturers should adhere to the drying times specified by the paint manufacturer to ensure the best results.
The Future of Antistatic Paint in Electronics Manufacturing
As technology continues to evolve, the demand for more efficient and effective static control solutions will persist.
The development of next-generation antistatic paints represents a significant step forward in protecting sensitive electronic components from the harmful effects of static electricity.
Looking ahead, we can expect further innovations that will enhance the functionality and application of antistatic paints.
These advancements will contribute to improved safety, efficiency, and product quality in electronics manufacturing, ultimately supporting the growth and success of the industry.
資料ダウンロード
QCD管理受発注クラウド「newji」は、受発注部門で必要なQCD管理全てを備えた、現場特化型兼クラウド型の今世紀最高の受発注管理システムとなります。
ユーザー登録
受発注業務の効率化だけでなく、システムを導入することで、コスト削減や製品・資材のステータス可視化のほか、属人化していた受発注情報の共有化による内部不正防止や統制にも役立ちます。
NEWJI DX
製造業に特化したデジタルトランスフォーメーション(DX)の実現を目指す請負開発型のコンサルティングサービスです。AI、iPaaS、および先端の技術を駆使して、製造プロセスの効率化、業務効率化、チームワーク強化、コスト削減、品質向上を実現します。このサービスは、製造業の課題を深く理解し、それに対する最適なデジタルソリューションを提供することで、企業が持続的な成長とイノベーションを達成できるようサポートします。
製造業ニュース解説
製造業、主に購買・調達部門にお勤めの方々に向けた情報を配信しております。
新任の方やベテランの方、管理職を対象とした幅広いコンテンツをご用意しております。
お問い合わせ
コストダウンが利益に直結する術だと理解していても、なかなか前に進めることができない状況。そんな時は、newjiのコストダウン自動化機能で大きく利益貢献しよう!
(β版非公開)