- お役立ち記事
- Die-casting defect mechanism and countermeasure technology, as well as high-quality and long-life mold technology
Die-casting defect mechanism and countermeasure technology, as well as high-quality and long-life mold technology
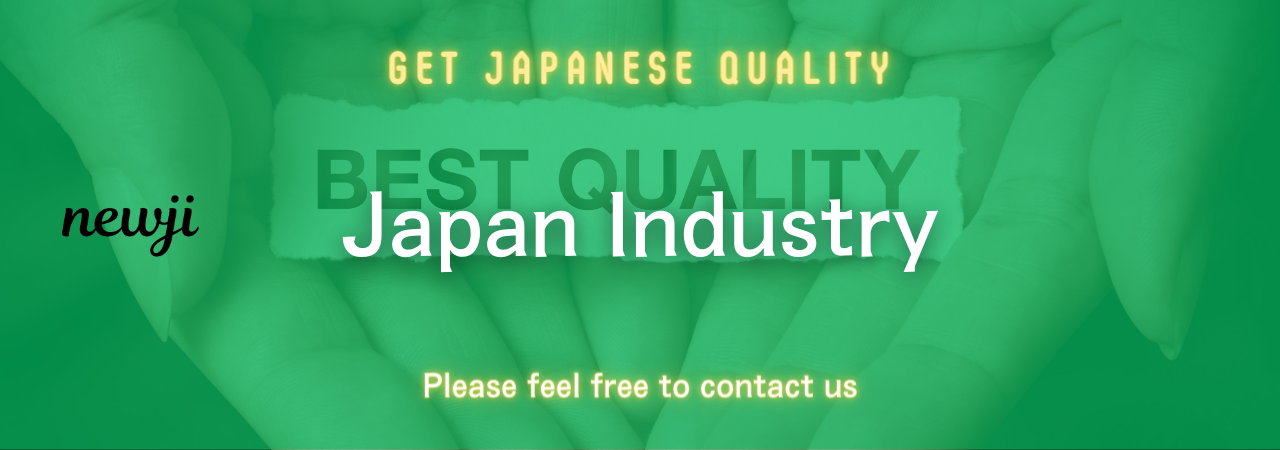
目次
Understanding Die-Casting Defects
Die-casting is a manufacturing process that involves forcing molten metal under high pressure into a mold cavity.
While this method is efficient and cost-effective, it can sometimes result in defects.
Understanding these defects and their root causes is crucial for improving product quality and prolonging the life of molds.
Common Defects in Die-Casting
Several types of defects can occur in die-casting, each caused by various factors.
Some common defects include porosity, cold shuts, and shrinkage.
Porosity is the presence of small voids or pores within the casting.
This defect often occurs due to air entrapment or gas release during the cooling process.
Cold shuts are lines or seams visible on the surface of the casting, indicating incomplete fusion of metal flows.
This defect occurs when two streams of molten metal do not cool quickly enough to fuse, often due to low injection temperatures or insufficient pressure.
Shrinkage refers to the localized contraction of metal as it cools, leading to voids or cavities within the casting.
Mechanisms Behind Die-Casting Defects
To effectively counteract these defects, it’s essential to understand the mechanisms behind them.
Porosity can be caused by impurities within the metal, improper temperature control, or inadequate venting within the mold.
For cold shuts, insufficient temperature or speed during the injection process can result in molten metal solidifying before fully filling the mold.
This issue often arises from incorrect machine settings or suboptimal mold design.
Shrinkage is primarily a result of improper cooling rates and can be addressed by adjusting the cooling time or redesigning the mold to better accommodate metal contraction.
Preventing Die-Casting Defects
Prevention of defects is possible through careful control of the die-casting process.
Ensuring that the mold and metal temperatures are optimal is crucial.
Using high-quality materials and maintaining equipment can also minimize the risk of defects.
Proper venting and gating design are equally important to prevent gas entrapment.
Regular inspection and maintenance of molds can help identify any potential issues before they lead to defects.
Countermeasure Technologies in Die-Casting
Advances in technology provide new ways to counteract common defects in die-casting.
Real-time monitoring systems can track temperature and pressure throughout the process, allowing for adjustments before defects occur.
Simulation software can predict potential problem areas in a design before production begins.
This allows engineers to modify mold designs to minimize the risk of defects like porosity and cold shuts.
Vacuum die-casting is another technology used to reduce porosity by minimizing air entrapment during molding.
By drawing a vacuum, air is removed from the mold cavity, ensuring denser, higher-quality castings.
Improving Mold Quality and Longevity
High-quality molds are essential for producing defect-free products and ensuring efficient production cycles.
Material choice plays a critical role in mold longevity.
Using durable materials that can withstand high temperatures and pressures extends the life of the mold.
Regular cleaning and maintenance prevent wear and tear, which can otherwise lead to defects.
Applying surface coatings can also protect molds from corrosion and thermal fatigue.
Optimizing the design of the mold can improve heat dissipation, reducing cooling times and preventing shrinkage-related defects.
Incorporating cooling channels within the mold design can help maintain consistent temperatures.
High-Quality Die-Casting Practices
Implementing best practices in the die-casting process can significantly enhance the quality and longevity of molds.
Consistent monitoring and control of production parameters is essential.
Training and knowledge sharing among workers can help maintain attention to detail and understanding of potential defect causes.
Using specialized lubricants can reduce friction and wear on molds, further extending their lifespan.
Periodically reviewing and updating die-casting processes with the latest technological advancements can lead to more efficient production and reduced defect rates.
By maintaining high standards and using comprehensive techniques, defects in die-casting can be minimized substantially, resulting in high-quality products that meet rigorous industry standards.
In summary, understanding and mitigating die-casting defects involves a multifaceted approach that includes a thorough understanding of defect mechanisms, technological innovations, and proactive process management.
These practices not only enhance product quality but also ensure the prolonged use and efficiency of molds in production.
資料ダウンロード
QCD調達購買管理クラウド「newji」は、調達購買部門で必要なQCD管理全てを備えた、現場特化型兼クラウド型の今世紀最高の購買管理システムとなります。
ユーザー登録
調達購買業務の効率化だけでなく、システムを導入することで、コスト削減や製品・資材のステータス可視化のほか、属人化していた購買情報の共有化による内部不正防止や統制にも役立ちます。
NEWJI DX
製造業に特化したデジタルトランスフォーメーション(DX)の実現を目指す請負開発型のコンサルティングサービスです。AI、iPaaS、および先端の技術を駆使して、製造プロセスの効率化、業務効率化、チームワーク強化、コスト削減、品質向上を実現します。このサービスは、製造業の課題を深く理解し、それに対する最適なデジタルソリューションを提供することで、企業が持続的な成長とイノベーションを達成できるようサポートします。
オンライン講座
製造業、主に購買・調達部門にお勤めの方々に向けた情報を配信しております。
新任の方やベテランの方、管理職を対象とした幅広いコンテンツをご用意しております。
お問い合わせ
コストダウンが利益に直結する術だと理解していても、なかなか前に進めることができない状況。そんな時は、newjiのコストダウン自動化機能で大きく利益貢献しよう!
(Β版非公開)