- お役立ち記事
- Differences Between AGVs and AMRs on Production Lines and Selection Criteria
月間76,176名の
製造業ご担当者様が閲覧しています*
*2025年3月31日現在のGoogle Analyticsのデータより
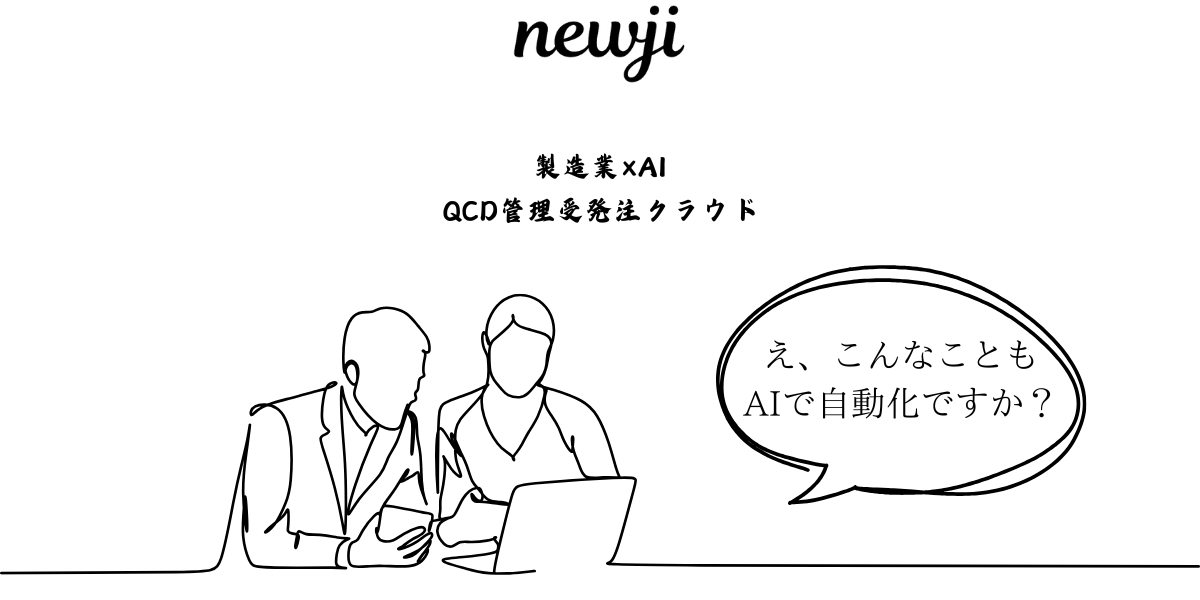
Differences Between AGVs and AMRs on Production Lines and Selection Criteria
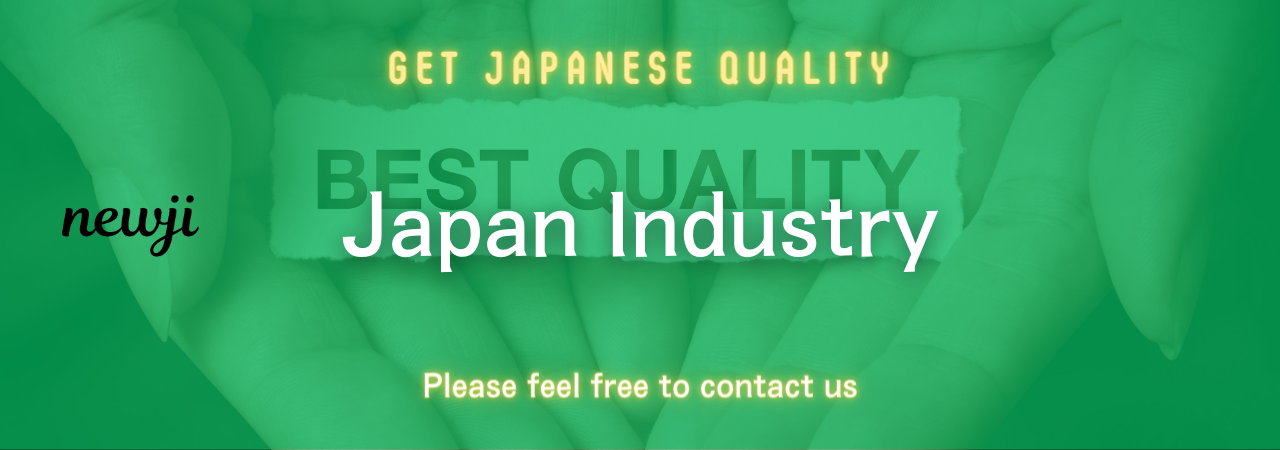
目次
Understanding AGVs and AMRs
When it comes to automating production lines, two terms often come up: Automated Guided Vehicles (AGVs) and Autonomous Mobile Robots (AMRs).
Both AGVs and AMRs play a crucial role in enhancing the efficiency of modern manufacturing processes.
However, they differ in functionality, technology, and application.
Understanding these differences is essential for choosing the right solution for your production line.
What are AGVs?
Automated Guided Vehicles, or AGVs, are mobile robots that follow predefined paths or tracks.
Typically, they navigate using markers, wires, magnetic strips, or optical sensors embedded in the floor, which they follow meticulously without deviation.
This guidance system ensures AGVs maintain a fixed route, making them highly reliable for repetitive tasks.
AGVs are an excellent fit for environments where the layout does not frequently change, such as in straightforward, linear production processes.
They are primarily used for moving raw materials, components, or finished products between fixed points in a warehouse or factory setting.
What are AMRs?
Autonomous Mobile Robots, or AMRs, represent an advanced form of mobile automation.
Unlike AGVs, AMRs possess the ability to understand and interpret their surroundings using sophisticated onboard sensors, cameras, and 3D scanners.
This advanced perception allows AMRs to navigate dynamically within an environment, modifying their paths to avoid obstacles and optimize their routes in real time.
AMRs are particularly beneficial in complex, dynamic environments where flexibility and adaptability are required.
Their ability to operate safely around humans and dynamically reshuffle priorities makes them ideal for various sectors, including order fulfillment, inventory management, and material distribution in unpredictable or changing layouts.
Key Differences Between AGVs and AMRs
Navigation and Flexibility
The most significant difference between AGVs and AMRs is how they navigate a space.
AGVs rely on fixed pathways and external guidance, such as wires or magnetic strips, which limit their flexibility.
Any change in the production line or path requires a manual adjustment of the track, which can disrupt operations and incur additional costs.
Conversely, AMRs use advanced technologies like LiDAR and computer vision to independently understand and navigate their environment.
This flexibility allows AMRs to operate with minimal infrastructure, adapt to new routes efficiently, and immediately respond to unforeseen changes or obstacles in their way.
This capability is particularly advantageous in environments where processes and layouts are constantly evolving.
Implementation Costs and Complexity
Implementing AGVs can be straightforward compared to AMRs due to their reliance on established guiding systems.
However, changes to their paths or layouts can be costly and time-consuming.
AGVs require significant infrastructure investment upfront and continuous maintenance of the guiding systems.
AMRs, while initially more complex and potentially more expensive, offer long-term cost benefits.
Since they don’t depend on fixed guidance systems, the layout redesign costs are minimal.
Their implementation might require an initial investment in software integration and training, but the flexibility and scalability of AMRs can offer superior economic advantages over time.
Applications and Suitability
AGVs are best suited for environments that involve consistent, repetitive transport routes.
Their precision on fixed paths makes them ideal for production lines where the processes and layouts do not frequently change.
Common applications include automotive manufacturing, where parts need to be moved systematically between assembly stations.
AMRs shine in dynamic environments that demand adaptability and real-time decision-making capabilities.
They are ideal for e-commerce warehouses, dynamic production lines, and facilities with high variability in material handling needs.
AMRs can operate efficiently around human workers, collaborate seamlessly, and enhance safety by avoiding obstacles autonomously.
Selection Criteria for Choosing Between AGVs and AMRs
Evaluating Your Operational Needs
When deciding between AGVs and AMRs for your production line, consider the nature and demands of your operation.
If your environment is stable with consistent tasks, an AGV might be appropriate due to its simplicity and reliability.
However, if the operation requires adaptability and involves complex routing and interactive tasks, an AMR would be a better fit.
Assessing Infrastructure and Budget
Infrastructure requirements and budget constraints are crucial factors.
For businesses with limited ability to adjust physical spaces, AMRs provide significant advantages, as they need little to no infrastructure alteration.
In contrast, AGVs require substantial upfront investment in path-setting infrastructure but might be less costly in operation for stable environments.
Future-Proofing and Scalability
If your business anticipates expansion or changes in production processes, favoring AMRs can ensure long-term sustainability.
AMRs offer unparalleled scalability and the ability to integrate new technologies or process alterations without significant reinvestment.
However, in scenarios with predictable scales and processes, AGVs can offer a cost-efficient solution.
Safety Considerations
Operating alongside human workers necessitates a robust safety mechanism.
AMRs come equipped with advanced safety features, making them safer around people as they can anticipate and react to human presence in the workspace.
AGVs offer safety by maintaining a rigid path, reducing unpredictability in specific settings.
Conclusion
Choosing between AGVs and AMRs depends significantly on the specific needs of your production line, the flexibility required, and the existing infrastructure.
Understanding the distinct differences in navigation, flexibility, cost structure, and application suitability will help you make an informed decision.
Whether opting for the precision of AGVs or the adaptability of AMRs, both technologies offer transformative benefits to enhance productivity and efficiency in industrial operations.
資料ダウンロード
QCD管理受発注クラウド「newji」は、受発注部門で必要なQCD管理全てを備えた、現場特化型兼クラウド型の今世紀最高の受発注管理システムとなります。
ユーザー登録
受発注業務の効率化だけでなく、システムを導入することで、コスト削減や製品・資材のステータス可視化のほか、属人化していた受発注情報の共有化による内部不正防止や統制にも役立ちます。
NEWJI DX
製造業に特化したデジタルトランスフォーメーション(DX)の実現を目指す請負開発型のコンサルティングサービスです。AI、iPaaS、および先端の技術を駆使して、製造プロセスの効率化、業務効率化、チームワーク強化、コスト削減、品質向上を実現します。このサービスは、製造業の課題を深く理解し、それに対する最適なデジタルソリューションを提供することで、企業が持続的な成長とイノベーションを達成できるようサポートします。
製造業ニュース解説
製造業、主に購買・調達部門にお勤めの方々に向けた情報を配信しております。
新任の方やベテランの方、管理職を対象とした幅広いコンテンツをご用意しております。
お問い合わせ
コストダウンが利益に直結する術だと理解していても、なかなか前に進めることができない状況。そんな時は、newjiのコストダウン自動化機能で大きく利益貢献しよう!
(β版非公開)