- お役立ち記事
- Differences Between Chemical Polishing and Electrolytic Polishing
月間76,176名の
製造業ご担当者様が閲覧しています*
*2025年3月31日現在のGoogle Analyticsのデータより
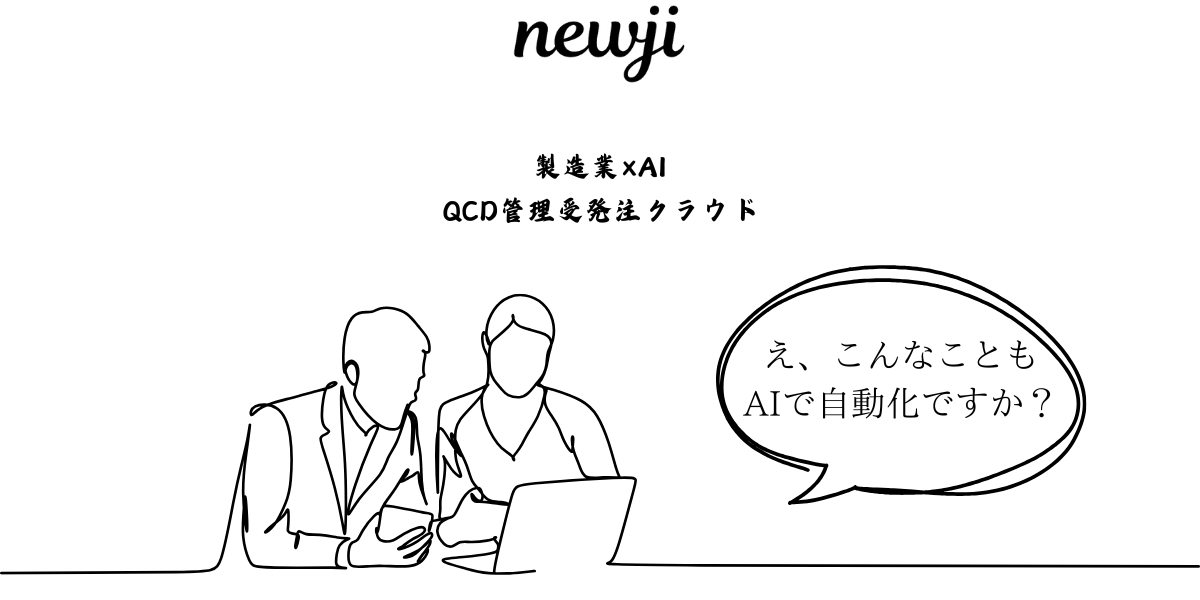
Differences Between Chemical Polishing and Electrolytic Polishing
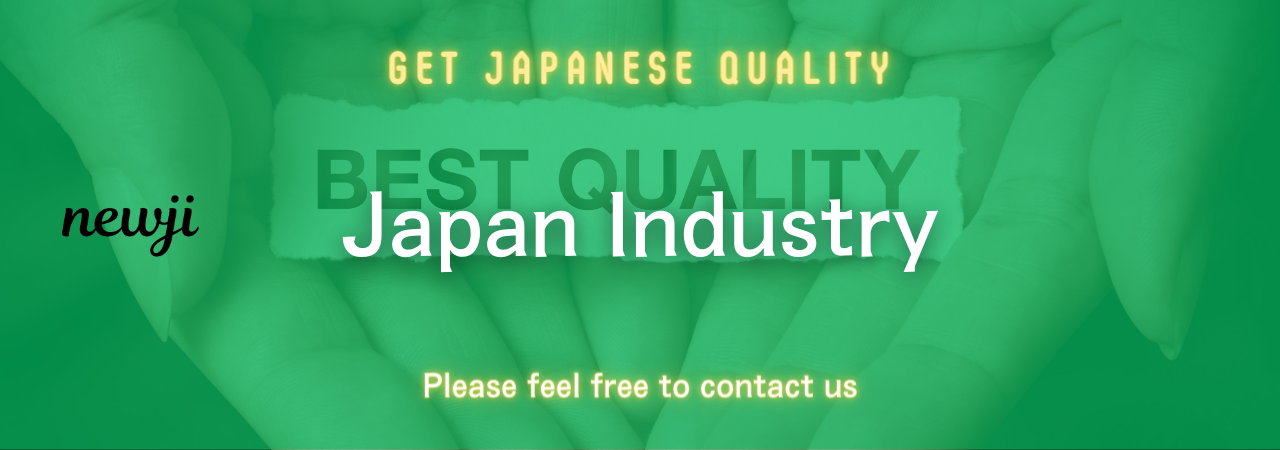
目次
Introduction to Polishing Techniques
Polishing is an essential process in various industries to achieve smooth and glossy surfaces.
Two prevalent methods include chemical polishing and electrolytic polishing.
Both aim to enhance the surface finish but utilize different approaches.
Understanding their differences can help in choosing the appropriate technique for a specific application.
What is Chemical Polishing?
Chemical polishing involves using a chemical solution to remove material from a surface.
This solution, often acidic, interacts with the substrate, dissolving surface irregularities and producing a polished finish.
The process is non-mechanical, relying on chemical reactions rather than physical abrasion.
This method is particularly suitable for complex shapes and intricate details, as the solution can uniformly access all areas.
Chemical polishing is widely used in the metal and jewelry industries due to its ability to deliver a smooth and reflective surface.
The Process of Chemical Polishing
In chemical polishing, substrates are immersed in a chemical bath.
The solution’s composition, temperature, and immersion time are critical factors that influence the polishing quality.
Different materials require specific solutions to achieve optimal results.
For instance, aluminum requires different chemicals compared to stainless steel.
It is essential to control the reaction rate to prevent over-polishing, which can lead to material loss and surface imperfections.
Proper handling and expertise are crucial in ensuring consistent and desirable outcomes.
Understanding Electrolytic Polishing
Electrolytic polishing, also known as electro-polishing, is an electrochemical process used to polish metal surfaces.
Unlike chemical polishing, this method uses an electrical current to expedite the removal of material from the surface.
The process results in a smooth, bright, and highly reflective finish.
Electrolytic polishing is favored for its precision and ability to enhance surface properties, making it ideal for industries such as aerospace, medical devices, and stainless steel manufacturing.
The Electrolytic Polishing Process
In electrolytic polishing, the workpiece acts as the anode and is submerged in an electrolyte bath along with a cathode.
An electrical current passes through the setup, leading to the dissolution of surface material.
The process selectively removes peaks and irregularities, resulting in a uniform finish.
Key parameters like current density, temperature, and electrolyte composition significantly affect the polishing efficiency and quality.
Understanding and maintaining these parameters is critical to achieving the desired finish.
Differences Between Chemical and Electrolytic Polishing
While both methods aim to polish surfaces, their mechanisms and applications differ substantially.
Process Mechanism
Chemical polishing relies solely on chemical reactions, while electrolytic polishing uses both chemicals and electrical current.
This fundamental difference affects their applications and suitability for specific materials and shapes.
Surface Finish and Precision
Electrolytic polishing typically provides a more precise and controlled finish due to its ability to selectively target surface peaks.
This precision is particularly beneficial for critical applications requiring high tolerance and reduced surface roughness.
In contrast, chemical polishing might not achieve the same level of precision, especially for materials with varying chemical resistance.
Applicable Materials
The choice between chemical and electrolytic polishing often depends on the material.
While both techniques can polish metals, electrolytic polishing is preferred for certain stainless steels and complex alloys due to its capability to enhance corrosion resistance.
Chemical polishing is more versatile, handling a broader range of materials, including certain non-metallic surfaces.
Equipment and Complexity
Electrolytic polishing requires more complex equipment, including power sources and precise controls, making it more suitable for industrial setups.
In contrast, chemical polishing setups can be simpler and more flexible, though they require careful handling and waste disposal considerations due to the chemicals involved.
Applications and Use Cases
Both polishing methods find applications across a broad array of industries.
Chemical polishing is widely used in the jewelry industry for enhancing the luster and appearance of precious metals.
It is also prevalent in the automotive and architectural sectors for decorative finishes.
Electrolytic polishing is critical in sectors where surface quality is paramount, such as medical implants, where biocompatibility and cleanliness are essential.
Aerospace components also benefit from this method due to its ability to improve fatigue resistance and corrosion protection.
Choosing the Right Polishing Method
Selecting between chemical and electrolytic polishing depends on several factors, including the material characteristics, desired surface finish, and application requirements.
Cost, environmental considerations, and safety regulations also play a vital role.
For complex and intricate workpieces, chemical polishing offers an advantage due to its ability to reach areas inaccessible to mechanical methods.
However, for applications demanding high precision and consistent quality, electrolytic polishing may be the better choice, despite the higher initial setup cost.
Conclusion
Both chemical and electrolytic polishing provide valuable solutions for enhancing surface finishes, each with its unique benefits and limitations.
Understanding the distinctions between these techniques can aid in making informed decisions tailored to specific industrial needs.
By considering factors such as material compatibility, finish requirements, and cost implications, industries can optimize their polishing processes for desired outcomes.
資料ダウンロード
QCD管理受発注クラウド「newji」は、受発注部門で必要なQCD管理全てを備えた、現場特化型兼クラウド型の今世紀最高の受発注管理システムとなります。
ユーザー登録
受発注業務の効率化だけでなく、システムを導入することで、コスト削減や製品・資材のステータス可視化のほか、属人化していた受発注情報の共有化による内部不正防止や統制にも役立ちます。
NEWJI DX
製造業に特化したデジタルトランスフォーメーション(DX)の実現を目指す請負開発型のコンサルティングサービスです。AI、iPaaS、および先端の技術を駆使して、製造プロセスの効率化、業務効率化、チームワーク強化、コスト削減、品質向上を実現します。このサービスは、製造業の課題を深く理解し、それに対する最適なデジタルソリューションを提供することで、企業が持続的な成長とイノベーションを達成できるようサポートします。
製造業ニュース解説
製造業、主に購買・調達部門にお勤めの方々に向けた情報を配信しております。
新任の方やベテランの方、管理職を対象とした幅広いコンテンツをご用意しております。
お問い合わせ
コストダウンが利益に直結する術だと理解していても、なかなか前に進めることができない状況。そんな時は、newjiのコストダウン自動化機能で大きく利益貢献しよう!
(β版非公開)