- お役立ち記事
- Differences Between Dimensional Tolerance and Geometric Tolerance
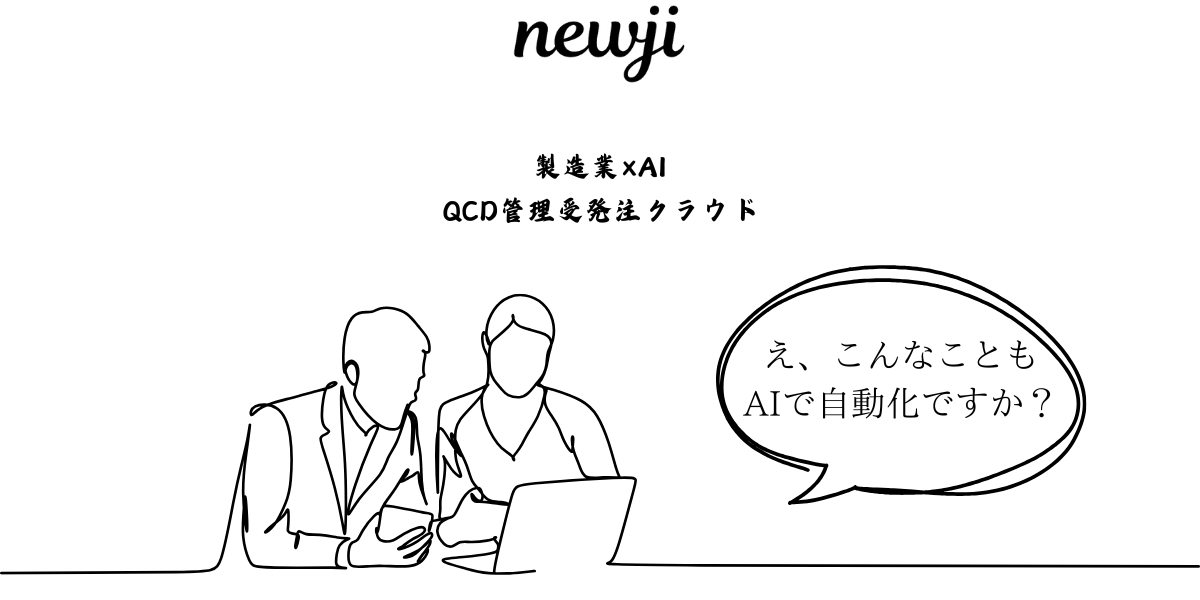
Differences Between Dimensional Tolerance and Geometric Tolerance
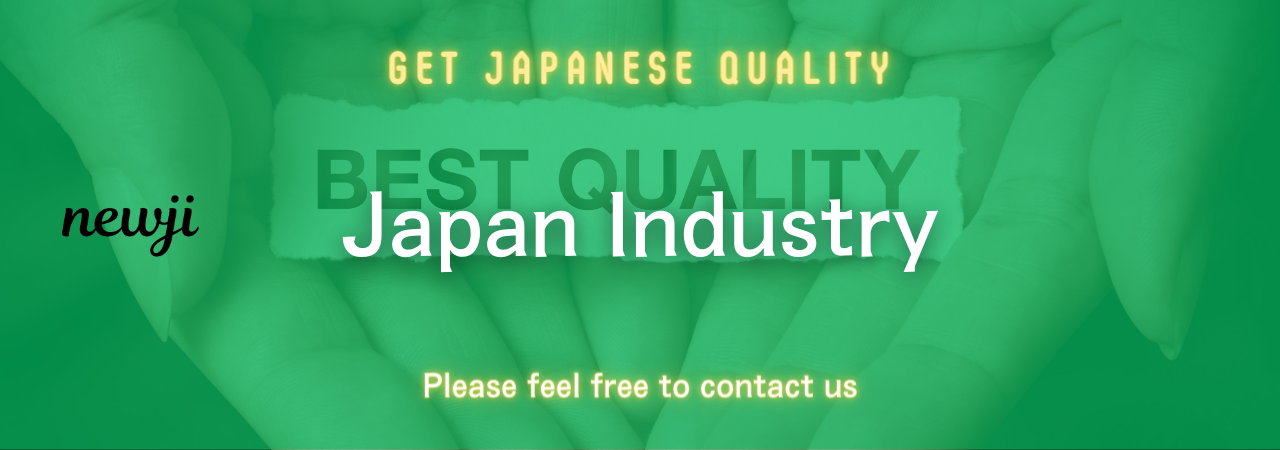
目次
Understanding Dimensional Tolerance
Dimensional tolerance is a critical term in the field of engineering and manufacturing.
It refers to the permissible limit or limits of variation in a physical dimension.
Manufacturers need to keep this in mind while designing and producing parts or components.
It ensures that even if there are slight variations in measurements, the parts will still fit together and function as intended.
For instance, if you’re making a bolt that needs to fit into a nut, both must be made within certain dimensional tolerances to ensure a snug fit.
The idea is to have parts that are interchangeable even when made in different production runs.
Why Dimensional Tolerance Matters
Dimensional tolerance is fundamental to ensuring product quality and consistency.
It helps reduce waste by minimizing the risk of parts being left unusable due to sizing errors.
Additionally, it saves costs and ensures efficiency as precise and accurate parts reduce the chances of rework.
Moreover, it plays a crucial role in maintaining safety standards, especially in industries like aerospace and automotive, where precision is paramount.
Delving into Geometric Tolerance
Geometric tolerance, on the other hand, deals with the shape and positioning of the parts rather than their size.
It provides a more comprehensive description of the part’s design, ensuring that the parts function correctly within an assembly.
Geometric tolerance is crucial when the relationship between different parts matters to ensure proper functionality.
It accounts not just for dimensional aspects but also for characteristics like flatness, angularity, and concentricity.
Importance of Geometric Tolerance
Geometric tolerances allow for a more holistic approach to design and manufacturing.
They ensure that each part will fit as required, even if slight variations occur during production.
This tolerance is essential in complex assemblies where parts must align precisely for the product to function correctly.
It also helps maintain consistency and uniformity, ensuring that each part works seamlessly with others.
Key Differences Between Dimensional and Geometric Tolerances
While both dimensional and geometric tolerances aim to ensure precision, they serve different purposes.
Dimensional tolerance is focused on the size of the part, ensuring it fits within specified limits.
In contrast, geometric tolerance focuses on the shape of the part and how it relates to other parts.
This means that a part can be within dimensional tolerance limits but still fail to meet geometric tolerance requirements.
Application in the Real World
In practice, dimensional and geometric tolerances are often used together to achieve desired quality and functionality.
Dimensional tolerance might dictate the diameter of a hole, while geometric tolerance will ensure that hole is perfectly round and positioned precisely where needed.
Both tolerances are critical to ensuring that products perform as intended in real-world conditions.
Different industries prioritize these tolerances based on their unique needs.
For example, the automotive industry places high importance on both tolerances to ensure safety and performance.
How to Measure Tolerances Effectively
Measurement is crucial when dealing with both dimensional and geometric tolerances.
Using advanced measurement tools such as calipers, micrometers, and coordinate measuring machines (CMM), producers can achieve the required precision.
With technological advancements, the measurement process is becoming more accurate and efficient, reducing the margin of error.
This precision is paramount in ensuring that tolerances are maintained and quality standards are met.
Challenges in Managing Tolerances
While tolerances are crucial, managing them poses certain challenges.
One major challenge is ensuring that all parts produced meet the specified tolerances, which can be difficult for complex designs.
Another challenge is the cost associated with maintaining tight tolerances, which can be high.
This requires striking a balance between precision and production costs.
Finally, ensuring consistency across large production runs can be a hurdle, necessitating stringent quality control measures.
Conclusion
Both dimensional and geometric tolerances are integral to the design and manufacturing process.
While they have distinct roles, they often work in tandem to produce parts that meet stringent quality and functionality standards.
As manufacturing technology continues to advance, the precision and management of these tolerances will continue to improve.
Understanding and applying the right tolerances is crucial for anyone involved in manufacturing or engineering, ensuring that products are safe, reliable, and of high quality.
資料ダウンロード
QCD調達購買管理クラウド「newji」は、調達購買部門で必要なQCD管理全てを備えた、現場特化型兼クラウド型の今世紀最高の購買管理システムとなります。
ユーザー登録
調達購買業務の効率化だけでなく、システムを導入することで、コスト削減や製品・資材のステータス可視化のほか、属人化していた購買情報の共有化による内部不正防止や統制にも役立ちます。
NEWJI DX
製造業に特化したデジタルトランスフォーメーション(DX)の実現を目指す請負開発型のコンサルティングサービスです。AI、iPaaS、および先端の技術を駆使して、製造プロセスの効率化、業務効率化、チームワーク強化、コスト削減、品質向上を実現します。このサービスは、製造業の課題を深く理解し、それに対する最適なデジタルソリューションを提供することで、企業が持続的な成長とイノベーションを達成できるようサポートします。
オンライン講座
製造業、主に購買・調達部門にお勤めの方々に向けた情報を配信しております。
新任の方やベテランの方、管理職を対象とした幅広いコンテンツをご用意しております。
お問い合わせ
コストダウンが利益に直結する術だと理解していても、なかなか前に進めることができない状況。そんな時は、newjiのコストダウン自動化機能で大きく利益貢献しよう!
(Β版非公開)