- お役立ち記事
- Differences Between Forecasted Production and Planned Production
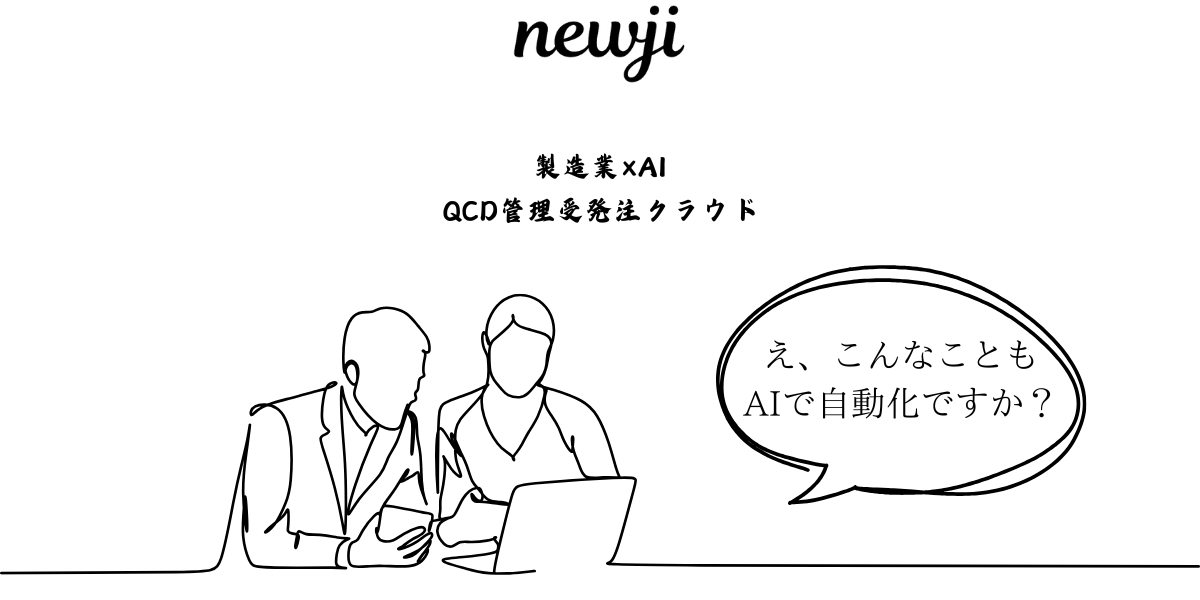
Differences Between Forecasted Production and Planned Production
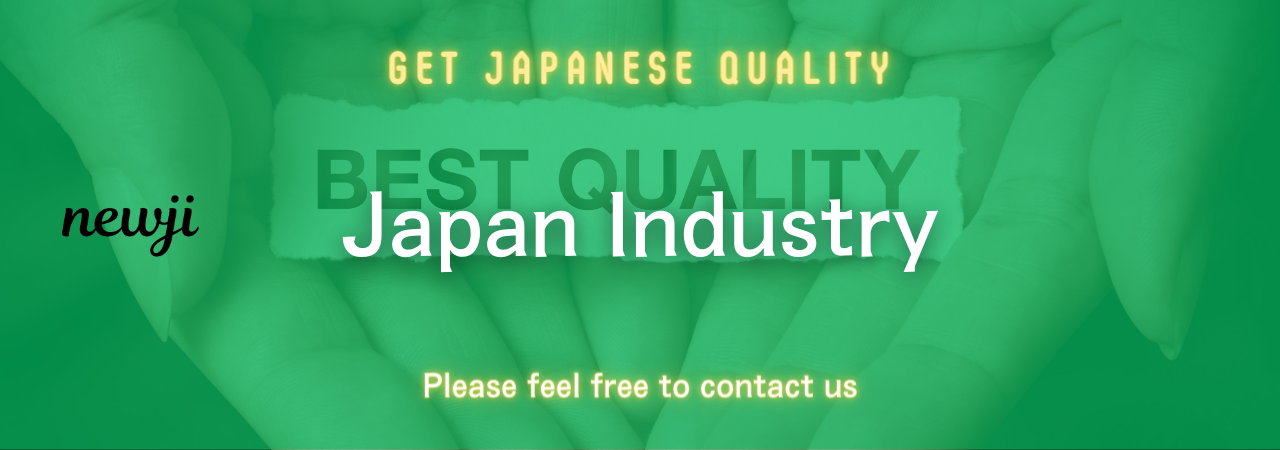
目次
Understanding Production Plans
Production is a crucial component in any manufacturing process.
To effectively manage production, businesses rely on two key concepts: forecasted production and planned production.
While these terms are often used interchangeably, they have distinct meanings and purposes.
Forecasted production refers to the estimation of the amount of product a company expects to manufacture over a specific period.
This estimate is based on historical data, current market trends, and anticipated demand.
Forecasters analyze these factors to predict the quantity of goods that should meet customer demand without overproducing.
On the other hand, planned production involves the detailed scheduling and allocation of resources to achieve the forecasted output.
This plan takes into account the company’s capacity, available materials, and workforce to ensure production goals are met efficiently.
Key Differences Between Forecasted and Planned Production
The primary difference between forecasted and planned production revolves around the purpose and execution of each process.
Forecasted production focuses on predicting market needs, while planned production centers on meeting those needs through resource management.
Nature of Forecasting and Planning
Forecasting is a demand-driven process.
It serves as a guide for what the production team needs to prepare for, but it is an estimate rather than a precise figure.
Forecasting considers external factors such as market demand, seasonality, and emerging trends.
It is inherently uncertain and subject to change as new information becomes available.
Planned production, in contrast, is based on internal capabilities.
It is a more concrete process that involves creating an actionable strategy to meet forecasted demand.
Planned production accounts for tangible elements like machinery availability, workforce hours, and inventory levels.
This plan is typically more rigid, structured to optimize the use of resources and minimize inefficiencies.
Flexibility and Adaptability
Forecasted production is inherently flexible.
As it is an estimate, companies can adjust their forecasts in response to new data or changes in market conditions.
For example, if a sudden increase in demand is observed, a company might revise its forecast upward to avoid stockouts.
Planned production, however, is less adaptable.
Once resources are allocated and schedules are set, changes can be costly and disruptive.
Modifications to the production plan might require adjusting employees’ working hours, reordering materials, or rescheduling machine use.
Therefore, changes to planned production are often made with caution and significant consideration.
Impact on Business Operations
Accurate forecasted production is crucial for maintaining balance in supply chains.
Underestimating demand can lead to missed sales opportunities, while overestimation may result in excess inventory and increased storage costs.
Thus, precise forecasting helps businesses optimize their operations and maintain customer satisfaction.
Planned production impacts internal operations.
An efficient production plan ensures that resources are utilized effectively, reducing downtime and waste.
This efficiency can lead to lower production costs and increased profitability.
The Importance of Collaboration
To successfully manage both forecasted and planned production, collaboration among various departments within a company is essential.
Sales and marketing teams provide valuable insights into demand trends that are crucial for accurate forecasting.
Meanwhile, production managers and operations staff need to communicate effectively to create viable production plans.
Technology can facilitate this collaboration by providing platforms for data sharing and real-time communication.
Advanced analytics and forecasting tools can enhance the accuracy of demand predictions.
Scheduling software can assist in creating realistic production plans that account for potential constraints.
Challenges in Bridging the Gap
Bridging the gap between forecasted and planned production can be challenging.
Forecasts are not always perfect, and unexpected changes in demand can lead to misalignment.
External factors like economic shifts, political events, or natural disasters can impact both forecasted and planned production.
One common challenge is dealing with variability in supply chains.
Supplier delays or shortages can disrupt planned production, requiring adjustments to maintain output levels.
Companies need contingency plans to address these potential disruptions.
Strategies for Improvement
To improve alignment between forecasted and planned production, companies can employ several strategies:
Enhance Data Accuracy
Invest in advanced analytics and forecasting tools to improve the accuracy of demand predictions.
Utilize historical data and market analysis to refine forecast models.
Foster Interdepartmental Communication
Promote regular communication between sales, marketing, and production teams.
Shared insights and feedback can lead to better-informed forecasts and more feasible production plans.
Implement Flexible Solutions
Incorporate flexibility into your production plans.
Consider adopting just-in-time inventory systems and cross-training employees to adapt more easily to changes in demand.
Monitor External Factors
Stay informed about external factors that could affect demand and production capabilities.
This awareness will help in making timely adjustments to forecasts and production plans.
Conclusion
In summary, understanding the differences between forecasted production and planned production is vital for effective manufacturing management.
While forecasted production guides companies towards anticipated market needs, planned production ensures that internal resources are well-organized to meet those demands.
By fostering collaboration, employing data-driven strategies, and maintaining flexibility, businesses can bridge the gap between these two crucial components of production.
資料ダウンロード
QCD調達購買管理クラウド「newji」は、調達購買部門で必要なQCD管理全てを備えた、現場特化型兼クラウド型の今世紀最高の購買管理システムとなります。
ユーザー登録
調達購買業務の効率化だけでなく、システムを導入することで、コスト削減や製品・資材のステータス可視化のほか、属人化していた購買情報の共有化による内部不正防止や統制にも役立ちます。
NEWJI DX
製造業に特化したデジタルトランスフォーメーション(DX)の実現を目指す請負開発型のコンサルティングサービスです。AI、iPaaS、および先端の技術を駆使して、製造プロセスの効率化、業務効率化、チームワーク強化、コスト削減、品質向上を実現します。このサービスは、製造業の課題を深く理解し、それに対する最適なデジタルソリューションを提供することで、企業が持続的な成長とイノベーションを達成できるようサポートします。
オンライン講座
製造業、主に購買・調達部門にお勤めの方々に向けた情報を配信しております。
新任の方やベテランの方、管理職を対象とした幅広いコンテンツをご用意しております。
お問い合わせ
コストダウンが利益に直結する術だと理解していても、なかなか前に進めることができない状況。そんな時は、newjiのコストダウン自動化機能で大きく利益貢献しよう!
(Β版非公開)