- お役立ち記事
- Differences Between Gas Welding and Arc Welding
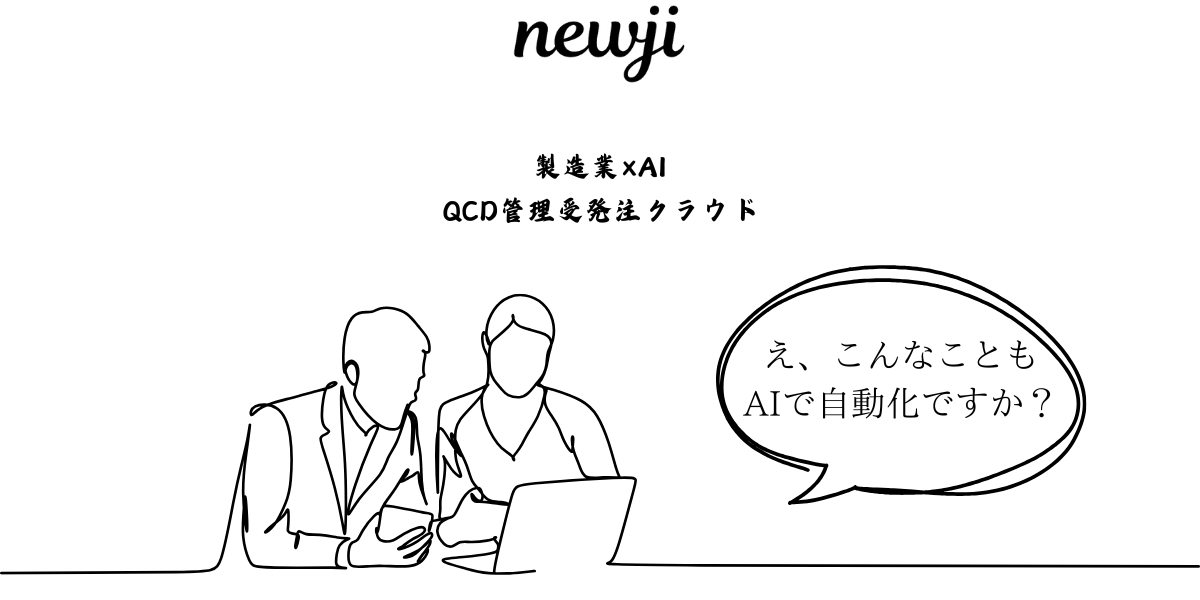
Differences Between Gas Welding and Arc Welding
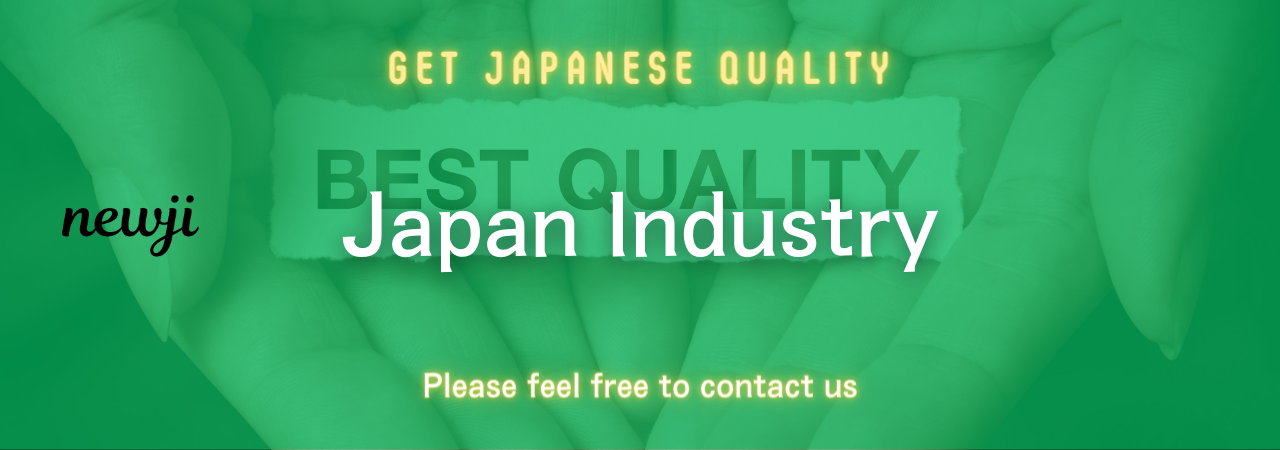
目次
Introduction to Welding
Welding is a crucial process in many industries, from automotive to construction, playing a vital role in joining metal parts together.
Two of the most common welding techniques are gas welding and arc welding.
Understanding the differences between these methods can help you choose the best one for your project needs.
In this article, we will explore the characteristics, applications, advantages, and disadvantages of both gas welding and arc welding.
What is Gas Welding?
Gas welding, also known as oxy-fuel welding, is a process that uses a flame produced by burning a mixture of oxygen and a fuel gas, typically acetylene.
The flame melts the metal workpieces and allows them to fuse together upon cooling.
How Gas Welding Works
The procedure involves using a welding torch connected to oxygen and fuel gas cylinders.
By adjusting the flame, welders can achieve precise control over heating and cooling processes, making it suitable for delicate and thin materials.
Gas welding requires a filler rod, which is manually added to the weld pool to strengthen the joint.
Applications of Gas Welding
Gas welding is versatile and often used in automotive repair, artwork, and plumbing.
It works well for welding thin metal sheets, non-ferrous metals like copper and aluminum, and for repairs in hard-to-reach areas due to its portability.
Advantages of Gas Welding
– **Cost-Effective**: Equipment is generally less expensive and easier to maintain.
– **Portability**: It’s easier to transport and set up because it doesn’t require an external power source.
– **Flexibility**: Effective for cutting, brazing, and soldering, besides welding.
– **Temperature Control**: Welders have excellent control over the heat applied, reducing the risk of warping or damaging sensitive parts.
Disadvantages of Gas Welding
– **Slower Process**: Compared to arc welding, gas welding can be slower, which may not be ideal for large-scale projects.
– **Limited Material Usage**: It is not suitable for thicker metals.
– **Skill Requirement**: It requires a high level of skill and experience to achieve quality welds.
What is Arc Welding?
Arc welding is a technique that uses an electric arc to melt and fuse metals.
The electric arc is created between an electrode and the base material.
The intense heat from the arc melts the metals, and when cooled, they solidify to form a strong joint.
How Arc Welding Works
Arc welding involves using an electrode that carries electrical current to create an arc between the electrode and the base material.
The arc’s heat melts the base metal and the electrode’s filler material to form a weld pool.
Various arc welding methods include Shielded Metal Arc Welding (SMAW), Gas Metal Arc Welding (GMAW), and Tungsten Inert Gas (TIG) welding, each with different applications and material compatibilities.
Applications of Arc Welding
Arc welding is widely used in construction, shipbuilding, and heavy machinery manufacturing due to its ability to handle thicker metals and produce strong welds.
It is ideal for projects that require fast production speeds and robust connections.
Advantages of Arc Welding
– **High Strength Joints**: Produces welds with high tensile strength, suitable for structural applications.
– **Speed**: Faster than gas welding, suitable for high-production environments.
– **Versatility**: Works with a wide range of materials and thicknesses.
– **Automation Possibilities**: Arc welding can be automated to increase efficiency and precision.
Disadvantages of Arc Welding
– **Equipment Cost**: Requires more expensive equipment and a reliable power source.
– **Complexity**: The technology can be complex, requiring training and skill to operate effectively.
– **Health and Safety Risks**: Produces intense UV radiation and harmful fumes, necessitating protective gear and proper ventilation.
Comparing Gas Welding and Arc Welding
Speed and Efficiency
Arc welding tends to be faster and more efficient, making it better suited for large-scale industrial projects.
Gas welding is slower and more labor-intensive but offers precision and control in more delicate applications.
Material Compatibility
Arc welding can handle thicker materials and offers versatility with a variety of metals.
Gas welding excels with thinner materials and is often chosen for non-ferrous metals.
Portability and Equipment
Gas welding equipment is more portable and doesn’t require a power supply, making it convenient for fieldwork.
Arc welding requires electricity, which can limit its portability, but it supports automation for mass production.
Safety Considerations
Both techniques involve risks, including exposure to high heat, harmful fumes, and bright light.
Proper protective gear and safety measures are crucial for both methods.
However, arc welding generally poses more severe risks due to electric currents and UV radiation.
Conclusion
Understanding the differences between gas welding and arc welding is vital for selecting the appropriate technique for your project.
Both methods have unique advantages and drawbacks, catering to different requirements and materials.
Gas welding offers precision and control for smaller, more detailed tasks, while arc welding provides faster speeds and strong welds for industrial applications.
Whether you choose gas or arc welding, always prioritize safety and ensure that operators are well-trained and equipped to handle the demands of the task.
資料ダウンロード
QCD調達購買管理クラウド「newji」は、調達購買部門で必要なQCD管理全てを備えた、現場特化型兼クラウド型の今世紀最高の購買管理システムとなります。
ユーザー登録
調達購買業務の効率化だけでなく、システムを導入することで、コスト削減や製品・資材のステータス可視化のほか、属人化していた購買情報の共有化による内部不正防止や統制にも役立ちます。
NEWJI DX
製造業に特化したデジタルトランスフォーメーション(DX)の実現を目指す請負開発型のコンサルティングサービスです。AI、iPaaS、および先端の技術を駆使して、製造プロセスの効率化、業務効率化、チームワーク強化、コスト削減、品質向上を実現します。このサービスは、製造業の課題を深く理解し、それに対する最適なデジタルソリューションを提供することで、企業が持続的な成長とイノベーションを達成できるようサポートします。
オンライン講座
製造業、主に購買・調達部門にお勤めの方々に向けた情報を配信しております。
新任の方やベテランの方、管理職を対象とした幅広いコンテンツをご用意しております。
お問い合わせ
コストダウンが利益に直結する術だと理解していても、なかなか前に進めることができない状況。そんな時は、newjiのコストダウン自動化機能で大きく利益貢献しよう!
(Β版非公開)