- お役立ち記事
- Differences between heat-resistant rubber and cold-resistant rubber and their market applications [automobile industry]
月間77,185名の
製造業ご担当者様が閲覧しています*
*2025年2月28日現在のGoogle Analyticsのデータより
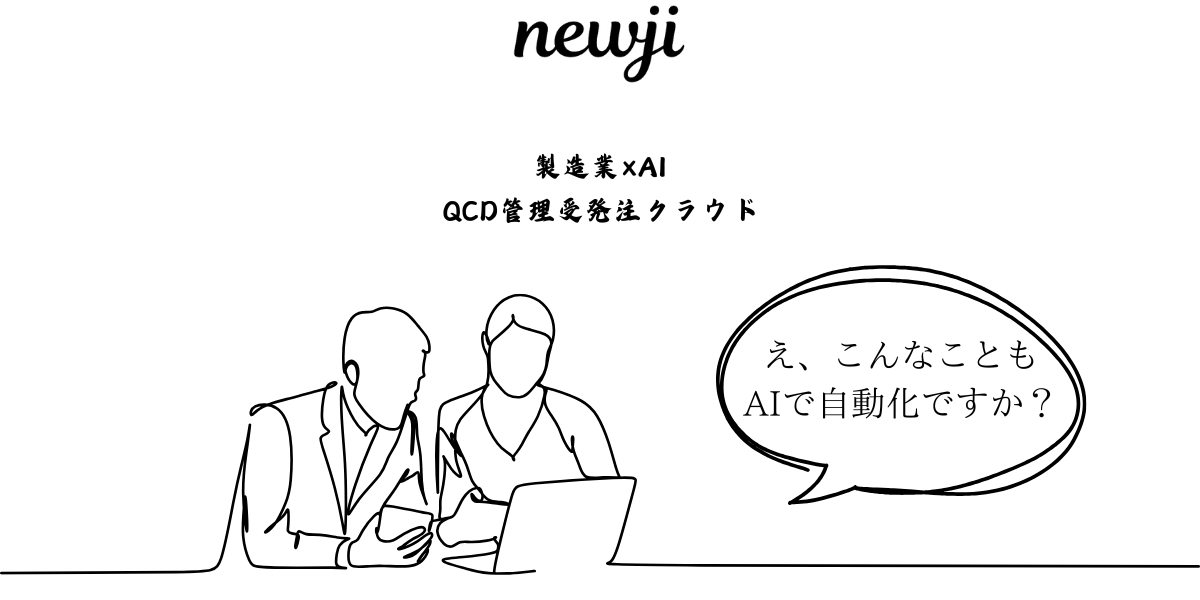
Differences between heat-resistant rubber and cold-resistant rubber and their market applications [automobile industry]
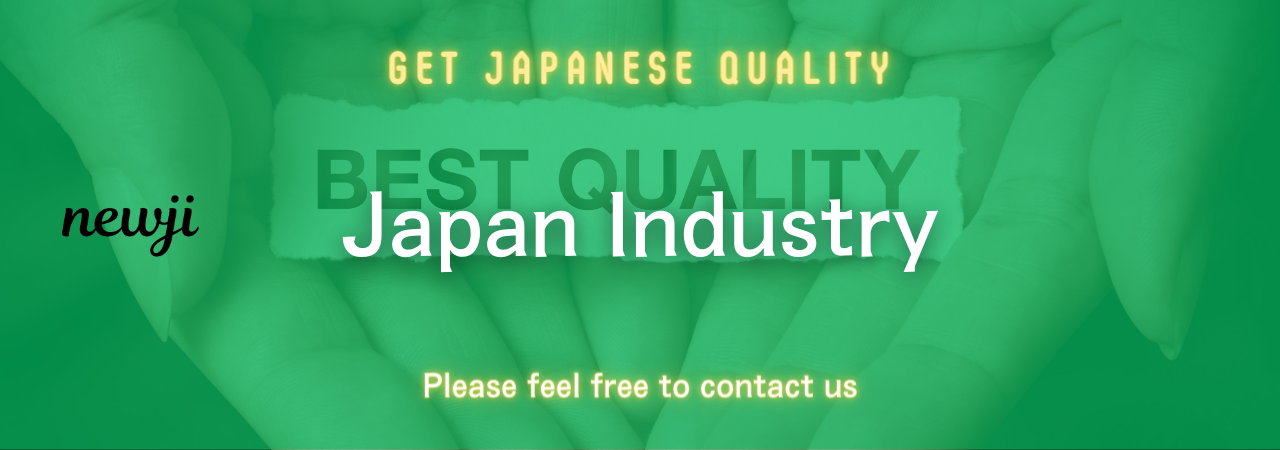
目次
Understanding Heat-Resistant Rubber
Heat-resistant rubber is designed to maintain its structural integrity and performance even under high temperatures.
This type of rubber is crucial in environments where heat exposure is a consistent threat.
One of the most common types of heat-resistant rubber in the automotive industry is silicone rubber.
Silicone rubber can withstand temperatures ranging from -60°C to 230°C.
This makes it ideal for under-the-hood applications, such as seals, gaskets, and hoses.
It remains flexible and stable even when exposed to high engine heat, ensuring that the parts it protects remain intact and operational.
In addition to silicone rubber, fluoroelastomer is another type of heat-resistant rubber that is often employed in the automotive sector.
Fluoroelastomer is preferred for its excellent resistance to a wide range of chemicals and high temperatures.
It is typically used in fuel system components and under-bonnet applications due to its ability to handle temperatures up to 250°C.
The Importance of Cold-Resistant Rubber
Just as vehicles need parts that withstand heat, they also require materials that remain flexible in frigid conditions.
Cold-resistant rubber is formulated to maintain elasticity and prevent brittleness when temperatures drop.
Neoprene rubber is a popular choice for cold climates because it retains flexibility down to -40°C.
This makes it suitable for use in car doors, windows, and weatherstripping, where it consistently faces exposure to the elements.
Nitrile rubber, while primarily known for its oil-resistance, also offers decent cold-resistant properties.
Although not as robust at extreme lows as neoprene, nitrile rubber remains pliable and effective for many automotive applications that require moderate cold resistance.
EPDM rubber is another valuable option, especially in automotive weather-sealing applications.
It has a wide temperature range, maintaining resilience from -50°C up to 150°C.
This makes EPDM rubber highly versatile for designing components that need durability against both heat and cold.
Key Differences Between Heat-Resistant and Cold-Resistant Rubber
The main difference between heat-resistant and cold-resistant rubber lies in their ability to perform in specific temperature ranges.
Heat-resistant rubbers, like silicone and fluoroelastomer, are designed to handle high temperature environments, often prioritizing thermal stability over flexibility.
Conversely, cold-resistant rubbers, such as neoprene and EPDM, focus on maintaining their elasticity and structure even as temperatures plummet.
While each rubber type includes properties that allow them to perform in varied conditions, their formulations address opposite ends of the temperature spectrum.
The chemical composition of these rubbers allows for their specialized properties.
For example, the presence of silicone in heat-resistant rubber contributes to its stability at high temperatures, while the chemical structure of EPDM provides resilience to both heat and cold.
Market Applications in the Automotive Industry
In the automotive industry, the selection of rubber type is often dictated by the environment and functionality required by different parts and components.
Applications of Heat-Resistant Rubber
Heat-resistant rubber finds extensive use in many areas under the hood of vehicles.
From engine gaskets to turbocharger hoses, it is employed where there is a need for materials that do not degrade under intense heat.
Exhaust systems also benefit from the properties of heat-resistant rubbers since they remain intact despite consistent thermal cycling.
Furthermore, heat-resistant rubber is used in thermal insulation applications.
It ensures that the heat generated by cars does not affect other parts of the vehicle, maintaining safety and efficiency.
Applications of Cold-Resistant Rubber
Cold-resistant rubber is essential for automotive parts that need to maintain performance during extreme winter conditions.
It is commonly used in areas exposed to the outdoors, such as tires, seals, and boot linings.
Automotive manufacturers often use cold-resistant materials for door and window seals, as their ability to stay flexible at low temperatures helps prevent drafts and noise, improving overall vehicle comfort.
Cold-resistant rubber can also be used in suspension systems, where material flexibility is crucial for maintaining ride comfort and handling even in cold weather.
Balancing Requirements: Dual-Resistant Rubbers
Some applications necessitate materials that can withstand both ends of the temperature spectrum.
This has led to the development of dual-resistant rubbers, such as EPDM, which are crafted to work efficiently in both hot and cold conditions.
This kind of rubber offers automotive designers the flexibility to use one material for parts subject to varying climates, avoiding the need to switch materials between seasons.
Yet, compromises typically exist in their performance, and dual-resistant rubbers may not perform as exceptionally as specialized heat or cold-resistant types.
Conclusion
Understanding the differences and applications between heat-resistant and cold-resistant rubbers is crucial for automotive industry professionals.
Properly selecting these materials ensures longevity, safety, and performance of vehicle components in diverse environments.
The advancements in rubber technology continue to provide innovative solutions, making modern cars more reliable and adaptable to the demands of today’s varied climates and conditions.
As the automotive industry progresses, the role of these specialty rubbers becomes increasingly vital, driving forward developments in vehicle design and engineering.
資料ダウンロード
QCD管理受発注クラウド「newji」は、受発注部門で必要なQCD管理全てを備えた、現場特化型兼クラウド型の今世紀最高の受発注管理システムとなります。
ユーザー登録
受発注業務の効率化だけでなく、システムを導入することで、コスト削減や製品・資材のステータス可視化のほか、属人化していた受発注情報の共有化による内部不正防止や統制にも役立ちます。
NEWJI DX
製造業に特化したデジタルトランスフォーメーション(DX)の実現を目指す請負開発型のコンサルティングサービスです。AI、iPaaS、および先端の技術を駆使して、製造プロセスの効率化、業務効率化、チームワーク強化、コスト削減、品質向上を実現します。このサービスは、製造業の課題を深く理解し、それに対する最適なデジタルソリューションを提供することで、企業が持続的な成長とイノベーションを達成できるようサポートします。
製造業ニュース解説
製造業、主に購買・調達部門にお勤めの方々に向けた情報を配信しております。
新任の方やベテランの方、管理職を対象とした幅広いコンテンツをご用意しております。
お問い合わせ
コストダウンが利益に直結する術だと理解していても、なかなか前に進めることができない状況。そんな時は、newjiのコストダウン自動化機能で大きく利益貢献しよう!
(β版非公開)