- お役立ち記事
- Differences Between High-Frequency Hardening and Low-Frequency Hardening
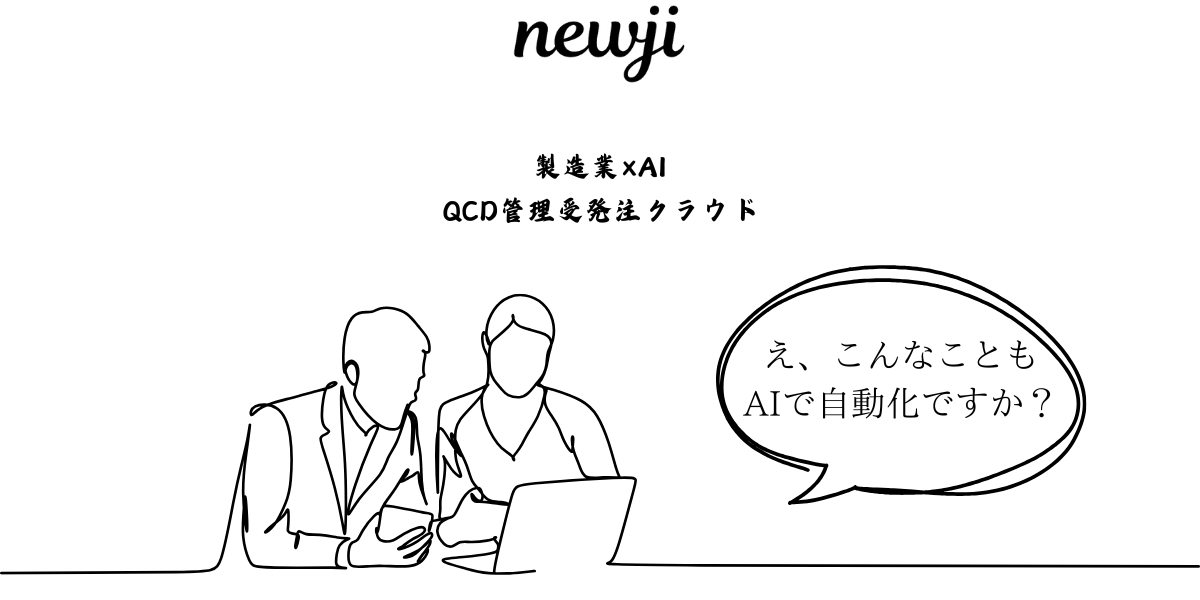
Differences Between High-Frequency Hardening and Low-Frequency Hardening
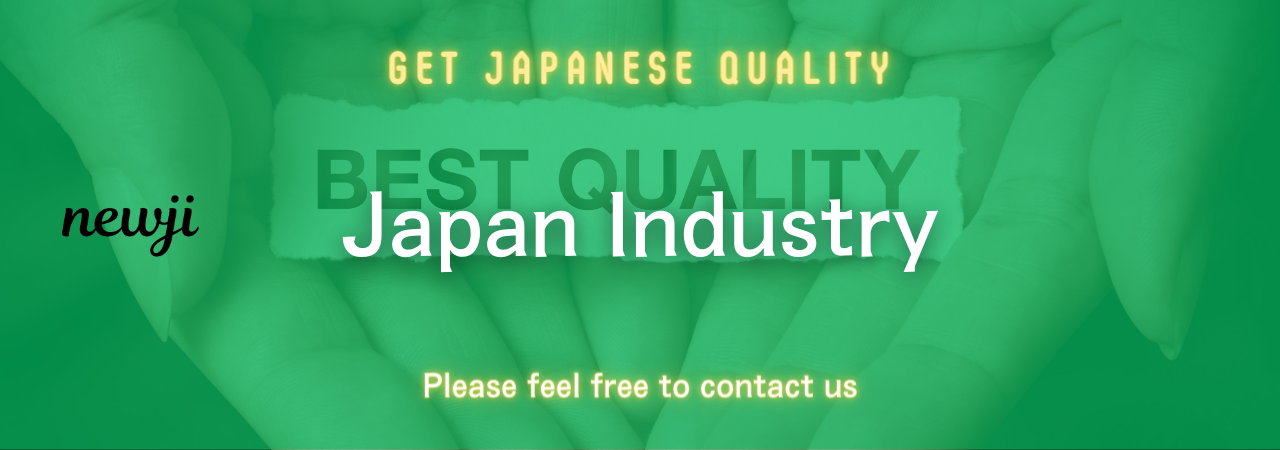
目次
Understanding High-Frequency and Low-Frequency Hardening
In the world of metalworking and engineering, hardening processes are vital to improve the durability and performance of metal components.
High-frequency and low-frequency hardening are two methods used to enhance the wear resistance and robustness of metals.
Despite having the same objective, these processes differ in their application, advantages, and ideal use cases.
What is High-Frequency Hardening?
High-frequency hardening is a process that uses electromagnetic induction to heat the surface of a metal component to a high temperature.
This method involves alternating currents with frequencies typically above 10 kHz.
The heat generated by the high-frequency currents rapidly brings the metal to its critical temperature.
Once the surface of the metal has been heated, it is quickly cooled or quenched, resulting in a hard, durable outer layer.
Advantages of High-Frequency Hardening
High-frequency hardening offers several benefits.
Firstly, it provides excellent control over the heating process, allowing for precise hardening of specific areas.
This results in components that are harder where it matters most, while maintaining the original properties in other areas.
Secondly, this method is efficient and fast, reducing production time significantly.
Lastly, the high level of automation associated with high-frequency hardening reduces human error and improves product consistency.
Applications of High-Frequency Hardening
Due to its precision and efficiency, high-frequency hardening is ideal for components that require specific hardness profiles.
This includes tools, gears, shafts, and spindles, especially those used in the automotive and tool-making industries, where surface durability is crucial.
What is Low-Frequency Hardening?
Low-frequency hardening also involves the use of heating by electromagnetic induction.
However, this method uses a lower frequency current, typically ranging from 1 to 10 kHz.
The energy generated by the low-frequency currents takes longer to heat the metal to the desired temperature.
After reaching the critical temperature, the metal is quenched, much like high-frequency hardening.
Advantages of Low-Frequency Hardening
Low-frequency hardening offers its own set of advantages.
Because the heating process is slower, it penetrates deeper into the material, resulting in a more uniform hardness throughout the component.
This makes it ideal for components that require a comprehensive hardening approach.
Moreover, it is often more energy-efficient than high-frequency hardening due to the lower frequency of the current used.
Applications of Low-Frequency Hardening
Low-frequency hardening is most suitable for larger components that require overall toughness.
Common applications include agricultural machinery parts, large gears, and heavy-duty machine components.
In industries where the fatigue resistance and toughness of large components are crucial, low-frequency hardening is preferred.
Key Differences Between the Two Processes
While both high and low-frequency hardening aim to increase the hardness and longevity of metal components, they do so in distinct ways.
The primary difference lies in the frequency of the currents used, which affects heating speed, penetration, and the areas hardened.
High-frequency hardening is best for targeted and surface-level applications, whereas low-frequency hardening is better for thorough, deeper-hardening needs.
Another difference is the surface finish.
Due to the rapid heating and cooling involved in high-frequency hardening, components often exhibit little to no distortion.
In contrast, low-frequency hardening might produce slight warping or require finishing processes due to more prolonged heat exposure.
Choosing the Right Hardening Process
Deciding between high-frequency and low-frequency hardening depends on several factors.
These include the size and type of the component, the specific application requirements, and the desired hardness profile.
For precise and surface-only applications, high-frequency hardening is preferred.
For larger components where thorough hardness is necessary, low-frequency hardening stands out.
Furthermore, the cost of equipment and the production timeline play a role in deciding on the process.
High-frequency hardening equipment is generally more expensive but offers faster processing times.
In contrast, low-frequency equipment may be less expensive, but the process itself can take longer.
Conclusion
In summary, both high-frequency and low-frequency hardening are valuable methods in the world of metal treatment, each serving unique purposes.
Understanding their differences and applications is crucial for selecting the right process for enhancing metal durability and performance.
By aligning the hardening method with specific industry and component needs, businesses can ensure optimal product quality and longevity, ultimately leading to better performance and reduced maintenance costs.
資料ダウンロード
QCD調達購買管理クラウド「newji」は、調達購買部門で必要なQCD管理全てを備えた、現場特化型兼クラウド型の今世紀最高の購買管理システムとなります。
ユーザー登録
調達購買業務の効率化だけでなく、システムを導入することで、コスト削減や製品・資材のステータス可視化のほか、属人化していた購買情報の共有化による内部不正防止や統制にも役立ちます。
NEWJI DX
製造業に特化したデジタルトランスフォーメーション(DX)の実現を目指す請負開発型のコンサルティングサービスです。AI、iPaaS、および先端の技術を駆使して、製造プロセスの効率化、業務効率化、チームワーク強化、コスト削減、品質向上を実現します。このサービスは、製造業の課題を深く理解し、それに対する最適なデジタルソリューションを提供することで、企業が持続的な成長とイノベーションを達成できるようサポートします。
オンライン講座
製造業、主に購買・調達部門にお勤めの方々に向けた情報を配信しております。
新任の方やベテランの方、管理職を対象とした幅広いコンテンツをご用意しております。
お問い合わせ
コストダウンが利益に直結する術だと理解していても、なかなか前に進めることができない状況。そんな時は、newjiのコストダウン自動化機能で大きく利益貢献しよう!
(Β版非公開)