- お役立ち記事
- Differences Between Laser Welding and TIG Welding
月間77,185名の
製造業ご担当者様が閲覧しています*
*2025年2月28日現在のGoogle Analyticsのデータより
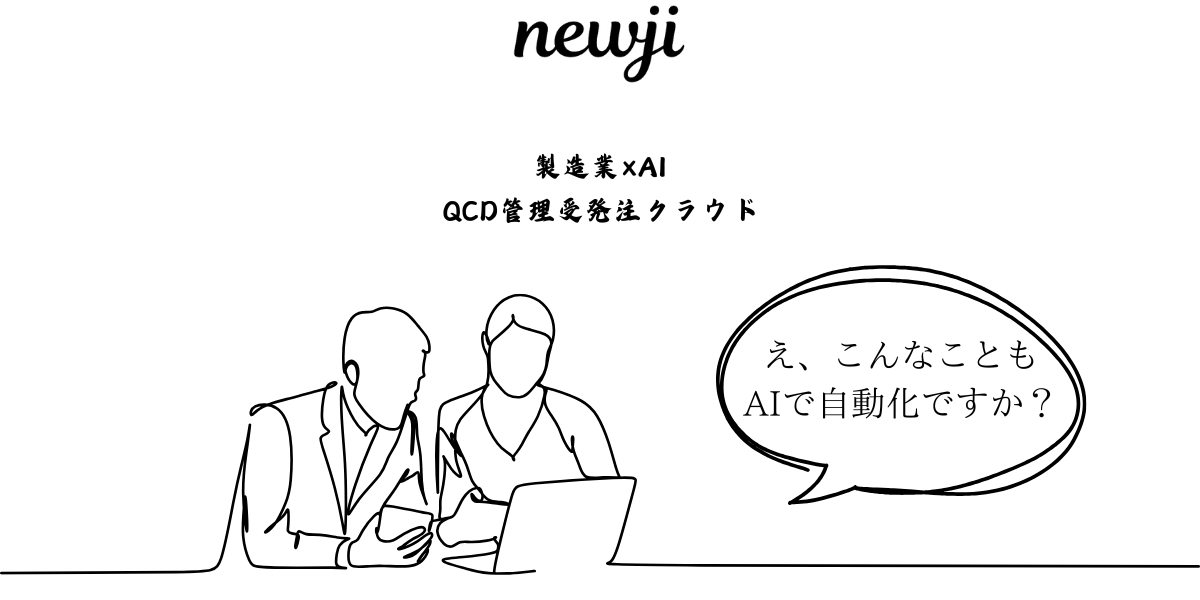
Differences Between Laser Welding and TIG Welding
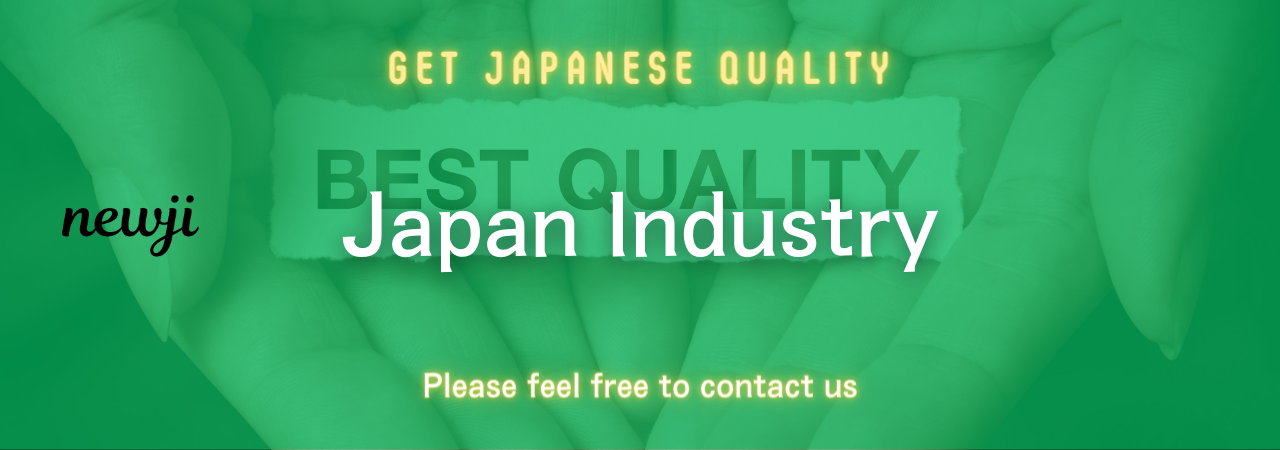
目次
Understanding Welding Processes
Welding is a crucial process used across various industries to join materials, typically metals or thermoplastics, by causing coalescence.
There are multiple welding techniques, each with its unique characteristics, advantages, and applications.
Two widely-used methods are Laser Welding and Tungsten Inert Gas (TIG) Welding.
Before delving into their differences, it’s important to understand what each type of welding involves.
This will lay the groundwork for comparing them based on key factors.
What is Laser Welding?
Laser welding is a process that uses a laser beam to join pieces of metal or thermoplastics.
This technique is known for its ability to produce high-precision welds.
The laser provides a concentrated heat source, allowing for narrow, deep welds and high welding rates.
Laser welding can be performed in different modes, such as continuous or pulsed.
Continuous mode is typically used for deep welds, while pulsed mode is suitable for applications requiring low heat input.
Advantages of Laser Welding
One of the main advantages of laser welding is its precision.
The laser beam is easily controlled, leading to precise and accurate welds with minimal distortion.
This precision is crucial in industries like aerospace and electronics, where weld quality and accuracy are paramount.
Laser welding also allows for greater welding speeds compared to traditional methods.
This increase in speed leads to higher productivity and reduced costs over time.
Applications of Laser Welding
Laser welding is widely used in automotive, medical device manufacture, electronics, and aerospace applications.
Its ability to precisely join small parts without causing heat damage to surrounding materials makes it indispensable in manufacturing delicate components.
What is TIG Welding?
Tungsten Inert Gas (TIG) welding, also known as Gas Tungsten Arc Welding (GTAW), uses a tungsten electrode to produce the weld.
The tungsten electrode is non-consumable, meaning it does not melt during the welding process.
In TIG welding, an inert gas, typically argon or helium, is used to protect the weld area from contamination.
This process is manual and requires a skilled welder to produce high-quality joints.
Advantages of TIG Welding
TIG welding is renowned for producing high-quality and clean welds with a superior finish.
It offers control over the heat input and allows for precision when joining components, which is crucial in situations where quality and aesthetics are important.
Moreover, TIG welding is highly versatile.
It can be used on thin materials as well as thick sections and is compatible with a wide range of metals, including steel, aluminum, and copper alloys.
Applications of TIG Welding
Due to its precision and the quality of the weld produced, TIG welding is often used in industries where highly durable and visually appealing welds are necessary.
It is common in the fabrication and repair of motorcycles, bicycles, and aircraft, as well as in art and sculpture.
Comparing Laser Welding and TIG Welding
Understanding the differences between laser welding and TIG welding can help you choose the right method for your project.
Here are the key aspects where they differ:
Heat Input and Precision
Laser welding offers lower heat input compared to TIG welding, which is beneficial for maintaining the integrity of the materials being joined.
This lower heat input results in less thermal distortion, making laser welding the preferred choice for thin and delicate materials.
In contrast, TIG welding involves higher heat input.
While this can lead to more thermal distortion, it also means that TIG welding is more suitable for thicker materials where deep penetration is necessary.
Speed and Efficiency
In terms of speed, laser welding has a significant advantage.
The high energy density of the laser allows for faster welding speeds than TIG welding, enhancing production efficiency and reducing project completion times.
However, the TIG welding process, being manual and slow, allows for meticulous control, which makes it ideal for projects where precision and craftsmanship are more important than speed.
Cost Considerations
When it comes to cost, laser welding equipment is typically more expensive than TIG welding setups.
Laser systems are technologically advanced and include safety features that add to the initial investment.
However, the increased efficiency and reduced labor costs can make laser welding more cost-effective in the long run for large-scale production.
TIG welding, on the other hand, has a lower initial equipment cost, making it accessible for small-scale businesses and individual craftsmen.
The cost-effectiveness of TIG welding is often realized in one-off or small batch projects where precision is prioritized over speed.
Skill Level and Operation
Laser welding requires operators who are trained to handle advanced machinery and understand the parameters that need to be altered for different materials and thicknesses.
This necessitates a level of expertise in handling laser welding equipment.
TIG welding, while manual, requires significant skill and experience as well.
The welder’s proficiency directly influences the quality and appearance of the weld.
Therefore, both processes demand skilled operators, albeit in different capacities.
Making a Choice Between Laser and TIG Welding
Choosing between laser and TIG welding depends on the specific requirements of your project.
Consider the type of materials you are working with, the thickness of these materials, and the desired quality and appearance of the weld.
If speed, precision, and minimal thermal distortion are critical, laser welding may be the better choice.
For projects that require flexibility with different materials and where manual craftsmanship is key, TIG welding is typically more suitable.
Ultimately, both methods have their strengths and ideal use cases.
Understanding these differences will allow you to leverage the right welding process to meet your specific needs and achieve the best possible results.
資料ダウンロード
QCD管理受発注クラウド「newji」は、受発注部門で必要なQCD管理全てを備えた、現場特化型兼クラウド型の今世紀最高の受発注管理システムとなります。
ユーザー登録
受発注業務の効率化だけでなく、システムを導入することで、コスト削減や製品・資材のステータス可視化のほか、属人化していた受発注情報の共有化による内部不正防止や統制にも役立ちます。
NEWJI DX
製造業に特化したデジタルトランスフォーメーション(DX)の実現を目指す請負開発型のコンサルティングサービスです。AI、iPaaS、および先端の技術を駆使して、製造プロセスの効率化、業務効率化、チームワーク強化、コスト削減、品質向上を実現します。このサービスは、製造業の課題を深く理解し、それに対する最適なデジタルソリューションを提供することで、企業が持続的な成長とイノベーションを達成できるようサポートします。
製造業ニュース解説
製造業、主に購買・調達部門にお勤めの方々に向けた情報を配信しております。
新任の方やベテランの方、管理職を対象とした幅広いコンテンツをご用意しております。
お問い合わせ
コストダウンが利益に直結する術だと理解していても、なかなか前に進めることができない状況。そんな時は、newjiのコストダウン自動化機能で大きく利益貢献しよう!
(β版非公開)