- お役立ち記事
- Differences Between Maintenance Planning and Preventive Maintenance Planning
月間76,176名の
製造業ご担当者様が閲覧しています*
*2025年3月31日現在のGoogle Analyticsのデータより
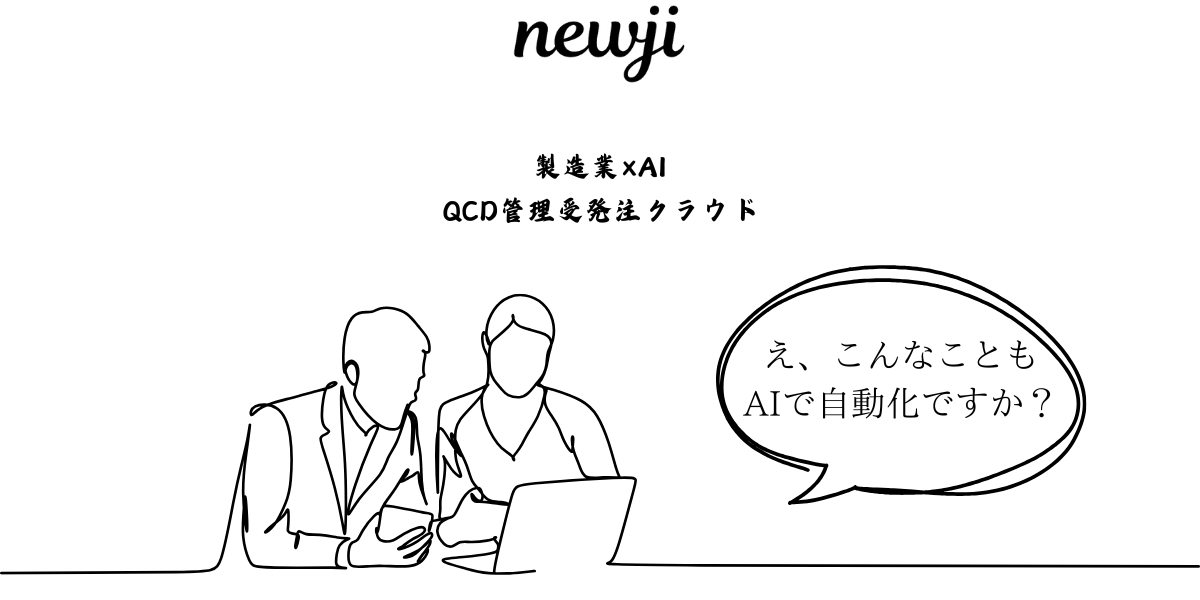
Differences Between Maintenance Planning and Preventive Maintenance Planning
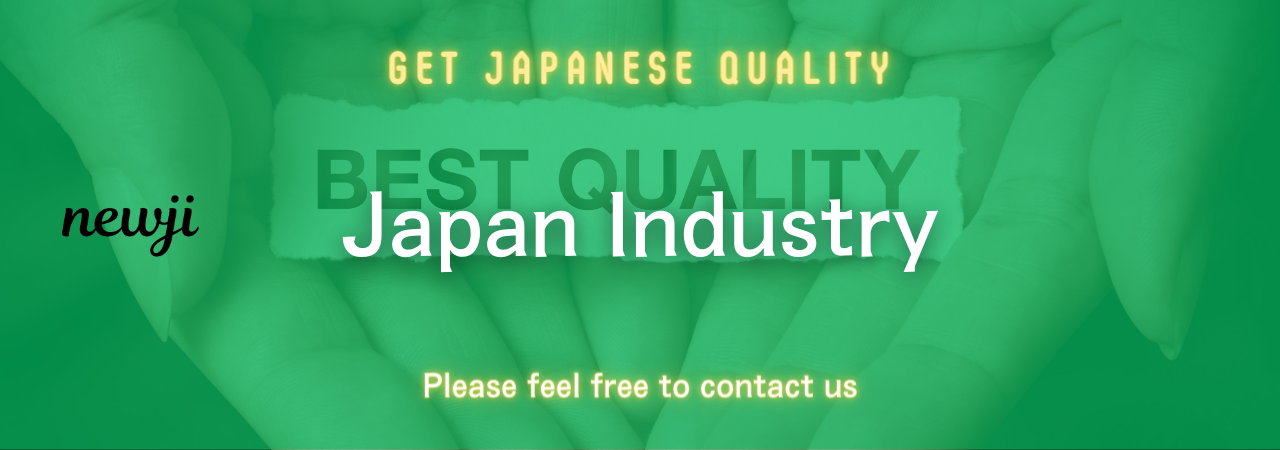
目次
Understanding Maintenance Planning
Maintenance planning is an essential aspect of managing machinery and equipment within any industry.
It involves organizing, scheduling, and executing maintenance tasks to ensure that machines and systems operate efficiently and reliably.
The primary goal of maintenance planning is to minimize downtime, reduce repair costs, and extend the lifespan of machinery.
This process requires a well-structured approach that includes identifying maintenance needs, assigning resources, and scheduling the work to be carried out.
By having a clear maintenance plan, companies can avoid unexpected breakdowns and ensure that their equipment remains in good working condition.
To achieve this, it is crucial to have a proactive mindset, anticipating potential issues before they become major problems.
In essence, maintenance planning is about being prepared and making smart decisions about when and how maintenance tasks should be undertaken.
The Role of a Maintenance Planner
A maintenance planner plays a critical role in the maintenance planning process.
This person is responsible for developing maintenance strategies and tactics to address specific needs.
They must analyze equipment usage, performance data, and manufacturer recommendations to create an effective maintenance schedule.
The maintenance planner also coordinates with other departments to ensure that necessary resources, such as parts and labor, are available when needed.
In addition to scheduling routine tasks, the maintenance planner must also be prepared for unforeseen issues that may require immediate attention.
This involves creating contingency plans and being flexible enough to adjust schedules when necessary.
By working closely with technicians and engineers, the planner ensures that maintenance activities are completed efficiently and to the highest standards.
Understanding Preventive Maintenance Planning
Preventive maintenance planning is a subset of maintenance planning, but with a distinct focus on preventing equipment failures before they occur.
This proactive approach involves regularly scheduled inspections, servicing, and adjustments to keep machinery running smoothly.
The philosophy behind preventive maintenance is that regular attention to equipment will lead to fewer unexpected breakdowns, improved safety, and more reliable operation.
Preventive maintenance is typically scheduled based on time, usage, or condition, depending on the specific needs of the equipment.
For example, a vehicle might require an oil change every 5,000 miles, while a piece of manufacturing equipment could need a thorough inspection every six months.
The key is to establish a routine that ensures all equipment receives the attention it needs at the right intervals.
The Role of Preventive Maintenance Technicians
Preventive maintenance technicians are specialized professionals who carry out the tasks outlined in preventive maintenance plans.
Their role is to conduct regular checks and maintenance activities, following specific procedures to ensure equipment remains in top condition.
Technicians must have a keen eye for detail and the ability to recognize potential issues before they escalate.
In addition to routine checks, preventive maintenance technicians are also responsible for documenting their work.
Accurate records are vital for tracking the condition of equipment over time and for making informed decisions about future maintenance needs.
Key Differences Between Maintenance Planning and Preventive Maintenance Planning
While maintenance planning and preventive maintenance planning share some similarities, they differ in their overall goals and approaches.
Maintenance planning is a broad strategy that encompasses all types of maintenance activities, including corrective, preventive, and predictive maintenance.
Its objective is to ensure that all aspects of maintenance are well-organized and executed effectively.
On the other hand, preventive maintenance planning focuses specifically on preventing equipment failures through routine maintenance activities.
It is a more narrowly defined approach that aims to preemptively address potential issues to reduce the likelihood of unexpected downtime.
Another key difference is the nature of the tasks involved.
Maintenance planning is more strategic, incorporating long-term considerations and coordination across departments.
Preventive maintenance planning, meanwhile, is more tactical, dealing with the practical execution of regular maintenance tasks.
Benefits of Maintenance and Preventive Maintenance Planning
Both maintenance planning and preventive maintenance planning offer significant benefits to organizations.
Effective maintenance planning ensures that equipment operates at peak efficiency, leading to cost savings and reduced downtime.
It also extends the lifespan of machinery, providing a better return on investment.
Preventive maintenance planning, in particular, helps enhance safety by eliminating potential hazards before they result in accidents or injuries.
By identifying and addressing issues early, preventive maintenance reduces the risk of catastrophic failures, ensuring a safer working environment.
Moreover, a well-implemented preventive maintenance plan can lead to more predictable maintenance costs, making budget management easier.
Overall, the combination of these planning processes results in improved reliability and efficiency of operations.
Implementing Successful Maintenance Strategies
To implement successful maintenance strategies, organizations need to invest in both planning and execution.
This includes training staff, utilizing technology for tracking and record-keeping, and fostering a culture of proactive maintenance.
It is also vital to regularly review and update maintenance plans to ensure they remain relevant and effective.
Leveraging modern technologies, such as maintenance management software, can significantly enhance planning capabilities.
Such tools provide powerful analytics, real-time tracking, and automated scheduling, all of which contribute to more effective maintenance management.
In conclusion, while maintenance and preventive maintenance planning have distinct roles, they are both crucial components of any successful maintenance strategy.
By understanding and implementing these approaches, organizations can ensure the longevity and reliability of their equipment, ultimately contributing to their overall success.
資料ダウンロード
QCD管理受発注クラウド「newji」は、受発注部門で必要なQCD管理全てを備えた、現場特化型兼クラウド型の今世紀最高の受発注管理システムとなります。
ユーザー登録
受発注業務の効率化だけでなく、システムを導入することで、コスト削減や製品・資材のステータス可視化のほか、属人化していた受発注情報の共有化による内部不正防止や統制にも役立ちます。
NEWJI DX
製造業に特化したデジタルトランスフォーメーション(DX)の実現を目指す請負開発型のコンサルティングサービスです。AI、iPaaS、および先端の技術を駆使して、製造プロセスの効率化、業務効率化、チームワーク強化、コスト削減、品質向上を実現します。このサービスは、製造業の課題を深く理解し、それに対する最適なデジタルソリューションを提供することで、企業が持続的な成長とイノベーションを達成できるようサポートします。
製造業ニュース解説
製造業、主に購買・調達部門にお勤めの方々に向けた情報を配信しております。
新任の方やベテランの方、管理職を対象とした幅広いコンテンツをご用意しております。
お問い合わせ
コストダウンが利益に直結する術だと理解していても、なかなか前に進めることができない状況。そんな時は、newjiのコストダウン自動化機能で大きく利益貢献しよう!
(β版非公開)