- お役立ち記事
- Differences Between Material Costs and Manufacturing Costs
Differences Between Material Costs and Manufacturing Costs
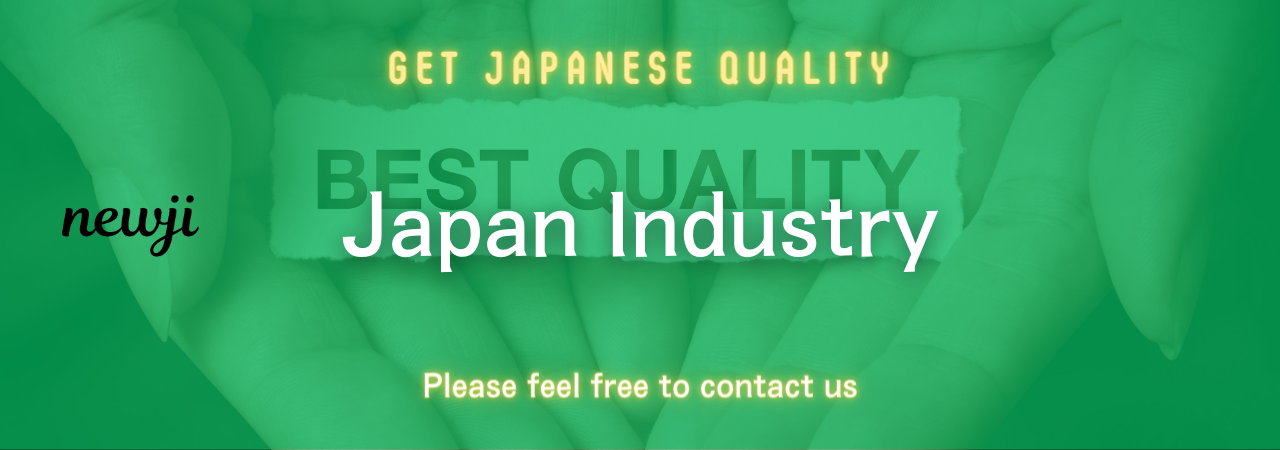
目次
Understanding Material Costs
Material costs are expenses incurred for the raw materials used directly to produce products.
These raw materials form the foundation of the product and are essential for its creation.
Typically, these costs fluctuate based on market demand, scarcity of resources, or economic conditions.
In manufacturing, businesses strive to manage and optimize material costs to maintain profitability.
Examples of material costs include metals, textiles, plastics, and natural resources like wood or rubber.
Each industry varies in terms of what materials are considered essential.
For example, in the automotive industry, steel and aluminum are critical materials, whereas in the fashion industry, fabrics and dyes are primary materials.
Material costs are typically categorized as direct costs because they can be directly traced to the production of specific goods.
Companies usually account for these costs in their financial statements by determining the amount of raw material needed for production and then multiplying it by the cost per unit of material.
Materials are also subject to wastage and defects, which companies need to monitor to ensure cost-effectiveness.
Factors Influencing Material Costs
Material costs are influenced by various market conditions.
Supply chain disruptions, geopolitical tensions, or changes in trade policies can greatly impact the cost of raw materials.
Additionally, inflation rates, environmental regulations, and evolving consumer preferences are also important factors that can affect the cost of materials.
For instance, an increase in oil prices can affect the cost of plastics, as they are petroleum-based products.
Similarly, stricter environmental laws might increase the demand and cost of recycled materials.
Being aware of these factors allows businesses to plan effectively and adopt strategies to minimize cost increases.
Managing Material Costs
Managing material costs is crucial for sustaining a business’s profitability.
One effective strategy is bulk purchasing, where companies buy large quantities of materials to receive volume discounts.
Alternatively, businesses may establish long-term contracts with suppliers to secure stable pricing.
Moreover, adopting waste reduction measures and improving production efficiency can significantly lower material costs.
By investing in quality control processes, businesses can minimize defects and wastage during manufacturing, thus reducing expenses associated with faulty materials.
Understanding Manufacturing Costs
Manufacturing costs, on the other hand, encompass more than just material costs.
These are the total expenses required to transform raw materials into finished products ready for sale.
Manufacturing costs include direct material costs, direct labor costs, and manufacturing overhead.
Direct labor costs involve the wages paid to workers directly engaged in the production process.
From assembly line workers to machine operators, their efforts are crucial to turning raw materials into completed goods.
Manufacturing overhead involves all other costs necessary for production that are not directly tied to materials or labor.
This includes costs such as factory utilities, maintenance of equipment, and salaries for personnel in managerial roles.
Overhead also covers expenses like depreciation of machinery, insurance, and quality assurance costs.
Factors Affecting Manufacturing Costs
Manufacturing costs can vary based on technology, labor rates, and production volume.
Technology improvements often lead to more efficient production processes, thereby reducing overall costs.
For example, automation may decrease direct labor costs but could increase overhead costs due to higher maintenance needs.
Wages and labor laws also influence manufacturing costs.
An increase in minimum wage, for instance, directly impacts labor costs.
Furthermore, as businesses scale up, the costs may decrease due to economies of scale, where larger production volumes lead to lower costs per unit.
Government regulations, tariffs, and economic policies are further factors that can influence these costs.
Companies must continuously adapt to these changes to keep their production cost-effective.
Breaking Down Manufacturing Costs
Understanding the composition of manufacturing costs is essential for businesses to optimize production.
By analyzing cost allocations, companies can identify areas for improvement or cost-cutting.
Implementing lean manufacturing techniques can help in minimizing waste and maximizing efficiency.
Additionally, regular audits of production processes ensure that all components of manufacturing costs are within the budgetary limits and align with business objectives.
Key Differences between Material Costs and Manufacturing Costs
While both material costs and manufacturing costs are crucial components in the production process, they differ significantly in scope and impact.
Material costs are a subset of manufacturing costs, focusing solely on the expenses for raw materials.
In contrast, manufacturing costs provide a broader view, encompassing labor, overhead, and materials involved in production.
Material costs are more variable and sensitive to market conditions.
In comparison, manufacturing costs involve fixed and variable elements, where some costs remain consistent regardless of production volume.
To effectively manage production expenses, companies must balance both material and manufacturing costs.
Identifying the key drivers of each and understanding their relationship enables businesses to minimize expenditures while optimizing product quality.
Conclusion
Navigating the complexities of material and manufacturing costs is critical for business success.
While material costs concern the acquisition of essential raw materials, manufacturing costs cover the entire spectrum of production expenses.
Both play integral roles in the manufacturing process, and managing them effectively requires strategic planning and a keen understanding of market dynamics.
By employing innovative solutions, companies can control material costs and streamline manufacturing processes, securing profitability and competitive advantage.
Ultimately, businesses that excel in managing these costs are better positioned to flourish in today’s dynamic market environment.
資料ダウンロード
QCD調達購買管理クラウド「newji」は、調達購買部門で必要なQCD管理全てを備えた、現場特化型兼クラウド型の今世紀最高の購買管理システムとなります。
ユーザー登録
調達購買業務の効率化だけでなく、システムを導入することで、コスト削減や製品・資材のステータス可視化のほか、属人化していた購買情報の共有化による内部不正防止や統制にも役立ちます。
NEWJI DX
製造業に特化したデジタルトランスフォーメーション(DX)の実現を目指す請負開発型のコンサルティングサービスです。AI、iPaaS、および先端の技術を駆使して、製造プロセスの効率化、業務効率化、チームワーク強化、コスト削減、品質向上を実現します。このサービスは、製造業の課題を深く理解し、それに対する最適なデジタルソリューションを提供することで、企業が持続的な成長とイノベーションを達成できるようサポートします。
オンライン講座
製造業、主に購買・調達部門にお勤めの方々に向けた情報を配信しております。
新任の方やベテランの方、管理職を対象とした幅広いコンテンツをご用意しております。
お問い合わせ
コストダウンが利益に直結する術だと理解していても、なかなか前に進めることができない状況。そんな時は、newjiのコストダウン自動化機能で大きく利益貢献しよう!
(Β版非公開)