- お役立ち記事
- Differences Between Metalworking and Plastic Processing
月間76,176名の
製造業ご担当者様が閲覧しています*
*2025年3月31日現在のGoogle Analyticsのデータより
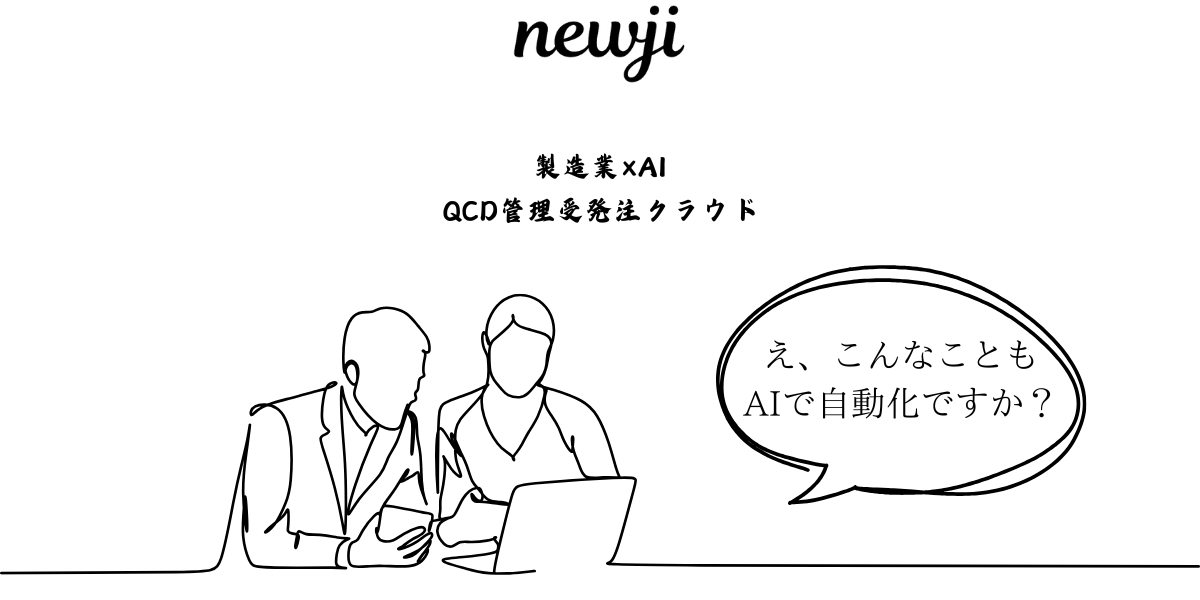
Differences Between Metalworking and Plastic Processing
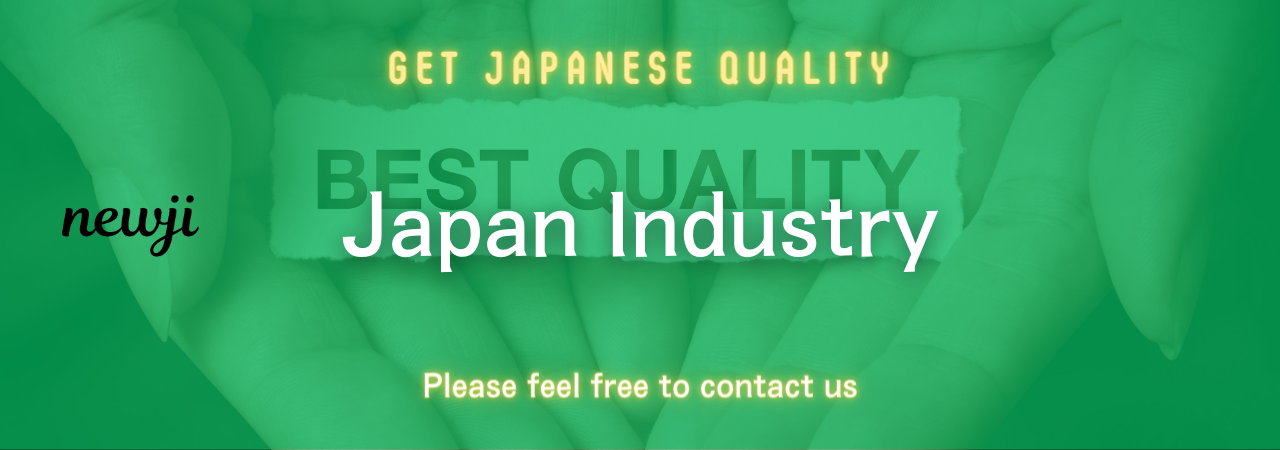
目次
Introduction to Metalworking and Plastic Processing
Metalworking and plastic processing are two fundamental techniques utilized in manufacturing and production industries worldwide.
Both processes involve shaping and transforming raw materials into final products, but they differ significantly in terms of materials, techniques, and applications.
Understanding these differences is crucial for making informed decisions in manufacturing and for choosing the right materials and processes for specific applications.
Materials Used in Metalworking and Plastic Processing
Metalworking Materials
Metalworking involves using metals such as steel, aluminum, copper, titanium, and iron.
These materials are prized for their strength, durability, and resistance to high temperatures.
Each metal has specific properties that make it suitable for different applications.
For instance, aluminum is lightweight and resistant to corrosion, making it ideal for aerospace applications, whereas steel is strong and durable, often used in construction and automotive industries.
Plastic Processing Materials
On the other hand, plastic processing involves the use of synthetic or semi-synthetic organic materials.
These materials include, but are not limited to, polyethylene, polypropylene, PVC, and acrylics.
Plastics are lightweight, versatile, and can be molded into various shapes, which makes them useful in diverse industries ranging from packaging to electronics.
Different types of plastics also offer unique properties, such as UV resistance or flexibility, depending on the additives and processing methods used.
Techniques in Metalworking and Plastic Processing
Metalworking Techniques
Metalworking encompasses various techniques that shape and form metal into desired shapes.
Some common metalworking techniques include forging, welding, casting, and machining.
– **Forging**: This involves shaping metal using compressive forces, often with a hammer or press.
Forged parts are strong and have few internal defects.
– **Welding**: This process joins two or more metal pieces by melting and fusing them together.
Welding is essential in fabrication and construction industries.
– **Casting**: In casting, molten metal is poured into molds to shape them.
This technique is efficient for complex shapes and mass production.
– **Machining**: Machining removes material from a workpiece to achieve the desired shape and size, often using cutters or drills.
Plastic Processing Techniques
Plastic processing also involves various techniques that modify and shape plastic materials.
– **Injection Molding**: This process involves injecting molten plastic into a mold.
It is efficient for creating consistent and complex parts in large quantities.
– **Blow Molding**: Blow molding forms hollow plastic parts, such as bottles, by expanding molten plastic inside a mold.
– **Extrusion**: This technique forces molten plastic through a die to create long continuous shapes, like pipes and sheets.
– **Thermoforming**: Thermoforming heats plastic sheets until pliable and then forms them over a mold.
This process is commonly used for packaging and containers.
Applications of Metalworking and Plastic Processing
Applications of Metalworking
Metalworking is crucial in industries that require strength and durability.
The automotive industry relies heavily on metalworking for chassis, engine components, and body panels.
Aerospace applications use metals for aircraft frames and parts due to their strength-to-weight ratio.
Construction uses metalworking for structural components like beams and columns.
Additionally, the electronics industry uses metalworking for reliable connections and heat dissipation in circuits.
Applications of Plastic Processing
Plastic processing finds applications in a multitude of industries due to its versatility and cost-effectiveness.
The packaging industry utilizes plastics for containers, wraps, and bottles, benefiting from their lightweight and durability.
Consumer products, like toys and household items, heavily rely on plastics for design flexibility and vibrant colors.
The healthcare industry uses plastics for single-use consumables, medical devices, and equipment due to hygiene and customization capabilities.
Automotive and aerospace industries incorporate plastics for interior components and lightweight parts that improve fuel efficiency.
Environmental Impact and Sustainability
Environmental Considerations in Metalworking
Metalworking processes can have significant environmental impacts due to energy consumption and waste generation.
Mining and refining metals are energy-intensive processes that contribute to carbon emissions.
Additionally, metalworking processes often require lubricants and coolants, which can pose environmental hazards if not managed properly.
Recycling metals is a key strategy to mitigate environmental impact, as it conserves resources and reduces emissions associated with raw material extraction.
Environmental Considerations in Plastic Processing
Plastic processing also poses environmental challenges, particularly regarding waste and pollution.
Plastics are derived from fossil fuels, and their production emits greenhouse gases.
Moreover, plastic waste contributes to pollution in oceans and landfills.
Efforts to improve sustainability in plastic processing include developing biodegradable plastics, promoting recycling programs, and reducing single-use plastics.
Innovations in bioplastics, made from renewable resources, offer promising alternatives to conventional plastics.
Conclusion
In conclusion, while metalworking and plastic processing share the overarching goal of transforming materials into functional products, they differ considerably in terms of materials, techniques, applications, and environmental impacts.
Understanding these differences is essential for selecting the appropriate methods for specific projects and industries.
As technology advances, both fields continue to evolve towards more efficient and sustainable practices, shaping the future of manufacturing.
資料ダウンロード
QCD管理受発注クラウド「newji」は、受発注部門で必要なQCD管理全てを備えた、現場特化型兼クラウド型の今世紀最高の受発注管理システムとなります。
ユーザー登録
受発注業務の効率化だけでなく、システムを導入することで、コスト削減や製品・資材のステータス可視化のほか、属人化していた受発注情報の共有化による内部不正防止や統制にも役立ちます。
NEWJI DX
製造業に特化したデジタルトランスフォーメーション(DX)の実現を目指す請負開発型のコンサルティングサービスです。AI、iPaaS、および先端の技術を駆使して、製造プロセスの効率化、業務効率化、チームワーク強化、コスト削減、品質向上を実現します。このサービスは、製造業の課題を深く理解し、それに対する最適なデジタルソリューションを提供することで、企業が持続的な成長とイノベーションを達成できるようサポートします。
製造業ニュース解説
製造業、主に購買・調達部門にお勤めの方々に向けた情報を配信しております。
新任の方やベテランの方、管理職を対象とした幅広いコンテンツをご用意しております。
お問い合わせ
コストダウンが利益に直結する術だと理解していても、なかなか前に進めることができない状況。そんな時は、newjiのコストダウン自動化機能で大きく利益貢献しよう!
(β版非公開)