- お役立ち記事
- Differences Between Multi-Axis Milling and Single Spindle Milling
月間77,185名の
製造業ご担当者様が閲覧しています*
*2025年2月28日現在のGoogle Analyticsのデータより
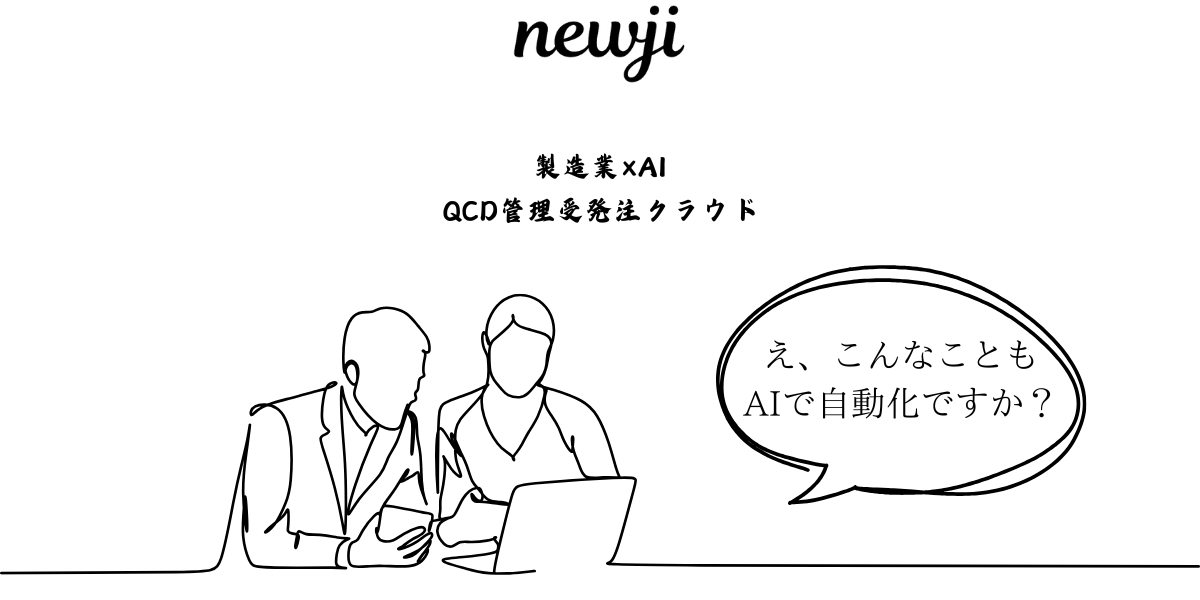
Differences Between Multi-Axis Milling and Single Spindle Milling
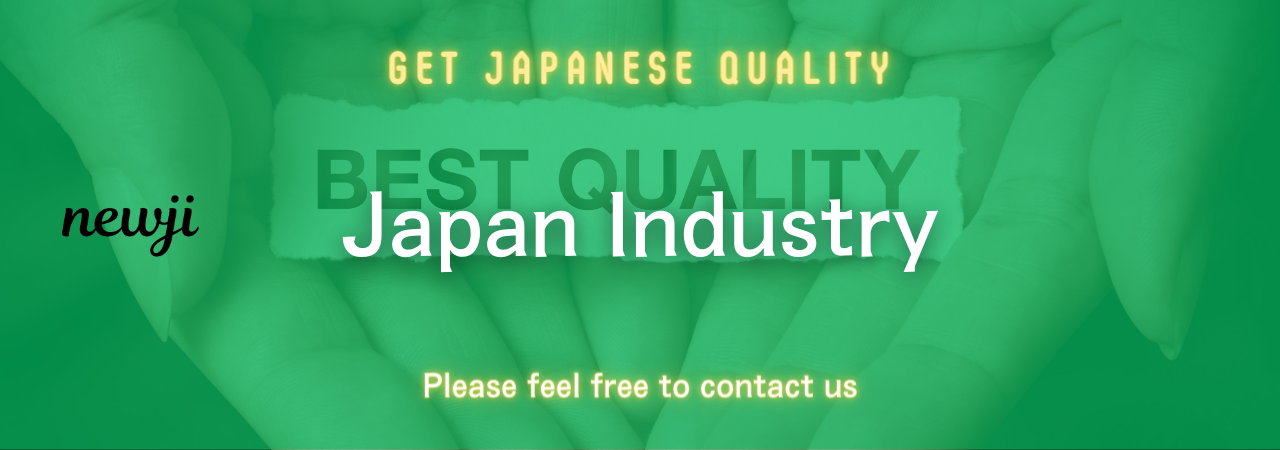
目次
Introduction to Milling
Milling is a crucial process in the manufacturing industry.
It involves the precise removal of material using rotary cutters.
This process allows manufacturers to shape and create parts with a high degree of accuracy.
Milling machines have evolved significantly over the years, and two common types you may encounter are multi-axis milling and single spindle milling.
Understanding the differences between these two methods can be pivotal for choosing the right approach in manufacturing.
What is Single Spindle Milling?
Single spindle milling is one of the more traditional approaches to milling.
It relies on a single spindle that operates with a single axis of movement.
This method typically involves the movement of the workpiece against a stationary milling cutter.
With single spindle milling, the machine primarily moves in a linear or rotational motion.
The precision of this method is notable, especially for simpler projects requiring less complex shapes and surfaces.
It is often used for creating flat surfaces, grooves, or slotting applications.
Advantages of Single Spindle Milling
Single spindle milling is known for its simplicity and ease of use.
The machinery is usually less costly compared to more complex milling machines.
Maintenance is typically more straightforward due to its simpler design.
Additionally, operators can achieve high precision in less intricate tasks, making it a popular choice for tasks that do not require the complexity of multi-axis operations.
Single spindle milling is also a great option for small-scale production or specialty items where cost and simplicity outweigh the need for speed or complexity.
Understanding Multi-Axis Milling
Multi-axis milling offers a more advanced approach compared to single spindle milling.
Instead of operating along a single axis, multi-axis milling involves the use of multiple axes at the same time.
For example, a common setup may involve 3-axis, 4-axis, or even 5-axis machines, allowing for intricate shaping and detailed manufacturing of parts.
This means that the cutting tool can move across multiple dimensions, creating complex geometries that are not possible with traditional single spindle milling.
Advantages of Multi-Axis Milling
The primary benefit of multi-axis milling is its ability to produce complex parts in a single setup.
It reduces the need for multiple fixtures and repositioning, which saves time and enhances precision.
Multi-axis milling is ideal for producing parts with detailed features or those requiring a high degree of precision.
It is especially beneficial in industries such as aerospace, automotive, and medical devices where complex geometries are common.
Moreover, multi-axis milling can lead to a superior finish on the surfaces of parts because of its capability to perform continuous machining operations with limited manual intervention.
Comparing the Costs
Cost is a significant factor when deciding between single spindle and multi-axis milling.
Single spindle machines are typically less expensive upfront.
They may also incur lower maintenance costs due to their simpler design and fewer moving parts, which can be advantageous for companies with budget constraints.
On the other hand, multi-axis milling systems might demand a higher investment initially.
They also tend to have more complex maintenance needs.
However, the efficiency and ability to handle complex projects often justify the higher costs, particularly in production environments requiring high precision and intricate detailing.
Efficiency and Speed
When it comes to efficiency, multi-axis milling often stands out.
It allows manufacturers to complete complex tasks quickly due to its capability of moving along multiple axes simultaneously.
This reduces the time spent on production and increases throughput.
Single spindle milling, while efficient for simpler tasks, may require multiple setups or operations for more complex designs, leading to longer production times.
The choice between the two might depend on the scale and nature of production.
For large-scale, intricate projects, multi-axis may provide the speed and precision needed.
In contrast, for smaller, simpler tasks, single spindle milling may suffice.
Choosing Between the Two
There’s no one-size-fits-all answer when it comes to choosing between multi-axis and single spindle milling.
The decision largely depends on the specific requirements of your projects.
If your production involves intricate designs with complex three-dimensional shapes and high accuracy requirements, multi-axis milling is likely the more suitable choice.
The ability to produce complex parts quickly with excellent finishes can significantly enhance productivity and quality.
Conversely, if your needs are for simpler parts, or you are working within a tight budget, single spindle milling offers a reliable and cost-effective solution.
Conclusion
Both multi-axis milling and single spindle milling play vital roles in manufacturing, each with distinct advantages and drawbacks.
Considering factors such as cost, complexity, precision, and production requirements will help guide the decision on which method to employ.
Understanding these differences allows manufacturers to tailor their operations for optimal efficiency and effectiveness, ensuring the production of high-quality parts tailored to their specific needs.
資料ダウンロード
QCD管理受発注クラウド「newji」は、受発注部門で必要なQCD管理全てを備えた、現場特化型兼クラウド型の今世紀最高の受発注管理システムとなります。
ユーザー登録
受発注業務の効率化だけでなく、システムを導入することで、コスト削減や製品・資材のステータス可視化のほか、属人化していた受発注情報の共有化による内部不正防止や統制にも役立ちます。
NEWJI DX
製造業に特化したデジタルトランスフォーメーション(DX)の実現を目指す請負開発型のコンサルティングサービスです。AI、iPaaS、および先端の技術を駆使して、製造プロセスの効率化、業務効率化、チームワーク強化、コスト削減、品質向上を実現します。このサービスは、製造業の課題を深く理解し、それに対する最適なデジタルソリューションを提供することで、企業が持続的な成長とイノベーションを達成できるようサポートします。
製造業ニュース解説
製造業、主に購買・調達部門にお勤めの方々に向けた情報を配信しております。
新任の方やベテランの方、管理職を対象とした幅広いコンテンツをご用意しております。
お問い合わせ
コストダウンが利益に直結する術だと理解していても、なかなか前に進めることができない状況。そんな時は、newjiのコストダウン自動化機能で大きく利益貢献しよう!
(β版非公開)