- お役立ち記事
- Differences Between Operation Planning and Equipment Planning
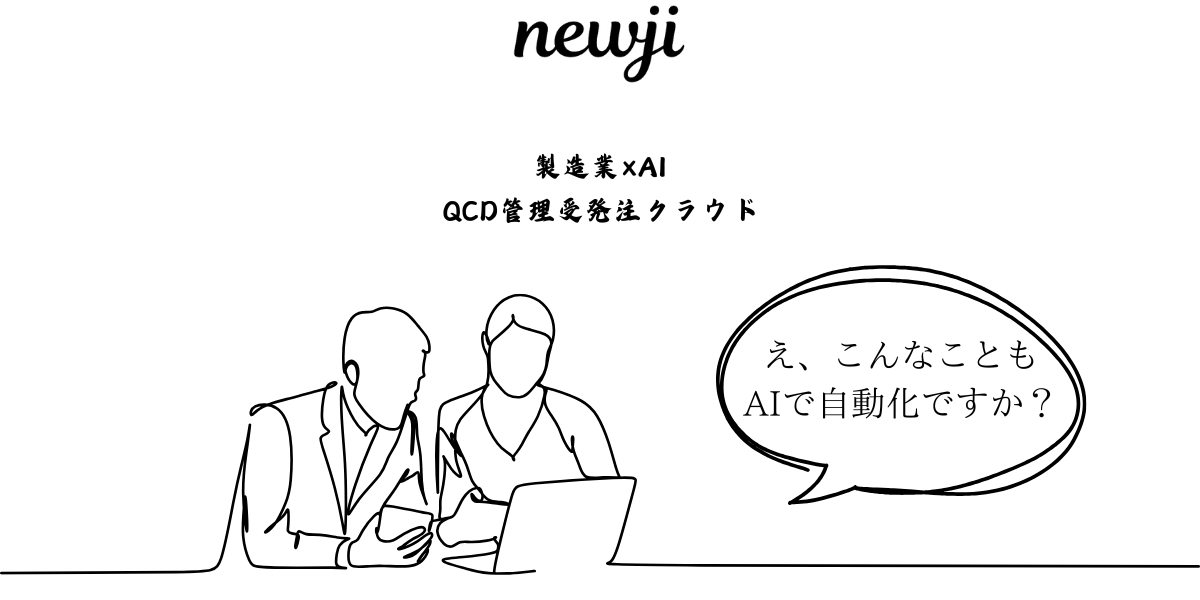
Differences Between Operation Planning and Equipment Planning
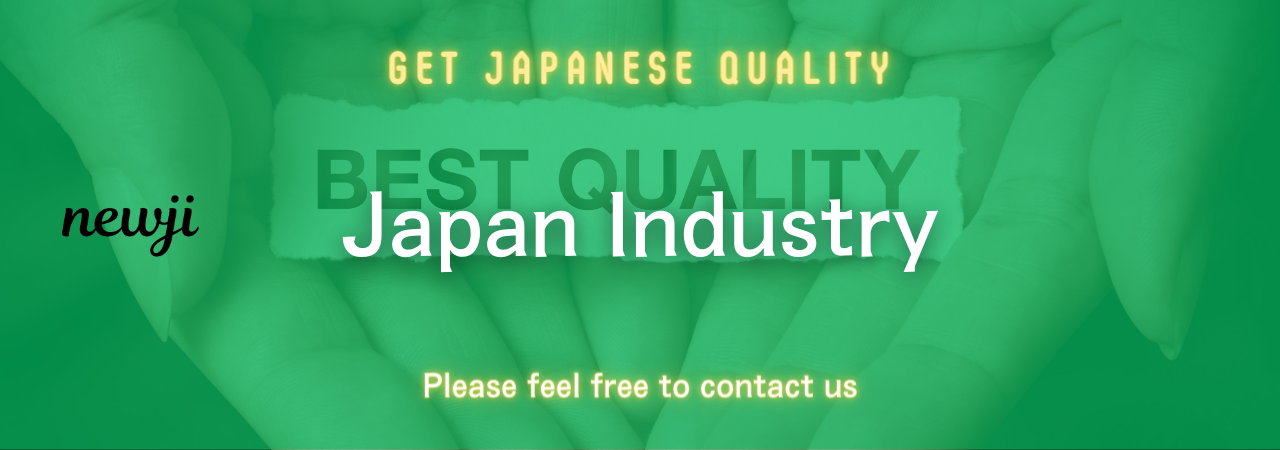
目次
Understanding Operation Planning
Operation planning is a vital component in the field of management that focuses on the day-to-day operations of a business to ensure efficiency and productivity.
It involves creating detailed processes and strategies to manage resources, time, and personnel.
The core aim of operation planning is to optimize the use of available resources, reduce costs, and fulfill customer demands effectively.
One primary aspect of operation planning is scheduling.
This involves outlining tasks and allocating resources to ensure that all operations proceed smoothly without unnecessary delays.
It includes determining what needs to be done, by whom, and within what time frame.
Another critical element is workflow management.
This comprises the steps required to produce a product or deliver a service, along with ensuring each stage of the process is optimally synchronized and efficient.
Identifying potential bottlenecks and opportunities for improvement are constant activities within operation planning.
Inventory control is also a pivotal part of operation planning.
This involves managing inventory levels to meet customers’ demands without overstocking or understocking.
Efficient inventory management can have a direct impact on cost reduction and customer satisfaction.
Furthermore, operation planning involves continuous quality management.
Ensuring that products or services meet specific quality standards is crucial for maintaining customer satisfaction.
Operation planners constantly seek feedback and implement consistent improvements to the processes involved.
Understanding Equipment Planning
Equipment planning, on the other hand, revolves around acquiring, maintaining, and managing the various tools and machines necessary for production operations.
Its primary focus is ensuring that equipment is available, reliable, and functioning efficiently.
The first step in equipment planning is understanding equipment requirements.
This involves identifying the specific equipment needed for different tasks or projects and assessing their impact on productivity and cost.
It’s crucial to choose the right equipment that fits the specific needs of the business operations.
Once the equipment is selected, the next stage is procurement.
This involves purchasing or leasing the necessary machinery or tools while considering factors such as cost, maintenance, durability, and efficiency.
Effective procurement strategies can lead to significant savings and better equipment performance in the long run.
Maintenance planning is a significant component of equipment planning.
Regular maintenance activities are essential to prolong the lifespan of equipment, enhance safety, and prevent unexpected breakdowns.
Establishing a proactive maintenance schedule ensures machinery operates smoothly and efficiently.
Equipment planning also involves replacement and upgrade strategies.
As technology advances and wear and tear occur, planners must decide when to replace outdated equipment or invest in new technologies to remain competitive.
This aspect of planning can have a profound impact on the overall output and effectiveness of operations.
Finally, an essential element of equipment planning is compliance and safety.
Ensuring that all equipment adheres to safety regulations and standards is not only important for worker safety but also helps avoid legal issues and fines.
Key Differences between Operation Planning and Equipment Planning
While both operation and equipment planning are crucial for an organization’s success, they focus on different aspects of the business process.
Operation planning primarily deals with the process management side.
It emphasizes optimizing resource allocation, workflow management, scheduling, and inventory control.
Its goal is to ensure that routine operations are as efficient as possible, reducing waste and meeting customer demands effectively.
Equipment planning, by contrast, centers on the tools and machines themselves.
It involves procurement, maintenance, and the effective management of machinery and technology.
The focus here is on ensuring all equipment is available and functioning optimally, preventing downtime, and enhancing productivity.
In terms of scope, operational planning is broader as it encompasses all aspects of running the operations smoothly.
On the other hand, equipment planning is more specialized, focusing specifically on the physical means required to perform the operational tasks.
Interconnection Between Operation Planning and Equipment Planning
Despite their differences, operation planning and equipment planning are interconnected and can significantly influence each other.
Effective equipment planning can facilitate successful operation planning by ensuring the right tools and machinery are in place when needed.
This availability can enhance task scheduling, workflow processes, and ultimately the quality of products or services.
Similarly, operation planning can inform equipment needs by identifying areas where new machinery or technology could streamline processes or improve efficiency.
This feedback loop allows businesses to prioritize investments in equipment that will have the most meaningful impact on overall operations.
Both types of planning require a collaborative approach among various departments within an organization to ensure alignment with broader organizational goals.
By integrating operation and equipment planning, businesses can create a well-rounded strategy that encompasses all necessary resources, ensuring smooth and efficient operations.
In conclusion, while operation planning and equipment planning serve distinct purposes within an organization, they are both essential for achieving operational excellence.
By understanding the unique features and interdependencies of each, businesses can better optimize their processes and achieve competitive advantages in their industries.
資料ダウンロード
QCD調達購買管理クラウド「newji」は、調達購買部門で必要なQCD管理全てを備えた、現場特化型兼クラウド型の今世紀最高の購買管理システムとなります。
ユーザー登録
調達購買業務の効率化だけでなく、システムを導入することで、コスト削減や製品・資材のステータス可視化のほか、属人化していた購買情報の共有化による内部不正防止や統制にも役立ちます。
NEWJI DX
製造業に特化したデジタルトランスフォーメーション(DX)の実現を目指す請負開発型のコンサルティングサービスです。AI、iPaaS、および先端の技術を駆使して、製造プロセスの効率化、業務効率化、チームワーク強化、コスト削減、品質向上を実現します。このサービスは、製造業の課題を深く理解し、それに対する最適なデジタルソリューションを提供することで、企業が持続的な成長とイノベーションを達成できるようサポートします。
オンライン講座
製造業、主に購買・調達部門にお勤めの方々に向けた情報を配信しております。
新任の方やベテランの方、管理職を対象とした幅広いコンテンツをご用意しております。
お問い合わせ
コストダウンが利益に直結する術だと理解していても、なかなか前に進めることができない状況。そんな時は、newjiのコストダウン自動化機能で大きく利益貢献しよう!
(Β版非公開)