- お役立ち記事
- Differences Between Parts Inspection and Final Product Inspection
月間76,176名の
製造業ご担当者様が閲覧しています*
*2025年3月31日現在のGoogle Analyticsのデータより
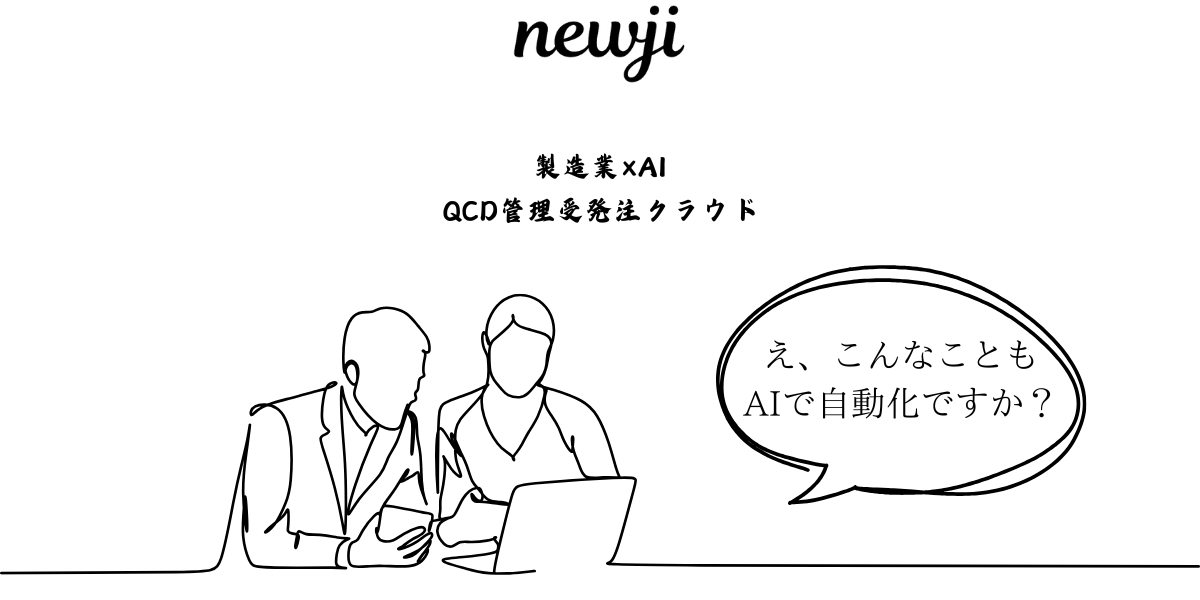
Differences Between Parts Inspection and Final Product Inspection
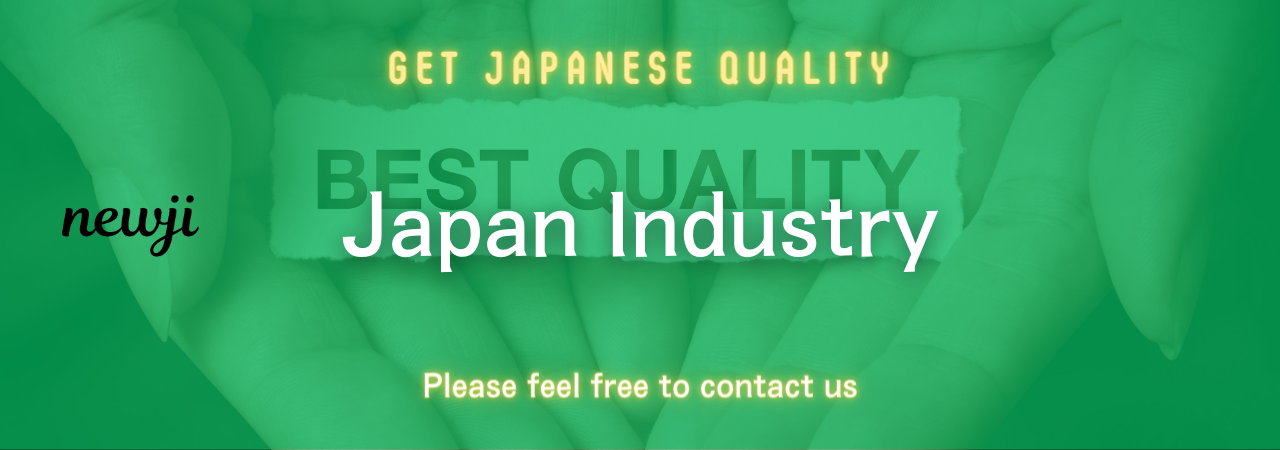
When it comes to manufacturing, quality control is essential.
Two crucial processes in ensuring that products meet required standards are parts inspection and final product inspection.
Both play integral roles, but they serve different purposes.
In this article, we will delve into the differences between parts inspection and final product inspection and why each is important.
目次
What Is Parts Inspection?
Definition
Parts inspection involves examining individual components that make up a final product.
This is usually done at various stages of production.
The goal is to identify defects or inconsistencies before they become part of the final product.
When It Happens
Parts inspection can happen before, during, or after the part has been produced.
For example, raw materials might be inspected before they are used in manufacturing.
Similarly, semi-finished parts can undergo inspection during the production process.
Purpose
The primary purpose of parts inspection is to catch issues early.
Identifying and rectifying problems at the component level can save time and resources.
It ensures that only quality parts make it to the next stage of production.
Methods
There are various methods for parts inspection, including visual inspection, dimensional checks, and functional tests.
Automated systems, such as machine vision, can also be used to inspect parts for flaws.
The method chosen often depends on the type of part being inspected.
What Is Final Product Inspection?
Definition
Final product inspection involves examining the complete product after all the parts have been assembled and any additional processes have been completed.
This is the last stage of quality control before the product reaches the customer.
When It Happens
As the name suggests, final product inspection occurs at the end of the production process.
It serves as the last checkpoint to ensure that the product meets all specifications and quality criteria.
Purpose
The purpose of final product inspection is to provide a comprehensive check of the entire product.
This includes verifying that all parts have been correctly assembled, performing functional tests, and ensuring the product meets customer expectations.
Methods
Methods for final product inspection are often more comprehensive.
These can include visual inspections, functional tests, performance assessments, and safety checks.
Sometimes, specialized equipment is used to simulate how the product will be used in real-world conditions.
Key Differences Between Parts Inspection and Final Product Inspection
Focus
Parts inspection focuses on individual components, while final product inspection looks at the entire product.
This fundamental difference guides the methods and objectives of each process.
Timing
Parts inspection occurs throughout the production process.
Final product inspection, on the other hand, happens only after the product is fully assembled.
Scope
The scope of parts inspection is limited to specific components.
In contrast, final product inspection covers the complete product, ensuring that all parts work together as intended.
Cost
Catching defects during parts inspection can be more cost-effective.
It prevents the need for reworking the final product, which can be expensive.
However, final product inspection is crucial for ensuring that the end product is of high quality.
Why Both Are Important
Both parts inspection and final product inspection are essential for maintaining quality in manufacturing.
Parts inspection helps to catch defects early, saving time and resources.
Final product inspection ensures that the complete product meets all necessary standards.
Customer Satisfaction
Customers expect high-quality products.
By combining parts inspection with final product inspection, manufacturers can ensure that the final product meets or exceeds customer expectations.
This leads to higher customer satisfaction and repeat business.
Compliance
Many industries have stringent regulations that products must meet.
Both types of inspections help manufacturers comply with these regulations.
Failure to do so can result in penalties, recalls, or even legal action.
Efficiency
Identifying issues early through parts inspection can streamline the production process.
Final product inspection ensures that the product is ready for market, eliminating the need for costly recalls or rework.
Conclusion
In summary, parts inspection and final product inspection are both critical components of the quality control process.
While they serve different purposes, both are essential for ensuring that the final product is of the highest quality.
By implementing both types of inspections, manufacturers can improve efficiency, comply with regulations, and, most importantly, satisfy their customers.
Understanding the differences between parts inspection and final product inspection can help businesses optimize their quality control processes.
This, in turn, leads to better products and a stronger reputation in the market.
By valuing both types of inspections, manufacturers are well-positioned to succeed in today’s competitive landscape.
資料ダウンロード
QCD管理受発注クラウド「newji」は、受発注部門で必要なQCD管理全てを備えた、現場特化型兼クラウド型の今世紀最高の受発注管理システムとなります。
ユーザー登録
受発注業務の効率化だけでなく、システムを導入することで、コスト削減や製品・資材のステータス可視化のほか、属人化していた受発注情報の共有化による内部不正防止や統制にも役立ちます。
NEWJI DX
製造業に特化したデジタルトランスフォーメーション(DX)の実現を目指す請負開発型のコンサルティングサービスです。AI、iPaaS、および先端の技術を駆使して、製造プロセスの効率化、業務効率化、チームワーク強化、コスト削減、品質向上を実現します。このサービスは、製造業の課題を深く理解し、それに対する最適なデジタルソリューションを提供することで、企業が持続的な成長とイノベーションを達成できるようサポートします。
製造業ニュース解説
製造業、主に購買・調達部門にお勤めの方々に向けた情報を配信しております。
新任の方やベテランの方、管理職を対象とした幅広いコンテンツをご用意しております。
お問い合わせ
コストダウンが利益に直結する術だと理解していても、なかなか前に進めることができない状況。そんな時は、newjiのコストダウン自動化機能で大きく利益貢献しよう!
(β版非公開)