- お役立ち記事
- Differences Between Parts Ordering and Material Ordering
月間76,176名の
製造業ご担当者様が閲覧しています*
*2025年3月31日現在のGoogle Analyticsのデータより
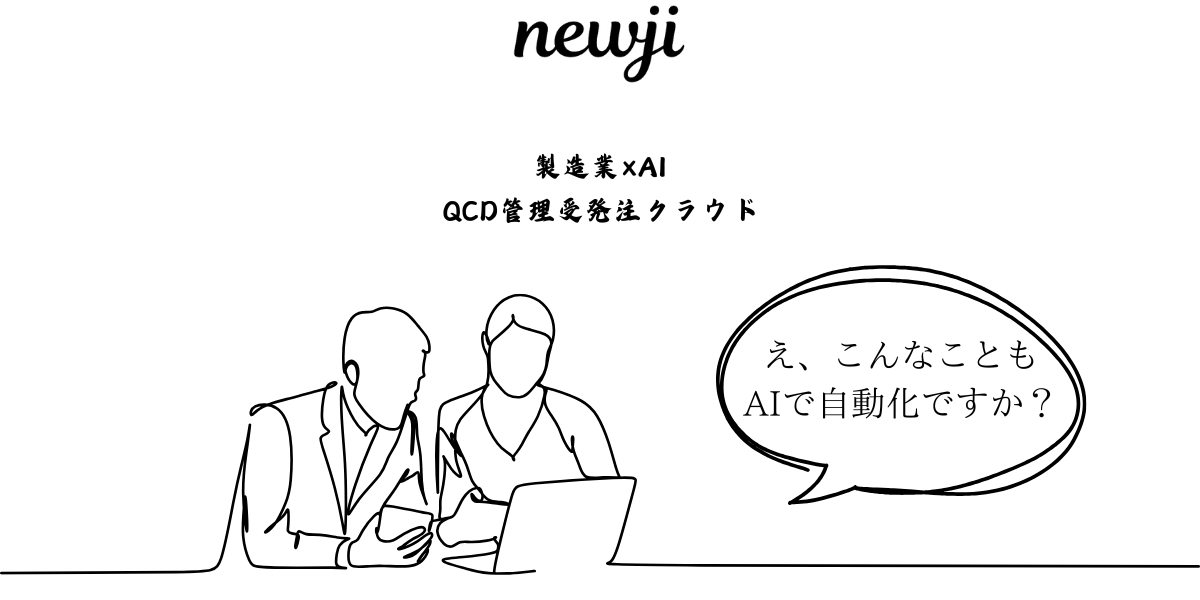
Differences Between Parts Ordering and Material Ordering
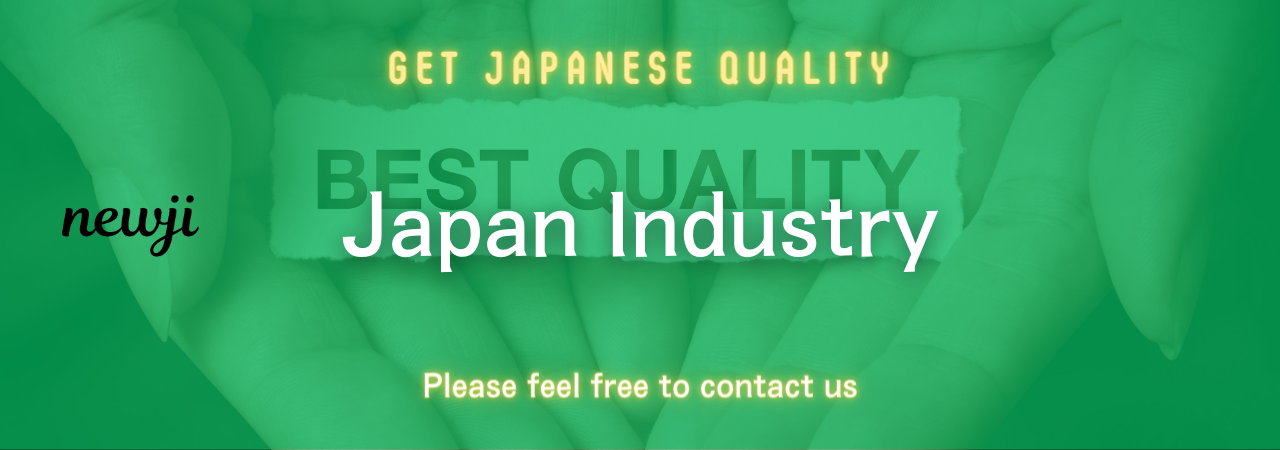
目次
Understanding Parts Ordering
Ordering parts is a fundamental aspect of supply chain management, particularly in industries like automotive, electronics, and manufacturing.
Parts ordering involves requesting specific components required to complete a product or repair an item.
This type of ordering is typically detailed and often requires precise specifications to ensure the correct part is delivered.
Parts ordering usually happens when a specific component of a machine or device needs to be repaired or replaced.
The ordering process may involve consulting manuals or databases to find precise part numbers, dimensions, material composition, and other details.
Once identified, these parts are procured through suppliers, distributors, or sometimes the original equipment manufacturer (OEM).
An essential part of this process is maintaining a parts inventory list that assists in quick reordering when supplies run low.
Advanced systems can even automate this process, sending requests directly to suppliers when thresholds are met.
Effective parts ordering ensures minimal downtime for machinery and products, maintaining operational efficiency.
Steps in Parts Ordering
1. **Identification:** Identify the required part using precise specifications or part numbers.
2. **Verification:** Confirm the part with technical manuals or expert advice to ensure compatibility.
3. **Supplier Selection:** Choose a reliable supplier or distributor for the order.
4. **Order Placement:** Place the order, detailing specifications, quantities, and delivery timelines.
5. **Delivery and Inspection:** Upon delivery, inspect the parts to confirm they meet the required standards.
Understanding Material Ordering
Material ordering differs from parts ordering in scope and purpose.
It involves acquiring the bulk raw materials necessary for production processes.
These materials may include metals, plastics, textiles, chemicals, or other foundational substances used in manufacturing.
Material ordering is crucial for industries looking to maintain a seamless production line.
It focuses on procurement strategies, inventory management, and cost efficiency.
Unlike parts ordering, which is detail-oriented, material ordering often deals with larger quantities and potentially less precision on individual item specifications.
The ordering process for materials also requires comprehensive planning.
This can involve market analysis to track price trends, choosing the right vendors, and sometimes even long-term contracts to lock in prices or ensure ongoing supply.
Steps in Material Ordering
1. **Needs Assessment:** Determine the types and amounts of materials required for upcoming production.
2. **Market Research:** Analyze market conditions and pricing to make cost-effective purchases.
3. **Supplier Evaluation:** Vet suppliers for their reliability, quality of materials, and pricing.
4. **Procurement Planning:** Develop a procurement plan that aligns with production schedules.
5. **Order Execution:** Execute the order, specifying required quantities and delivery schedules.
6. **Quality Assurance:** Upon receipt, test materials to ensure they meet production standards.
Key Differences Between Parts and Material Ordering
While both processes aim to ensure that enough resources are available for production or repair, they diverge in several key ways:
– **Scope and Detail:** Parts ordering is highly specific, focusing on individual components.
Material ordering, on the other hand, encompasses whole categories of raw materials.
– **Volume:** Parts are usually ordered in smaller quantities compared to materials, which are often procured in bulk.
– **Specification Precision:** Parts require precise specifications; materials may allow for a range of acceptable qualities.
– **Use Case:** Parts are used for specific repairs and assemblies, while materials form the essential elements of new productions.
– **Order Timing:** Parts are often ordered as needed for maintenance, whereas materials are typically ordered well in advance of production cycles.
Integration of Parts and Materials in Supply Chains
Successful businesses integrate both parts and materials ordering into their supply chains harmoniously.
It’s crucial to have robust systems that track inventories of both types, ensuring that neither parts nor materials run out unexpectedly.
A comprehensive supply chain management system can help forecast needs, streamline ordering processes, and reduce costs.
Additionally, flexibility in updating orders as demand changes allows for smooth, uninterrupted operations.
Cross-departmental communication is also vital.
Production, engineering, and procurement teams must collaborate to ensure that both parts and materials align with current projects and future needs.
When executed effectively, streamlined parts and materials ordering benefits businesses by reducing downtime, ensuring product quality, and optimizing resource utilization.
Conclusion
Understanding the differences between parts ordering and material ordering provides clarity on how each contributes to the manufacturing and maintenance processes.
Each type has its unique processes, requirements, and implications for production efficiency.
While parts ordering focuses on precision and specific components, material ordering emphasizes bulk procurement and production support.
By mastering both areas, companies can enhance their operational capabilities, improve cost management, and maintain high standards of product integrity.
Incorporating sophisticated management systems and market-responsive strategies ensures ongoing success in meeting supply chain demands.
資料ダウンロード
QCD管理受発注クラウド「newji」は、受発注部門で必要なQCD管理全てを備えた、現場特化型兼クラウド型の今世紀最高の受発注管理システムとなります。
ユーザー登録
受発注業務の効率化だけでなく、システムを導入することで、コスト削減や製品・資材のステータス可視化のほか、属人化していた受発注情報の共有化による内部不正防止や統制にも役立ちます。
NEWJI DX
製造業に特化したデジタルトランスフォーメーション(DX)の実現を目指す請負開発型のコンサルティングサービスです。AI、iPaaS、および先端の技術を駆使して、製造プロセスの効率化、業務効率化、チームワーク強化、コスト削減、品質向上を実現します。このサービスは、製造業の課題を深く理解し、それに対する最適なデジタルソリューションを提供することで、企業が持続的な成長とイノベーションを達成できるようサポートします。
製造業ニュース解説
製造業、主に購買・調達部門にお勤めの方々に向けた情報を配信しております。
新任の方やベテランの方、管理職を対象とした幅広いコンテンツをご用意しております。
お問い合わせ
コストダウンが利益に直結する術だと理解していても、なかなか前に進めることができない状況。そんな時は、newjiのコストダウン自動化機能で大きく利益貢献しよう!
(β版非公開)