- お役立ち記事
- Differences Between Precision Lathe Machining and Rough Lathe Machining
月間77,185名の
製造業ご担当者様が閲覧しています*
*2025年2月28日現在のGoogle Analyticsのデータより
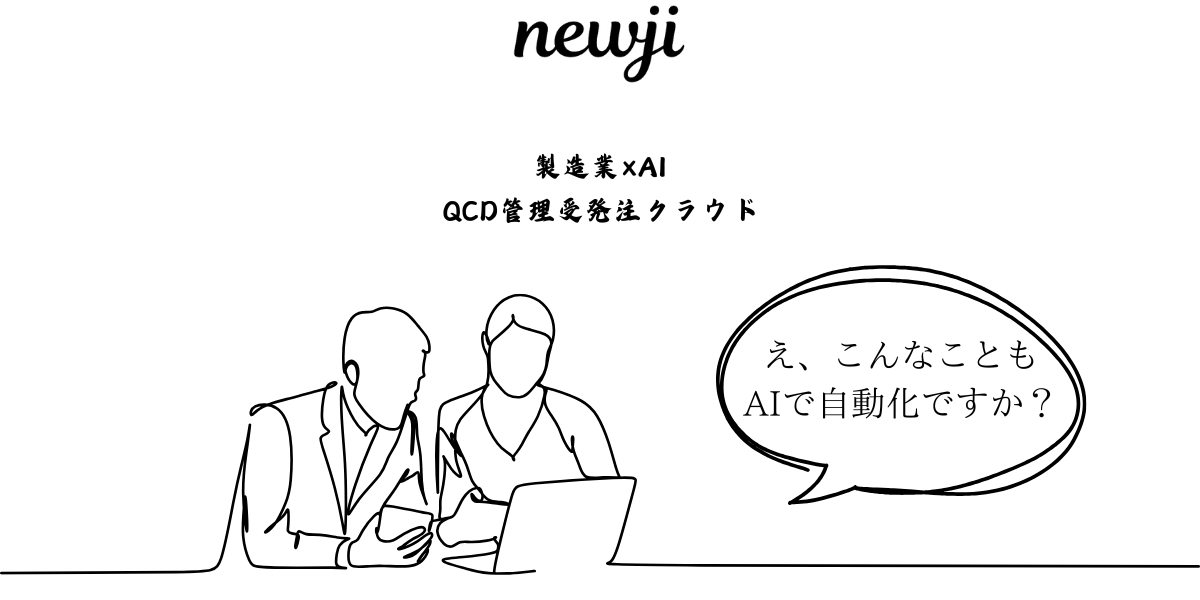
Differences Between Precision Lathe Machining and Rough Lathe Machining
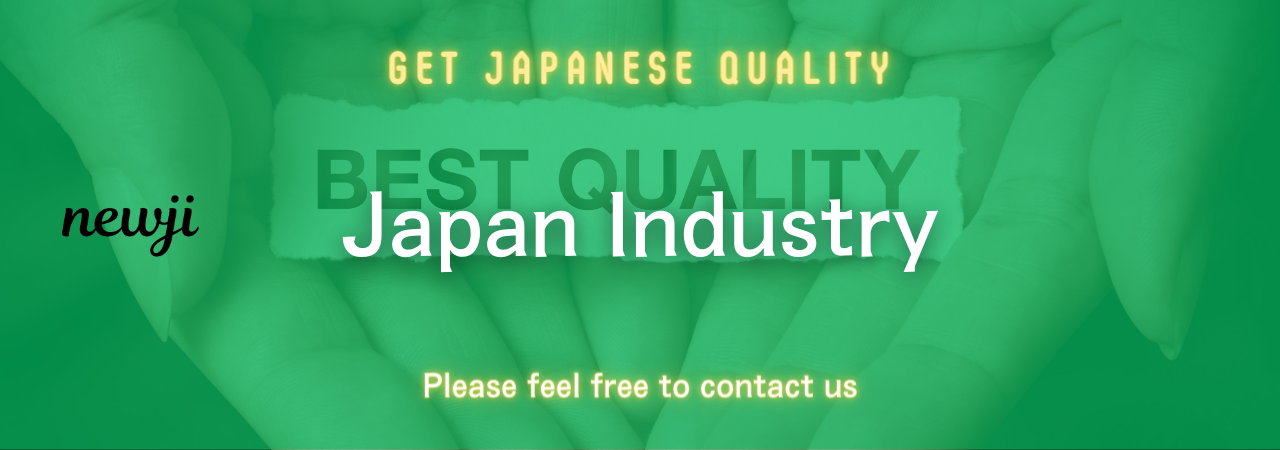
When it comes to machining, understanding the differences between precision lathe machining and rough lathe machining can make all the difference in achieving the results you want for your project.
Both types serve unique purposes and have specific applications.
Let’s dive into these two machining processes to uncover their distinctions and advantages.
目次
Introduction to Lathe Machining
Lathe machining is a classical technique used in manufacturing to shape materials, primarily metals, using a lathe.
This process involves the material being held in place and rotated at high speed while a cutting tool shapes it.
Lathes are crucial in fields ranging from automotive to aerospace engineering.
Understanding the difference between precision lathe machining and rough lathe machining starts with grasping what each process entails.
What Is Rough Lathe Machining?
Rough lathe machining is the initial stage in the machining process.
It focuses on removing the maximum amount of material from the workpiece as quickly as possible.
This involves using larger, more aggressive cutting tools to take larger cuts.
Characteristics of Rough Lathe Machining
Several features define rough lathe machining.
First, it deals with a much higher material removal rate than precision machining.
It employs larger cutting tools that can handle heavy loads.
Second, it prioritizes speed over accuracy.
The end product after rough machining may have a significant degree of surface roughness and may require further processing.
Third, rough machining usually sets the groundwork for subsequent precision machining processes.
When to Use Rough Lathe Machining
Rough lathe machining is ideal when you need to quickly shape a raw material to a basic form.
It is commonly used in the early stages of a project where the primary goal is to achieve a general form, leaving finer details for later.
It’s particularly useful for preparing large metal components in industries such as shipbuilding or heavy machinery manufacturing.
What Is Precision Lathe Machining?
Precision lathe machining, on the other hand, is all about accuracy and fine details.
This process takes over after rough machining and focuses on refining the shape and dimensions to meet precise specifications.
Characteristics of Precision Lathe Machining
Precision lathe machining is characterized by its meticulous focus on detail.
It uses smaller, more precise cutting tools to make fine cuts, ensuring the dimensions and surface finish meet exact standards.
This method often operates at slower speeds compared to rough machining but yields a much smoother finish and higher accuracy.
It is a critical step in producing high-quality components used in industries where tolerance and accuracy are crucial.
When to Use Precision Lathe Machining
Precision lathe machining comes into play in the final stages of production or when the project requires high accuracy and a fine surface finish from the beginning.
It is essential for manufacturing parts that need to fit together precisely, such as in the aerospace, automotive, and medical device industries.
By employing precision machining, manufacturers can achieve the exact dimensions and surface finish required for high-performance applications.
Key Differences Between Rough and Precision Lathe Machining
Having delved into the specifics of each process, let’s highlight the key differences to provide a clearer comparison.
Material Removal vs. Accuracy
The primary difference lies in their focus: rough machining is centered on rapid material removal, while precision machining is focused on intricate details and accuracy.
Rough machining uses larger tools to quickly remove significant amounts of material, whereas precision machining employs finer tools for meticulous, exact cuts.
Tools and Techniques
While rough machining uses robust tools capable of withstanding heavier loads and removing more material, precision machining tools are designed for detailed work.
In terms of techniques, rough machining may involve straight cuts and broader strokes, whereas precision machining requires carefully controlled movements and often employs computer numerical control (CNC) tools for enhanced accuracy.
Surface Finish
Rough lathe machining typically results in a surface with higher roughness, necessitating further processing.
In contrast, precision lathe machining aims for a finished surface that meets specific smoothness and texture criteria without needing additional refinishing.
Speed vs. Quality
Rough machining prioritizes speed, getting the basic shape done fast.
Precision machining prioritizes quality, taking longer to ensure every detail is perfected.
Benefits of Combining Both Methods
Manufacturers often combine both rough and precision lathe machining for optimal results.
This combination allows for efficient material removal and detailed finish, ensuring both speed and accuracy in the final product.
This approach is particularly advantageous in large-scale production where both raw efficiency and meticulous detail are required.
Cost Efficiency
By using rough machining first, you significantly reduce the time and cost required for the initial shaping.
Transitioning to precision machining ensures that the final product meets all necessary standards without unnecessary material wastage or rework.
Optimized Workflow
Combining both methods enables a streamlined workflow, moving from rapid material removal to detailed finishing without unnecessary delays.
This can lead to faster project completion and optimized use of resources.
Conclusion
Understanding the differences between precision lathe machining and rough lathe machining can guide you in choosing the right approach for your project.
While rough machining provides speed and efficiency in the initial stages, precision machining ensures detailed accuracy and a fine finish.
Combining both strategies can offer the best of both worlds, achieving high-quality results in a cost-effective manner.
Whether you’re developing large industrial components or intricate precision parts, knowing when and how to utilize rough and precision lathe machining is crucial for successful manufacturing.
資料ダウンロード
QCD管理受発注クラウド「newji」は、受発注部門で必要なQCD管理全てを備えた、現場特化型兼クラウド型の今世紀最高の受発注管理システムとなります。
ユーザー登録
受発注業務の効率化だけでなく、システムを導入することで、コスト削減や製品・資材のステータス可視化のほか、属人化していた受発注情報の共有化による内部不正防止や統制にも役立ちます。
NEWJI DX
製造業に特化したデジタルトランスフォーメーション(DX)の実現を目指す請負開発型のコンサルティングサービスです。AI、iPaaS、および先端の技術を駆使して、製造プロセスの効率化、業務効率化、チームワーク強化、コスト削減、品質向上を実現します。このサービスは、製造業の課題を深く理解し、それに対する最適なデジタルソリューションを提供することで、企業が持続的な成長とイノベーションを達成できるようサポートします。
製造業ニュース解説
製造業、主に購買・調達部門にお勤めの方々に向けた情報を配信しております。
新任の方やベテランの方、管理職を対象とした幅広いコンテンツをご用意しております。
お問い合わせ
コストダウンが利益に直結する術だと理解していても、なかなか前に進めることができない状況。そんな時は、newjiのコストダウン自動化機能で大きく利益貢献しよう!
(β版非公開)