- お役立ち記事
- Differences Between Preventive Maintenance and Condition-Based Maintenance
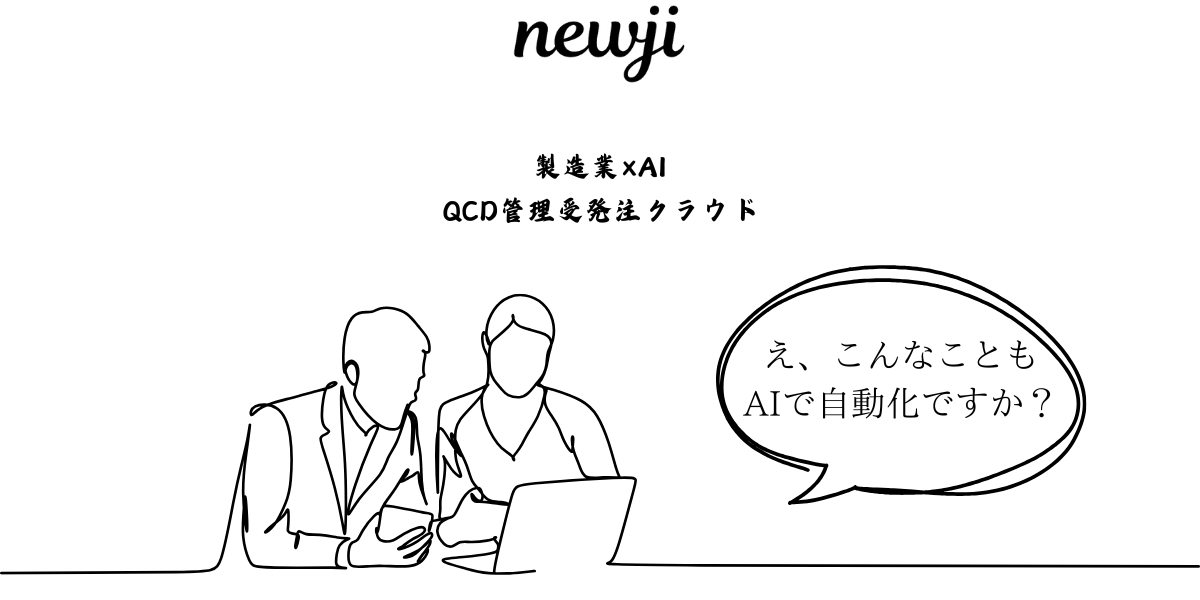
Differences Between Preventive Maintenance and Condition-Based Maintenance
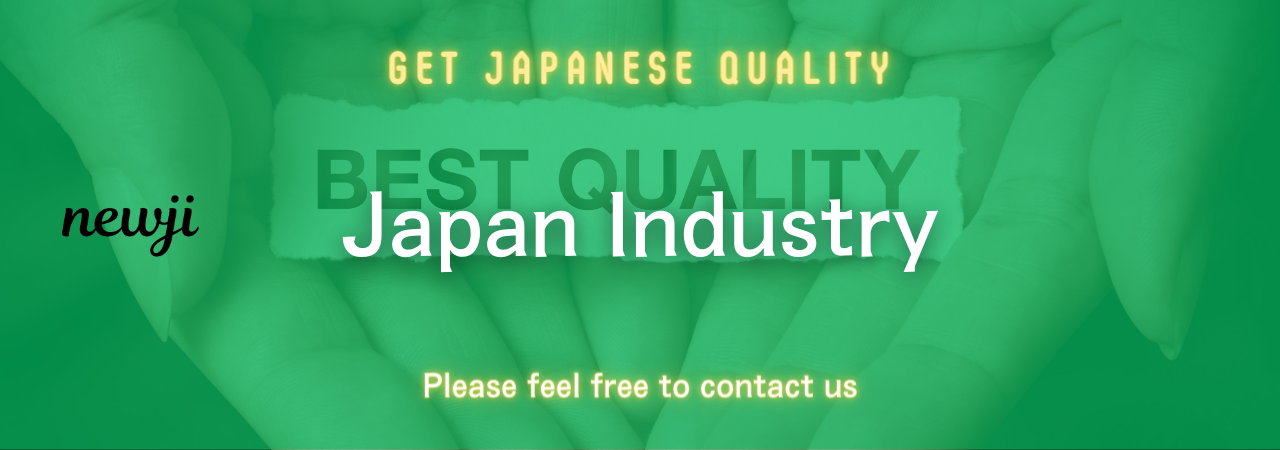
目次
Understanding Preventive Maintenance
Preventive maintenance is a proactive approach employed by organizations to maintain their equipment and systems in optimal working condition.
This maintenance strategy involves routinely scheduled inspections, adjustments, and replacements, designed to prevent unexpected failures or breakdowns.
The primary goal of preventive maintenance is to extend the lifespan of equipment, enhance productivity, and ensure the safety of operations.
Regularly scheduled maintenance tasks can include cleaning, lubrication, parts replacement, and performance checks.
In industrial settings, preventive maintenance might be applied using manual inspections and checklists or through computerized systems that schedule maintenance activities based on time intervals.
By identifying and fixing potential issues before they lead to significant problems, companies can avoid costly repairs and reduce downtime.
Benefits of Preventive Maintenance
One of the key advantages of preventive maintenance is the ability to plan for equipment servicing in advance.
This planning helps organizations minimize disruptions to daily operations.
By regularly servicing equipment, companies can significantly reduce the risk of unexpected failures that can halt production processes.
This maintenance approach also helps in controlling operational costs over time.
Since equipment is serviced before major problems arise, the likelihood of needing expensive emergency repairs is reduced.
Additionally, preventive maintenance promotes safety by ensuring that machinery operates correctly, minimizing the risk of accidents.
The strategy is environmentally friendly too, as well-maintained equipment generally consumes less energy and runs more efficiently.
Delving into Condition-Based Maintenance
Condition-based maintenance (CBM) is another proactive maintenance strategy, but it differs from preventive maintenance by focusing on the actual condition of equipment rather than on predetermined schedules.
CBM relies on monitoring the operating conditions of machinery in real-time or at regular intervals, using various diagnostic tools and sensors.
These tools include temperature sensors, vibration analysis devices, and oil analysis techniques.
The data collected is analyzed to assess the health and performance of the equipment, predicting when maintenance should be performed to avoid failures.
This approach is data-driven and involves advanced technologies to detect signs of wear and tear or potential issues.
The aim of condition-based maintenance is to perform maintenance tasks only when they are genuinely needed, based on the condition indicators revealed through constant monitoring.
Advantages of Condition-Based Maintenance
One of the most significant benefits of CBM is its efficiency in managing resources.
Since maintenance is performed based on the actual need rather than on arbitrary schedules, resources such as time, labor, and materials are used more effectively.
This efficiency can lead to substantial cost savings.
Condition-based maintenance reduces the risk of unnecessary maintenance actions, thereby extending the life of parts and systems.
It also allows for early detection of potential issues, which can be addressed before they escalate into serious problems.
Another advantage is improved equipment reliability and availability.
With CBM, maintenance is performed exactly when it is needed, which helps ensure that equipment is in top condition and ready for use when required.
This method also aligns well with modern industry trends that emphasize data analytics and IoT technology for smart and efficient operations.
Key Differences between Preventive and Condition-Based Maintenance
While both preventive and condition-based maintenance aim to keep equipment in good working condition, their methodologies and implementations differ considerably.
Preventive maintenance follows a set schedule determined by time intervals, such as weekly, monthly, or yearly.
In contrast, condition-based maintenance relies on the continuous monitoring of equipment conditions and performs maintenance based on the actual data collected.
This means CBM requires investment in monitoring technologies and data analysis tools, which may initially be costly but can prove economical in the long run due to the reduction of unnecessary maintenance tasks.
Preventive maintenance, due to its fixed scheduling, may sometimes result in servicing that is not immediately necessary, leading to excess use of resources.
However, it is easier to plan and does not require the extensive monitoring systems needed for condition-based maintenance.
Choosing the Right Maintenance Strategy
Deciding whether to implement preventive maintenance or condition-based maintenance depends on several factors, including the type of equipment, industry, and specific operational needs.
Preventive maintenance might be more suitable for companies with equipment that has been historically stable and reliable without complex monitoring requirements.
It is also more practical for organizations looking for predictable and planned maintenance activities.
On the other hand, industries with highly critical or complex machinery might find condition-based maintenance more effective, as it allows for real-time monitoring and timely interventions.
Companies seeking to embrace cutting-edge technology and data utilization for optimized operations may favor CBM.
It’s important to evaluate the cost implications, available technology, and the criticality of equipment when making this decision.
Some organizations might even benefit from a hybrid approach, utilizing both preventive and condition-based methods for different types of equipment within the same facility.
Conclusion
Understanding the differences between preventive maintenance and condition-based maintenance is crucial for effective asset management.
Both strategies have their distinct benefits and applications, and the choice between them should align with an organization’s specific needs and capabilities.
By maintaining equipment through these proactive strategies, businesses can reduce downtime, enhance productivity, and improve safety, ultimately leading to better operational efficiency and financial performance.
資料ダウンロード
QCD調達購買管理クラウド「newji」は、調達購買部門で必要なQCD管理全てを備えた、現場特化型兼クラウド型の今世紀最高の購買管理システムとなります。
ユーザー登録
調達購買業務の効率化だけでなく、システムを導入することで、コスト削減や製品・資材のステータス可視化のほか、属人化していた購買情報の共有化による内部不正防止や統制にも役立ちます。
NEWJI DX
製造業に特化したデジタルトランスフォーメーション(DX)の実現を目指す請負開発型のコンサルティングサービスです。AI、iPaaS、および先端の技術を駆使して、製造プロセスの効率化、業務効率化、チームワーク強化、コスト削減、品質向上を実現します。このサービスは、製造業の課題を深く理解し、それに対する最適なデジタルソリューションを提供することで、企業が持続的な成長とイノベーションを達成できるようサポートします。
オンライン講座
製造業、主に購買・調達部門にお勤めの方々に向けた情報を配信しております。
新任の方やベテランの方、管理職を対象とした幅広いコンテンツをご用意しております。
お問い合わせ
コストダウンが利益に直結する術だと理解していても、なかなか前に進めることができない状況。そんな時は、newjiのコストダウン自動化機能で大きく利益貢献しよう!
(Β版非公開)