- お役立ち記事
- Differences Between Process Improvement and Quality Improvement
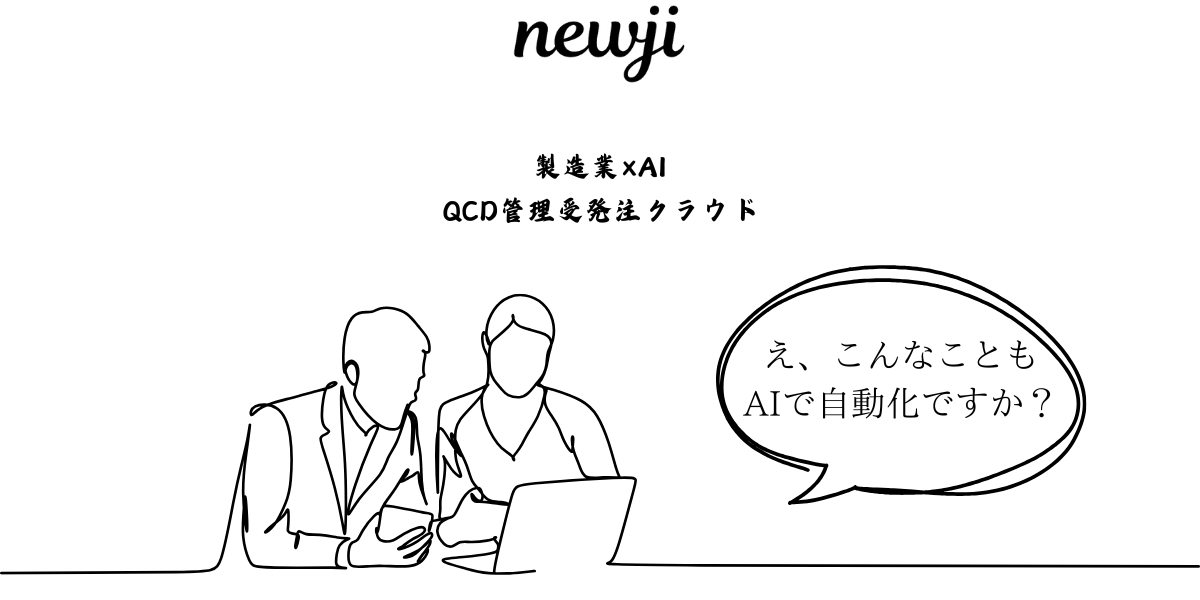
Differences Between Process Improvement and Quality Improvement
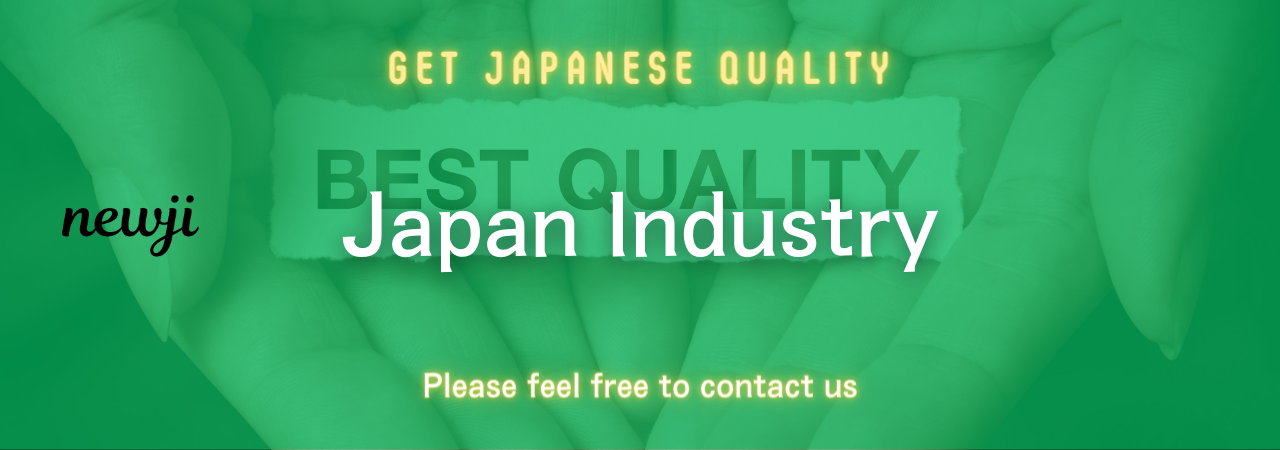
目次
Understanding Process Improvement
Process improvement is a systematic approach aimed at enhancing the way a business operates.
It involves analyzing the existing processes and identifying areas where efficiency can be improved.
The goal is to streamline operations and reduce waste, which can lead to increased productivity and reduced costs.
A key aspect of process improvement is its focus on the entire workflow.
It examines how tasks are completed from start to finish, looking for redundancies, bottlenecks, or unnecessary steps.
Techniques like Lean and Six Sigma are commonly used to guide process improvement initiatives.
These methodologies help organizations eliminate waste and optimize processes, ensuring that resources are used effectively.
Benefits of Process Improvement
Process improvement can lead to significant benefits for an organization.
Firstly, it can considerably increase efficiency.
By removing unnecessary steps and streamlining operations, businesses can produce products or services faster and with less effort.
Secondly, it can lead to cost savings.
Resources are used more effectively, and waste is minimized, allowing companies to reduce their expenses.
Additionally, process improvement can enhance customer satisfaction.
With improved efficiency and reduced errors, customers receive higher-quality products or services in a timely manner.
This can lead to increased customer loyalty and repeat business.
Understanding Quality Improvement
Quality improvement, on the other hand, focuses specifically on enhancing the quality of products or services.
While process improvement is concerned with efficiency, quality improvement aims to ensure products meet or exceed customer standards.
This involves analyzing products or services for defects or areas that do not meet quality expectations.
Quality improvement often incorporates feedback from customers and focuses on upgrading or redesigning aspects of a product or service.
Benefits of Quality Improvement
Quality improvement can result in higher customer satisfaction.
By consistently delivering superior products, businesses can build strong, lasting relationships with their customers.
Another benefit is reduced wastage and rework.
Improving quality can minimize the need for repairs, returns, or corrections, which can help in cutting costs and saving resources.
Moreover, businesses that prioritize quality can differentiate themselves from competitors.
High-quality offerings can create competitive advantages, making it easier to attract and retain customers.
Key Differences Between Process Improvement and Quality Improvement
While both process improvement and quality improvement aim to enhance business performance, they focus on different areas.
Process improvement primarily targets the efficiency of operations.
It seeks to make business processes faster, cost-effective, and more streamlined.
In contrast, quality improvement centers on the product or service itself, ensuring it meets high quality standards.
Another distinction lies in their scopes.
Process improvement looks at the broader operation, whereas quality improvement often involves specific products or services.
Tools used in each approach can also differ.
Process improvement may use techniques like Lean for efficiency, while quality improvement might leverage Total Quality Management (TQM) principles or ISO standards focusing on quality.
Integration of Both Improvements
Although process and quality improvements differ, integrating both can have compounding effects.
When combined, organizations can build workflows that are not only efficient but also produce high-quality outputs.
For instance, a company may utilize process improvement to streamline its production line, thereby speeding up manufacturing.
Simultaneously, it can apply quality improvement techniques to ensure the items produced are of top-notch quality.
The result is a lean, efficient operation that also delivers excellent products, meeting or exceeding customer expectations.
Steps to Implement Improvements
Both process and quality improvements require systematic approaches for successful implementation.
For process improvement:
1. Identify a process to improve.
2. Map out the current process, noting each step.
3. Analyze the process for inefficiencies or redundancies.
4. Develop strategies to streamline the process.
5. Implement changes and monitor outcomes.
For quality improvement:
1. Collect and analyze customer feedback.
2. Identify products or services needing upgrades.
3. Develop improvement plans, possibly redesigning products.
4. Implement quality control measures.
5. Review and adjust strategies based on performance metrics.
Conclusion
Understanding the differences between process improvement and quality improvement is crucial for businesses aiming for excellence.
Both approaches offer unique benefits and, when implemented effectively, can complement each other to optimize business operations.
Organizations should not view these strategies in isolation.
Integrating process and quality improvements can lead to optimized performance, satisfied customers, and overall business success.
資料ダウンロード
QCD調達購買管理クラウド「newji」は、調達購買部門で必要なQCD管理全てを備えた、現場特化型兼クラウド型の今世紀最高の購買管理システムとなります。
ユーザー登録
調達購買業務の効率化だけでなく、システムを導入することで、コスト削減や製品・資材のステータス可視化のほか、属人化していた購買情報の共有化による内部不正防止や統制にも役立ちます。
NEWJI DX
製造業に特化したデジタルトランスフォーメーション(DX)の実現を目指す請負開発型のコンサルティングサービスです。AI、iPaaS、および先端の技術を駆使して、製造プロセスの効率化、業務効率化、チームワーク強化、コスト削減、品質向上を実現します。このサービスは、製造業の課題を深く理解し、それに対する最適なデジタルソリューションを提供することで、企業が持続的な成長とイノベーションを達成できるようサポートします。
オンライン講座
製造業、主に購買・調達部門にお勤めの方々に向けた情報を配信しております。
新任の方やベテランの方、管理職を対象とした幅広いコンテンツをご用意しております。
お問い合わせ
コストダウンが利益に直結する術だと理解していても、なかなか前に進めることができない状況。そんな時は、newjiのコストダウン自動化機能で大きく利益貢献しよう!
(Β版非公開)