- お役立ち記事
- Differences Between Quality Inspection and Reliability Testing
月間76,176名の
製造業ご担当者様が閲覧しています*
*2025年3月31日現在のGoogle Analyticsのデータより
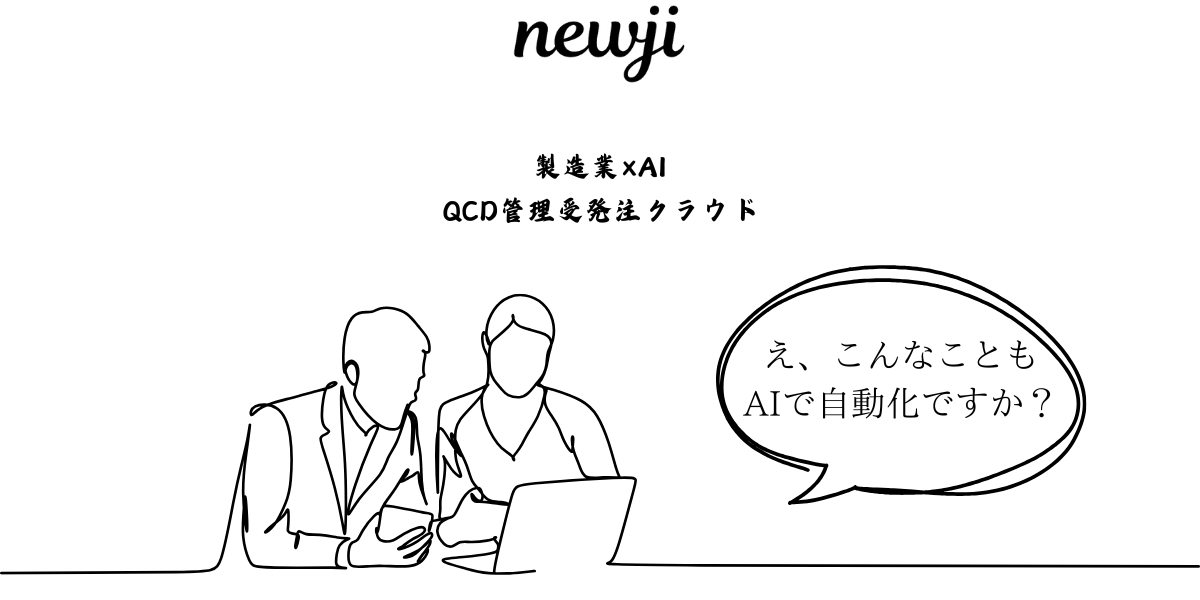
Differences Between Quality Inspection and Reliability Testing
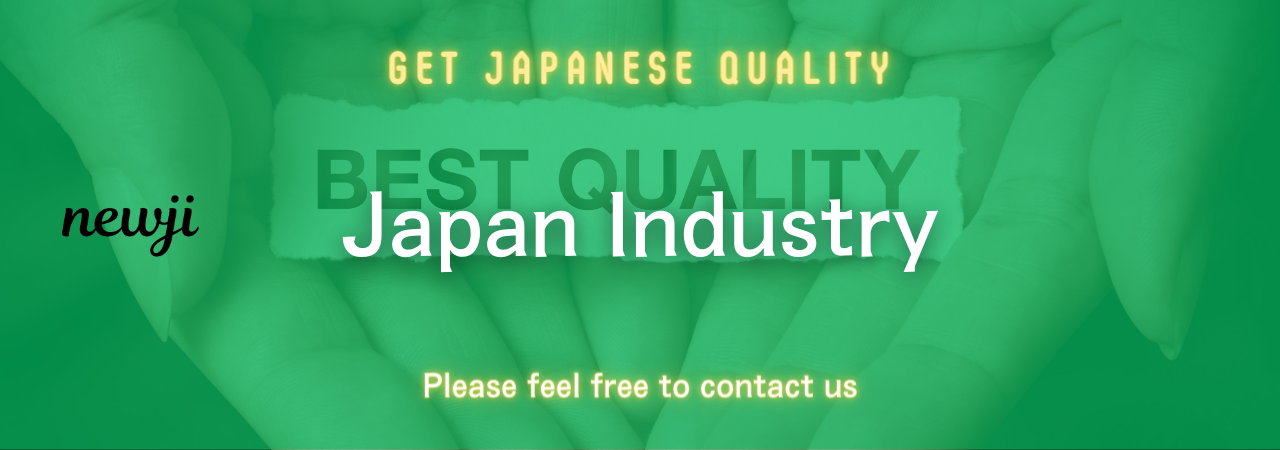
目次
Understanding Quality Inspection
Quality inspection is an essential part of the manufacturing process.
It ensures that products meet specific standards before they are delivered to customers.
This process involves examining a product to verify that it adheres to certain criteria, such as measurements, material quality, and functionality.
Manufacturers perform quality inspections to identify any defects or deviations from the desired standards.
Typically, quality inspection is performed at various stages of production.
This includes checking raw materials before they enter the production line and inspecting finished goods before shipping them out.
The main goal is to catch any issues early on, which helps in maintaining product quality and customer satisfaction.
Types of Quality Inspections
Quality inspections can be categorized into several types, each focusing on different aspects of the product.
**Pre-production Inspection** is performed before the manufacturing process starts.
It ensures that the raw materials and components meet the required standards.
**In-process Inspection**, on the other hand, occurs during the manufacturing process.
Inspectors check products at various stages to ensure consistency and to catch any defects early.
Finally, **Pre-shipment Inspection** occurs after the product is manufactured but before it is shipped to the customer.
This type of inspection verifies that the finished goods meet all the required specifications and quality standards.
Tools Used in Quality Inspection
Various tools and techniques are employed to conduct quality inspections.
**Visual Inspection** involves examining the product with the naked eye or with magnifying tools.
It’s one of the simplest methods but can be very effective in spotting obvious defects.
**Measuring Instruments** like calipers, micrometers, and gauges are used to verify dimensions and tolerances.
These tools help ensure that the product meets precise measurements.
**Non-destructive Testing (NDT)** methods, such as ultrasonic testing, radiographic testing, and magnetic particle inspection, help identify internal defects without damaging the product.
These techniques are particularly useful for detecting issues that are not visible to the naked eye.
Understanding Reliability Testing
While quality inspection focuses on identifying defects in individual products, reliability testing aims to determine how well a product will perform over time.
It assesses the product’s ability to function under various conditions and its likelihood of failure.
Reliability testing is crucial because it provides insights into the product’s lifespan and its performance in real-world scenarios.
Manufacturers use this data to improve the design and durability of their products.
Types of Reliability Testing
There are several types of reliability testing, each designed to assess different aspects of product performance.
**Life Testing** evaluates how long a product can operate before it fails.
It involves subjecting the product to normal operational conditions and monitoring its performance over time.
**Environmental Testing** examines how a product responds to different environmental conditions, such as extreme temperatures, humidity, and vibration.
This testing is essential for products that will be used in harsh environments.
**Stress Testing** subjects the product to conditions beyond its normal operational limits.
This helps identify the product’s breaking point and determines its robustness.
**Burn-in Testing** involves operating the product continuously for a specific period to identify early failures.
This testing helps ensure that only reliable products are delivered to customers.
Tools Used in Reliability Testing
Reliability testing utilizes various advanced tools and equipment to simulate real-world conditions.
**Accelerated Life Testing** uses environmental chambers to subject the product to extreme conditions and speeds up the aging process.
This helps predict the product’s lifespan in a shorter amount of time.
**Thermal Cycling Chambers** expose the product to rapid temperature changes, simulating conditions that may cause thermal stress.
**Vibration Test Systems** apply mechanical vibrations to the product to assess its durability under vibratory conditions.
Key Differences Between Quality Inspection and Reliability Testing
While both quality inspection and reliability testing aim to ensure high product standards, they differ in several key areas.
Focus and Objectives
Quality inspection focuses on identifying defects in individual products at various stages of production.
Its primary goal is to ensure that each product meets the specified criteria before it reaches the customer.
Reliability testing, on the other hand, assesses the product’s overall performance and durability over time.
It aims to predict the product’s lifespan and identify potential points of failure.
Timing in the Manufacturing Process
Quality inspection is performed throughout the manufacturing process, from pre-production to post-production stages.
It involves continuous monitoring to catch any defects early on.
Reliability testing is usually conducted after the product has been fully developed.
It focuses on long-term performance and is often part of the final validation process before a product is released to the market.
Methods and Tools
Quality inspection relies on visual examinations, measuring instruments, and non-destructive testing methods.
These tools help verify that the product meets specific standards and specifications.
Reliability testing uses advanced simulation and testing equipment to expose the product to various conditions.
It often involves stress, environmental, and life testing to assess the product’s durability.
Outcome and Action
The outcome of quality inspection is typically a pass or fail result based on the product meeting the required standards.
If a defect is found, corrective actions are taken immediately to address the issue.
In contrast, reliability testing provides data on the product’s performance over time.
This information is used to make improvements in product design and manufacturing processes.
Both quality inspection and reliability testing are vital for ensuring high product standards and customer satisfaction.
By understanding their differences and roles, manufacturers can create products that are not only defect-free but also reliable and durable in the long run.
資料ダウンロード
QCD管理受発注クラウド「newji」は、受発注部門で必要なQCD管理全てを備えた、現場特化型兼クラウド型の今世紀最高の受発注管理システムとなります。
ユーザー登録
受発注業務の効率化だけでなく、システムを導入することで、コスト削減や製品・資材のステータス可視化のほか、属人化していた受発注情報の共有化による内部不正防止や統制にも役立ちます。
NEWJI DX
製造業に特化したデジタルトランスフォーメーション(DX)の実現を目指す請負開発型のコンサルティングサービスです。AI、iPaaS、および先端の技術を駆使して、製造プロセスの効率化、業務効率化、チームワーク強化、コスト削減、品質向上を実現します。このサービスは、製造業の課題を深く理解し、それに対する最適なデジタルソリューションを提供することで、企業が持続的な成長とイノベーションを達成できるようサポートします。
製造業ニュース解説
製造業、主に購買・調達部門にお勤めの方々に向けた情報を配信しております。
新任の方やベテランの方、管理職を対象とした幅広いコンテンツをご用意しております。
お問い合わせ
コストダウンが利益に直結する術だと理解していても、なかなか前に進めることができない状況。そんな時は、newjiのコストダウン自動化機能で大きく利益貢献しよう!
(β版非公開)