- お役立ち記事
- Differences Between Thermal Spraying and Plating
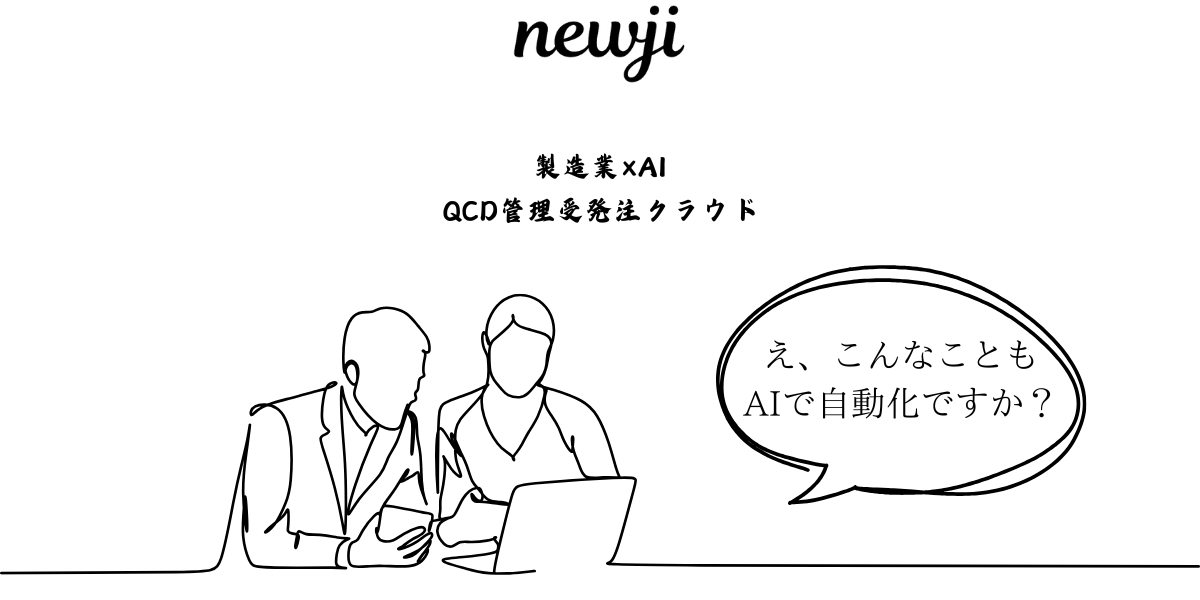
Differences Between Thermal Spraying and Plating
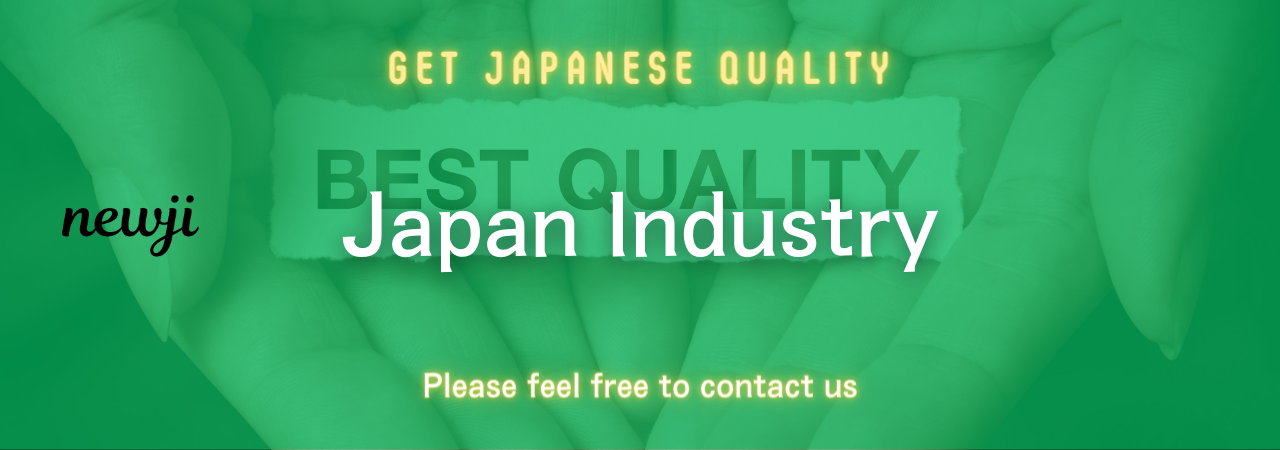
目次
Introduction to Surface Coating Techniques
In the world of material science and engineering, improving the surface properties of materials is crucial.
Two popular methods for enhancing surface performance are thermal spraying and plating.
Both processes aim to protect and enhance the endurance of substrates, but they have significant differences in their methods and outcomes.
This article explores these differences, highlighting the unique aspects of each technique.
What is Thermal Spraying?
Thermal spraying is a coating process used to apply materials onto a substrate to modify its surface properties.
In this process, the coating material is heated to a molten or semi-molten state and then projected onto the surface.
Various thermal spray processes exist, including plasma spraying, flame spraying, arc spraying, and high-velocity oxy-fuel (HVOF) spraying.
Each technique uses different energy sources, but the underlying principle remains the same—using high temperatures to melt the coating material.
Through thermal spraying, manufacturers can apply a wide range of coating materials, such as metals, ceramics, and polymers.
The coating is typically thick, offering excellent wear and corrosion resistance.
Understanding Plating
Plating, on the other hand, is a method of depositing material onto a substrate’s surface using electrochemical or electroless processes.
A common example of this is electroplating, where an electric current is used to reduce dissolved metal cations so that they form a coherent metal coating on an electrode.
Electroless plating relies on a chemical reaction rather than electricity.
Plating is often used to improve durability, corrosion resistance, and aesthetic appearance.
Unlike thermal spraying, plating usually results in thinner layers, with the coating materials typically limited to metals.
Common materials used in plating include nickel, chrome, gold, and silver.
Comparative Analysis: Process and Applications
Process Differences
The primary distinction between thermal spraying and plating is their application process.
Thermal spraying involves heating the coating material to a high temperature and projecting it onto the substrate, which allows for thicker coatings and the use of a broader range of materials.
In contrast, plating involves a chemical or electrochemical process to form a coating layer.
This results in thinner, more uniform coatings but is usually limited to metallic materials.
Material Versatility
Thermal spraying offers greater versatility in terms of materials.
It can apply metals, ceramics, and polymers, making it suitable for diverse applications, including protective coatings for turbines, aerospace components, and medical implants.
Plating is typically restricted to metallic deposits, such as nickel, gold, or chrome, catering more to applications requiring metallic finishing, like electronics and automotive parts.
Coating Thickness
The coating thickness is another key difference.
Thermal spray coatings tend to be thicker, often ranging from a few microns to several millimeters, providing excellent wear and corrosion resistance.
Plating, however, is better suited for applications requiring precise and thinner coatings, often in the range of microns.
Surface Preparation and Adhesion
Surface preparation is crucial for both methods.
Thermal spraying often requires the substrate to be grit-blasted to ensure good mechanical adhesion of the coating.
For plating, surface preparation involves cleaning and, in some cases, applying a pre-treatment layer to enhance adhesion.
While thermal spray coatings adhere via mechanical bonding, plating achieves adhesion through molecular or atomic interaction, resulting in stronger bonds.
Application Suitability
Industries and Uses
Thermal spraying and plating find applications across various industries due to their unique attributes.
Thermal spraying is ideal for situations requiring high-temperature resistance, such as coating turbine blades, boiler components, and engine parts.
Its ability to apply ceramic coatings makes it invaluable in environments exposed to extreme heat and wear.
Plating, with its metal-centric coatings, is extensively used in the automotive industry for decorative applications and corrosion resistance.
It is also crucial in the electronics industry, where thin and uniform metallic coatings are necessary for conductivity and durability.
Customization and Aesthetics
Plating excels where aesthetic value is critical, offering options like gold or chrome finishes for a shiny appearance.
Customization in plating generally revolves around the choice of metal and thickness, catering to specific electrical or aesthetic needs.
Thermal spraying focuses on functional attributes like wear resistance and heat protection rather than appearance.
Environmental and Economic Considerations
Environmental Impact
The environmental impact of both methods should be considered.
Thermal spraying processes can produce overspray and dust, necessitating effective control measures to minimize environmental pollution.
Plating involves the use of chemicals, which require careful handling and disposal to prevent environmental contamination.
Cost Implications
Cost considerations can also influence the choice between thermal spraying and plating.
Thermal spraying might be costlier due to the equipment and material costs, but it can offer long-term savings through durability and reduced maintenance.
Plating typically involves lower upfront costs but might require more frequent replacements due to thinner coatings.
Conclusion: Choosing the Right Method
In conclusion, both thermal spraying and plating offer unique advantages and are suited for different applications.
The decision between the two depends on factors like application requirements, material compatibility, desired coating thickness, and budget constraints.
Understanding these differences aids in selecting the most appropriate method for enhancing the surface properties of materials, ensuring optimal performance and longevity.
資料ダウンロード
QCD調達購買管理クラウド「newji」は、調達購買部門で必要なQCD管理全てを備えた、現場特化型兼クラウド型の今世紀最高の購買管理システムとなります。
ユーザー登録
調達購買業務の効率化だけでなく、システムを導入することで、コスト削減や製品・資材のステータス可視化のほか、属人化していた購買情報の共有化による内部不正防止や統制にも役立ちます。
NEWJI DX
製造業に特化したデジタルトランスフォーメーション(DX)の実現を目指す請負開発型のコンサルティングサービスです。AI、iPaaS、および先端の技術を駆使して、製造プロセスの効率化、業務効率化、チームワーク強化、コスト削減、品質向上を実現します。このサービスは、製造業の課題を深く理解し、それに対する最適なデジタルソリューションを提供することで、企業が持続的な成長とイノベーションを達成できるようサポートします。
オンライン講座
製造業、主に購買・調達部門にお勤めの方々に向けた情報を配信しております。
新任の方やベテランの方、管理職を対象とした幅広いコンテンツをご用意しております。
お問い合わせ
コストダウンが利益に直結する術だと理解していても、なかなか前に進めることができない状況。そんな時は、newjiのコストダウン自動化機能で大きく利益貢献しよう!
(Β版非公開)