- お役立ち記事
- Differences Between Yield Improvement and Defect Reduction
Differences Between Yield Improvement and Defect Reduction
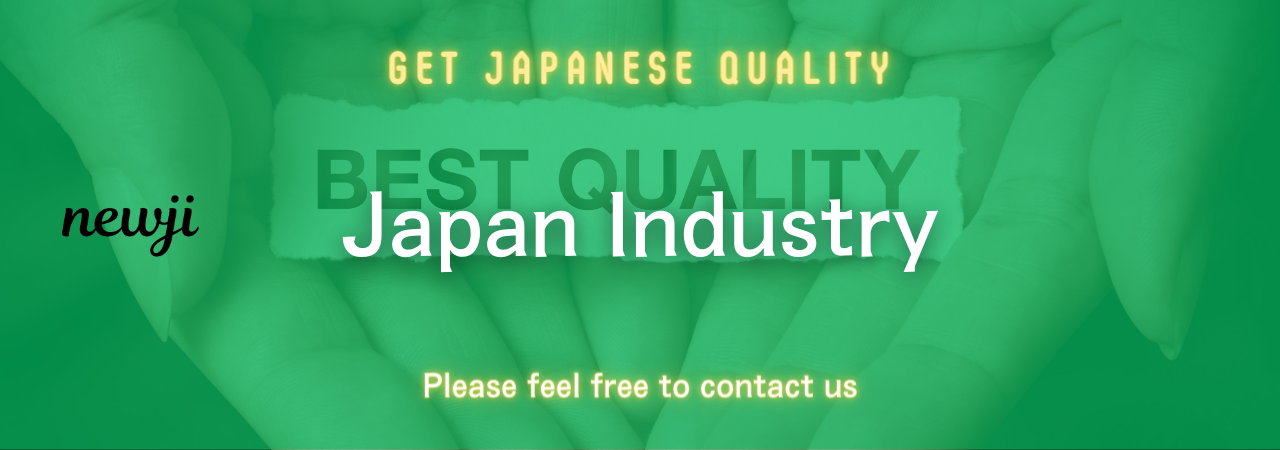
目次
Understanding Yield Improvement
Yield improvement is an essential concept in manufacturing and production processes.
It refers to the process of increasing the number of good units produced without defects or flaws.
The ultimate goal is to maximize the production output by minimizing waste and optimizing processes.
In yield improvement, the focus is on enhancing the efficiency of the production process.
This can involve upgrading machinery, optimizing workflows, and training personnel to perform their tasks more effectively.
By improving yield, companies can produce more products with the same amount of resources, thereby increasing profitability.
Techniques for Yield Improvement
Several techniques are commonly used to achieve yield improvement.
One approach is process optimization, where companies analyze every step of the manufacturing process to identify bottlenecks and inefficiencies.
Another technique involves material management.
Using higher quality raw materials and ensuring consistent supply can significantly contribute to yield improvement.
Furthermore, technology integration can play a crucial role.
The use of advanced technologies like AI and IoT can result in better real-time monitoring and control of processes, ensuring optimal performance.
Benefits of Yield Improvement
Yield improvement brings multiple benefits to the table.
Firstly, it enables companies to increase their production capacity without investing in additional resources.
Secondly, it can lead to significant cost savings.
By reducing waste and optimizing resource use, companies can lower their operational costs.
Lastly, yield improvement enhances product quality.
With fewer defects and higher consistency, companies can ensure that their products meet customer expectations and regulatory standards.
Exploring Defect Reduction
While yield improvement focuses on overall production efficiency, defect reduction specifically targets minimizing the number of defective products.
This is critical because defects can lead to increased costs, customer dissatisfaction, and brand tarnishment.
Defect reduction involves identifying and eliminating the root causes of defects in the production process.
It aims to ensure that each product meets the required quality standards before reaching the customer.
Strategies for Defect Reduction
There are various strategies employed for defect reduction.
Quality control methods such as Six Sigma and Total Quality Management (TQM) are prevalent.
These methods emphasize a rigorous approach to measuring and improving product quality.
Another effective strategy is regular maintenance and calibration of machinery.
Ensuring that equipment operates at optimal conditions can prevent faults that lead to defects.
Employee training is also crucial.
By educating workers about quality standards and defect recognition, companies can better ensure that production teams are adept at spotting and addressing quality issues early in the process.
Advantages of Defect Reduction
Reducing defects in production offers substantial benefits.
Primarily, it leads to improved customer satisfaction, as customers receive products that fulfill their expectations.
Additionally, it reduces costs associated with returns and repairs.
By minimizing defects, companies save on expenses related to rectifying product issues after they have been manufactured.
Moreover, a lower defect rate enhances the company’s reputation.
Consistently producing high-quality products solidifies trust and brand loyalty among consumers.
Key Differences Between Yield Improvement and Defect Reduction
While yield improvement and defect reduction are interconnected, they have distinct focuses.
Yield improvement concentrates on increasing the proportion of non-defective units in the total production, whereas defect reduction focuses on decreasing the occurrence of defective units themselves.
In essence, yield improvement is a broader endeavor, aiming to elevate the entire production system.
Meanwhile, defect reduction zeroes in on the specific aspect of product quality.
It’s important to note that both concepts can overlap.
Enhancing yield often involves reducing defects, as fewer defective units can lead to higher yield percentages.
Conversely, by addressing defects, companies can indirectly contribute to yield improvement by ensuring that more products meet the criteria of being ‘good’.
Achieving a Balance
In practice, striking a balance between yield improvement and defect reduction is essential for optimal production performance.
Focusing too heavily on one aspect may neglect vital improvements in the other.
Manufacturers need to implement an integrated approach that blends efforts across both dimensions.
This involves continuous monitoring, analysis, and adjustment of processes to ensure both high yields and low defect rates.
Leveraging data-driven insights and technological advancements can facilitate this balance.
By systematically implementing improvements and monitoring their impacts, companies can innovate their processes while maintaining quality standards.
Ultimately, understanding and addressing both yield improvement and defect reduction is crucial for any manufacturing process striving for excellence.
By combining efforts, businesses can achieve cost efficiency, customer satisfaction, and market competitiveness.
資料ダウンロード
QCD調達購買管理クラウド「newji」は、調達購買部門で必要なQCD管理全てを備えた、現場特化型兼クラウド型の今世紀最高の購買管理システムとなります。
ユーザー登録
調達購買業務の効率化だけでなく、システムを導入することで、コスト削減や製品・資材のステータス可視化のほか、属人化していた購買情報の共有化による内部不正防止や統制にも役立ちます。
NEWJI DX
製造業に特化したデジタルトランスフォーメーション(DX)の実現を目指す請負開発型のコンサルティングサービスです。AI、iPaaS、および先端の技術を駆使して、製造プロセスの効率化、業務効率化、チームワーク強化、コスト削減、品質向上を実現します。このサービスは、製造業の課題を深く理解し、それに対する最適なデジタルソリューションを提供することで、企業が持続的な成長とイノベーションを達成できるようサポートします。
オンライン講座
製造業、主に購買・調達部門にお勤めの方々に向けた情報を配信しております。
新任の方やベテランの方、管理職を対象とした幅広いコンテンツをご用意しております。
お問い合わせ
コストダウンが利益に直結する術だと理解していても、なかなか前に進めることができない状況。そんな時は、newjiのコストダウン自動化機能で大きく利益貢献しよう!
(Β版非公開)