- お役立ち記事
- Differences in flow properties in injection molding of polypropylene and polycarbonate
月間77,185名の
製造業ご担当者様が閲覧しています*
*2025年2月28日現在のGoogle Analyticsのデータより
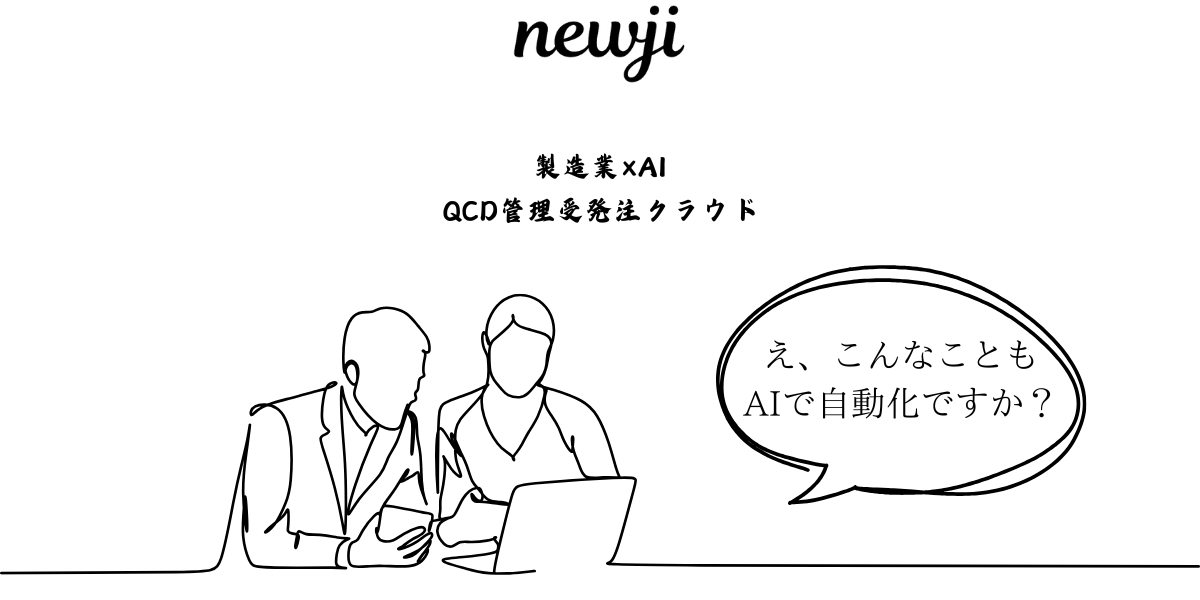
Differences in flow properties in injection molding of polypropylene and polycarbonate
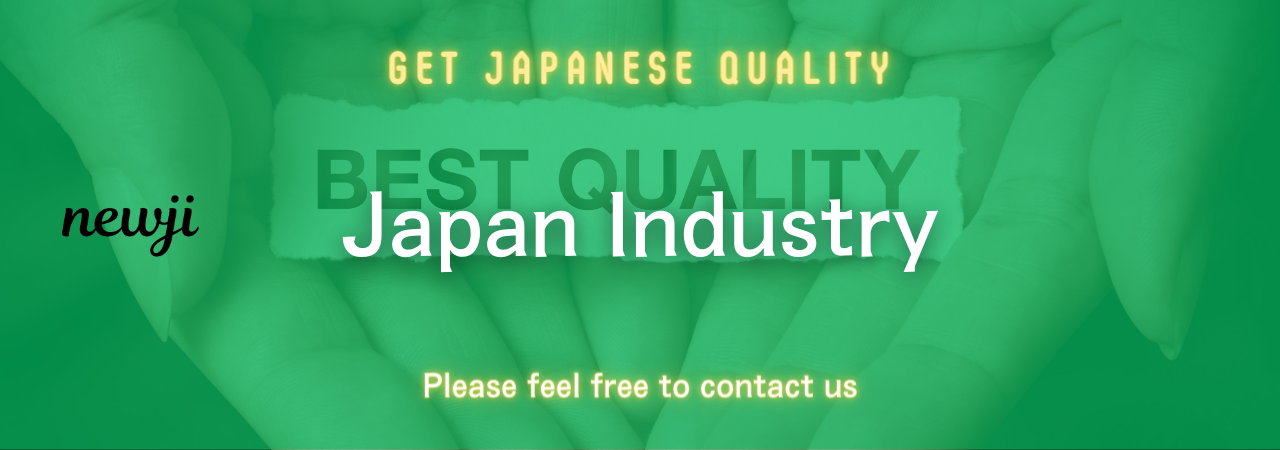
目次
Introduction to Injection Molding
Injection molding is a popular manufacturing process used to create a wide variety of plastic parts and products.
It’s known for its efficiency in producing high volumes of complex shapes with precision.
In injection molding, plastic materials, such as polypropylene and polycarbonate, are melted and then injected into a mold.
Once cooled, they take the shape of the mold to form the final product.
Polypropylene vs. Polycarbonate
Polypropylene and polycarbonate are two of the most commonly used plastics in the injection molding industry.
Understanding their flow properties is essential for manufacturers to achieve optimal results.
Both materials have unique characteristics that affect how they perform in the injection molding process.
Polypropylene
Polypropylene (PP) is a thermoplastic polymer known for its versatility and affordability.
It has a wide range of applications from packaging and labeling to automotive and consumer products.
The flow properties of polypropylene are generally favorable in injection molding, making it a preferred choice for many manufacturers.
1. **Low Melt Viscosity**: Polypropylene has a lower melt viscosity compared to many other plastics, allowing it to flow easily into the mold.
This property helps in filling complex molds quickly and efficiently.
2. **Wide Processing Window**: The material can be processed at a variety of temperatures and conditions, offering flexibility in designing the injection molding process.
3. **Good Impact Resistance**: Despite its ease of flow, polypropylene offers decent impact resistance, making it suitable for durable products.
However, polypropylene’s relatively low melting point can pose challenges when products are subjected to high temperatures.
Polycarbonate
Polycarbonate (PC) is another thermoplastic polymer known for its strength and transparency.
It is extensively used in applications that require high impact resistance and visibility, such as optical discs and protective gear.
1. **Higher Melt Viscosity**: Polycarbonate has a higher melt viscosity than polypropylene, which means it does not flow as easily into molds.
This can be a disadvantage in terms of energy consumption and processing time.
2. **Excellent Impact and Heat Resistance**: Despite its higher processing difficulties, polycarbonate excels in impact and thermal resistance, making it ideal for high-performance applications.
3. **Optical Clarity**: The transparency of polycarbonate is a significant advantage for applications where clarity is essential.
Due to these properties, polycarbonate is often used in applications where strength, durability, and clarity are required despite the additional processing efforts it may require.
Key Differences in Flow Properties
The flow properties of polypropylene and polycarbonate significantly influence their behavior during injection molding.
Understanding these differences is crucial for manufacturers aiming to optimize their production processes.
Viscosity and Melt Flow Index
The melt flow index (MFI) is a key indicator of a material’s flow behavior during the injection molding process.
– **Polypropylene** generally has a higher MFI, indicating a lower viscosity, which simplifies the molding process.
This allows for easier filling of molds without the need for excessive pressure.
– **Polycarbonate** has a lower MFI, suggesting a thicker melt and requiring higher pressures for adequate mold filling.
While this can lead to longer cycle times and higher energy consumption, it is necessary for achieving the material’s desirable properties.
Processing Temperature
Processing temperatures also vary significantly between these two materials.
– **Polypropylene’s processing temperature** is comparatively lower, typically ranging from 180°C to 240°C.
– **Polycarbonate**, on the other hand, requires higher processing temperatures, generally between 250°C and 300°C, which can affect energy costs and equipment wear.
Challenges in Mold Design
The differences in flow properties also present unique challenges in mold design.
– For **polypropylene**, the lower viscosity allows for more freedom in designing intricate and complex shapes with minimal risk of defects.
– With **polycarbonate**, the mold design needs to account for the higher viscosity by incorporating features that facilitate filling, such as venting and strategically placed gates.
Conclusion
Understanding the differences in flow properties between polypropylene and polycarbonate is critical for optimizing the injection molding process.
While polypropylene offers ease of processing with its low viscosity and wide processing window, polycarbonate provides superior strength and clarity, albeit with more demanding processing requirements.
Manufacturers must consider these properties carefully when choosing between these materials for injection molding projects.
By aligning the material choice with the desired product characteristics and processing capabilities, it’s possible to achieve efficient production and high-quality products.
In doing so, manufacturers can leverage the unique advantages of each material to meet diverse industry needs, from consumer goods to industrial applications.
資料ダウンロード
QCD管理受発注クラウド「newji」は、受発注部門で必要なQCD管理全てを備えた、現場特化型兼クラウド型の今世紀最高の受発注管理システムとなります。
ユーザー登録
受発注業務の効率化だけでなく、システムを導入することで、コスト削減や製品・資材のステータス可視化のほか、属人化していた受発注情報の共有化による内部不正防止や統制にも役立ちます。
NEWJI DX
製造業に特化したデジタルトランスフォーメーション(DX)の実現を目指す請負開発型のコンサルティングサービスです。AI、iPaaS、および先端の技術を駆使して、製造プロセスの効率化、業務効率化、チームワーク強化、コスト削減、品質向上を実現します。このサービスは、製造業の課題を深く理解し、それに対する最適なデジタルソリューションを提供することで、企業が持続的な成長とイノベーションを達成できるようサポートします。
製造業ニュース解説
製造業、主に購買・調達部門にお勤めの方々に向けた情報を配信しております。
新任の方やベテランの方、管理職を対象とした幅広いコンテンツをご用意しております。
お問い合わせ
コストダウンが利益に直結する術だと理解していても、なかなか前に進めることができない状況。そんな時は、newjiのコストダウン自動化機能で大きく利益貢献しよう!
(β版非公開)