- お役立ち記事
- Digital Alarm Clock Manufacturing Process and Alarm Accuracy Improvement
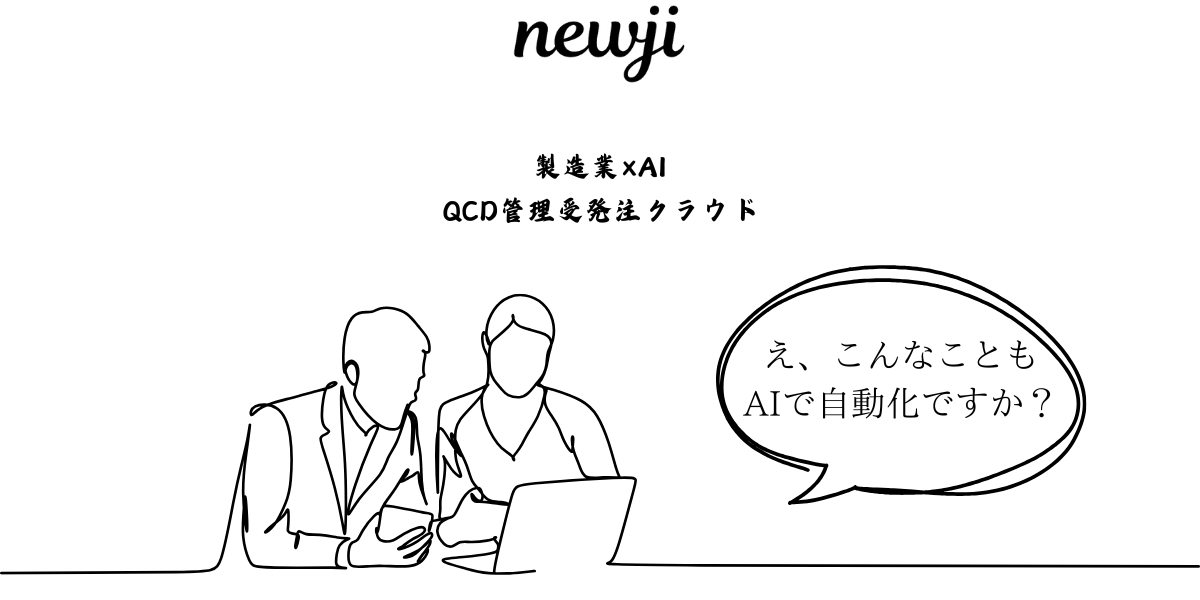
Digital Alarm Clock Manufacturing Process and Alarm Accuracy Improvement
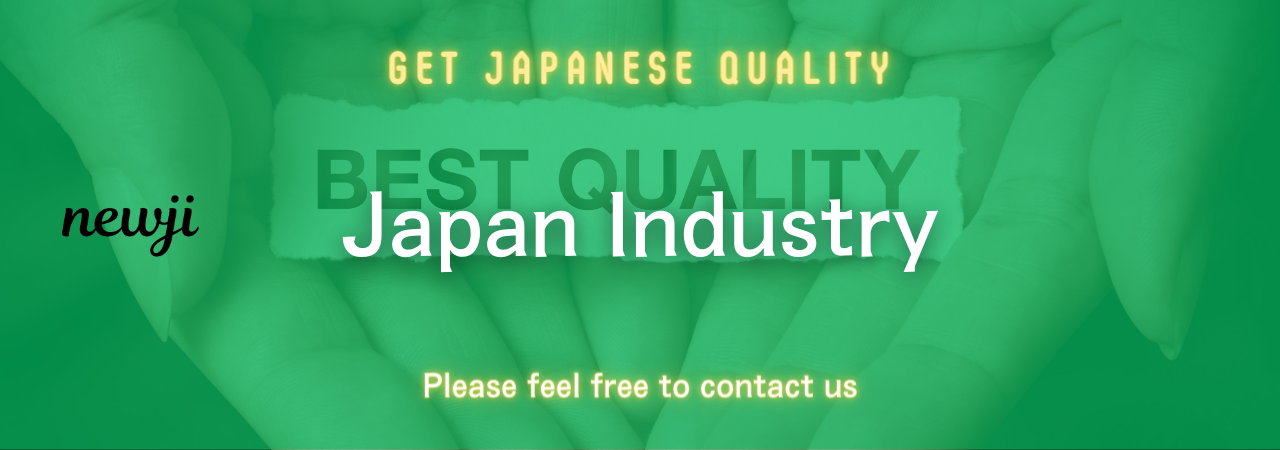
目次
Understanding the Digital Alarm Clock Manufacturing Process
The digital alarm clock is a common household item that blends technology and functionality into a small device that helps us wake up on time each morning.
Understanding the manufacturing process of digital alarm clocks sheds light on how these innovative devices come to life.
From design to assembly, each step is crucial in creating a reliable product that accurately serves its purpose.
Design and Conceptualization
The journey of a digital alarm clock starts with design and conceptualization.
Engineers and designers collaborate to develop a blueprint that defines the clock’s functions, appearance, and features.
They consider various factors such as size, display type, and user interface to ensure the clock is both functional and easy to use.
Designers often create a prototype to test the concept before production begins.
This phase is crucial for ironing out any potential issues with the design and making adjustments to meet consumer needs and market demands.
Component Sourcing and Procurement
Once the design is finalized, the next step is sourcing and procuring the necessary components.
Digital alarm clocks require a variety of parts including circuits, displays, buttons, casings, and speakers.
Manufacturers work with suppliers to obtain high-quality materials that will ensure the durability and longevity of the clocks.
Sourcing reliable components is essential for maintaining the quality and performance of digital alarm clocks.
Manufacturers often have strict quality control measures in place to ensure that each part meets the required standards.
Assembly Line Production
With the components ready, the assembly line production begins.
Assembly lines are meticulously organized to efficiently combine various parts into a finished product.
Employees at different stations perform specific tasks such as soldering circuit boards, mounting displays, and enclosing the components in their housing.
Automated machines may also be used in certain stages to ensure precision and speed up the production process.
Quality control checks are conducted throughout the assembly line to identify and rectify any defects or errors.
This ensures that only well-functioning products proceed to the final stages of production.
Software Integration and Testing
Digital alarm clocks run on software that controls functions such as time display, alarms, and additional features like radio or weather updates.
Integrating this software into the hardware is a critical phase.
Technicians load the software onto the devices and test them to ensure everything operates smoothly.
During testing, each clock is checked for accuracy in timekeeping and alarm functions.
Engineers may simulate different scenarios to verify that the device will respond correctly under various conditions.
This ensures that consumers receive a product that not only looks good but works flawlessly.
Packaging and Distribution
Once the digital alarm clocks pass all quality tests, they are ready to be packaged for distribution.
Packaging is designed to protect the device during transit and provide customers with essential information about its features and usage.
Manufacturers often focus on eco-friendly packaging options to minimize environmental impact.
Warehouses are used to store the finished clocks until they are shipped to retailers or directly to consumers.
Efficient logistics systems are employed to ensure timely delivery to various locations around the world.
Improving the Accuracy of Alarms
Alarm accuracy is a vital aspect of any digital alarm clock.
A device that is off by even a few minutes can disrupt daily routines.
Fortunately, there are several ways manufacturers enhance the precision of alarms in digital clocks.
Utilizing High-Quality Components
One of the most effective methods for improving alarm accuracy is using high-quality components.
Precise circuits, sensors, and oscillators play a significant role in maintaining time accuracy.
Working with reputable suppliers ensures that the best materials are used, reducing the margin for error in timekeeping.
Employing Advanced Software Algorithms
Sophisticated software algorithms help digital alarm clocks maintain accurate time.
These algorithms account for factors that could affect timekeeping, such as temperature variations or power fluctuations.
By continuously adjusting the clock’s internal mechanisms, the software ensures that the alarm remains on schedule.
Regular software updates further enhance the clock’s capabilities, allowing it to adapt to changes and improve performance over time.
Conducting Rigorous Testing
Rigorous testing is vital for ensuring alarm accuracy.
Manufacturers simulate various environmental conditions to see how the clock performs under different circumstances.
This process identifies potential issues that could affect timekeeping and allows engineers to make necessary adjustments.
Through testing, alarm clocks are fine-tuned to deliver precise and reliable performance, giving users confidence in the product.
User Feedback and Continuous Improvement
Listening to user feedback is an important aspect of improving alarm accuracy.
Consumers often provide valuable insights into how the clock performs in real-world settings.
Manufacturers use this feedback to make improvements and produce a better product.
Continuous improvement is an ongoing process that involves analyzing user experience and evolving the design and technology to meet changing needs.
By prioritizing constant enhancement, manufacturers ensure that digital alarm clocks remain efficient and dependable for consumers worldwide.
Understanding the journey of digital alarm clocks from conception to creation, along with the methods used to improve alarm accuracy, highlights the intricate work that goes into producing these reliable devices.
With consistent innovation and dedication to quality, digital alarm clocks continue to be essential tools in households around the globe.
資料ダウンロード
QCD調達購買管理クラウド「newji」は、調達購買部門で必要なQCD管理全てを備えた、現場特化型兼クラウド型の今世紀最高の購買管理システムとなります。
ユーザー登録
調達購買業務の効率化だけでなく、システムを導入することで、コスト削減や製品・資材のステータス可視化のほか、属人化していた購買情報の共有化による内部不正防止や統制にも役立ちます。
NEWJI DX
製造業に特化したデジタルトランスフォーメーション(DX)の実現を目指す請負開発型のコンサルティングサービスです。AI、iPaaS、および先端の技術を駆使して、製造プロセスの効率化、業務効率化、チームワーク強化、コスト削減、品質向上を実現します。このサービスは、製造業の課題を深く理解し、それに対する最適なデジタルソリューションを提供することで、企業が持続的な成長とイノベーションを達成できるようサポートします。
オンライン講座
製造業、主に購買・調達部門にお勤めの方々に向けた情報を配信しております。
新任の方やベテランの方、管理職を対象とした幅広いコンテンツをご用意しております。
お問い合わせ
コストダウンが利益に直結する術だと理解していても、なかなか前に進めることができない状況。そんな時は、newjiのコストダウン自動化機能で大きく利益貢献しよう!
(Β版非公開)