- お役立ち記事
- Digital Engineering Benefits in Manufacturing
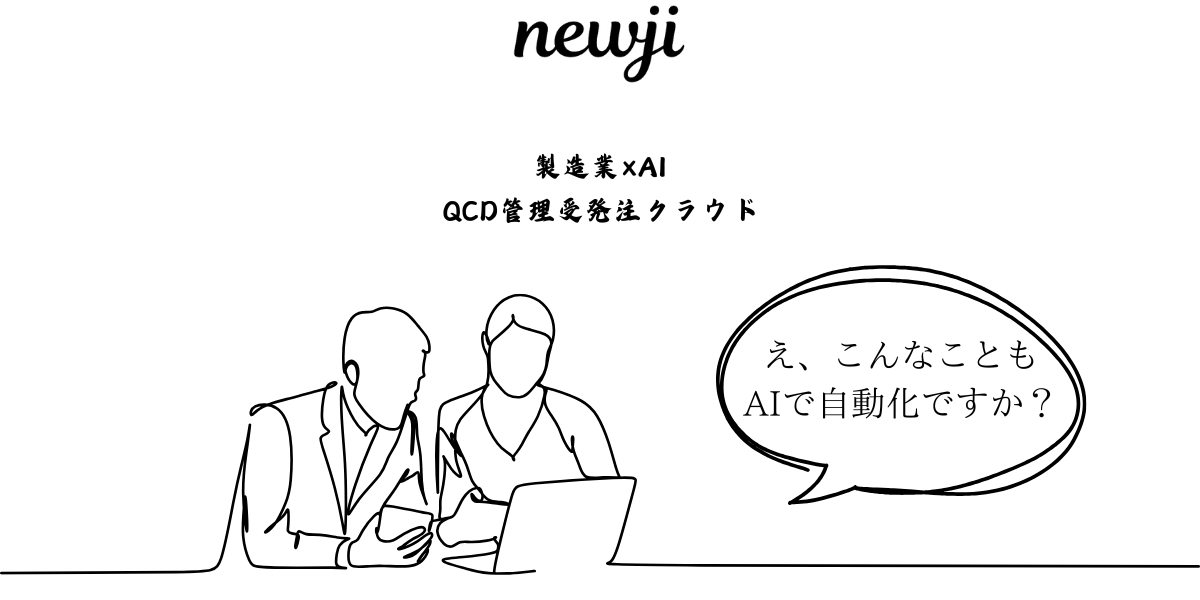
Digital Engineering Benefits in Manufacturing
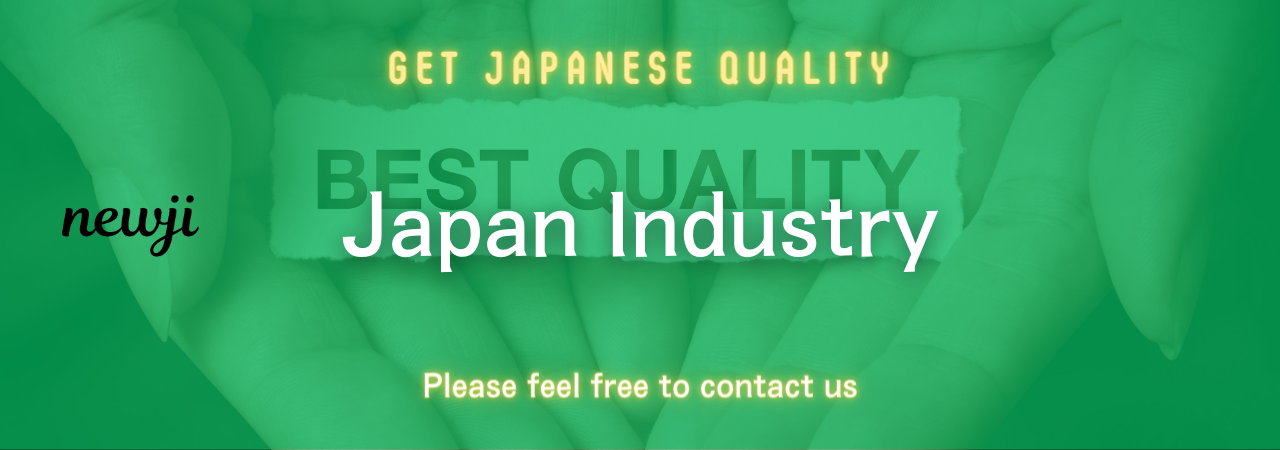
目次
Understanding Digital Engineering
Digital engineering is a transformative approach that leverages computer-based models, simulations, and various digital tools to optimize manufacturing processes.
Traditionally, engineering relied heavily on physical prototypes and manual calculations to design and manufacture products.
With digital engineering, manufacturers can visualize and analyze systems and components in a virtual space.
This new method allows engineers to identify potential issues, optimize designs, and streamline production, all before any physical models are created.
The Shift From Traditional to Digital Processes
In the past, manufacturing often involved linear processes with limited flexibility.
Engineers would create physical prototypes, undergo testing, and make necessary adjustments based on those tests.
This process was time-consuming and costly.
Digital engineering changes the dynamics by integrating advanced technologies such as computer-aided design (CAD), augmented reality (AR), and simulation software into the manufacturing process.
These tools allow for more sophisticated designs and faster implementation of solutions.
Faster Prototyping and Testing
One of the most significant benefits of digital engineering is the ability to rapidly prototype and test designs.
Engineers can create detailed virtual models and simulate real-world conditions to test these models.
This approach reduces the time and resources spent on creating physical prototypes.
It also enables quicker iterations and modifications, allowing for more innovative and efficient design solutions.
Efficiency Gains and Cost Reductions
Digital engineering streamlines manufacturing processes, leading to significant efficiency gains.
The use of digital models means that processes can be optimized before they are implemented on the production floor.
This leads to a reduction in material waste, energy consumption, and production time.
When errors are identified and rectified in the virtual space, it prevents costly mistakes during actual production.
Overall, this translates into substantial cost savings for manufacturers.
Improved Quality and Precision
Digital engineering facilitates enhanced precision in the design and manufacturing processes.
Through detailed simulations and analysis, engineers can identify and correct flaws before production begins.
This leads to higher-quality products with fewer defects.
Precision is further enhanced with technologies such as 3D printing, where digital precision directly translates into perfect physical counterparts.
Innovation and Design Flexibility
Another advantage of digital engineering is the surge in innovation it encourages.
With digital tools, designers have more creative freedom and flexibility.
They can easily explore various design possibilities without the need to commit resources to physical prototypes.
This freedom accelerates innovation cycles, bringing new ideas and products to market quicker than ever before.
Collaboration and Communication
Digital engineering opens new avenues for collaboration among teams and across different regions.
Engineers, designers, and stakeholders can share and work on digital models in real-time, regardless of their physical location.
This fosters better communication, alignment, and quicker decision-making, leading to more coherent and unified product development.
Sustainability and Environmental Impact
In modern manufacturing, sustainability is more crucial than ever.
Digital engineering contributes to more environmentally friendly manufacturing processes.
By reducing material waste and energy consumption, companies lower their carbon footprints.
Furthermore, digital simulations allow for the development of more sustainable product designs, with optimized materials and processes that factor in environmental considerations.
Adaptation to Market Changes
The market landscape is constantly evolving, demanding agility from manufacturers.
Digital engineering allows companies to quickly adapt to these changes.
Whether it’s modifying product features based on consumer feedback or scaling up production to meet demand, digital tools make these transitions smoother and quicker.
Conclusion
Digital engineering is transforming the manufacturing industry, offering unprecedented benefits in terms of efficiency, innovation, and sustainability.
By leveraging digital models and simulations, manufacturers can significantly reduce costs and optimize their processes.
The enhancements in design precision, quality, and collaboration further amplify the potential of digital engineering.
As companies continue to integrate these digital tools and methodologies, the future of manufacturing looks promising, with more sustainable, innovative, and efficient production lines.
資料ダウンロード
QCD調達購買管理クラウド「newji」は、調達購買部門で必要なQCD管理全てを備えた、現場特化型兼クラウド型の今世紀最高の購買管理システムとなります。
ユーザー登録
調達購買業務の効率化だけでなく、システムを導入することで、コスト削減や製品・資材のステータス可視化のほか、属人化していた購買情報の共有化による内部不正防止や統制にも役立ちます。
NEWJI DX
製造業に特化したデジタルトランスフォーメーション(DX)の実現を目指す請負開発型のコンサルティングサービスです。AI、iPaaS、および先端の技術を駆使して、製造プロセスの効率化、業務効率化、チームワーク強化、コスト削減、品質向上を実現します。このサービスは、製造業の課題を深く理解し、それに対する最適なデジタルソリューションを提供することで、企業が持続的な成長とイノベーションを達成できるようサポートします。
オンライン講座
製造業、主に購買・調達部門にお勤めの方々に向けた情報を配信しております。
新任の方やベテランの方、管理職を対象とした幅広いコンテンツをご用意しております。
お問い合わせ
コストダウンが利益に直結する術だと理解していても、なかなか前に進めることができない状況。そんな時は、newjiのコストダウン自動化機能で大きく利益貢献しよう!
(Β版非公開)