- お役立ち記事
- Digital Partnerships Shaping the Future of Manufacturing
月間76,176名の
製造業ご担当者様が閲覧しています*
*2025年3月31日現在のGoogle Analyticsのデータより
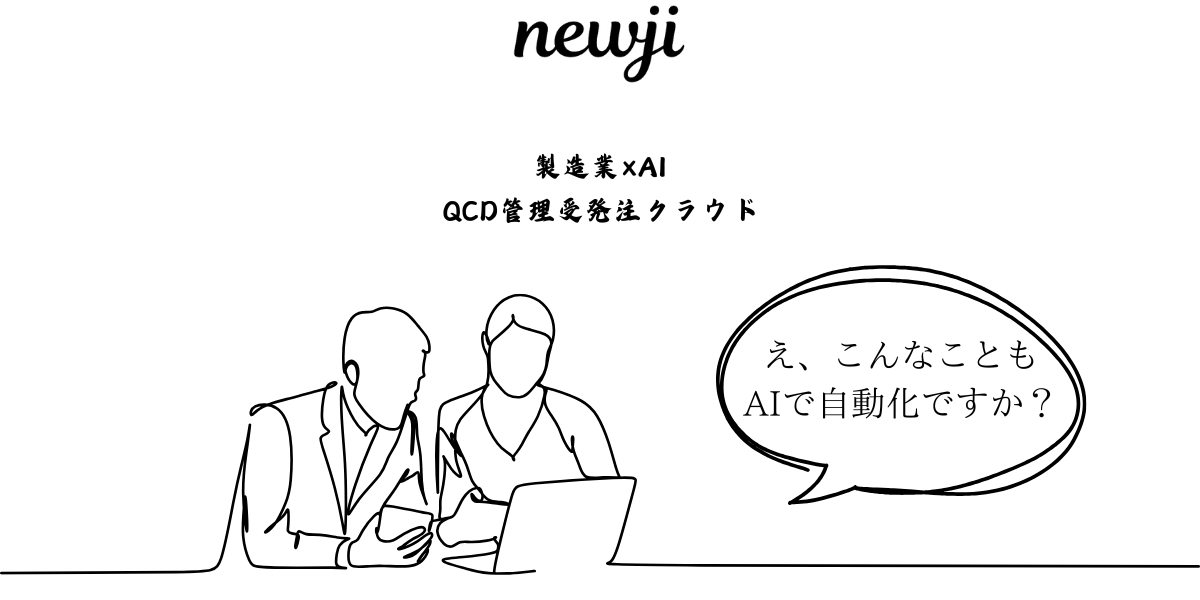
Digital Partnerships Shaping the Future of Manufacturing
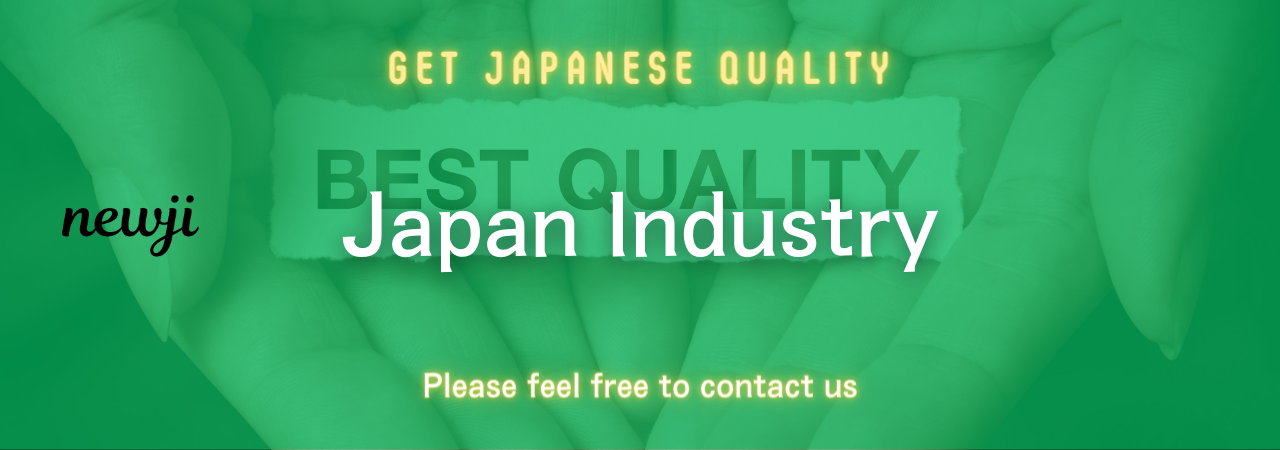
In today’s ever-evolving world, the face of manufacturing is undergoing a monumental transformation.
With the advent of cutting-edge technologies and innovative partnerships, the manufacturing industry is poised for a future that was once the stuff of science fiction.
These digital partnerships are more than mere collaborations; they represent a strategic union that is reshaping how products are designed, produced, and delivered.
目次
The New Age of Digital Manufacturing
The traditional manufacturing model, once heavily reliant on human labor and manual processes, is now being revolutionized by digital technologies.
From 3D printing to automation and the Internet of Things (IoT), the landscape has shifted dramatically.
Digital partnerships play a crucial role in this transformation by bringing together diverse expertise and technological advancements.
These partnerships often involve technology companies, manufacturers, and even educational institutions working collaboratively to develop state-of-the-art solutions.
For instance, imagine a scenario where a leading tech company teams up with a car manufacturer to create smarter, more efficient vehicles through IoT integration.
Such partnerships ensure that manufacturing processes are not only optimized but also sustainable and forward-thinking.
The Role of Data in Modern Manufacturing
One of the cornerstones of digital partnerships in manufacturing is data.
Today, data is more than just numbers and statistics; it is an invaluable asset that can drive decision-making and innovation.
When manufacturing entities collaborate with tech companies, they gain access to sophisticated analytical tools and platforms capable of processing massive datasets.
These tools help manufacturers monitor equipment performance, predict maintenance needs, and even foresee potential production issues.
Moreover, data-sharing between partners enables a more cohesive approach to product development.
By examining customer feedback, manufacturing defects, and market trends, companies can make informed decisions that enhance product quality and customer satisfaction.
In essence, data-driven insights lead to superior products and processes, benefiting both manufacturers and consumers alike.
Smart Factories: The Future is Now
Smart factories are a prime example of how digital partnerships are reshaping the manufacturing world.
A smart factory integrates digital technologies such as artificial intelligence (AI), IoT, and robotics to create a self-optimizing production environment.
These factories can adapt to changes in real-time, significantly improving efficiency and reducing downtime.
Imagine a factory where robots communicate with each other and human operators through a centralized system, ensuring seamless coordination.
When a machine identifies a potential fault, AI algorithms can suggest optimal solutions or even autonomously initiate corrective actions.
Such advancements are only possible through collaborative efforts between various stakeholders, including tech companies, equipment manufacturers, and industry experts.
Artificial Intelligence: The Game Changer
Artificial intelligence is a pivotal element in the evolution of smart factories.
AI-powered systems can analyze vast amounts of data swiftly, identifying patterns and trends that human operators might miss.
For instance, predictive maintenance is one area where AI shines.
By continuously monitoring machinery, AI systems can predict when components are likely to fail, allowing for timely maintenance and reducing unplanned outages.
Furthermore, AI can enhance quality control processes.
Through machine learning algorithms, AI can detect defects in products with remarkable accuracy, even at high speeds.
IoT and Connectivity
The Internet of Things (IoT) is another critical player in the realm of smart factories.
IoT devices embedded in machinery and production lines collect and share data across the network, providing real-time visibility into the manufacturing process.
This interconnectedness facilitates better coordination between different parts of the production line, leading to smoother operations.
IoT-driven predictive analytics also play a crucial role in supply chain management, ensuring timely delivery of raw materials and finished products.
The Human Element in Digital Manufacturing
While technology and data are driving forces behind modern manufacturing, the human element remains irreplaceable.
Digital partnerships must prioritize upskilling the workforce to effectively harness new technologies.
Training programs and workshops can equip employees with the necessary skills to operate and maintain advanced machinery.
Moreover, fostering a culture of innovation and continuous learning ensures that the workforce can adapt to technological advancements.
In this context, educational institutions and training centers become vital partners in the digital manufacturing ecosystem.
Collaborating with these entities ensures a steady pipeline of skilled professionals ready to take on the challenges of a digitally-driven manufacturing environment.
Challenges and Opportunities
Despite the numerous benefits, digital partnerships in manufacturing are not without challenges.
Issues such as data security, technological compatibility, and resistance to change can hinder progress.
Nevertheless, these challenges also present opportunities.
For instance, developing robust cybersecurity measures and standardized protocols can enhance trust and collaboration between partners.
Furthermore, embracing change and fostering open communication within organizations can mitigate resistance and encourage a more inclusive transition towards digital manufacturing.
Conclusion
The future of manufacturing lies in the successful integration of digital partnerships.
By leveraging data, AI, IoT, and other innovative technologies, these collaborations pave the way for smarter, more efficient, and sustainable manufacturing practices.
As we navigate this digital revolution, it is essential to embrace change, invest in skill development, and prioritize collaboration across industries.
In doing so, we lay the foundation for a manufacturing landscape that is not only advanced and competitive but also resilient and adaptive to future challenges.
資料ダウンロード
QCD管理受発注クラウド「newji」は、受発注部門で必要なQCD管理全てを備えた、現場特化型兼クラウド型の今世紀最高の受発注管理システムとなります。
ユーザー登録
受発注業務の効率化だけでなく、システムを導入することで、コスト削減や製品・資材のステータス可視化のほか、属人化していた受発注情報の共有化による内部不正防止や統制にも役立ちます。
NEWJI DX
製造業に特化したデジタルトランスフォーメーション(DX)の実現を目指す請負開発型のコンサルティングサービスです。AI、iPaaS、および先端の技術を駆使して、製造プロセスの効率化、業務効率化、チームワーク強化、コスト削減、品質向上を実現します。このサービスは、製造業の課題を深く理解し、それに対する最適なデジタルソリューションを提供することで、企業が持続的な成長とイノベーションを達成できるようサポートします。
製造業ニュース解説
製造業、主に購買・調達部門にお勤めの方々に向けた情報を配信しております。
新任の方やベテランの方、管理職を対象とした幅広いコンテンツをご用意しております。
お問い合わせ
コストダウンが利益に直結する術だと理解していても、なかなか前に進めることができない状況。そんな時は、newjiのコストダウン自動化機能で大きく利益貢献しよう!
(β版非公開)