- お役立ち記事
- Digital Strategies for Cost Reduction and Efficiency in Manufacturing
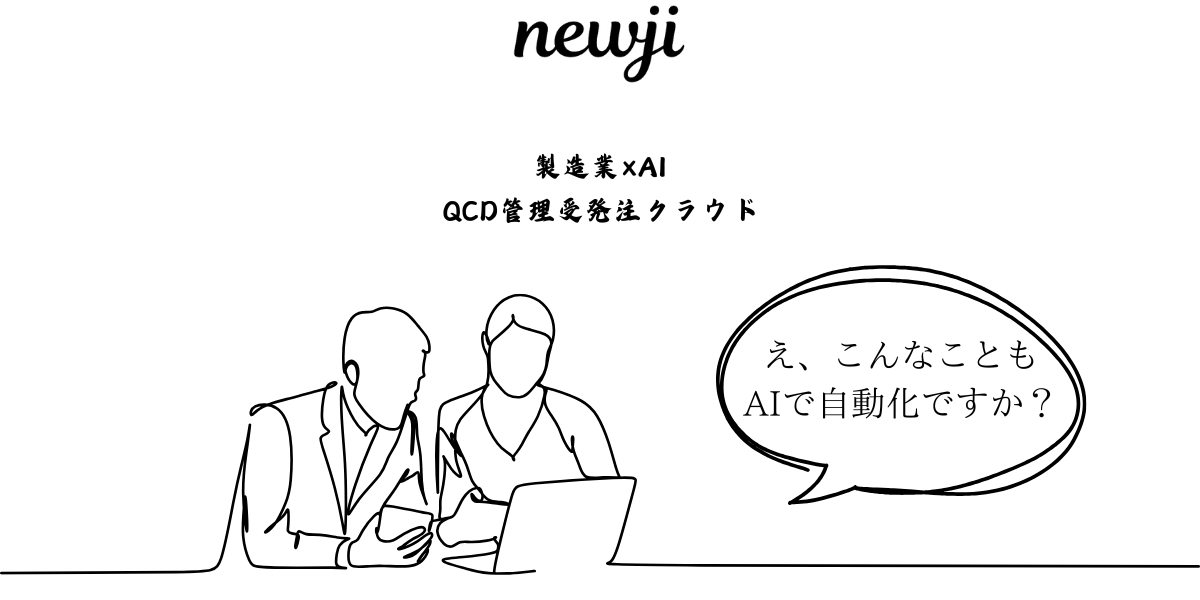
Digital Strategies for Cost Reduction and Efficiency in Manufacturing
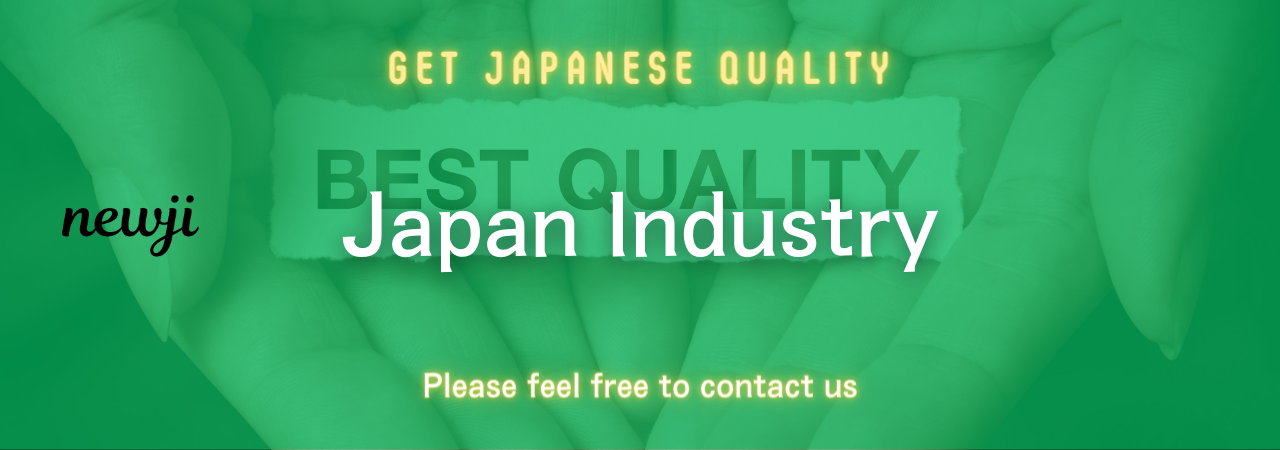
Manufacturing is a field that has always been at the forefront of innovation.
With the development of new technologies, the industry has the opportunity to become more efficient and reduce costs.
Digital strategies are paving the way for manufacturers to hone their operations and remain competitive.
Let’s explore how digital strategies can revolutionize cost reduction and efficiency in manufacturing.
目次
Understanding the Digital Transformation
Digital transformation involves integrating digital technology into all areas of a business, fundamentally changing how operations are conducted.
For manufacturers, this means leveraging technologies such as the Internet of Things (IoT), artificial intelligence (AI), and big data analytics.
By adopting these technologies, manufacturers can streamline processes, improve product quality, and reduce costs.
Understanding the benefits and applications of these digital strategies is crucial for any manufacturer aiming to stay ahead.
Internet of Things (IoT) in Manufacturing
The Internet of Things refers to the network of physical devices connected to the internet, enabling these devices to collect and share data.
In manufacturing, IoT can be used for various applications.
For instance, connected sensors can monitor equipment health in real-time, predicting potential failures before they occur.
This predictive maintenance reduces downtime and extends the life of machinery, resulting in significant cost savings.
IoT also allows tracking of inventory levels in real-time, optimizes supply chain management, and ensures that manufacturing processes run smoothly.
Artificial Intelligence (AI) for Smarter Decision-Making
Artificial Intelligence is transforming manufacturing by providing insights that were previously unattainable.
AI can analyze vast amounts of data quickly, identifying patterns and trends that human analysts might miss.
In manufacturing, AI can be used for quality control, detecting defects in products faster and more accurately than manual inspection.
Additionally, AI algorithms can improve production processes by identifying inefficiencies and suggesting optimizations.
Supply chain management and demand forecasting are another area where AI shines, helping manufacturers make informed decisions that reduce waste and lower costs.
Big Data Analytics for Enhanced Performance
Big data analytics involves examining large sets of data to uncover hidden patterns, correlations, and insights.
In the manufacturing industry, big data can be used to enhance performance at multiple levels.
For example, data from various sensors and devices can be analyzed to optimize production schedules, reduce energy consumption, and increase operational efficiency.
By understanding the data generated from manufacturing processes, companies can make more informed decisions, leading to cost savings and improved productivity.
Implementing Digital Strategies Successfully
Simply recognizing the potential of digital technologies is not enough; manufacturers must also know how to implement them effectively.
This requires a strategic approach and a willingness to invest in both technology and human capital.
Employee Training and Development
The successful implementation of digital technologies depends significantly on the workforce’s ability to use and maintain them.
Investing in employee training and development ensures that the team is well-equipped to handle new digital tools.
Workshops, seminars, and hands-on training sessions can help employees gain a thorough understanding of new technologies.
By fostering a culture of continuous learning, manufacturers can keep their workforce motivated and up-to-date with the latest advancements.
Scalable and Flexible Solutions
When investing in digital technologies, it’s essential to choose scalable and flexible solutions.
Manufacturers should look for technologies that can grow with their business and adapt to changing requirements.
Scalable solutions can easily be expanded or modified as needed, ensuring that the investment remains valuable over time.
Flexibility in technology allows for seamless integration with existing systems, reducing the risk of disruption during the transition phase.
Collaboration with Technology Partners
Collaborating with technology partners can significantly enhance the successful implementation of digital strategies.
Technology partners bring a wealth of expertise and resources, helping manufacturers navigate the complexities of digital transformation.
These partners can provide tailored solutions that meet the specific needs of the manufacturing industry.
Additionally, collaboration with technology partners can help manufacturers stay updated with the latest trends and innovations, ensuring they always remain competitive.
Real-World Examples of Digital Transformation
To understand the impact of digital strategies on cost reduction and efficiency, let’s look at some real-world examples.
General Electric (GE) and Predictive Maintenance
General Electric implemented IoT solutions to monitor the health of their manufacturing equipment.
By using connected sensors and predictive maintenance algorithms, GE reduced equipment downtime by 30%.
This improvement translated to significant cost savings and enhanced productivity.
Siemens and AI-Driven Quality Control
Siemens utilized artificial intelligence to improve their quality control processes.
With AI-driven inspection systems, Siemens detected defects in products more accurately and quickly than manual inspections.
This resulted in a 40% reduction in defects and decreased rework costs, underlining the efficiency gains brought by AI.
Procter & Gamble (P&G) and Big Data Analytics
Procter & Gamble leveraged big data analytics to optimize their supply chain and production processes.
By analyzing data from various sources, P&G improved their forecasting accuracy and reduced inventory costs by 15%.
Moreover, the use of big data analytics helped P&G enhance operational efficiency across their manufacturing plants.
The Future of Manufacturing
The digital transformation in manufacturing is still in its early stages, yet it has already demonstrated tremendous potential.
As technology continues to evolve, manufacturers will have access to even more sophisticated tools.
Future advancements in areas like 5G connectivity, augmented reality (AR), and digital twins are expected to further revolutionize the industry.
5G Connectivity
The deployment of 5G networks will provide faster and more reliable connectivity, enabling real-time data transfer and communication.
For manufacturers, this means enhanced automation, improved remote monitoring, and better connectivity between devices.
The increased speed and reliability of 5G will free up more resources, helping manufacturers further reduce costs and improve efficiency.
Augmented Reality (AR)
Augmented reality has the potential to revolutionize maintenance and repair procedures.
Technicians can use AR glasses to receive real-time guidance and information, enabling more accurate and efficient repairs.
This can reduce downtime and minimize errors, resulting in cost savings and improved productivity.
Digital Twins
Digital twins are virtual replicas of physical assets that allow manufacturers to simulate and analyze real-world conditions.
By creating digital twins of machinery and equipment, manufacturers can test different scenarios and predict outcomes.
This predictive capability enables better decision-making, reduces the risk of equipment failure, and optimizes production processes.
In conclusion, digital strategies are transforming the landscape of manufacturing.
By embracing IoT, AI, and big data analytics, manufacturers can achieve significant cost reductions and efficiency gains.
To stay competitive, manufacturers must invest in employee training, seek scalable solutions, and collaborate with technology partners.
The future holds even more promise, with advancements in 5G, AR, and digital twins set to further revolutionize the industry.
Digital transformation is not just an option; it’s a necessity for manufacturers aiming to thrive in the evolving landscape.
資料ダウンロード
QCD調達購買管理クラウド「newji」は、調達購買部門で必要なQCD管理全てを備えた、現場特化型兼クラウド型の今世紀最高の購買管理システムとなります。
ユーザー登録
調達購買業務の効率化だけでなく、システムを導入することで、コスト削減や製品・資材のステータス可視化のほか、属人化していた購買情報の共有化による内部不正防止や統制にも役立ちます。
NEWJI DX
製造業に特化したデジタルトランスフォーメーション(DX)の実現を目指す請負開発型のコンサルティングサービスです。AI、iPaaS、および先端の技術を駆使して、製造プロセスの効率化、業務効率化、チームワーク強化、コスト削減、品質向上を実現します。このサービスは、製造業の課題を深く理解し、それに対する最適なデジタルソリューションを提供することで、企業が持続的な成長とイノベーションを達成できるようサポートします。
オンライン講座
製造業、主に購買・調達部門にお勤めの方々に向けた情報を配信しております。
新任の方やベテランの方、管理職を対象とした幅広いコンテンツをご用意しております。
お問い合わせ
コストダウンが利益に直結する術だと理解していても、なかなか前に進めることができない状況。そんな時は、newjiのコストダウン自動化機能で大きく利益貢献しよう!
(Β版非公開)