- お役立ち記事
- Digital Tools to Strengthen QCD Management
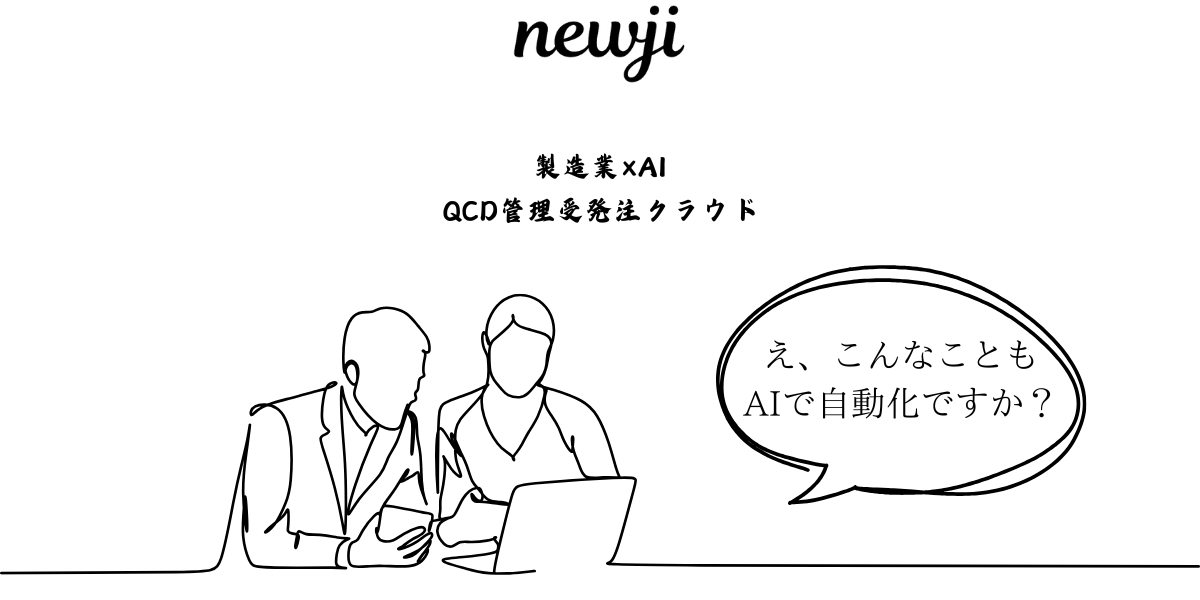
Digital Tools to Strengthen QCD Management
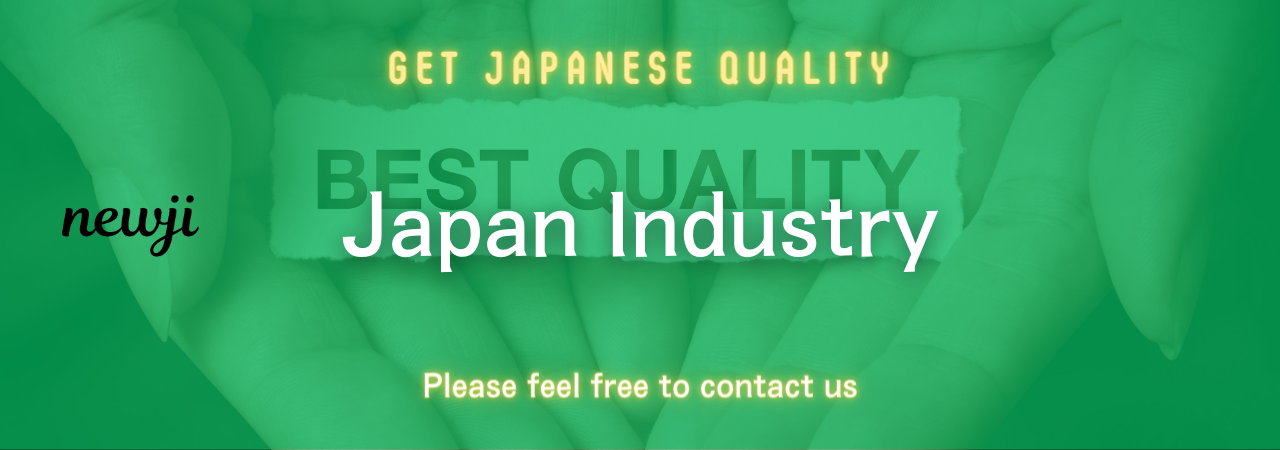
In today’s fast-paced business environment, maintaining perfect Quality, Cost, and Delivery (QCD) management is crucial for success.
Digital tools have evolved to play a significant role in strengthening QCD management processes.
These tools not only make the management workflow more efficient but also reduce errors, save time, and minimize costs.
目次
Understanding QCD Management
QCD management is a comprehensive approach designed to ensure the quality of products, control production costs, and meet delivery schedules.
It plays a vital role in business operations, particularly in manufacturing and production industries.
Quality ensures that products meet customer expectations and standards.
Cost management involves controlling expenditure to optimize profitability.
Delivery refers to meeting timelines to keep customers satisfied.
The Role of Digital Tools in QCD Management
Integrating digital tools into QCD management processes significantly optimizes efficiency and accuracy.
Enhancing Quality Control
Digital tools offer advanced quality control capabilities.
Automated systems can monitor production lines in real-time, immediately identifying defects and issues.
This swift identification allows for quick corrections, ensuring that the final products maintain high standards.
Additionally, digital tools often incorporate Artificial Intelligence (AI), which can predict potential quality issues before they occur by analyzing historical data.
Optimizing Cost Management
Managing costs effectively is a critical component of QCD management.
Digital tools aid in tracking expenses at every production stage.
They provide detailed reports and analytics, offering insights into areas where costs can be reduced.
For example, software solutions can monitor resource usage to ensure materials are utilized efficiently, minimizing waste.
Additionally, digital tools can streamline procurement processes, automate supplier management, and negotiate better rates.
Improving Delivery Schedules
Timely delivery is essential to meet customer expectations and maintain satisfaction.
Digital tools provide real-time tracking of production timelines, enabling better planning and scheduling.
They assist in identifying bottlenecks in the production process, allowing for adjustments to be made promptly.
Moreover, automated scheduling tools can allocate resources more effectively, ensuring that deadlines are consistently met.
Popular Digital Tools for Strengthening QCD Management
Several digital tools are specifically designed to enhance different aspects of QCD management.
These tools span various functions, including project management, quality control, cost management, and logistics.
Project Management Tools
Tools like Trello, Asana, and Microsoft Project help manage and streamline complex projects.
They offer features like task assignment, progress tracking, and deadline reminders.
These tools ensure that all team members are aligned and aware of their responsibilities, which helps maintain delivery schedules and control costs.
Quality Management Software
Quality management software, such as SAP QM and MasterControl, provides comprehensive solutions for quality assurance.
They offer functionalities like document control, audit management, and compliance tracking.
These tools ensure that production processes adhere to quality standards, significantly reducing the risk of defects.
Cost Management Systems
Cost management systems, like Oracle Financials and FreshBooks, help businesses keep tight control over their finances.
These tools offer real-time tracking of expenses, budgeting features, and detailed financial reporting.
They enable companies to make informed decisions about where to cut costs without compromising quality or delivery.
Logistics and Supply Chain Solutions
Effective logistics and supply chain management are critical for timely deliveries.
Tools like SAP SCM and Oracle SCM Cloud provide visibility and control over the entire supply chain.
They assist in inventory management, supplier coordination, and logistics planning.
These tools ensure that materials and products move smoothly through the production process, reducing delays.
The Benefits of Integrating Digital Tools into QCD Management
Integrating digital tools into QCD management offers numerous benefits to businesses.
Enhanced Efficiency
Automation and real-time monitoring provided by digital tools significantly enhance operational efficiency.
With automated reporting and data analysis, businesses can quickly identify and address issues, leading to smoother operations.
Cost Savings
Implementing digital tools reduces manual labor, minimizing human errors and associated costs.
Additionally, these tools optimize resource usage, reduce waste, and improve procurement processes, leading to substantial cost savings.
Improved Product Quality
With advanced quality control features, digital tools help maintain the highest standards.
They enable businesses to detect and rectify defects quickly, ensuring that only top-quality products reach customers.
Timely Deliveries
Better scheduling, resource allocation, and logistics management provided by digital tools ensure that products are delivered on time.
This results in higher customer satisfaction and strengthens business relationships.
Challenges and Considerations
While digital tools offer significant advantages, integrating them into QCD management does come with challenges.
Businesses must consider several factors before implementation.
Initial Investment
The initial investment for digital tools can be substantial.
Businesses need to evaluate the long-term benefits and ROI to justify the upfront costs.
Training and Adoption
Employees may require training to use new digital tools effectively.
Ensuring that the entire team is comfortable with the technology is crucial for successful integration.
Data Security
With digital tools, data security becomes a concern.
Businesses must implement robust cybersecurity measures to protect sensitive information.
Conclusion
Digital tools have revolutionized QCD management, offering unprecedented efficiency, accuracy, and cost savings.
By enhancing quality control, optimizing cost management, and improving delivery schedules, these tools help businesses stay competitive in today’s dynamic market.
While the initial investment and learning curve may pose challenges, the long-term benefits far outweigh the costs.
Integrating digital tools into QCD management is no longer an option but a necessity for businesses aiming to achieve operational excellence and customer satisfaction.
資料ダウンロード
QCD調達購買管理クラウド「newji」は、調達購買部門で必要なQCD管理全てを備えた、現場特化型兼クラウド型の今世紀最高の購買管理システムとなります。
ユーザー登録
調達購買業務の効率化だけでなく、システムを導入することで、コスト削減や製品・資材のステータス可視化のほか、属人化していた購買情報の共有化による内部不正防止や統制にも役立ちます。
NEWJI DX
製造業に特化したデジタルトランスフォーメーション(DX)の実現を目指す請負開発型のコンサルティングサービスです。AI、iPaaS、および先端の技術を駆使して、製造プロセスの効率化、業務効率化、チームワーク強化、コスト削減、品質向上を実現します。このサービスは、製造業の課題を深く理解し、それに対する最適なデジタルソリューションを提供することで、企業が持続的な成長とイノベーションを達成できるようサポートします。
オンライン講座
製造業、主に購買・調達部門にお勤めの方々に向けた情報を配信しております。
新任の方やベテランの方、管理職を対象とした幅広いコンテンツをご用意しております。
お問い合わせ
コストダウンが利益に直結する術だと理解していても、なかなか前に進めることができない状況。そんな時は、newjiのコストダウン自動化機能で大きく利益貢献しよう!
(Β版非公開)