- お役立ち記事
- Disaster prevention plan and response manual for purchasing departments in preparation for supply chain risks
月間76,176名の
製造業ご担当者様が閲覧しています*
*2025年3月31日現在のGoogle Analyticsのデータより
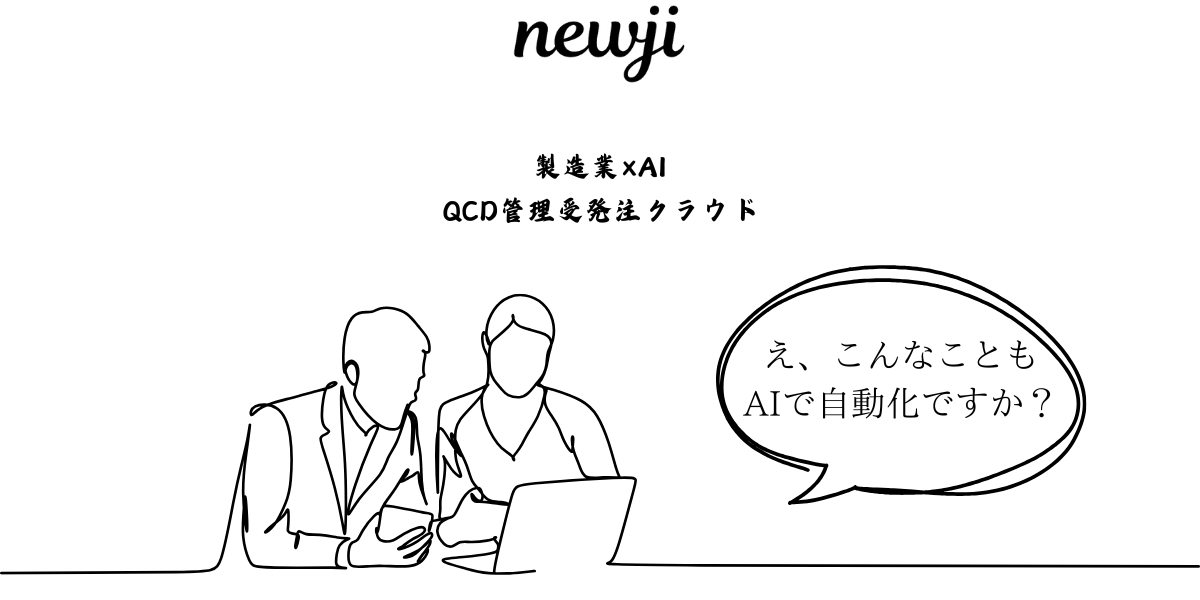
Disaster prevention plan and response manual for purchasing departments in preparation for supply chain risks
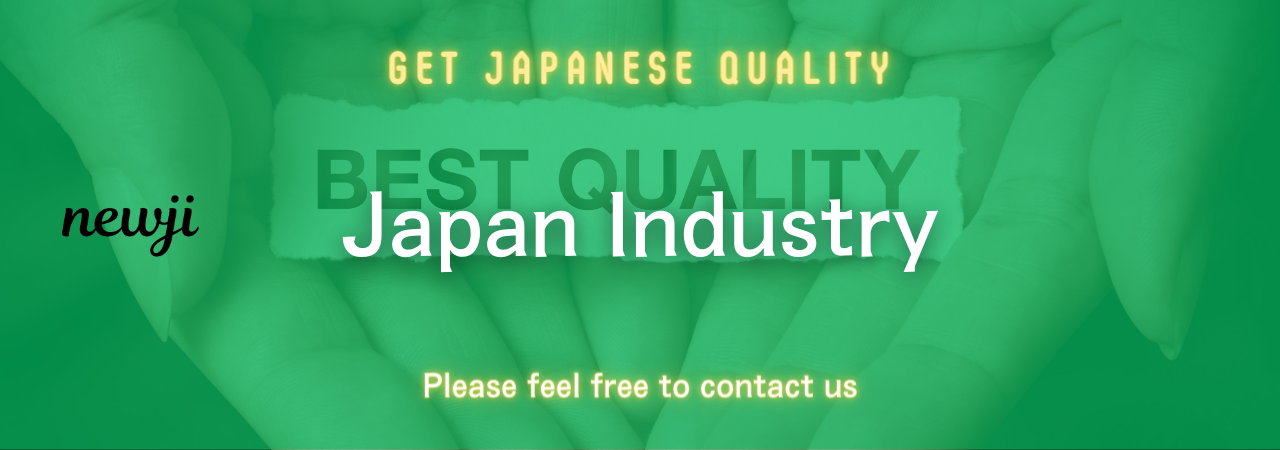
目次
Understanding Supply Chain Risks
In today’s interconnected world, supply chains are the backbone of any business.
A supply chain involves various processes that connect companies with their suppliers and customers.
It ensures that products are produced and delivered seamlessly.
However, this intricate web of processes is not without risks.
Disruptions can arise from natural disasters, geopolitical tensions, or even unforeseeable events like pandemics.
For purchasing departments, understanding these risks and having a robust disaster prevention plan is crucial.
Supply chain risks can manifest in numerous ways.
Natural disasters such as earthquakes, floods, or hurricanes can halt production in affected areas.
Political upheavals or changes in trade policies can create delays and increase costs.
Moreover, supplier insolvency or quality issues can disrupt the flow of goods.
These disruptions can lead to production delays, increased costs, and ultimately, dissatisfied customers.
The Importance of a Disaster Prevention Plan
Developing a disaster prevention plan is essential for purchasing departments to mitigate supply chain risks.
Such a plan involves identifying potential risks, evaluating their impact, and establishing strategies to minimize or respond to these threats.
This proactive approach not only ensures business continuity but also builds resilience in the face of uncertainties.
A comprehensive disaster prevention plan encompasses several key components.
Firstly, it should involve risk identification and assessment, where potential threats to the supply chain are identified.
Secondly, the plan should include risk evaluation, which determines the severity and likelihood of these risks.
Finally, risk mitigation strategies are developed to reduce the impact of identified threats.
Steps to Develop a Disaster Prevention Plan
Conduct a Risk Assessment
The first step in creating a disaster prevention plan is conducting a thorough risk assessment.
This involves mapping out the supply chain to identify critical points and potential vulnerabilities.
It includes evaluating suppliers, transportation routes, and the political and environmental conditions of regions involved.
Develop Risk Mitigation Strategies
Once risks are identified, the next step is to develop strategies to mitigate them.
This can include diversifying suppliers to reduce dependency on a single source.
Maintaining safety stock in warehouses can provide a buffer against unexpected supply chain interruptions.
Additionally, leveraging technology for real-time monitoring can help in anticipating and responding to disruptions swiftly.
Create a Communication Plan
An effective disaster response hinges on clear and timely communication.
Establish a communication plan to ensure that stakeholders, including suppliers, logistics partners, and customers, are informed about any disruptions and the steps being taken.
This helps in managing expectations and maintaining trust.
Establish Contingency Plans
Contingency plans are essential components of a disaster prevention strategy.
These plans should outline specific actions to be taken in case of disruption.
For example, if a supplier is unable to deliver, identify alternate suppliers or materials that can be used as substitutes without compromising quality.
Implementing and Reviewing the Disaster Prevention Plan
Employee Training
Implementing a disaster prevention plan is not a one-time task.
It involves continuous training and awareness for purchasing department staff.
Regular drills and training sessions ensure that employees are well-versed with the plan and can act swiftly and effectively when needed.
Plan Testing and Review
Periodic testing and reviewing of the disaster prevention plan are crucial to ensure its efficacy.
Simulate different disaster scenarios to test the practicality of your strategies and adjust the plan based on lessons learned from these exercises.
Regular reviews also help in incorporating changes due to evolving risks or new supply chain processes.
The Role of Technology in Disaster Prevention
In the digital age, technology plays a pivotal role in disaster prevention and response.
Supply chain management software can provide real-time data and insights, helping businesses monitor their supply chain operations closely.
Technological solutions like AI and machine learning can predict potential disruptions by analyzing patterns and trends, enabling businesses to take preemptive measures.
Moreover, blockchain technology can enhance transparency and traceability in supply chains.
This allows for faster response times by providing a clear chain of custody for products and materials.
Technology not only aids in prevention but also facilitates quicker recovery and continuity during disruptions.
Building a Resilient Supply Chain
In conclusion, a well-crafted disaster prevention plan is vital for purchasing departments to navigate supply chain risks effectively.
By understanding potential risks, developing mitigation strategies, and leveraging technology, businesses can build resilient supply chains.
This resilience not only safeguards the company’s operations but also strengthens relationships with suppliers and customers.
It’s essential for companies to view disaster prevention as an ongoing process that requires regular updates and improvements.
In doing so, they can ensure that they are well-prepared to weather any storm and maintain a competitive edge in the marketplace.
By prioritizing disaster prevention and response, purchasing departments can safeguard their supply chains, protect their brand reputation, and ensure long-term success.
資料ダウンロード
QCD管理受発注クラウド「newji」は、受発注部門で必要なQCD管理全てを備えた、現場特化型兼クラウド型の今世紀最高の受発注管理システムとなります。
ユーザー登録
受発注業務の効率化だけでなく、システムを導入することで、コスト削減や製品・資材のステータス可視化のほか、属人化していた受発注情報の共有化による内部不正防止や統制にも役立ちます。
NEWJI DX
製造業に特化したデジタルトランスフォーメーション(DX)の実現を目指す請負開発型のコンサルティングサービスです。AI、iPaaS、および先端の技術を駆使して、製造プロセスの効率化、業務効率化、チームワーク強化、コスト削減、品質向上を実現します。このサービスは、製造業の課題を深く理解し、それに対する最適なデジタルソリューションを提供することで、企業が持続的な成長とイノベーションを達成できるようサポートします。
製造業ニュース解説
製造業、主に購買・調達部門にお勤めの方々に向けた情報を配信しております。
新任の方やベテランの方、管理職を対象とした幅広いコンテンツをご用意しております。
お問い合わせ
コストダウンが利益に直結する術だと理解していても、なかなか前に進めることができない状況。そんな時は、newjiのコストダウン自動化機能で大きく利益貢献しよう!
(β版非公開)