- お役立ち記事
- Discover the Impact of Oxidation in Japanese Manufacturing: Insights and Innovations
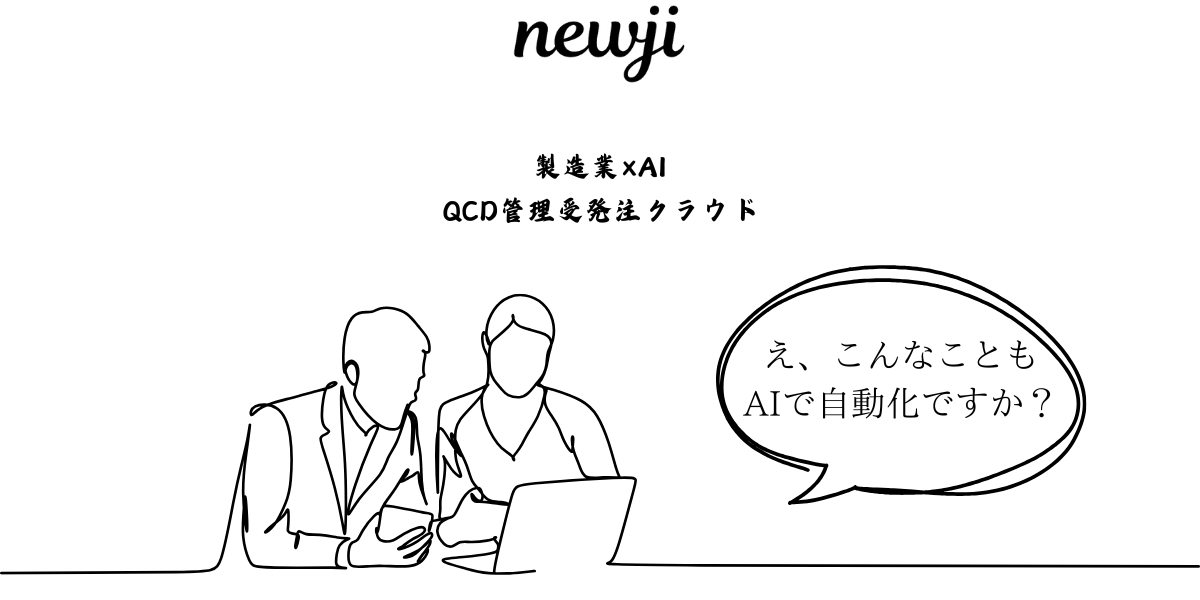
Discover the Impact of Oxidation in Japanese Manufacturing: Insights and Innovations
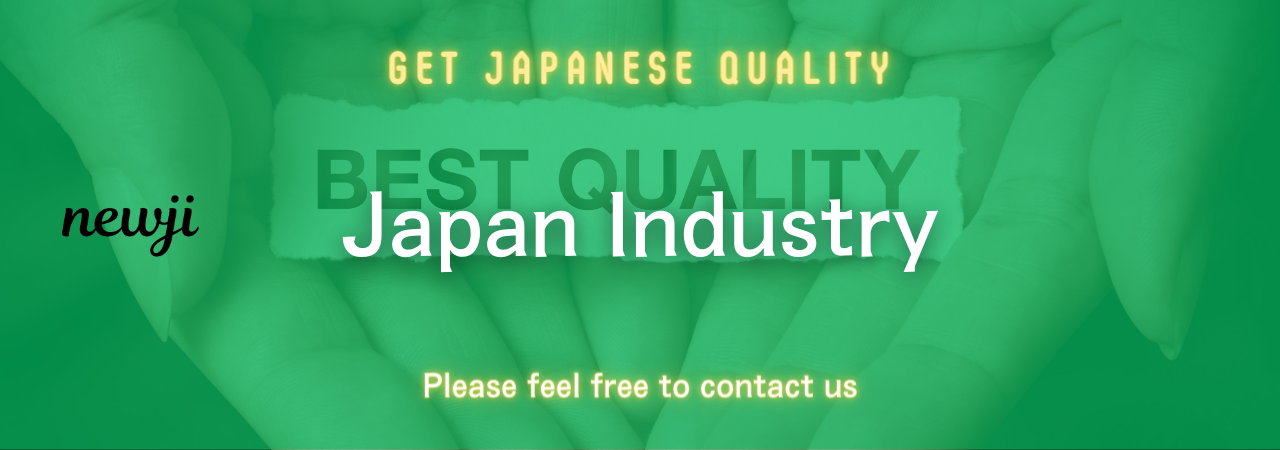
目次
Introduction to Oxidation in Japanese Manufacturing
In the realm of manufacturing, oxidation is a critical concern that can significantly impact product quality and longevity.
Japan, renowned for its exceptional manufacturing prowess and stringent quality standards, pays particular attention to the effects of oxidation on materials and components.
By understanding oxidation, its implications, and the innovations Japanese manufacturing companies employ to mitigate its effects, procurement professionals can make informed decisions and foster successful supplier relationships.
Understanding Oxidation
Oxidation is an electrochemical reaction where a material, typically metal, reacts with oxygen, leading to the formation of oxides.
This process can deteriorate material properties, such as strength, conductivity, and resistance.
In manufacturing, oxidation can manifest as rust on steel, tarnish on silver, or even the formation of a thin film on semiconductor materials.
Given Japan’s emphasis on quality, understanding and mitigating oxidation is crucial for maintaining the integrity and functionality of manufactured products.
The Impact of Oxidation on Product Quality
Material Degradation
Oxidation can lead to the degradation of materials, affecting their mechanical and physical properties.
For instance, rusting can weaken steel structures, while tarnishing can diminish the aesthetic value and conductivity of metals like silver.
In the electronics industry, oxide layers can impair the performance of semiconductors and connectors.
Increased Maintenance Costs
Oxidation-induced degradation necessitates frequent maintenance and replacement of parts, leading to increased operational costs.
For manufacturers, managing these costs while ensuring product quality is a delicate balance.
Product Failures
In critical applications, such as automotive and aerospace, oxidation can lead to catastrophic product failures.
For example, corroded engine components can compromise vehicle safety, and oxidized aerospace parts can lead to mission-critical failures.
Innovations in Japanese Manufacturing to Combat Oxidation
Japanese manufacturers have developed a suite of innovative techniques and materials to combat oxidation and ensure product longevity.
Protective Coatings
One of the most effective ways to combat oxidation is through protective coatings.
Japanese manufacturers extensively use coatings such as galvanization, anodization, and passivation to shield materials from oxidative effects.
These coatings form a barrier, preventing oxygen from interacting with the base material.
Advanced Materials
Incorporating advanced materials resistant to oxidation is another strategy.
For instance, stainless steel, which contains chromium, forms a self-healing oxide layer that prevents further oxidation.
Japanese manufacturers are at the forefront of developing and employing advanced alloys and composites with superior oxidation resistance.
Controlled Environments
Maintaining controlled manufacturing environments, such as cleanrooms and inert atmosphere chambers, is crucial in oxidation-sensitive production processes.
This approach is particularly prevalent in semiconductor and pharmaceutical manufacturing, where even trace levels of oxidation can lead to significant defects.
Innovative Manufacturing Techniques
Japan’s continuous pursuit of innovation has led to the development of manufacturing techniques that mitigate oxidation.
Cold welding, laser processing, and additive manufacturing (3D printing) are examples of methods that minimize oxidation by reducing thermal exposure or controlling environmental conditions during production.
Practical Insights from Procurement and Purchasing Perspectives
Understanding the implications of oxidation and the strategies to mitigate it can significantly influence procurement and purchasing decisions.
Supplier Assessment
Evaluating suppliers’ capabilities to manage oxidation is crucial.
This involves assessing their use of protective coatings, advanced materials, and manufacturing techniques.
Experienced procurement professionals often conduct audits and inspections to ensure suppliers meet the required standards.
Cost-Benefit Analysis
Balancing the costs of anti-oxidation measures with the benefits is essential.
While advanced materials and coatings may incur higher upfront costs, the long-term benefits in terms of reduced maintenance and enhanced product reliability often justify the investment.
Calculating the total cost of ownership (TCO) can help in making informed decisions.
Collaborative Innovation
Engaging in collaborative innovation with Japanese suppliers can lead to mutually beneficial outcomes.
Joint development projects often result in customized solutions that address specific oxidation challenges.
Building strong relationships with suppliers fosters trust and transparency, enabling effective collaboration.
Market Conditions and Trends
Staying updated with market conditions and trends related to oxidation-resistant materials and technologies is vital.
Industry forums, trade shows, and technical journals are valuable resources for gaining insights into new developments.
Procurement professionals should leverage these platforms to stay ahead of the curve.
Supplier Negotiation Techniques
Effective negotiation with suppliers is critical to securing the best terms and ensuring that anti-oxidation measures are integrated into the manufacturing process.
Negotiation Preparation
Thorough preparation is the foundation of successful negotiations.
Understanding the technical aspects of oxidation and the specific requirements of your applications allows for informed discussions with suppliers.
Gathering data on market prices, supplier capabilities, and potential alternatives provides leverage during negotiations.
Focus on Value
While cost is an important factor, focusing solely on the price can be shortsighted.
Emphasize the value that oxidation mitigation measures bring to the table, such as improved product quality, reduced maintenance costs, and extended product lifespan.
Highlighting these benefits helps in justifying higher costs for advanced materials and protective coatings.
Long-Term Agreements
Long-term agreements with suppliers often result in better terms and improved supplier commitment.
By securing long-term contracts, procurement professionals can negotiate terms such as volume discounts, priority production slots, and continuous improvement initiatives.
Quality Assurance Clauses
Including quality assurance clauses in contracts is essential.
These clauses should specify the standards for protective coatings, materials, and manufacturing techniques that suppliers must adhere to.
Regular audits and inspections ensure compliance and help in maintaining product quality.
Best Practices for Managing Oxidation in the Supply Chain
Implementing best practices for managing oxidation within the supply chain is crucial for maintaining product quality and ensuring customer satisfaction.
Collaborative Supplier Relationships
Building strong, collaborative relationships with suppliers is a best practice that yields significant benefits.
Regular communication, joint development projects, and shared goals contribute to a deeper understanding of oxidation challenges and foster collaborative solutions.
Continuous Improvement
Adopting a mindset of continuous improvement is essential.
Regularly reviewing and updating anti-oxidation measures, incorporating feedback from quality control teams, and staying abreast of technological advancements help in maintaining the highest standards.
Training and Development
Investing in training and development for procurement and manufacturing teams is crucial.
Understanding the technical aspects of oxidation, the benefits of different mitigation strategies, and the latest industry trends equips teams to make informed decisions and drive continuous improvement.
Leveraging Technology
Leveraging technology, such as data analytics and predictive maintenance, can significantly improve the management of oxidation.
Data analytics provides insights into oxidation patterns, enabling proactive measures to prevent degradation.
Predictive maintenance helps in identifying and addressing oxidation issues before they lead to product failures.
Case Studies: Success Stories in Japanese Manufacturing
Examining case studies of successful oxidation management in Japanese manufacturing provides valuable insights and inspiration.
Automotive Industry Example
A leading Japanese automotive manufacturer implemented advanced protective coatings and stainless steel components in their vehicle line-up.
This strategy not only enhanced the longevity and reliability of their vehicles but also reduced warranty claims by 30%.
By collaborating closely with suppliers, they developed customized solutions that met their specific needs.
Electronics Industry Example
A prominent Japanese electronics company adopted controlled environment manufacturing and innovative laser processing techniques to mitigate oxidation in semiconductor production.
This approach resulted in a 20% increase in yield and a significant reduction in defects.
By investing in state-of-the-art technology and fostering supplier partnerships, they maintained their competitive edge.
Pharmaceutical Industry Example
A major Japanese pharmaceutical manufacturer employed advanced materials and controlled atmosphere packaging to combat oxidation in drug formulations.
These measures ensured the stability and efficacy of their products throughout the shelf life.
Their proactive approach to oxidation management solidified their reputation for high-quality pharmaceuticals.
Conclusion: Embracing Innovations and Insights
Oxidation poses significant challenges in manufacturing, affecting product quality and longevity.
However, Japanese manufacturers have pioneered innovative solutions to combat these effects, ensuring their products meet the highest standards.
For procurement professionals, understanding the impact of oxidation, leveraging supplier relationships, and adopting best practices are key to achieving optimal outcomes.
By embracing the insights and innovations in Japanese manufacturing, companies can enhance their procurement strategies, drive continuous improvement, and enjoy the benefits of superior product quality.
As the industry continues to evolve, staying informed and proactive in managing oxidation will be crucial for maintaining a competitive edge.
資料ダウンロード
QCD調達購買管理クラウド「newji」は、調達購買部門で必要なQCD管理全てを備えた、現場特化型兼クラウド型の今世紀最高の購買管理システムとなります。
ユーザー登録
調達購買業務の効率化だけでなく、システムを導入することで、コスト削減や製品・資材のステータス可視化のほか、属人化していた購買情報の共有化による内部不正防止や統制にも役立ちます。
NEWJI DX
製造業に特化したデジタルトランスフォーメーション(DX)の実現を目指す請負開発型のコンサルティングサービスです。AI、iPaaS、および先端の技術を駆使して、製造プロセスの効率化、業務効率化、チームワーク強化、コスト削減、品質向上を実現します。このサービスは、製造業の課題を深く理解し、それに対する最適なデジタルソリューションを提供することで、企業が持続的な成長とイノベーションを達成できるようサポートします。
オンライン講座
製造業、主に購買・調達部門にお勤めの方々に向けた情報を配信しております。
新任の方やベテランの方、管理職を対象とした幅広いコンテンツをご用意しております。
お問い合わせ
コストダウンが利益に直結する術だと理解していても、なかなか前に進めることができない状況。そんな時は、newjiのコストダウン自動化機能で大きく利益貢献しよう!
(Β版非公開)