- お役立ち記事
- Diversification of designs through combination sintering
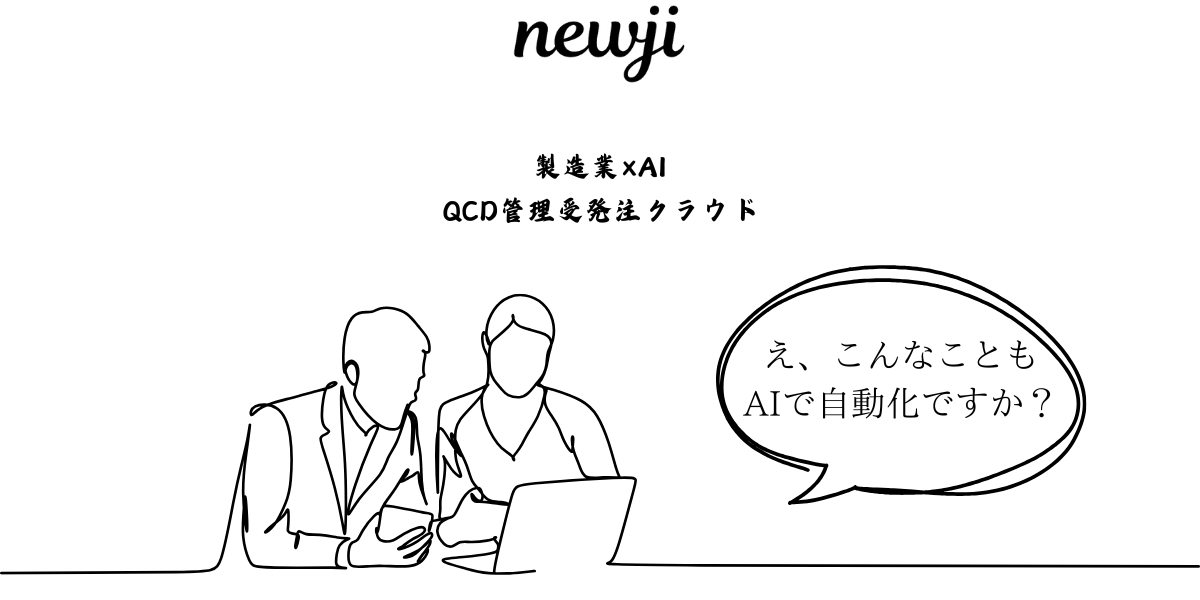
Diversification of designs through combination sintering
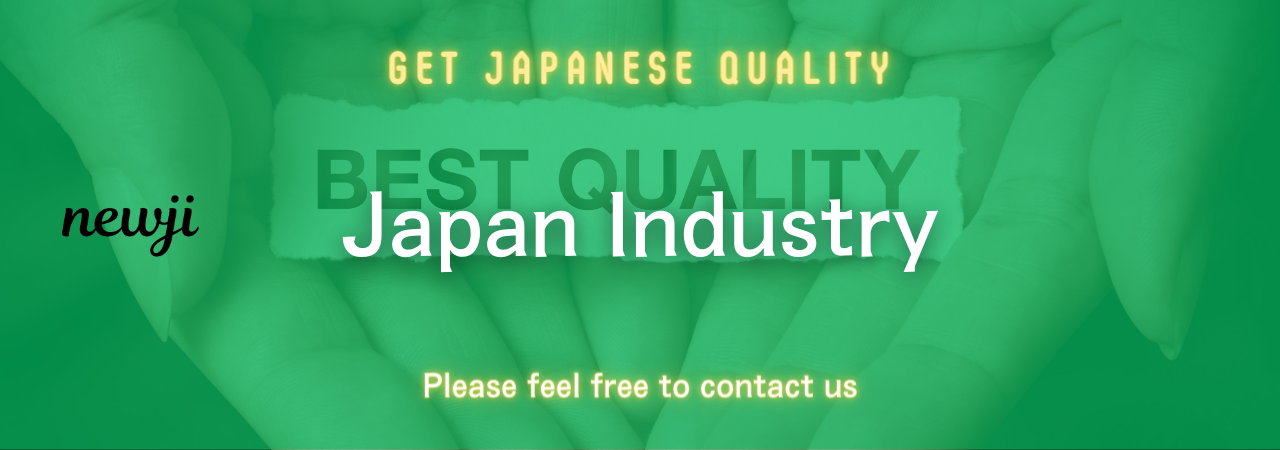
目次
Understanding Combination Sintering
Combination sintering is a fascinating process in the field of materials science and manufacturing that allows for the diversification of designs.
Sintering itself involves the compacting and forming of a solid mass of material using heat or pressure without melting the material to the point of liquefaction.
Combination sintering takes this a step further by mixing various materials or design elements to achieve unique attributes.
This method opens the door to innovative and diverse design possibilities, giving manufacturers and designers the flexibility to create materials with tailored properties.
By understanding the principles of combination sintering, you can appreciate how this process enhances the diversification of designs across different industries.
The Process of Combination Sintering
Combination sintering involves several steps, each crucial to the creation of a final product with specific characteristics.
First, material selection is crucial, where the combination of materials is chosen based on the desired outcome.
These materials are then mixed together to form a homogenous mixture.
After mixing, the material goes through a process of compaction.
This is where the mixture is pressed into a desired shape or form using mechanical pressure.
Following this, the compacted form is subjected to a sintering process, where it is heated to a temperature below its melting point.
During this heating, atomic diffusion occurs, leading to the bonding of particles and the elimination of porosity, resulting in a dense and robust material.
Variety in Design with Combination Sintering
One of the unique aspects of combination sintering is the ability to diversify designs through the strategic selection of materials.
Different materials bring varied properties, such as strength, flexibility, thermal conductivity, and corrosion resistance.
By combining these materials, manufacturers can obtain a product tailored specifically to their needs.
For example, in the automotive industry, metallic and ceramic materials can be combined through sintering to create components that are lightweight yet capable of withstanding high temperatures.
In electronics, the combination of different conductive materials could lead to components that are compact yet highly efficient.
Applications in Modern Industries
Combination sintering has found its place across various sectors, from automotive to aerospace, to biomedical Engineering.
In aerospace, lightweight and durable materials are essential.
Combination sintering allows the creation of components that can withstand the extreme conditions of space travel.
In the biomedical field, combination sintering is applied to create implants and prosthetics that mimic the mechanical properties of natural bones.
By customizing the combination of materials, it’s possible to produce implants that promote better integration with the human body.
Eco-friendly and Cost-effective Manufacturing
Besides its versatility, combination sintering also offers environmental and economic benefits.
The process tends to be more energy-efficient compared to other manufacturing methods, as it operates below melting points.
This energy efficiency can result in lower production costs, making it an attractive option for large-scale manufacturing.
Furthermore, combination sintering can also utilize recycled materials as part of the initial combination, reducing waste and promoting sustainability.
This aligns with the growing trend towards greener manufacturing practices, allowing companies to reduce their carbon footprints while still producing high-quality products.
Future Trends in Combination Sintering
As technology evolves, so too does the potential for combination sintering.
With advancements in material science, the possibilities for new combinations and applications grow.
The development of new materials can lead to the creation of even more unique and customized products.
Moreover, the integration of digital technologies, such as computer-aided design (CAD) and 3D printing, can further enhance the precision and possibilities in design diversification.
These technologies allow for more intricate and complex designs to be achieved through combination sintering, expanding its applications across industries.
Conclusion
In summary, combination sintering is a pivotal process in the realm of manufacturing and design.
Its ability to combine different materials to achieve a wide array of properties opens up new avenues for innovation and design diversification.
By leveraging the principles of combination sintering, industries can create products that are not only efficient and cost-effective but also environmentally sustainable.
As the field advances, we can expect even greater contributions from combination sintering in the development of new designs and applications, underscoring its importance in modern manufacturing and materials science.
資料ダウンロード
QCD調達購買管理クラウド「newji」は、調達購買部門で必要なQCD管理全てを備えた、現場特化型兼クラウド型の今世紀最高の購買管理システムとなります。
ユーザー登録
調達購買業務の効率化だけでなく、システムを導入することで、コスト削減や製品・資材のステータス可視化のほか、属人化していた購買情報の共有化による内部不正防止や統制にも役立ちます。
NEWJI DX
製造業に特化したデジタルトランスフォーメーション(DX)の実現を目指す請負開発型のコンサルティングサービスです。AI、iPaaS、および先端の技術を駆使して、製造プロセスの効率化、業務効率化、チームワーク強化、コスト削減、品質向上を実現します。このサービスは、製造業の課題を深く理解し、それに対する最適なデジタルソリューションを提供することで、企業が持続的な成長とイノベーションを達成できるようサポートします。
オンライン講座
製造業、主に購買・調達部門にお勤めの方々に向けた情報を配信しております。
新任の方やベテランの方、管理職を対象とした幅広いコンテンツをご用意しております。
お問い合わせ
コストダウンが利益に直結する術だと理解していても、なかなか前に進めることができない状況。そんな時は、newjiのコストダウン自動化機能で大きく利益貢献しよう!
(Β版非公開)