- お役立ち記事
- Diving Fin Manufacturing Process and Propulsion Enhancement
月間76,176名の
製造業ご担当者様が閲覧しています*
*2025年3月31日現在のGoogle Analyticsのデータより
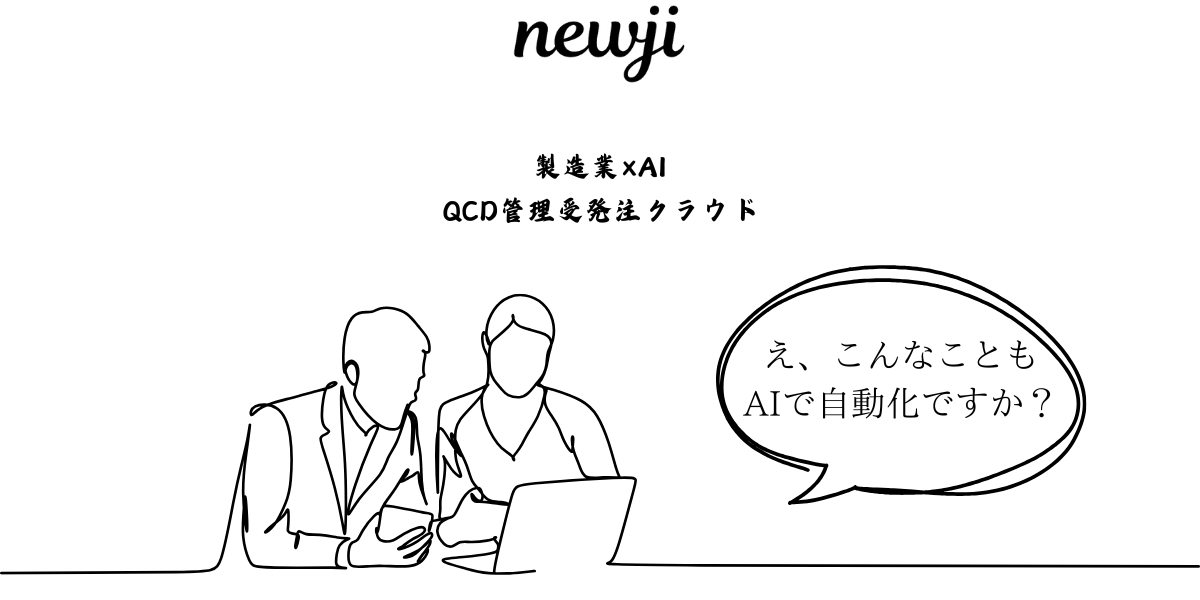
Diving Fin Manufacturing Process and Propulsion Enhancement
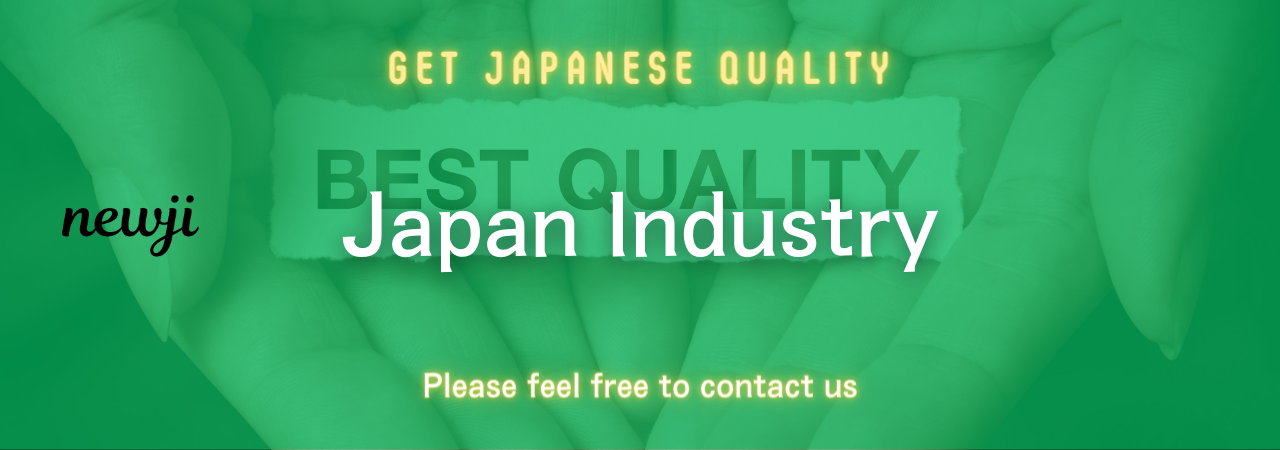
目次
An Introduction to Diving Fins
Diving fins are essential tools that help divers glide gracefully through the water.
They increase propulsion, making underwater exploration more efficient and enjoyable.
Have you ever wondered how these crucial pieces of diving equipment are made, or how their design improves propulsion?
Let’s dive deeper into the manufacturing process of diving fins and explore how their design can enhance propulsion underwater.
The Diving Fin Manufacturing Process
The process of making diving fins involves several key steps, each aiming to produce a reliable and efficient product.
Crafting a pair of diving fins involves a blend of science, precision, and a keen understanding of materials.
1. Material Selection
Diving fins are typically made from rubber, plastic, or a combination of composites.
Rubber offers flexibility and durability, which is important for enduring the stresses of water movement.
On the other hand, plastic fins are lightweight and can be molded into various shapes more easily.
Composites provide a balance of both worlds, combining flexibility with strength.
2. Designing the Model
Design plays a pivotal role in the creation of diving fins.
Engineers and designers work closely to create models that provide maximum thrust while minimizing muscle fatigue.
Advanced technologies, such as computer-aided design (CAD), are often used to create prototypes, simulating water flow and testing performance.
3. Mold Creation
Once the design is settled, a mold is created to shape the material into a fin.
Creating a mold is a detailed process, often involving metal or other durable materials to ensure precision and longevity.
The mold must reflect the design exactly, capturing every contour to produce a functioning fin.
4. Molding Process
In this step, the selected material is heated and injected into the mold.
This process, known as injection molding, ensures uniformity and precision.
It’s where the raw materials transform into the familiar shape of a diving fin.
5. Cooling and Trimming
After the material cools and solidifies, the fins are carefully removed from the mold.
They are then trimmed to remove excess material.
This stage requires significant attention to detail, ensuring the fins have a smooth finish and are free of manufacturing defects.
6. Assembly and Quality Testing
In some designs, parts of the fins are assembled to increase functionality or enhance comfort.
Once assembled, the fins undergo rigorous quality testing to ensure they meet performance standards.
They’re tested for durability, flexibility, and resistance to water, ensuring they can handle real-world diving conditions.
Propulsion Enhancement in Diving Fins
The effectiveness of diving fins lies in their ability to enhance propulsion.
But how do they do it?
Let’s look at the factors and structural features of diving fins that help divers move efficiently underwater.
Blade Design
The blade of a diving fin is crucial for propulsion.
A well-designed blade has the right balance of flexibility and stiffness.
Some fins incorporate vented designs that reduce drag and enhance thrust by allowing water to flow through slots in the blade.
This design can make kicking easier and more effective, propelling divers forward with less effort.
Foot Pocket and Strap Features
Comfort and efficient energy transfer are ensured through the design of the foot pocket and straps.
A good foot pocket should snugly fit the diver’s foot, channeling energy directly into the fin without loss.
Adjustable straps or bungee models improve fit and comfort, making sure divers can focus on their underwater experience rather than adjusting equipment.
Size and Weight Considerations
Fin size and weight significantly affect propulsion.
Longer fins often provide more power, suitable for open water diving.
However, they’re also heavier and require more muscle strength.
Shorter fins are lighter, offering greater maneuverability, ideal for diving in confined spaces or for divers who may tire easily.
Manufacturers strive to find a happy medium, balancing size and weight to achieve optimal efficiency.
Advanced Technologies
In recent years, manufacturers have embraced advanced technology to enhance propulsion.
For example, some diving fins use materials developed with aerospace technology, improving energy transfer from the diver’s legs to the fin.
Innovative designs, such as split fins or channel designs, also help in pushing the water effectively, increasing thrust without straining the diver.
Conclusion
Understanding the processes involved in manufacturing diving fins and the features that enhance propulsion can give us a deeper appreciation for these essential diving tools.
Every phase of production—from selecting materials to designing and testing—plays a significant role in ensuring the final product is effective and reliable.
For divers, the right pair of fins makes all the difference, allowing for smoother, more efficient underwater adventures.
So next time you slip on a pair of diving fins, remember the thoughtful engineering and technology that help you glide through the aquatic realm with ease.
資料ダウンロード
QCD管理受発注クラウド「newji」は、受発注部門で必要なQCD管理全てを備えた、現場特化型兼クラウド型の今世紀最高の受発注管理システムとなります。
ユーザー登録
受発注業務の効率化だけでなく、システムを導入することで、コスト削減や製品・資材のステータス可視化のほか、属人化していた受発注情報の共有化による内部不正防止や統制にも役立ちます。
NEWJI DX
製造業に特化したデジタルトランスフォーメーション(DX)の実現を目指す請負開発型のコンサルティングサービスです。AI、iPaaS、および先端の技術を駆使して、製造プロセスの効率化、業務効率化、チームワーク強化、コスト削減、品質向上を実現します。このサービスは、製造業の課題を深く理解し、それに対する最適なデジタルソリューションを提供することで、企業が持続的な成長とイノベーションを達成できるようサポートします。
製造業ニュース解説
製造業、主に購買・調達部門にお勤めの方々に向けた情報を配信しております。
新任の方やベテランの方、管理職を対象とした幅広いコンテンツをご用意しております。
お問い合わせ
コストダウンが利益に直結する術だと理解していても、なかなか前に進めることができない状況。そんな時は、newjiのコストダウン自動化機能で大きく利益貢献しよう!
(β版非公開)